Π¦Π΅Ρ β ΠΠΈΠΊΠΈΠΏΠ΅Π΄ΠΈΡ
ΠΠ°ΡΠ΅ΡΠΈΠ°Π» ΠΈΠ· ΠΠΈΠΊΠΈΠΏΠ΅Π΄ΠΈΠΈ β ΡΠ²ΠΎΠ±ΠΎΠ΄Π½ΠΎΠΉ ΡΠ½ΡΠΈΠΊΠ»ΠΎΠΏΠ΅Π΄ΠΈΠΈ
Π’Π΅ΠΊΡΡΠ°Ρ Π²Π΅ΡΡΠΈΡ ΡΡΡΠ°Π½ΠΈΡΡ ΠΏΠΎΠΊΠ° Π½Π΅ ΠΏΡΠΎΠ²Π΅ΡΡΠ»Π°ΡΡ ΠΎΠΏΡΡΠ½ΡΠΌΠΈ ΡΡΠ°ΡΡΠ½ΠΈΠΊΠ°ΠΌΠΈ ΠΈ ΠΌΠΎΠΆΠ΅Ρ Π·Π½Π°ΡΠΈΡΠ΅Π»ΡΠ½ΠΎ ΠΎΡΠ»ΠΈΡΠ°ΡΡΡΡ ΠΎΡ Π²Π΅ΡΡΠΈΠΈ, ΠΏΡΠΎΠ²Π΅ΡΠ΅Π½Π½ΠΎΠΉ 24 ΠΎΠΊΡΡΠ±ΡΡ 2018; ΠΏΡΠΎΠ²Π΅ΡΠΊΠΈ ΡΡΠ΅Π±ΡΠ΅Ρ 1 ΠΏΡΠ°Π²ΠΊΠ°. Π’Π΅ΠΊΡΡΠ°Ρ Π²Π΅ΡΡΠΈΡ ΡΡΡΠ°Π½ΠΈΡΡ ΠΏΠΎΠΊΠ° Π½Π΅ ΠΏΡΠΎΠ²Π΅ΡΡΠ»Π°ΡΡ ΠΎΠΏΡΡΠ½ΡΠΌΠΈ ΡΡΠ°ΡΡΠ½ΠΈΠΊΠ°ΠΌΠΈ ΠΈ ΠΌΠΎΠΆΠ΅Ρ Π·Π½Π°ΡΠΈΡΠ΅Π»ΡΠ½ΠΎ ΠΎΡΠ»ΠΈΡΠ°ΡΡΡΡ ΠΎΡ Π²Π΅ΡΡΠΈΠΈ, ΠΏΡΠΎΠ²Π΅ΡΠ΅Π½Π½ΠΎΠΉ 24 ΠΎΠΊΡΡΠ±ΡΡ 2018; ΠΏΡΠΎΠ²Π΅ΡΠΊΠΈ ΡΡΠ΅Π±ΡΠ΅Ρ 1 ΠΏΡΠ°Π²ΠΊΠ°. Π¦Π΅Ρ ΠΎΠ²ΡΠ΅ Π΄ΠΎΠΌΠ° Π½Π° ΠΡΠ°Π½-ΠΏΠ»Π°Ρ Π² ΠΠ½ΡΠ²Π΅ΡΠΏΠ΅Π½Π΅. XVΒ Π².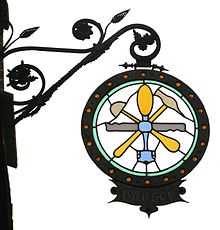
Π¦Π΅Ρ (ΡΠ΅ΡΠ΅Π· ΠΏΠΎΠ»ΡΡΠΊ. ΡΠ΅Ρh ΠΈΠ· ΡΡΠ΅Π΄Π½Π΅Π²Π΅ΡΡ Π½Π΅Π½Π΅ΠΌΠ΅ΡΠΊΠΎΠ³ΠΎ zΡΡh, zΡΡhΠ΅ Β«ΠΎΠ±ΡΠ΅Π΄ΠΈΠ½Π΅Π½ΠΈΠ΅ Π»ΠΈΡ ΠΎΠ΄Π½ΠΎΠ³ΠΎ ΡΠΎΡΠ»ΠΎΠ²ΠΈΡΒ», ΡΠΎΠ²Ρ. Π½Π΅ΠΌ.Β Zunft)Β β ΡΠΎΡΠ³ΠΎΠ²ΠΎ-ΡΠ΅ΠΌΠ΅ΡΠ»Π΅Π½Π½Π°Ρ
ru.wikipedia.org
Π§ΡΠΎ ΡΠ°ΠΊΠΎΠ΅ ΡΠ΅Ρ ? ΠΠΎΠ΄ΡΠΎΠ±Π½ΡΠΉ ΡΠ°Π·Π±ΠΎΡ
Π ΡΡΠ°ΡΡΠ΅ ΡΠ°ΡΡΠΊΠ°Π·ΡΠ²Π°Π΅ΡΡΡ ΠΎ ΡΠΎΠΌ, ΡΡΠΎ ΡΠ°ΠΊΠΎΠ΅ ΡΠ΅Ρ , ΠΊΠΎΠ³Π΄Π° ΠΎΠ½ΠΈ Π²ΠΏΠ΅ΡΠ²ΡΠ΅ ΠΏΠΎΡΠ²ΠΈΠ»ΠΈΡΡ ΠΈ ΠΊΠ°ΠΊΠΎΠ²Ρ Π±ΡΠ»ΠΈ ΠΏΡΠΈΡΠΈΠ½Ρ ΠΈΡ ΠΏΠΎΡΠ²Π»Π΅Π½ΠΈΡ Π² Π‘ΡΠ΅Π΄Π½ΠΈΠ΅ Π²Π΅ΠΊΠ°.
ΠΡΠΎΠΈΠ·Π²ΠΎΠ΄ΡΡΠ²ΠΎ
ΠΡΠ΄ΠΈ Π²ΠΎ Π²ΡΠ΅ Π²ΡΠ΅ΠΌΠ΅Π½Π° ΡΠ΅Π½ΠΈΠ»ΠΈ ΡΠ΅Ρ , ΠΊΡΠΎ ΠΎΠ±Π»Π°Π΄Π°Π» ΠΊΠ°ΠΊΠΈΠΌΠΈ-ΡΠΎ ΡΠΌΠ΅Π½ΠΈΡΠΌΠΈ, ΠΊ ΠΏΡΠΈΠΌΠ΅ΡΡ, ΡΠΈΡΡ ΠΎΠ΄Π΅ΠΆΠ΄Ρ ΠΈΠ»ΠΈ ΠΈΠ·Π³ΠΎΡΠ°Π²Π»ΠΈΠ²Π°ΡΡ ΠΎΡΡΠ΄ΠΈΡ ΡΡΡΠ΄Π°. ΠΠΎ ΠΏΠΎΡΡΠ΅ΠΏΠ΅Π½Π½ΠΎ, Ρ ΡΠ°Π·Π²ΠΈΡΠΈΠ΅ΠΌ ΡΠ΅Π»ΠΎΠ²Π΅ΡΠ΅ΡΠΊΠΎΠ³ΠΎ ΠΎΠ±ΡΠ΅ΡΡΠ²Π°, ΠΌΠ°ΡΡΠ΅ΡΠ°ΠΌ ΡΡΠ°Π½ΠΎΠ²ΠΈΠ»ΠΎΡΡ Π²ΡΠ΅ ΡΠ»ΠΎΠΆΠ½Π΅Π΅ ΠΎΠ±Π΅ΡΠΏΠ΅ΡΠΈΠ²Π°ΡΡ ΡΠΎΠ²Π°ΡΠΎΠΌ ΠΈΠ»ΠΈ ΠΈΠ½ΡΠΌ ΠΌΠ°ΡΠ΅ΡΠΈΠ°Π»ΠΎΠΌ Π²ΡΠ΅Ρ ΠΆΠ΅Π»Π°ΡΡΠΈΡ , ΠΈ ΠΏΠΎΡΠΎΠΌΡ Π² Π‘ΡΠ΅Π΄Π½Π΅Π²Π΅ΠΊΠΎΠ²ΠΎΠΉ ΠΠ²ΡΠΎΠΏΠ΅ ΡΡΠ°Π»ΠΈ ΠΏΠΎΡΠ²Π»ΡΡΡΡΡ ΡΠ΅Ρ Π°. Π’Π°ΠΊ ΡΡΠΎ ΡΠ°ΠΊΠΎΠ΅ ΡΠ΅Ρ ΠΈ ΠΊΠ°ΠΊΠΎΠ²Π° Π΅Π³ΠΎ ΡΠΎΠ»Ρ? ΠΠ± ΡΡΠΎΠΌ ΠΌΡ ΠΈ ΠΏΠΎΠ³ΠΎΠ²ΠΎΡΠΈΠΌ Π² Π΄Π°Π½Π½ΠΎΠΉ ΡΡΠ°ΡΡΠ΅.
ΠΠΏΡΠ΅Π΄Π΅Π»Π΅Π½ΠΈΠ΅
Π‘Π»ΠΎΠ²ΠΎ ΡΡΠΎ ΠΏΡΠΈΡΠ»ΠΎ ΠΈΠ· ΡΡΠ΅Π΄Π½Π΅Π²Π΅ΠΊΠΎΠ²ΠΎΠΉ Π²Π΅ΡΡΠΈΠΈ Π½Π΅ΠΌΠ΅ΡΠΊΠΎΠ³ΠΎ ΡΠ·ΡΠΊΠ°, ΠΈΠ·Π½Π°ΡΠ°Π»ΡΠ½ΠΎ ΠΎΠ½ΠΎ ΠΎΠ·Π½Π°ΡΠ°Π»ΠΎ Π½Π΅ΠΊΠΎΠ΅ ΠΎΠ±ΡΠ΅Π΄ΠΈΠ½Π΅Π½ΠΈΠ΅, Π»ΠΈΡΠ° ΠΊΠΎΡΠΎΡΠΎΠ³ΠΎ ΠΏΡΠΈΠ½Π°Π΄Π»Π΅ΠΆΠ°Π»ΠΈ ΠΊ ΠΎΠ΄Π½ΠΎΠΌΡ ΡΠΎΡΠ»ΠΎΠ²ΠΈΡ. Π ΡΠΎΠ²ΡΠ΅ΠΌΠ΅Π½Π½ΠΎΠΌ ΠΆΠ΅ ΠΏΠΎΠ½ΡΡΠΈΠΈ ΡΠ΅Ρ β ΡΡΠΎ ΠΎΠ΄Π½Π° ΠΈΠ· ΡΠ°ΡΡΠ΅ΠΉ ΠΏΡΠΎΠΈΠ·Π²ΠΎΠ΄ΡΡΠ²Π΅Π½Π½ΠΎΠ³ΠΎ ΠΏΡΠ΅Π΄ΠΏΡΠΈΡΡΠΈΡ, ΠΊΠΎΡΠΎΡΠΎΠ΅ ΡΡΠ°ΡΡΠ²ΡΠ΅Ρ Π² ΠΎΠ±ΡΠ΅ΠΌ ΠΏΡΠΎΡΠ΅ΡΡΠ΅ ΠΏΡΠΎΠΈΠ·Π²ΠΎΠ΄ΡΡΠ²Π° ΠΈ Π²ΡΠΏΡΡΠΊΠ΅ ΠΊΠ°ΠΊΠΎΠΉ-ΡΠΎ ΠΏΡΠΎΠ΄ΡΠΊΡΠΈΠΈ. ΠΡΠΎΡΠ΅ Π³ΠΎΠ²ΠΎΡΡ, ΡΡΠΎ ΠΎΡΠ΄Π΅Π»Π΅Π½ΠΈΠ΅ ΡΠ°Π±ΡΠΈΠΊΠΈ ΠΈΠ»ΠΈ Π·Π°Π²ΠΎΠ΄Π°, Π³Π΄Π΅ ΠΏΡΠΎΠΈΡΡ ΠΎΠ΄ΠΈΡ ΠΎΠ΄ΠΈΠ½ ΠΈΠ· ΡΡΠ°ΠΏΠΎΠ² ΠΏΡΠΎΠΈΠ·Π²ΠΎΠ΄ΡΡΠ²Π° ΠΊΠ°ΠΊΠΎΠΉ-ΡΠΎ ΠΏΡΠΎΠ΄ΡΠΊΡΠΈΠΈ. Π ΠΏΡΠΈΠΌΠ΅ΡΡ, Π΅Π΅ ΡΠ±ΠΎΡΠΊΠ°, ΠΏΡΠΎΠ²Π΅ΡΠΊΠ° Π½Π° Π΄Π΅ΡΠ΅ΠΊΡΡ, ΠΏΠΎΠΊΡΠ°ΡΠΊΠ° ΠΈ ΠΏΡΠΎΡΠ΅Π΅. Π’Π°ΠΊ ΡΡΠΎ ΡΠ΅ΠΏΠ΅ΡΡ ΠΌΡ Π·Π½Π°Π΅ΠΌ, ΡΡΠΎ ΡΠ°ΠΊΠΎΠ΅ ΡΠ΅Ρ .
ΠΡΠ²Π°ΡΡ ΠΎΠ½ΠΈ ΡΠ°Π·Π½ΠΎΠ³ΠΎ Π½Π°Π·Π½Π°ΡΠ΅Π½ΠΈΡ, ΠΈ Π΅ΡΠ»ΠΈ Π³ΠΎΠ²ΠΎΡΠΈΡΡ ΠΎ ΠΏΡΠΈΡΠΈΠ½Π°Ρ ΠΈΡ ΠΏΠΎΡΠ²Π»Π΅Π½ΠΈΡ, ΡΠΎ ΠΎΠ΄Π½Π° ΠΈΠ· Π½ΠΈΡ β ΡΡΠΎ ΡΠ΄ΠΎΠ±ΡΡΠ²ΠΎ. ΠΠΎΡΠ°Π·Π΄ΠΎ ΠΏΡΠΎΡΠ΅ ΠΈ Π²ΡΠ³ΠΎΠ΄Π½Π΅Π΅ Ρ ΡΠΊΠΎΠ½ΠΎΠΌΠΈΡΠ΅ΡΠΊΠΎΠΉ ΡΠΎΡΠΊΠΈ Π·ΡΠ΅Π½ΠΈΡ ΠΎΡΠ³Π°Π½ΠΈΠ·ΠΎΠ²Π°ΡΡ ΠΏΡΠΎΠΈΠ·Π²ΠΎΠ΄ΡΡΠ²ΠΎ ΠΊΠ°ΠΊΠΈΡ -ΡΠΎ Π²Π΅ΡΠ΅ΠΉ, ΠΌΠ°ΡΠ΅ΡΠΈΠ°Π»Π° ΠΈΠ»ΠΈ ΠΎΠ±ΠΎΡΡΠ΄ΠΎΠ²Π°Π½ΠΈΡ Π² ΠΎΠ΄Π½ΠΎΠΌ ΠΊΠΎΠ½ΠΊΡΠ΅ΡΠ½ΠΎΠΌ ΠΌΠ΅ΡΡΠ΅, Π³Π΄Π΅ Π΅ΡΡΡ Π²ΡΠ΅ Π½ΡΠΆΠ½ΡΠ΅ Π΄Π»Ρ ΡΡΠΎΠ³ΠΎ ΡΡΠ»ΠΎΠ²ΠΈΡ. Π’Π°ΠΊΠΆΠ΅ ΡΠ°Π±ΠΎΡΠ° ΡΠ΅Ρ ΠΎΠ² ΠΎΡΠ³Π°Π½ΠΈΠ·ΡΠ΅ΡΡΡ Ρ ΡΡΠ΅ΡΠΎΠΌ ΠΏΠΎΠ»ΡΡΠ΅Π½ΠΈΡ Π½Π°ΠΈΠ±ΠΎΠ»Π΅Π΅ ΠΏΡΠΎΠ΄ΡΠΊΡΠΈΠ²Π½ΠΎΠΉ ΡΠ°Π±ΠΎΡΡ ΡΠΎΡΡΡΠ΄Π½ΠΈΠΊΠΎΠ² ΠΈΠ»ΠΈ ΠΏΡΠΎΠΌΡΡΠ»Π΅Π½Π½ΡΡ ΡΡΠ°Π½ΠΊΠΎΠ².
ΠΡΠ΅ ΡΠ΅Ρ Π° ΠΏΡΠ΅Π΄ΠΏΡΠΈΡΡΠΈΡ ΠΈΠΌΠ΅ΡΡ ΡΠ²ΠΎΠ΅Π³ΠΎ Π³Π»Π°Π²Π½ΠΎΠ³ΠΎ ΠΌΠ°ΡΡΠ΅ΡΠ°, ΠΊΠΎΡΠΎΡΡΠΉ Π½Π°Π±Π»ΡΠ΄Π°Π΅Ρ Π·Π° ΠΏΡΠΎΠΈΠ·Π²ΠΎΠ΄ΡΡΠ²Π΅Π½Π½ΡΠΌ ΠΏΡΠΎΡΠ΅ΡΡΠΎΠΌ ΠΈΠ»ΠΈ ΠΆΠ΅ ΠΎΡΠ³Π°Π½ΠΈΠ·ΠΎΠ²ΡΠ²Π°Π΅Ρ Π΅Π³ΠΎ.
Π’Π΅Ρ Π½ΠΈΠΊΠ° Π±Π΅Π·ΠΎΠΏΠ°ΡΠ½ΠΎΡΡΠΈ, ΡΠ΅ΡΠΊΠΎΠ΅ ΡΠ°ΡΠΏΡΠ΅Π΄Π΅Π»Π΅Π½ΠΈΠ΅ ΡΠΎΠ»Π΅ΠΉ ΡΠ°Π±ΠΎΡΠΈΡ ΠΈ Π°Π²ΡΠΎΠΌΠ°ΡΠΈΠ·ΠΌ ΠΏΡΠΎΠΈΠ·Π²ΠΎΠ΄ΡΡΠ²Π° Π² ΠΈΡΠΎΠ³Π΅ ΠΏΠΎΠ·Π²ΠΎΠ»ΡΡΡ Π΄ΠΎΠ±ΠΈΡΡΡΡ Π²ΡΡΠΎΠΊΠΎΠΉ ΠΏΡΠΎΠΈΠ·Π²ΠΎΠ΄ΠΈΡΠ΅Π»ΡΠ½ΠΎΡΡΠΈ ΡΡΡΠ΄Π°. ΠΡΠ»ΠΈ Π³ΠΎΠ²ΠΎΡΠΈΡΡ ΠΎ ΡΠΎΠΌ, ΠΊΠ°ΠΊΠΈΠ΅ Π±ΡΠ²Π°ΡΡ ΡΠ΅Ρ Π°, ΡΠΎ ΠΈΡ ΠΎΡΠ΅Π½Ρ ΠΌΠ½ΠΎΠ³ΠΎ — ΡΠ±ΠΎΡΠΎΡΠ½ΡΠ΅, ΠΏΠΎΠΊΡΠ°ΡΠΎΡΠ½ΡΠ΅, Π»ΠΈΡΠ΅ΠΉΠ½ΡΠ΅, ΠΏΡΠΎΠΊΠ°ΡΠ½ΡΠ΅. ΠΠ±ΡΡΠ½ΠΎ Π½Π° ΠΊΠ°ΠΆΠ΄ΠΎΠΌ ΠΈΠ· Π½ΠΈΡ ΠΎΡΡΡΠ΅ΡΡΠ²Π»ΡΠ΅ΡΡΡ ΡΡΡΠΎΠ³ΠΎ ΠΎΠ΄ΠΈΠ½ Π²ΠΈΠ΄ ΡΠ°Π±ΠΎΡ.
Π‘ ΡΠ΅ΠΌ, ΡΡΠΎ ΡΠ°ΠΊΠΎΠ΅ ΡΠ΅Ρ , ΠΌΡ ΡΠ°Π·ΠΎΠ±ΡΠ°Π»ΠΈΡΡ. ΠΠ°ΠΊ ΠΌΡ ΡΠΆΠ΅ Π·Π½Π°Π΅ΠΌ, Π² Π‘ΡΠ΅Π΄Π½ΠΈΠ΅ Π²Π΅ΠΊΠ° ΡΡΠΈΠΌ ΡΠ»ΠΎΠ²ΠΎΠΌ Π½Π°Π·ΡΠ²Π°Π»ΠΈ ΠΎΠ±ΡΠ΅Π΄ΠΈΠ½Π΅Π½ΠΈΡ ΡΠ°Π±ΠΎΡΠΈΡ , Π±Π»Π°Π³ΠΎΠ΄Π°ΡΡ ΠΊΠΎΡΠΎΡΡΠΌ ΠΈ ΠΏΡΠΎΠΈΠ·ΠΎΡΠ΅Π» ΠΏΠ΅ΡΠ΅Ρ ΠΎΠ΄ ΠΎΡ ΡΠ°Π·ΡΠΎΠ·Π½Π΅Π½Π½ΡΡ ΡΠ΅ΠΌΠ΅ΡΠ»Π΅Π½Π½ΡΡ Π΄ΠΎΠΌΠΎΠ² ΠΈ ΠΌΠ°Π½ΡΡΠ°ΠΊΡΡΡ Π΄ΠΎ ΠΏΠΎΠ»Π½ΠΎΡΠ΅Π½Π½ΡΡ ΡΠ°Π±ΡΠΈΠΊ ΠΈ Π·Π°Π²ΠΎΠ΄ΠΎΠ². Π Π°ΡΡΠΌΠΎΡΡΠΈΠΌ ΠΊΡΠ°ΡΠΊΠΎ ΠΈΡ ΠΈΡΡΠΎΡΠΈΡ.
ΠΡΡΠΎΡΠΈΡ
ΠΠ·Π½Π°ΡΠ°Π»ΡΠ½ΠΎ Π΄Π΅ΡΡΠ΅Π»ΡΠ½ΠΎΡΡΡ ΡΠ΅Ρ ΠΎΠ² Π²ΠΎ Π²ΡΠ΅ΠΌΠ΅Π½Π° Π‘ΡΠ΅Π΄Π½Π΅Π²Π΅ΠΊΠΎΠ²ΡΡ Π½Π΅ ΠΎΠ³ΡΠ°Π½ΠΈΡΠΈΠ²Π°Π»Π°ΡΡ ΠΎΠ΄Π½ΠΈΠΌ Π»ΠΈΡΡ ΡΠ±ΡΡΠΎΠΌ Π³ΠΎΡΠΎΠ²ΠΎΠΉ ΠΏΡΠΎΠ΄ΡΠΊΡΠΈΠΈ. ΠΡ Π·Π°Π΄Π°ΡΠ° ΡΠ°ΠΊΠΆΠ΅ Π·Π°ΠΊΠ»ΡΡΠ°Π»Π°ΡΡ Π² ΡΠΎΠΌ, ΡΡΠΎΠ±Ρ ΠΎΠ³ΡΠ°Π΄ΠΈΡΡ ΡΠ΅Ρ ΠΎΠ²ΡΡ ΠΌΠ°ΡΡΠ΅ΡΠΎΠ² ΠΎΡ ΠΎΠ±ΡΡΠ½ΡΡ ΡΠ΅ΠΌΠ΅ΡΠ»Π΅Π½Π½ΠΈΠΊΠΎΠ² ΠΈ ΠΊΠΎΠ½ΠΊΡΡΠ΅Π½ΡΠΈΠΈ, ΠΊΠΎΡΠΎΡΡΡ ΠΏΠΎΡΡΠΎΡΠ½Π½ΠΎ ΡΠΎΠ·Π΄Π°Π²Π°Π»ΠΈ ΠΊΡΠ΅ΡΡΡΡΠ½Π΅, ΡΡΠΎ ΠΏΡΠΈΠ±ΡΠ²Π°Π»ΠΈ Π² Π³ΠΎΡΠΎΠ΄Π°. Π’Π°ΠΊΠΆΠ΅ ΡΡΠΊΠΎΠ²ΠΎΠ΄ΡΡΠ²ΠΎ ΠΏΠΎΠ΄ΠΎΠ±Π½ΡΡ ΡΠ΅Ρ ΠΎΠ² Π·Π°Π½ΠΈΠΌΠ°Π»ΠΎΡΡ ΡΠΈΠ½Π°Π½ΡΠΎΠ²ΡΠΌ, ΡΠ°Π±ΠΎΡΠΈΠΌ ΠΈ ΠΈΠ½ΡΠΌ ΠΏΠ»Π°Π½ΠΈΡΠΎΠ²Π°Π½ΠΈΠ΅ΠΌ, ΠΊ ΠΏΡΠΈΠΌΠ΅ΡΡ, Π²ΡΠ΅ΠΌΡ ΠΎΡ Π²ΡΠ΅ΠΌΠ΅Π½ΠΈ ΠΎΡΠ΄Π°Π²Π°Π»ΠΎ ΠΏΡΠΈΠΊΠ°Π·, ΠΈ ΠΊΠ°ΠΊΠΎΠΉ-ΡΠΎ ΡΠ°Π±ΠΎΡΠΈΠΉ ΡΠ΅Ρ ΡΠ½ΠΈΠΆΠ°Π» ΡΡΠΎΠ²Π΅Π½Ρ ΠΏΡΠΎΠΈΠ·Π²ΠΎΠ΄ΡΡΠ²Π°, ΡΡΠΎΠ±Ρ Π½Π΅ ΡΠΎΠ·Π΄Π°Π²Π°ΡΡ ΠΏΠ°Π΄Π΅Π½ΠΈΡ ΡΠ΅Π½ Π½Π° ΡΠΎΠ²Π°ΡΡ ΠΈΠ·-Π·Π° Π΅Π³ΠΎ ΠΈΠ·Π±ΡΡΠΊΠ° Π½Π° ΡΡΠ½ΠΊΠ΅.
Π’Π°ΠΊΠΆΠ΅ ΡΡΠ΅Π΄Π½Π΅Π²Π΅ΠΊΠΎΠ²ΡΠ΅ ΡΠ΅Ρ Π° ΠΏΡΠΈΠ²Π»Π΅ΠΊΠ°Π»ΠΈ ΠΏΡΠ°ΠΊΡΠΈΡΠ΅ΡΠΊΠΈ Π²ΡΠ΅Ρ ΠΌΠ°ΡΡΠ΅ΡΠΎΠ² ΠΈ ΡΠ΅ΠΌ, ΡΡΠΎ Π² Π½ΠΈΡ Π·Π° ΠΈΠ½ΡΠ΅ΡΠ΅ΡΠ°ΠΌΠΈ ΡΡΡΠΆΠ΅Π½ΠΈΠΊΠΎΠ² ΡΠ»Π΅Π΄ΠΈΠ»ΠΈ ΡΡΠ°ΡΠ΅ΠΉΡΠΈΠ½Ρ, Π° Π²Π»Π°Π΄Π΅Π»ΡΡΡ Π²ΡΠ΅Π³Π΄Π° ΠΏΡΠΈΡΠ»ΡΡΠΈΠ²Π°Π»ΠΈΡΡ ΠΊ ΠΈΡ ΡΠΎΠ²Π΅ΡΠ°ΠΌ. Π¦Π΅Ρ ΠΎΠ²ΠΎΠΉ ΡΠΎΠ²Π΅Ρ Π² ΡΠΎΠΌ ΡΠΈΡΠ»Π΅ ΠΎΡ Π²Π°ΡΡΠ²Π°Π» ΠΈ Π»ΠΈΡΠ½ΡΡ, ΡΠ΅ΠΌΠ΅ΠΉΠ½ΡΡ ΠΈΠ»ΠΈ ΠΎΠ±ΡΠ΅ΡΡΠ²Π΅Π½Π½ΡΡ ΠΆΠΈΠ·Π½Ρ ΠΌΠ°ΡΡΠ΅ΡΠ° ΠΈΠ»ΠΈ ΡΠ΅ΠΌΠ΅ΡΠ»Π΅Π½Π½ΠΈΠΊΠ°, ΠΎΠΊΠ°Π·ΡΠ²Π°Ρ ΠΏΠΎ Π²ΠΎΠ·ΠΌΠΎΠΆΠ½ΠΎΡΡΠΈ Π²ΡΡΡΠ΅ΡΠΊΡΡ ΠΏΠΎΠ΄Π΄Π΅ΡΠΆΠΊΡ.
ΠΠ°ΠΊ Π²ΠΈΠ΄ΠΈΠΌ, ΠΎΡΠ΅Π½Ρ ΠΌΠ½ΠΎΠ³ΠΈΠ΅ ΡΡΠΈ ΠΎΡΠ³Π°Π½ΠΈΠ·Π°ΡΠΈΠΎΠ½Π½ΡΠ΅ ΡΠ΅ΡΡΡ Π΄ΠΎΠΆΠΈΠ»ΠΈ ΠΈ Π΄ΠΎ Π½Π°ΡΠΈΡ Π΄Π½Π΅ΠΉ, ΠΊ ΠΏΡΠΈΠΌΠ΅ΡΡ, ΡΠΎΡ ΠΆΠ΅ ΠΏΡΠΎΡΡΠΎΡΠ·, ΠΊΠΎΡΠΎΡΡΠΉ Π·Π°ΠΌΠ΅Π½ΠΈΠ» ΡΠΎΠ±ΠΎΠΉ ΡΠ΅Ρ ΠΎΠ²ΠΎΠΉ ΡΠΎΠ²Π΅Ρ ΠΈΠ· Π½Π°ΠΈΠ±ΠΎΠ»Π΅Π΅ ΡΠ²Π°ΠΆΠ°Π΅ΠΌΡΡ ΠΈ ΠΎΠΏΡΡΠ½ΡΡ ΠΌΠ°ΡΡΠ΅ΡΠΎΠ².
ΠΡΠΈΡΠΈΠ½Ρ, ΠΏΠΎ ΠΊΠΎΡΠΎΡΡΠΌ ΡΠ΅Ρ Π° Π²ΠΎΠΎΠ±ΡΠ΅ ΡΡΠ°Π»ΠΈ Π²ΠΎΠ·Π½ΠΈΠΊΠ°ΡΡ, ΠΊΡΠΎΡΡΡΡ Π² ΠΎΡΠ΄Π΅Π»Π΅Π½ΠΈΠΈ ΠΏΡΠΎΠΌΡΡΠ»Π΅Π½Π½ΠΎΡΡΠΈ ΠΈ ΡΠ°Π·Π»ΠΈΡΠ½ΠΎΠ³ΠΎ ΡΠ΅ΠΌΠ΅ΡΠ»Π° Π² ΡΠ΅Π»ΠΎΠΌ ΠΎΡ Π·Π΅ΠΌΠ»Π΅Π΄Π΅Π»ΠΈΡ. ΠΡΠΎΡΠ΅ Π³ΠΎΠ²ΠΎΡΡ, Π³ΠΎΡΠΎΠ΄Π° ΠΎΡ Π΄Π΅ΡΠ΅Π²Π½ΠΈ. ΠΠΎΡΠ²Π»ΡΡΡΡΡ ΠΎΠ½ΠΈ ΡΡΠ°Π»ΠΈ, Π½Π°ΡΠΈΠ½Π°Ρ Ρ ΠΏΡΠΈΠΌΠ΅ΡΠ½ΠΎ X Π²Π΅ΠΊΠ°. Π ΠΏΡΠΈΠΌΠ΅ΡΡ, Π½Π΅Π΄Π°Π²Π½ΠΎ Π°ΡΡ Π΅ΠΎΠ»ΠΎΠ³Π°ΠΌΠΈ Π±ΡΠ» ΠΎΠ±Π½Π°ΡΡΠΆΠ΅Π½ ΡΠ΅Ρ ΠΏΠΎ ΠΏΡΠΎΠΈΠ·Π²ΠΎΠ΄ΡΡΠ²Ρ Π·Π½Π°ΠΌΠ΅Π½ΠΈΡΠΎΠ³ΠΎ Π½Π° Π²Π΅ΡΡ Π΄ΡΠ΅Π²Π½ΠΈΠΉ ΠΌΠΈΡ ΡΠ°ΡΡΠΎΡΠ° Π² ΠΎΠ΄Π½ΠΎΠΉ ΠΈΠ· ΠΊΠΈΡΠ°ΠΉΡΠΊΠΈΡ ΠΏΡΠΎΠ²ΠΈΠ½ΡΠΈΠΉ. ΠΠΎ ΠΏΠΎΠ΄ΡΡΠ΅ΡΠ°ΠΌ ΡΡΠ΅Π½ΡΡ , ΡΠ°Π±ΠΎΡΠ°Π» ΠΎΠ½ Π² ΠΏΠ΅ΡΠΈΠΎΠ΄ Ρ 1279 ΠΏΠΎ 1368 Π³Π³.
ΠΠΈΠ½ΠΈ-ΡΠ΅Ρ Π°
Π ΠΏΠΎΡΠ»Π΅Π΄Π½Π΅Π΅ Π²ΡΠ΅ΠΌΡ Π½Π° ΡΡΠ½ΠΊΠ΅ Π³ΠΎΡΠΎΠ²ΡΡ Π±ΠΈΠ·Π½Π΅Ρ-ΡΠ΅ΡΠ΅Π½ΠΈΠΉ Π²ΡΠ΅ ΡΠ°ΡΠ΅ ΠΌΠΎΠΆΠ½ΠΎ Π²ΡΡΡΠ΅ΡΠΈΡΡ ΡΠ°ΠΊΠΈΠ΅ ΠΏΡΠ΅Π΄Π»ΠΎΠΆΠ΅Π½ΠΈΡ, ΠΊΠ°ΠΊ ΠΌΠΈΠ½ΠΈ-ΡΠ΅Ρ Π°. ΠΡΠ΅Π΄ΡΡΠ°Π²Π»ΡΡΡ ΠΎΠ½ΠΈ ΡΠΎΠ±ΠΎΠΉ ΠΎΠ±ΠΎΡΡΠ΄ΠΎΠ²Π°Π½ΠΈΠ΅, ΠΊΠΎΡΠΎΡΠΎΠ³ΠΎ Π΄ΠΎΡΡΠ°ΡΠΎΡΠ½ΠΎ Π΄Π»Ρ ΠΏΠΎΠ»Π½ΠΎΠ³ΠΎ ΠΏΡΠΎΠΈΠ·Π²ΠΎΠ΄ΡΡΠ²Π΅Π½Π½ΠΎΠ³ΠΎ ΠΏΡΠΎΡΠ΅ΡΡΠ° ΠΊΠ°ΠΊΠΎΠΉ-ΡΠΎ ΠΏΡΠΎΠ΄ΡΠΊΡΠΈΠΈ ΠΈΠ»ΠΈ ΠΈΠ½ΠΎΠ³ΠΎ ΠΌΠ°ΡΠ΅ΡΠΈΠ°Π»Π°. Π ΠΏΡΠΈΠΌΠ΅ΡΡ, ΠΌΠΎΠΆΠ½ΠΎ ΠΏΡΠΈΠΎΠ±ΡΠ΅ΡΡΠΈ ΡΠ΅Ρ ΠΏΠΎ ΠΏΡΠΎΠΈΠ·Π²ΠΎΠ΄ΡΡΠ²Ρ Ρ Π»Π΅Π±ΠΎΠ±ΡΠ»ΠΎΡΠ½ΡΡ ΠΈΠ·Π΄Π΅Π»ΠΈΠΉ, ΠΌΠΎΠ»ΠΎΡΠ½ΠΎΠΉ ΠΏΡΠΎΠ΄ΡΠΊΡΠΈΠΈ ΠΈ Ρ.ΠΏ. Π‘ΡΡΠ΅ΡΡΠ²ΡΡΡ ΠΎΠ½ΠΈ ΠΊΠ°ΠΊ Π² Π²ΠΈΠ΄Π΅ ΡΠ»Π΅ΠΌΠ΅Π½ΡΠΎΠ² ΠΎΠ±ΠΎΡΡΠ΄ΠΎΠ²Π°Π½ΠΈΡ, ΡΠ°ΠΊ ΠΈ Π² Π²ΠΈΠ΄Π΅ ΠΌΠΎΠ΄ΡΠ»ΡΠ½ΡΡ ΡΠ΅ΡΠ΅Π½ΠΈΠΉ, ΠΏΡΠΈΠΎΠ±ΡΠ΅ΡΡ ΠΊΠΎΡΠΎΡΠΎΠ΅ Π½Π΅ Π½ΡΠΆΠ½ΠΎ Π±ΡΠ΄Π΅Ρ ΠΈΡΠΊΠ°ΡΡ ΠΎΡΠ΄Π΅Π»ΡΠ½ΠΎΠ΅ ΠΏΠΎΠΌΠ΅ΡΠ΅Π½ΠΈΠ΅. ΠΡΠ°Π²Π΄Π°, Π΄Π°Π»Π΅ΠΊΠΎ Π½Π΅ Π²ΡΠ΅ ΡΠΈΠΏΡ ΠΏΡΠΎΠΈΠ·Π²ΠΎΠ΄ΡΡΠ²Π° ΠΌΠΎΠΆΠ½ΠΎ ΡΠ°Π·ΠΌΠ΅ΡΡΠΈΡΡ Π² ΠΌΠΎΠ΄ΡΠ»ΡΠ½ΡΡ ΡΠ±ΠΎΡΠ½ΡΡ ΠΏΠΎΠΌΠ΅ΡΠ΅Π½ΠΈΡΡ , ΠΈ Π±ΠΎΠ»ΡΡΠ΅ Π²ΡΠ΅Π³ΠΎ ΠΏΠΎΠ΄Ρ ΠΎΠ΄ΡΡ ΠΎΠ½ΠΈ Π΄Π»Ρ ΠΈΠ·Π³ΠΎΡΠΎΠ²Π»Π΅Π½ΠΈΡ ΠΏΡΠΎΡΡΠΎΠΉ ΠΈΠ»ΠΈ ΠΏΠΈΡΠ΅Π²ΠΎΠΉ ΠΏΡΠΎΠ΄ΡΠΊΡΠΈΠΈ.
ΠΠ°ΠΊΠ»ΡΡΠ΅Π½ΠΈΠ΅
Π’Π°ΠΊ ΡΡΠΎ ΠΌΡ ΡΠ°Π·ΠΎΠ±ΡΠ°Π»ΠΈΡΡ Ρ ΡΠ΅ΠΌ, ΡΡΠΎ ΡΠΎΠ±ΠΎΠΉ ΠΏΡΠ΅Π΄ΡΡΠ°Π²Π»ΡΡΡ ΡΠ΅Ρ Π° ΠΈ Π΄Π»Ρ ΡΠ΅Π³ΠΎ ΠΎΠ½ΠΈ Π½ΡΠΆΠ½Ρ. Π ΡΠ²ΠΎΠ΅ Π²ΡΠ΅ΠΌΡ ΠΈΠΌΠ΅Π½Π½ΠΎ ΠΏΠ΅ΡΠ΅Ρ ΠΎΠ΄ Π½Π° ΡΠ΅Ρ ΠΎΠ²ΠΎΠ΅ ΠΈ ΡΠ°Π±ΡΠΈΡΠ½ΠΎΠ΅ ΠΏΡΠΎΠΈΠ·Π²ΠΎΠ΄ΡΡΠ²ΠΎ Π±Π»Π°Π³ΠΎΡΠ²ΠΎΡΠ½ΠΎ ΠΏΠΎΠ²Π»ΠΈΡΠ» Π½Π° Ρ ΠΎΠ΄ ΠΏΡΠΎΠΌΡΡΠ»Π΅Π½Π½ΠΎΠΉ ΡΠ΅Π²ΠΎΠ»ΡΡΠΈΠΈ. ΠΠ΅Π΄Ρ ΠΏΡΠΎΠΈΠ·Π²ΠΎΠ΄ΡΡΠ²ΠΎ ΠΌΠ°Π½ΡΡΠ°ΠΊΡΡΡΠ½ΠΎΠ³ΠΎ ΡΠΈΠΏΠ° Π±ΡΠ»ΠΎ Π½Π΅ Π² ΡΠΎΡΡΠΎΡΠ½ΠΈΠΈ ΠΎΠ±Π΅ΡΠΏΠ΅ΡΠΈΡΡ Π²ΡΠ΅ΠΌΠΈ Π½Π΅ΠΎΠ±Ρ ΠΎΠ΄ΠΈΠΌΡΠΌΠΈ ΡΠΎΠ²Π°ΡΠ°ΠΌΠΈ ΠΏΠΎΡΡΠΎΡΠ½Π½ΠΎ ΡΠ°ΡΡΡΡΠΈΠ΅ Π·Π°ΠΏΡΠΎΡΡ Π½Π°ΡΠ΅Π»Π΅Π½ΠΈΡ.
ΠΡΡΠ΅ΡΡΠ²Π΅Π½Π½ΠΎ, Π»ΡΠ±ΠΎΠΉ ΡΠ°Π±ΠΎΡΠΈΠΉ ΡΠ΅Ρ Π½ΡΠΆΠ΄Π°Π΅ΡΡΡ Π² ΠΏΡΠ°Π²ΠΈΠ»ΡΠ½ΠΎΠΌ ΡΡΠΊΠΎΠ²ΠΎΠ΄ΡΡΠ²Π΅, ΠΏΠΎΡΠΊΠΎΠ»ΡΠΊΡ Π±Π΅Π· Π½Π΅Π³ΠΎ Π΄Π°ΠΆΠ΅ ΡΠ°ΠΌΡΠ΅ Π²ΡΡΠΎΠΊΠΎΡΡΡΠ΅ΠΊΡΠΈΠ²Π½ΡΠ΅ ΡΠ±ΠΎΡΠΎΡΠ½ΡΠ΅ Π»ΠΈΠ½ΠΈΠΈ ΠΈ ΡΠ΅Ρ Π½ΠΈΠΊΠ° Π±ΡΠ΄ΡΡ Π±Π΅ΡΠΏΠΎΠ»Π΅Π·Π½Ρ.
fb.ru
Π¦Π΅Ρ ΠΏΠΎ Π΄Π΅ΠΌΠΎΠ½ΡΠ°ΠΆΡ ΡΠ΅ΠΊΡΡΡΠΈΡΡΠΎΠ½ΠΎΠ² | Π£Π±Π΅ΠΆΠΈΡΠ΅
ΠΠΎΠΊΠ°ΡΠΈΡ Old World Blues
Π¦Π΅Ρ
ΠΏΠΎ Π΄Π΅ΠΌΠΎΠ½ΡΠ°ΠΆΡ ΡΠ΅ΠΊΡΡΡΠΈΡΡΠΎΠ½ΠΎΠ²
ΠΠ½ΡΡΡΠΈ Π»ΠΎΠΊΠ°ΡΠΈΠΈ
ΠΠ°ΡΠΊΠ΅Ρ ΠΊΠ°ΡΡΡ
Π¦Π΅Ρ ΠΏΠΎ Π΄Π΅ΠΌΠΎΠ½ΡΠ°ΠΆΡ ΡΠ΅ΠΊΡΡΡΠΈΡΡΠΎΠ½ΠΎΠ²
cell name
NVDLC03SLSecuritron (ΡΠ½Π°ΡΡΠΆΠΈ)
NVDLC03SLSecuritronINT (Π²Π½ΡΡΡΠΈ)
ref id
xx001d0d (ΡΠ½Π°ΡΡΠΆΠΈ)xx0078eb (Π²Π½ΡΡΡΠΈ)
Π¦Π΅Ρ
ΠΏΠΎ Π΄Π΅ΠΌΠΎΠ½ΡΠ°ΠΆΡ ΡΠ΅ΠΊΡΡΡΠΈΡΡΠΎΠ½ΠΎΠ²[1] (Π°Π½Π³Π». Securitron De-Construction Plant)Β β Π»ΠΎΠΊΠ°ΡΠΈΡ Old World Blues, Π΄ΠΎΠΏΠΎΠ»Π½Π΅Π½ΠΈΡ ΠΊ Fallout: New Vegas.
ΠΡΠ΅Π΄ΠΏΡΠΈΡΡΠΈΠ΅ ΠΏΠΎ ΡΡΠΈΠ»ΠΈΠ·Π°ΡΠΈΠΈ ΡΠ΅ΠΊΡΡΡΠΈΡΡΠΎΠ½ΠΎΠ², Π²Π½ΡΡΡΠΈ Π½Π°Ρ ΠΎΠ΄ΠΈΡΡΡ Π½Π΅ΡΠΊΠΎΠ»ΡΠΊΠΎ Π±Π΅Π·ΡΠΌΠ½ΡΡ ΡΠ΅ΠΊΡΡΡΠΈΡΡΠΎΠ½ΠΎΠ², Π²ΡΠ°ΠΆΠ΄Π΅Π±Π½ΡΡ ΠΊ ΠΈΠ³ΡΠΎΠΊΡ, Π° ΡΠ°ΠΊΠΆΠ΅ ΡΠ½ΠΈΠΊΠ°Π»ΡΠ½ΡΠΉ ΡΠ΅ΠΊΡΡΡΠΈΡΡΠΎΠ½ Β«010011110110111001100101Β».
- ΠΠΎΠ»ΠΎΠ΄ΠΈΡΠΊ Ρ Π»ΠΈΡΠ½ΠΎΡΡΡΡ ΠΡΡΠΆΠΊΠ°Β β Π² ΠΊΡΠ·ΠΎΠ²Π΅ Π³ΡΡΠ·ΠΎΠ²ΠΈΠΊΠ°, Π²ΠΎΠ·Π»Π΅ Π²Ρ ΠΎΠ΄Π° Π½Π° Π·Π°Π²ΠΎΠ΄.
- Π£ΡΠΎΠ²Π΅ΡΡΠ΅Π½ΡΡΠ²ΠΎΠ²Π°Π½ΠΈΠ΅ Π΄Π»Ρ ΠΡΡΠΆΠΊΠ°, Π° ΡΠ°ΠΊΠΆΠ΅, Π²ΠΎΠ·ΠΌΠΎΠΆΠ½ΠΎ, Π±ΠΎΠ»ΡΡΠΎΠ΅ ΠΊΠΎΠ»ΠΈΡΠ΅ΡΡΠ²ΠΎ Π±ΠΎΠ΅ΠΏΡΠΈΠΏΠ°ΡΠΎΠ² ΠΊ ΡΠ½Π΅ΡΠ³ΠΎΠΎΡΡΠΆΠΈΡΒ β ΠΌΠΎΠΆΠ½ΠΎ ΡΠ½ΡΡΡ Ρ ΡΠ½ΠΈΠΊΠ°Π»ΡΠ½ΠΎΠ³ΠΎ Π±Π΅Π·ΡΠΌΠ½ΠΎΠ³ΠΎ Π‘Π΅ΠΊΡΡΡΠΈΡΡΠΎΠ½Π° 010011110110111001100101.
- Π‘ΠΏΠΎΡΡΠΈΠ²Π½Π°Ρ ΡΡΠΌΠΊΠ°Β β ΠΏΠΎΠ΄ ΠΎΠ±Π²Π°Π»ΠΈΠ²ΡΠ΅ΠΉΡΡ ΠΏΠ»Π°ΡΡΠΎΡΠΌΠΎΠΉ, Π²ΠΎΠ·Π»Π΅ Π·Π°Π΄Π°Π²Π»Π΅Π½Π½ΠΎΠ³ΠΎ ΡΠΊΠ΅Π»Π΅ΡΠ°.
- ΠΡΡΠ½Π°Π» Β«Π’Π΅ΡΠ°ΠΏΠ΅Π²Ρ ΡΠ΅Π³ΠΎΠ΄Π½Ρ» β ΡΠΏΡΠ°Π²Π° ΠΎΡ Π²Ρ ΠΎΠ΄Π° Π² ΠΎΡΠΈΡ, Π½Π° ΠΊΠ½ΠΈΠΆΠ½ΠΎΠΉ ΠΏΠΎΠ»ΠΊΠ΅.
- ΠΠ° ΡΠ»ΠΈΡΠ΅ Π½Π° ΠΊΡΠ°ΠΉΠ½Π΅ΠΌ ΡΡΠΎΠ»Π΅ Β«Π¨ΠΊΠΎΠ»Π° Π²ΡΠΆΠΈΠ²Π°Π½ΠΈΡΒ» .
- ΠΠ΅ΡΠ°ΡΠ΅Π»ΡΠ½ΡΠΉ ΠΏΡΠΎΡΠΎΠ½Π½ΡΠΉ ΡΠΎΠΏΠΎΡΒ β 5 ΡΡ., Π² ΠΎΡΠΊΡΡΡΠΎΠΌ ΡΠΊΠ°ΡΡ Π½Π° 2-ΠΌ ΡΡΠ°ΠΆΠ΅.
- Π―Π΄Π΅ΡΠ½Π°Ρ Π±Π°ΡΠ°ΡΠ΅ΡΒ β 13 ΡΡ., Π½Π° ΡΡΠΎΠ»Π΅ Π² ΠΏΠΎΠΌΠ΅ΡΠ΅Π½ΠΈΠΈ Ρ Π½Π΅ΡΠΊΠΎΠ»ΡΠΊΠΈΠΌΠΈ ΠΊΠΎΠΌΠΏΡΡΡΠ΅ΡΠ°ΠΌΠΈ.
- Π ΠΊΠΎΠ½Π²Π΅ΠΉΠ΅ΡΠ½ΠΎΠΌ ΡΠ΅Ρ Ρ Π±ΠΎΠ»ΡΡΠΎΠ΅ ΠΊΠΎΠ»ΠΈΡΠ΅ΡΡΠ²ΠΎ Π΄Π΅ΡΠ°Π»Π΅ΠΉ Π΄Π»Ρ ΡΠ°Π±ΠΎΡΡ Π½Π° Π²Π΅ΡΡΡΠ°ΠΊΠ΅, Π° ΡΠ°ΠΊΠΆΠ΅ ΡΠ°ΠΌ Π²Π΅ΡΡΡΠ°ΠΊ.
- ΠΠ°ΡΠ°Π±ΠΈΠ½ ΡΡΡΠ΅Π»ΠΊΠ°, 2 ΡΠ°ΠΌΠΏΡΡΠ° ΡΡΡΠ°Π½Π½ΠΎΠ³ΠΎ ΠΌΡΡΠ°,5,56-ΠΌΠΌ ΠΏΠ°ΡΡΠΎΠ½Ρ, Π·Π°ΠΌΠ°ΡΠ»Π΅Π½Π½ΡΠΉ ΡΡΠΈΠΊ Ρ ΠΈΠ½ΡΡΡΡΠΌΠ΅Π½ΡΠ°ΠΌΠΈΒ β Π²ΠΎΡΡΠΎΡΠ½Π΅Π΅ Π»ΠΎΠΊΠ°ΡΠΈΠΈ, Π½Π° Π²Π΅ΡΡ Ρ ΡΠ³Π»Π° Π½Π°Π΄Π·Π΅ΠΌΠ½ΠΎΠΉ ΡΡΡΠ±Ρ, Π²ΡΡ ΠΎΠ΄ΡΡΠ΅ΠΉ ΠΈΠ· Π·Π΅ΠΌΠ»ΠΈ.
- ΠΡΠΎΠ±ΠΎΠ²ΠΈΠΊ Ρ ΡΡΡΠ°ΠΆΠ½ΠΎΠΉ ΠΏΠ΅ΡΠ΅Π·Π°ΡΡΠ΄ΠΊΠΎΠΉ, ΠΏΠ°ΡΡΠΎΠ½Ρ ΠΊ Π½Π΅ΠΌΡ, ΡΠΏΠ°Π»ΡΠ½ΠΈΠΊΒ β Π½Π° ΡΠ΅Π²Π΅ΡΠ΅ Π»ΠΎΠΊΠ°ΡΠΈΠΈ, Π² ΡΡΠΏΠΈΠΊΠ΅ ΠΌΠ΅ΠΆΠ΄Ρ ΠΊΠΎΡΠΏΡΡΠ°ΠΌΠΈ.
- ΠΡΡΠ½Π°Π» Β«Π§ΠΈΠ½ΠΈΠΌ Ρами» β Π½Π° ΡΠ΅ΠΌΠΎΠ½ΡΠ½ΠΎΠΉ ΠΊΠ°ΠΏΡΡΠ»Π΅.
Π¦Π΅Ρ ΠΏΠΎ Π΄Π΅ΠΌΠΎΠ½ΡΠ°ΠΆΡ ΡΠ΅ΠΊΡΡΡΠΈΡΡΠΎΠ½ΠΎΠ² ΠΏΠΎΡΠ²Π»ΡΠ΅ΡΡΡ ΡΠΎΠ»ΡΠΊΠΎ Π² Π΄ΠΎΠΏΠΎΠ»Π½Π΅Π½ΠΈΠΈ ΠΊ
ΠΠ°ΡΠΈΠ°Π½Ρ ΠΏΠ΅ΡΠ΅Π²ΠΎΠ΄Π° Π½Π°Π·Π²Π°Π½ΠΈΡ: Β«Π€Π°Π±ΡΠΈΠΊΠ° ΡΠ°Π·Π±ΠΎΡΠΊΠΈ ΡΠ΅ΠΊΡΡΡΠΈΡΡΠΎΠ½ΠΎΠ²Β», Β«ΠΠ°Π²ΠΎΠ΄ ΠΏΠΎ ΡΡΠΈΠ»ΠΈΠ·Π°ΡΠΈΠΈ ΡΠ΅ΠΊΡΡΡΠΈΡΡΠΎΠ½ΠΎΠ²Β».
- β ΠΠ°Π²ΠΎΠ΄ ΠΏΠΎ ΠΏΠ΅ΡΠ΅ΡΠ°Π±ΠΎΡΠΊΠ΅ ΡΠ΅ΠΊΡΡΡΠΈΡΡΠΎΠ½ΠΎΠ²Β β Π½Π° ΠΊΠ°ΡΡΠ΅ ΠΌΠ΅ΡΡΠ½ΠΎΡΡΠΈ
ru.fallout.wikia.com
Π¦Π΅Ρ ΠΏΠΎ ΠΏΡΠΎΠΈΠ·Π²ΠΎΠ΄ΡΡΠ²Ρ ΠΊΠ΅ΡΠ°ΠΌΠ·ΠΈΡΠ°
Π‘ΠΎΠ΄Π΅ΡΠΆΠ°Π½ΠΈΠ΅
1.Β ΠΠ²Π΅Π΄Π΅Π½ΠΈΠ΅………………………………………………………………………….. Β Β 3
2.Β ΠΠ±ΡΠ°Ρ ΡΠ°ΡΡΡ…………………………………………………………………….. Β Β $
2.1Β Β Π‘ΠΎΡΡΠ°Π² ΠΏΡΠ΅Π΄ΠΏΡΠΈΡΡΠΈΡ…………………………………………………………. £
2.2Β Β Β Β Β Β Β Β Β Β Β Β Β Β Β Β Β Β Β Β Β Β ΠΠΎΠΌΠ΅Π½ΠΊΠ»Π°ΡΡΡΠ° ΠΈ Ρ Π°ΡΠ°ΠΊΡΠ΅ΡΠΈΡΡΠΈΠΊΠ° ΠΏΡΠΎΠ΄ΡΠΊΡΠΈΠΈ………………………….. Π±
2.3Β Β Β Β Β Β Β Β Β Β Β Β Β Β Β Β Β Β Β Β Β Β Π₯Π°ΡΠ°ΠΊΡΠ΅ΡΠΈΡΡΠΈΠΊΠ° ΠΈΡΠΏΠΎΠ»ΡΠ·ΠΎΠ²Π°Π½Π½ΠΎΠ³ΠΎ ΡΡΡΡΡ………………………………. β’?
3.Β Β Β Β Β Β Β Β Β Β Β Β Β Π’Π΅Ρ Π½ΠΎΠ»ΠΎΠ³ΠΈΡΠ΅ΡΠΊΠ°Ρ ΡΠ°ΡΡΡ……………………………………………… (%,
3.1Β Β ΠΠ±ΠΎΡΠ½ΠΎΠ²Π°Π½ΠΈΠ΅ ΠΏΡΠΈΠ½ΡΡΠΎΠΉ ΡΠ΅Ρ Π½ΠΎΠ»ΠΎΠ³ΠΈΠΈ ΠΏΡΠΎΠΈΠ·Π²ΠΎΠ΄ΡΡΠ²Π°……………………. {%,
3.2Β Β Β Β Β Β Β Β Β Β Β Β Β Β Β Β Β Β Β Β Β Β ΠΡΠΈΠ½ΡΡΠ°Ρ ΡΠ΅Ρ Π½ΠΎΠ»ΠΎΠ³ΠΈΡΠ΅ΡΠΊΠ°Ρ ΡΠ°ΡΡΡ…………………………………………. /(/
3.3Β Β Β Β Β Β Β Β Β Β Β Β Β Β Β Β Β Β Β Β Β Β ΠΠΏΠΈΡΠ°Π½ΠΈΠ΅ ΡΠ΅Ρ Π½ΠΎΠ»ΠΎΠ³ΠΈΠΈ………………………………………………………… \$
3.4Β Β Β Β Β Β Β Β Β Β Β Β Β Β Β Β Β Β Β Β Β Β Π’Π΅Ρ Π½ΠΎΠ»ΠΎΠ³ΠΈΡΠ΅ΡΠΊΠΈΠ΅ ΡΠ΅ΠΆΠΈΠΌΡ ΠΈ ΡΠ°ΡΡΠ΅ΡΡ…………………………………….. \%
3.5Β Β Β Β Β Β Β Β Β Β Β Β Β Β Β Β Β Β Β Β Β Β ΠΡΠ±ΠΎΡ ΠΈ Ρ Π°ΡΠ°ΠΊΡΠ΅ΡΠΈΡΡΠΈΠΊΠ° ΠΎΡΠ½ΠΎΠ²Π½ΠΎΠ³ΠΎ ΡΠ΅Ρ Π½ΠΎΠ»ΠΎΠ³ΠΈΡΠ΅ΡΠΊΠΎΠ³ΠΎ ΠΎΠ±ΠΎΡΡΠ΄ΠΎΠ²Π°Π½ΠΈΡΒ Β Β Β Β Β Β %ΠΎ
3.6Β Β Β Β Β Β Β Β Β Β Β Β Β Β Β Β Β Β Β Β Β Β ΠΠΎΠ½ΡΡΠΎΠ»Ρ ΠΏΡΠΎΠΈΠ·Π²ΠΎΠ΄ΡΡΠ²Π°…………………………………………………….. %Ρ
4.Β Β Β Β Β Β Β Β ΠΠΎΡΡΠ΅Π±Π½ΠΎΡΡΡ Π² ΡΠ½Π΅ΡΠ³ΠΎΡΠ΅ΡΡΡΡΠ°Ρ
………………………………………………. Β£3
5.Β Π¨ΡΠ°ΡΠ½Π°Ρ Π²Π΅Π΄ΠΎΠΌΠΎΡΡΡ ΡΠ΅Ρ Π°……………………………………………………… Β Β£3
6.Β ΠΡ ΡΠ°Π½Π° ΡΡΡΠ΄Π° ΠΈ ΠΎΠΊΡΡΠΆΠ°ΡΡΠ΅ΠΉ ΡΡΠ΅Π΄Ρ………………………………………. & ?
7.Β Π‘ΡΡΠΎΠΈΡΠ΅Π»ΡΠ½Π°Ρ ΡΠ°ΡΡΡ……………………………………………………………. Π― #
8.Β Π’Π΅Ρ Π½ΠΈΠΊΠΎ-ΡΠΊΠΎΠ½ΠΎΠΌΠΈΡΠ΅ΡΠΊΠ°Ρ ΡΠ°ΡΡΡ………………………………………………. $0
9.Β Π‘ΠΏΠΈΡΠΎΠΊ Π»ΠΈΡΠ΅ΡΠ°ΡΡΡΡ…………………………………………………………….. 33
ΠΠ²Π΅Π΄Π΅Π½ΠΈΠ΅
ΠΡΠΏΡΡΠΈΠ²Π°Π½ΠΈΠ΅ Π³Π»ΠΈΠ½Ρ ΠΏΡΠΈ ΠΎΠ±ΠΆΠΈΠ³Π΅ ΠΈΠ·Π²Π΅ΡΡΠ½ΠΎ Ρ Π½Π΅Π·Π°ΠΏΠ°ΠΌΡΡΠ½ΡΡ
Π²ΡΠ΅ΠΌΠ΅Π½. Π‘Π°ΠΌΠΎΠΏΡΠΎΠΈΠ·Π²ΠΎΠ»ΡΠ½ΠΎΠ΅ Π²ΡΠΏΡΡΠΈΠ²Π°Π½ΠΈΠ΅ Π½Π΅ΡΠ΅Π΄ΠΊΠΎ Π½Π°Π±Π»ΡΠ΄Π°Π΅ΡΡΡ Π² ΠΊΠ΅ΡΠ°ΠΌΠΈΡΠ΅ΡΠΊΠΎΠΌ ΠΏΡΠΎΠΈΠ·Π²ΠΎΠ΄ΡΡΠ²Π΅ — ΠΎΠ±ΡΠ°Π·ΠΎΠ²Π°Π½ΠΈΠ΅ ΠΏΡΠ·ΡΡΠ΅ΠΉ, Π²Π·Π΄ΡΡΠΈΠΉ ΠΈ Π΄ΡΡΠ³ΠΈΡ
ΠΏΠΎΡΠΎΠΊΠΎΠ² ΠΈΠ·Π΄Π΅Π»ΠΈΠΉ.
Π ΡΠ΅Π·ΡΠ»ΡΡΠ°ΡΠ΅ Π²ΡΠΏΡΡΠΈΠ²Π°Π½ΠΈΡ ΠΏΠΎΠ»ΡΡΠ°Π΅ΡΡΡ Π»Π΅Π³ΠΊΠΈΠΉ ΠΏΠΎΡΠΈΠ·ΠΎΠ²Π°Π½Π½ΡΠΉ ΠΌΠ°ΡΠ΅ΡΠΈΠ°Π» Ρ ΠΌΠ΅Π»ΠΊΠΎΡΡΠ΅ΠΈΡΡΠΎΠΉ ΡΡΡΡΠΊΡΡΡΠΎΠΉ, ΠΎΠ±Π»Π°Π΄Π°ΡΡΠ΅ΠΉ ΠΌΠ°Π»ΠΎΠΉ ΠΏΠ»ΠΎΡΠ½ΠΎΡΡΡΡ ΠΏΡΠΈ Π·Π½Π°ΡΠΈΡΠ΅Π»ΡΠ½ΠΎΠΉ ΠΏΡΠΎΡΠ½ΠΎΡΡΠΈ ΠΈ Π²ΡΡΠΎΠΊΠΈΠΌΠΈ ΡΠ΅ΠΏΠ»ΠΎΠ·Π°ΡΠΈΡΠ½ΡΠΌΠΈ ΡΠ²ΠΎΠΉΡΡΠ²Π°ΠΌΠΈ.
ΠΡΠΏΡΡΠΈΠ²Π°Π½ΠΈΠ΅ Π³Π»ΠΈΠ½ ΠΏΡΠΈ ΠΎΠ±ΠΆΠΈΠ³Π΅ ΡΠ²ΡΠ·Π°Π½ΠΎ Ρ Π΄Π²ΡΠΌΡ ΠΏΡΠΎΡΠ΅ΡΡΠ°ΠΌΠΈ: Π³Π°Π·ΠΎΠ²ΡΠ΄Π΅Π»Π΅Π½ΠΈΠ΅ΠΌ ΠΈ ΠΏΠ΅ΡΠ΅Ρ ΠΎΠ΄ΠΎΠΌ Π³Π»ΠΈΠ½Ρ Π² ΠΏΠ»Π°ΡΡΠΈΡΠ΅ΡΠΊΠΎΠ΅ ΡΠΎΡΡΠΎΡΠ½ΠΈΠ΅.
ΠΡΡΠΎΡΠ½ΠΈΠΊΠ°ΠΌΠΈ Π³Π°Π·ΠΎΠ²ΡΠ΄Π΅Π»Π΅Π½ΠΈΡ ΡΠ²Π»ΡΡΡΡΡ ΡΠ΅Π°ΠΊΡΠΈΠΈ Π²ΠΎΡΡΡΠ°Π½ΠΎΠ²Π»Π΅Π½ΠΈΡ ΠΎΠΊΡΠΈΠ΄ΠΎΠ² ΠΆΠ΅Π»Π΅Π·Π° ΠΏΡΠΈ ΠΈΡ Π²Π·Π°ΠΈΠΌΠΎΠ΄Π΅ΠΉΡΡΠ²ΠΈΠΈ Ρ ΠΎΡΠ³Π°Π½ΠΈΡΠ΅ΡΠΊΠΈΠΌΠΈ ΠΏΡΠΈΠΌΠ΅ΡΡΠΌΠΈ, ΠΎΠΊΠΈΡΠ»Π΅Π½ΠΈΠ΅ ΡΡΠΈΡ ΠΏΡΠΈΠΌΠ΅ΡΠ΅ΠΉ, Π΄Π΅Π³ΠΈΠ΄ΡΠ°ΡΠ°ΡΠΈΠΈ Π³ΠΈΠ΄ΡΠΎΡΠ»ΡΠ΄ ΠΈ Π΄ΡΡΠ³ΠΈΡ Π²ΠΎΠ΄ΠΎΡΠΎΠ΄Π΅ΡΠΆΠ°ΡΠΈΡ Π³Π»ΠΈΠ½ΠΈΡΡΡΡ ΠΌΠΈΠ½Π΅ΡΠ°Π»ΠΎΠ², Π΄ΠΈΡΡΠΎΡΠΈΠ°ΡΠΈΠΈ ΠΊΠ°ΡΠ±ΠΎΠ½Π°ΡΠΎΠ² ΠΈ Ρ. Π΄. Π ΠΏΠΈΡΠΎΠΏΠ»Π°ΡΡΠΈΡΠ΅ΡΠΊΠΎΠ΅ ΡΠΎΡΡΠΎΡΠ½ΠΈΠ΅ Π³Π»ΠΈΠ½Ρ ΠΏΠ΅ΡΠ΅Ρ ΠΎΠ΄ΡΡ, ΠΊΠΎΠ³Π΄Π° ΠΏΡΠΈ Π²ΡΡΠΎΠΊΠΎΠΉ ΡΠ΅ΠΌΠΏΠ΅ΡΠ°ΡΡΡΠ΅ Π² Π½ΠΈΡ ΠΎΠ±ΡΠ°Π·ΡΠ΅ΡΡΡ ΠΆΠΈΠ΄ΠΊΠ°Ρ ΡΠ°Π·Π° (ΡΠ°ΡΠΏΠ»Π°Π²), Π² ΡΠ΅Π·ΡΠ»ΡΡΠ°ΡΠ΅ ΡΠ΅Π³ΠΎ Π³Π»ΠΈΠ½Π° ΡΠ°Π·ΠΌΡΠ³ΡΠ°Π΅ΡΡΡ, ΠΏΡΠΈΠΎΠ±ΡΠ΅ΡΠ°Π΅Ρ ΡΠΏΠΎΡΠΎΠ±Π½ΠΎΡΡΡ ΠΊ ΠΏΠ»Π°ΡΡΠΈΡΠ΅ΡΠΊΠΎΠΉ Π΄Π΅ΡΠΎΡΠΌΠ°ΡΠΈΠΈ, Π² ΡΠΎ ΠΆΠ΅ Π²ΡΠ΅ΠΌΡ ΡΡΠ°Π½ΠΎΠ²ΠΈΡΡΡ Π³Π°Π·ΠΎΠ½Π΅ΠΏΡΠΎΠ½ΠΈΡΠ°Π΅ΠΌΠΎΠΉ ΠΈ Π²ΡΠΏΡΡΠΈΠ²Π°Π΅ΡΡΡ Π²ΡΠ΄Π΅Π»ΡΡΡΠΈΠΌΠΈ Π³Π°Π·Π°ΠΌΠΈ.
Π ΠΎΡΠ»ΠΈΡΠΈΠ΅ ΠΎΡ ΠΏΠ»ΠΎΡΠ½ΡΡ , ΠΏΠΎΡΠΈΡΡΡΡ ΠΈ ΠΏΡΡΡΠΎΡΠ΅Π»ΡΡ ΠΊΠ΅ΡΠ°ΠΌΠΈΡΠ΅ΡΠΊΠΈΡ ΠΌΠ°ΡΠ΅ΡΠΈΠ°Π»ΠΎΠ² ΠΈ ΠΈΠ·Π΄Π΅Π»ΠΈΠΉ, Π²ΡΡΠ°Π±Π°ΡΡΠ²Π°Π΅ΠΌΡΡ ΠΈΠ· Π³Π»ΠΈΠ½, Π²ΡΠΏΡΡΠ΅Π½Π½ΡΠΉ ΠΏΡΠΈ ΠΎΠ±ΠΆΠΈΠ³Π΅ Π³Π»ΠΈΠ½ΠΈΡΡΡΡ ΠΏΠΎΡΠΎΠ΄ ΠΌΠ°ΡΠ΅ΡΠΈΠ°Π» ΡΡΠ΅ΠΈΡΡΠΎΠ³ΠΎ ΡΡΡΠΎΠ΅Π½ΠΈΡ Π½Π°Π·ΡΠ²Π°ΡΡ ΠΊΠ΅ΡΠ°ΠΌΠ·ΠΈΡΠΎΠΌ.
Π’Π΅ΡΠΌΠΈΠ½ ΠΊΠ΅ΡΠ°ΠΌΠ·ΠΈΡ ΠΎΠ±ΠΎΠ·Π½Π°ΡΠ°Π΅Ρ Π½Π΅ ΠΊΠ°ΠΊΠΎΠΉ-Π»ΠΈΠ±ΠΎ Π²ΠΈΠ΄ Π³ΠΎΡΠΎΠ²ΠΎΠ³ΠΎ ΠΌΠ°ΡΠ΅ΡΠΈΠ°Π»Π° ΠΈΠ»ΠΈ ΠΈΠ·Π΄Π΅Π»ΠΈΡ, Π° Π²ΡΠΏΡΡΠ΅Π½Π½ΡΡ ΠΏΡΠΈ ΠΎΠ±ΠΆΠΈΠ³Π΅ Π³Π»ΠΈΠ½ΠΈΡΡΡΡ ΠΏΠΎΡΠΎΠ΄ ΠΌΠ°ΡΡΡ ΡΡΠ΅ΠΈΡΡΠΎΠ³ΠΎ ΡΡΡΠΎΠ΅Π½ΠΈΡ. ΠΠ°Π·Π²Π°Π½ΠΈΠ΅ ΠΆΠ΅ Π³ΠΎΡΠΎΠ²ΡΡ Π²ΠΈΠ΄ΠΎΠ² ΠΌΠ°ΡΠ΅ΡΠΈΠ°Π»Π° ΠΎΠ±ΡΠ°Π·ΡΠ΅ΡΡΡ ΠΏΠΎ ΠΎΠ±ΡΠ΅ΠΏΡΠΈΠ½ΡΡΠΎΠΌΡ Π² ΡΠ΅Ρ Π½ΠΈΠΊΠ΅ ΡΠ»ΠΎΠ²ΠΎΡΠΎΡΠ΅ΡΠ°Π½ΠΈΡ ΠΌΠ°ΡΠ΅ΡΠΈΠ°Π» -Π³ΠΎΡΠΎΠ²ΡΠΉ ΠΏΡΠΎΠ΄ΡΠΊΡ. ΠΠ°ΠΏΡΠΈΠΌΠ΅Ρ, ΡΡΠ°Π»ΡΠ½Π°Ρ ΠΏΡΠΎΠ²ΠΎΠ»ΠΎΠΊΠ°, ΡΡΠ°Π»ΡΠ½ΠΎΠΉ ΡΠ΅Π»ΡΡ, Π² ΡΠ°ΡΡΠΌΠ°ΡΡΠΈΠ²Π°Π΅ΠΌΠΎΠΌ ΡΠ»ΡΡΠ°Π΅ — ΠΊΠ΅ΡΠ°ΠΌΠ·ΠΈΡΠΎΠ²ΡΠΉ Π³ΡΠ°Π²ΠΈΠΉ, ΠΊΠ΅ΡΠ°ΠΌΠ·ΠΈΡΠΎΠ²ΡΠΉ ΠΏΠ΅ΡΠΎΠΊ, ΠΊΠ΅ΡΠ°ΠΌΠ·ΠΈΡΠΎΠ²ΡΠ΅ Π±Π»ΠΎΠΊΠΈ, ΠΊΠ΅ΡΠ°ΠΌΠ·ΠΈΡΠΎΠ²ΡΠΉ ΡΠ΅Π±Π΅Π½Ρ ΠΈ Ρ. Π΄.
ΠΠ»ΠΈΡΠ΅Π»ΡΠ½ΡΠΉ ΠΎΠΏΡΡ ΠΎΡΠ²ΠΎΠ΅Π½ΠΈΡ ΠΊΠ΅ΡΠ°ΠΌΠ·ΠΈΡΠ° ΠΏΠΎΠΊΠ°Π·Π°Π», ΡΡΠΎ ΠΌΠ΅ΡΠΎΠ΄Ρ Π΅Π³ΠΎ ΠΏΠΎΠ»ΡΡΠ΅Π½ΠΈΡ, Π° ΡΠ°ΠΊΠΆΠ΅ ΠΎΠ±Π»Π°ΡΡΠΈ ΠΈΡΠΏΠΎΠ»ΡΠ·ΠΎΠ²Π°Π½ΠΈΡ Π΅Π³ΠΎ ΡΠ΅Ρ Π½ΠΈΡΠ΅ΡΠΊΠΈΡ ΡΠ²ΠΎΠΉΡΡΠ²
ΠΌΠΎΠ³ΡΡ Π±ΡΡΡ ΡΠ°ΠΌΡΠΌΠΈ ΡΠ°Π·Π½ΠΎΠΎΠ±ΡΠ°Π·Π½ΡΠΌΠΈ. Π‘ ΡΠ°Π·Π²ΠΈΡΠΈΠ΅ΠΌ Π½Π°ΡΠΊΠΈ ΠΈ ΡΠ΅Ρ
Π½ΠΈΠΊΠΈ ΠΎΠ½ΠΈ Π½Π΅ΠΏΡΠ΅ΡΡΠ²Π½ΠΎ ΡΠΎΠ²Π΅ΡΡΠ΅Π½ΡΡΠ²ΡΡΡΡΡ ΠΈ ΡΠ°ΡΡΠΈΡΡΡΡΡΡ. Π’Π°ΠΊ, Π΅ΡΠ»ΠΈ Π² ΠΏΠ΅ΡΠΈΠΎΠ΄ Π·Π°ΡΠΎΠΆΠ΄Π΅Π½ΠΈΡ ΠΏΡΠΎΠΌΡΡΠ»Π΅Π½Π½ΠΎΡΡΠΈ ΠΊΠ΅ΡΠ°ΠΌΠ·ΠΈΡΠ° Π²ΡΠΏΡΡΠΈΠ²Π°Π½ΠΈΡ Π³Π»ΠΈΠ½ Π²Π΅Π»ΠΈ Π² Π³ΠΎΡΠ½Π°Ρ
ΠΏΠ΅ΡΠΈΠΎΠ΄ΠΈΡΠ΅ΡΠΊΠΎΠ³ΠΎ Π΄Π΅ΠΉΡΡΠ²ΠΈΡ ΠΈ ΡΡΠ½Π½Π΅Π»ΡΠ½ΡΡ
ΠΏΠ΅ΡΠ°Ρ
ΠΈ Π½Π° ΡΠ΅ΡΠ΅ΡΠΊΠ°Ρ
Ρ ΠΏΡΠΈΠ½ΡΠ΄ΠΈΡΠ΅Π»ΡΠ½ΡΠΌ ΠΏΡΠΎΡΠΎΡΠΎΠΌ Π²ΠΎΠ·Π΄ΡΡ
Π°, ΡΠΎ Π² Π½Π°ΡΡΠΎΡΡΠ΅Π΅ Π²ΡΠ΅ΠΌΡ ΠΏΡΠ΅Π΄Π»ΠΎΠΆΠ΅Π½Ρ ΠΈ Π²Π½Π΅Π΄ΡΡΡΡΡΡ Π½ΠΎΠ²ΡΠ΅ ΠΏΠ΅ΡΡΠΏΠ΅ΠΊΡΠΈΠ²Ρ ΠΌΠ΅ΡΠΎΠ΄Ρ Π²ΡΠΏΡΡΠΈΠ²Π°Π½ΠΈΡ: Π² Π΄Π²ΡΡ
Π±Π°ΡΠ°Π±Π°Π½Π½ΡΡ
ΠΏΠ΅ΡΠ°Ρ
, Π² ΠΊΠΈΠΏΡΡΠ΅ΠΌ ΡΠ»ΠΎΠ΅, Π² ΠΊΠΎΠ»ΡΡΠ΅Π²ΡΡ
, ΡΠ°Ρ
ΡΠ½ΡΡ
ΠΈ Π΄ΡΡΠ³ΠΈΡ
ΠΏΠ΅ΡΠ°Ρ
.
Π ΠΏΠΎΡΠ»Π΅Π΄Π½ΠΈΠ΅ Π΄Π΅ΡΡΡΠΈΠ»Π΅ΡΠΈΡ Π² ΠΏΡΠΎΠΈΠ·Π²ΠΎΠ΄ΡΡΠ²ΠΎ ΠΊΠ΅ΡΠ°ΠΌΠ·ΠΈΡΠΎΠ²ΠΎΠ³ΠΎ Π³ΡΠ°Π²ΠΈΡ Π½Π°ΡΡΠ΄Ρ Ρ ΠΊΠ»Π°ΡΡΠΈΡΠ΅ΡΠΊΠΈΠΌΠΈ Π»Π΅Π³ΠΊΠΎΠΏΠ»Π°Π²ΠΊΠΈΠΌΠΈ Π³Π»ΠΈΠ½ΠΈΡΡΡΠΌΠΈ ΠΏΠΎΡΠΎΠ΄Π°ΠΌΠΈ Π²ΠΎΠ²Π»Π΅ΠΊΠ°ΡΡΡΡ ΡΠ°Π·Π»ΠΈΡΠ½ΡΠ΅ ΠΎΡΡ ΠΎΠ΄Ρ ΡΠ³Π»Π΅ΠΎΠ±ΠΎΠ³Π°ΡΠ΅Π½ΠΈΡ, Π·ΠΎΠ»Ρ ΠΈ ΡΠ»Π°ΠΊΠΈ ΡΠ΅ΠΏΠ»ΠΎΠ²ΡΡ ΡΠ»Π΅ΠΊΡΡΠΎΡΡΠ°Π½ΡΠΈΠΉ, Π° ΡΠ°ΠΊΠΆΠ΅ ΡΡΠ΅ΠΏΠ΅Π»Π°, Π΄ΠΈΠ°ΡΠΎΠΌΠΈΡΡ Ρ. Π΄.
ΠΠΌΠ΅ΡΡΠ΅ Ρ ΡΠ΅ΠΌ, Π½Π΅ΡΠΌΠΎΡΡΡ Π½Π° ΠΎΡΠ΅Π²ΠΈΠ΄Π½ΡΠ΅ ΡΡΠΏΠ΅Ρ
ΠΈ Π² ΠΎΡΠ³Π°Π½ΠΈΠ·Π°ΡΠΈΠΈ ΠΏΡΠΎΠΈΠ·Π²ΠΎΠ΄ΡΡΠ²Π° ΠΈ ΠΏΡΠΈΠΌΠ΅Π½Π΅Π½ΠΈΠΈ ΠΊΠ΅ΡΠ°ΠΌΠ·ΠΈΡΠ°, ΡΠ΅Ρ
Π½ΠΈΡΠ΅ΡΠΊΠΈΠΉ ΡΡΠΎΠ²Π΅Π½Ρ Π΄Π΅ΠΉΡΡΠ²ΡΡΡΠΈΡ
ΠΊΠ΅ΡΠ°ΠΌΠ·ΠΈΡΠΎΠ²ΡΡ
ΠΏΡΠ΅Π΄ΠΏΡΠΈΡΡΠΈΠΉ ΠΈ ΠΊΠ°ΡΠ΅ΡΡΠ²ΠΎ Π²ΡΠΏΡΡΠΊΠ°Π΅ΠΌΠΎΠΉ ΠΈΠΌΠΈ ΠΏΡΠΎΠ΄ΡΠΊΡΠΈΠΈ, ΠΎΡΠΎΠ±Π΅Π½Π½ΠΎ Π² ΠΏΠΎΡΠ»Π΅Π΄Π½Π΅Π΅ Π΄Π΅ΡΡΡΠΈΠ»Π΅ΡΠΈΠ΅, Π΄Π°Π»Π΅ΠΊΠΎ Π½Π΅ ΠΎΡΠ²Π΅ΡΠ°ΡΡ Π²ΠΎΠ·ΡΠΎΡΡΠΈΠΌ ΡΡΠ΅Π±ΠΎΠ²Π°Π½ΠΈΡΠΌ ΡΠΎΠ²ΡΠ΅ΠΌΠ΅Π½Π½ΠΎΠΉ ΡΡΡΠΎΠΈΡΠ΅Π»ΡΠ½ΠΎΠΉ ΠΈΠ½Π΄ΡΡΡΡΠΈΠΈ.
Β Β Β Β Β Β Β Β Β Β Β Β Β Β Β Β Β Β Β Β Β Β Β Β Β 2. ΠΠ±ΡΠ°Ρ ΡΠ°ΡΡΡ
2.1. Π‘ΠΎΡΡΠ°Π² ΠΏΡΠ΅Π΄ΠΏΡΠΈΡΡΠΈΡ
Π Π΄Π°Π½Π½ΠΎΠΌ ΡΠ°Π·Π΄Π΅Π»Π΅ ΠΌΡ Π΄Π°Π΅ΠΌ ΠΏΡΠ΅Π΄ΡΡΠ°Π²Π»Π΅Π½ΠΈΠ΅ ΠΎΠ± ΠΎΡΠ΄Π΅Π»Π΅Π½ΠΈΡΡ , Π² ΠΊΠΎΡΠΎΡΡΡ ΠΈΡΠΏΠΎΠ»Π½ΡΡΡΡΡ ΠΎΡΠ΄Π΅Π»ΡΠ½ΡΠ΅ ΡΠ΅Ρ Π½ΠΎΠ»ΠΎΠ³ΠΈΡΠ΅ΡΠΊΠΈΠ΅ ΠΎΠΏΠ΅ΡΠ°ΡΠΈΠΈ, ΠΊΠΎΡΠΎΡΡΠ΅ ΡΠΎΡΡΠ°Π²Π»ΡΡΡ ΠΏΡΠΎΠΈΠ·Π²ΠΎΠ΄ΡΡΠ²ΠΎ, ΠΊΠΎΡΠΎΡΠΎΠ΅ ΠΏΡΠΎΠ΅ΠΊΡΠΈΡΡΠ΅ΡΡΡ.
ΠΡΠΈ ΠΏΡΠΎΠΈΠ·Π²ΠΎΠ΄ΡΡΠ²Π΅ ΠΊΠ΅ΡΠ°ΠΌΠ·ΠΈΡΠ° ΠΎΡΠ½ΠΎΠ²Π½ΡΠΌΠΈ ΡΠ΅Ρ Π½ΠΎΠ»ΠΎΠ³ΠΈΡΠ΅ΡΠΊΠΈΠΌΠΈ ΠΎΡΠ΄Π΅Π»Π΅Π½ΠΈΡΠΌΠΈ ΡΠ²Π»ΡΡΡΡΡ ΡΠ°ΠΊΠΈΠ΅ ΠΊΠ°ΠΊ:
—Β Β ΡΠΊΠ»Π°Π΄ ΡΡΡΡΡ;
—Β Β ΠΏΠΎΠ΄Π³ΠΎΡΠΎΠ²ΠΈΡΠ΅Π»ΡΠ½ΠΎΠ΅ ΠΎΡΠ΄Π΅Π»Π΅Π½ΠΈΠ΅;
—Β Β ΠΎΡΠ΄Π΅Π»Π΅Π½ΠΈΠ΅ ΡΠ΅ΠΏΠ»ΠΎΠ²ΠΎΠΉ ΠΎΠ±ΡΠ°Π±ΠΎΡΠΊΠΈ;
—Β Β ΡΠΎΡΡΠΈΡΠΎΠ²ΠΎΡΠ½ΠΎΠ΅ ΠΎΡΠ΄Π΅Π»Π΅Π½ΠΈΠ΅;
—Β Β ΡΠΊΠ»Π°Π΄ Π³ΠΎΡΠΎΠ²ΠΎΠΉ ΠΏΡΠΎΠ΄ΡΠΊΡΠΈΠΈ (ΡΠΈΠ»ΠΎΡΠ°)
ΠΠ° ΡΠΊΠ»Π°Π΄Π΅ ΡΡΡΡΡ Ρ ΡΠ°Π½ΡΡΡΡ ΠΌΠ°ΡΠ΅ΡΠΈΠ°Π»Ρ, ΠΊΠΎΡΠΎΡΠΎΠ΅ Π½Π΅ΠΎΠ±Ρ ΠΎΠ΄ΠΈΠΌΠΎ Π΄Π»Ρ ΠΏΡΠΎΠΈΠ·Π²ΠΎΠ΄ΡΡΠ²Π° ΠΊΠ΅ΡΠ°ΠΌΠ·ΠΈΡΠ°: Π³Π»ΠΈΠ½Π°, ΡΠ³ΠΎΠ»Ρ ΠΈ Π²ΠΎΠ΄Π°. ΠΠ»ΠΈΠ½Ρ ΠΌΠΎΠΆΠ½ΠΎ Ρ ΡΠ°Π½ΠΈΡΡ Π² ΠΎΡΠΊΡΡΡΡΡ ΡΠΊΠ»Π°Π΄Π°Ρ . ΠΠΎΠ΄Ρ Π² ΡΠΏΠ΅ΡΠΈΠ°Π»ΡΠ½ΠΎ ΠΏΡΠ΅Π΄Π½Π°Π·Π½Π°ΡΠ΅Π½Π½ΡΡ Π΄Π»Ρ Π½Π΅Π΅ Π΅ΠΌΠΊΠΎΡΡΡΡ .
ΠΠΎΠ΄Π³ΠΎΡΠΎΠ²ΠΈΡΠ΅Π»ΡΠ½ΠΎΠ΅Β Β ΠΎΡΠ΄Π΅Π»Π΅Π½ΠΈΠ΅Β Β Π²ΠΊΠ»ΡΡΠ°Π΅ΡΒ Β Π²Β Β ΡΠ΅Π±Ρ ΠΏΠ΅ΡΠ²ΠΈΡΠ½ΡΡ ΠΏΠ΅ΡΠ΅ΡΠ°Π±ΠΎΡΠΊΡ,Β Β Β Β ΠΏΡΠΈΠ³ΠΎΡΠΎΠ²Π»Π΅Π½ΠΈΠ΅Β Β Β Β Π³Π»ΠΈΠ½ΡΠ½ΠΎΠ³ΠΎΒ Β Β Β ΡΠ΅ΡΡΠ°, ΡΠΎΡΠΌΠΎΠ²Π°Π½ΠΈΠ΅ ΡΡΡΡΠΎΠ²ΡΡ Π³ΡΠ°Π½ΡΠ» ΠΈ ΠΎΠΏΡΠ΄ΡΠΈΠ²Π°Π½ΠΈΠ΅ (ΡΡΡ ΠΎΠΉ Π³Π»ΠΈΠ½ΠΎΠΉ).
ΠΒ Β Β ΠΎΡΠ΄Π΅Π»Π΅Π½ΠΈΡΒ Β Β ΡΠ΅ΠΏΠ»ΠΎΠ²ΠΎΠΉΒ Β Β ΠΎΠ±ΡΠ°Π±ΠΎΡΠΊΠΈΒ Β Β ΠΎΡΠ½ΠΎΡΡΡΡΡ ΡΡΡΠΊΠ° Π²ΠΎ Β Π²ΡΠ°ΡΠ°ΡΡΠ΅ΠΌΒ Β Β Β Π±Π°ΡΠ°Π±Π°Π½Π΅Β Β Β Β (WΠ½Π°Ρ=15-16%, WΠΊΠΎΠ½=3%) ΠΎΠ±ΠΆΠΈΠ³ Π²ΠΎ Π²ΡΠ°ΡΠ°ΡΡΠ΅ΠΉ ΠΏΠ΅ΡΠΈ (t ΠΎΠ±ΠΆ. =1200-1250Β°Π‘) ΠΈ ΠΎΡ Π»Π°ΠΆΠ΄Π΅Π½ΠΈΠ΅ Π² ΡΠΏΠ΅ΡΠΈΠ°Π»ΡΠ½ΡΡ Ρ ΠΎΠ»ΠΎΠ΄ΠΈΠ»ΡΠ½ΠΈΠΊΠ°Ρ ( ΠΎΡ t Π½Π°Ρ.=900Β°Π‘ Π΄ΠΎ t ΠΊΠΎΠ½. =50-60Β°Π‘).
Π ΡΠΎΡΡΠΈΡΠΎΠ²ΠΎΡΠ½ΠΎΠΌ ΠΎΡΠ΄Π΅Π»Π΅Π½ΠΈΠΈ Π½Π°Ρ ΠΎΠ΄ΠΈΡΡΡ Π³ΡΠΎΡ ΠΎΡ, ΠΊΠΎΡΠΎΡΡΠΉ Π΄Π΅Π»ΠΈΡ ΡΠΆΠ΅ Π³ΠΎΡΠΎΠ²ΡΠΉ ΠΏΡΠΎΠ΄ΡΠΊΡ ΠΏΠΎ ΠΊΡΡΠΏΠ½ΠΎΡΡΠΈ Π½Π° ΡΡΠ°ΠΊΡΠΈΠΈ: Π΄ΠΎ 5ΠΌΠΌ, 5-10ΠΌΠΌ, 10-20ΠΌΠΌ, 20-40ΠΌΠΌ.
ΠΠΎΡΠ»Π΅ ΡΠΎΡΡΠΈΡΠΎΠ²ΠΊΠΈ ΠΊΠ΅ΡΠ°ΠΌΠ·ΠΈΡ ΠΏΠΎΡΡΡΠΏΠ°Π΅Ρ Π½Π° ΡΠΊΠ»Π°Π΄ Π³ΠΎΡΠΎΠ²ΠΎΠΉ ΠΏΡΠΎΠ΄ΡΠΊΡΠΈΠΈ Ρ. Π΅. Π² ΡΠΈΠ»ΠΎΡΠ°, Π³Π΄Π΅ ΠΊΠ°ΠΆΠ΄Π°Ρ ΡΡΠ°ΠΊΡΠΈΡ Ρ
ΡΠ°Π½ΠΈΡΡΡ Π² ΠΎΡΠ΄Π΅Π»ΡΠ½ΡΡ
ΡΠΈΠ»ΠΎΡΠ°Ρ
Π² Π·Π°Π²ΠΈΡΠΈΠΌΠΎΡΡΠΈ ΠΎΡ Π΅Π΅ ΡΠ°Π·ΠΌΠ΅ΡΠ°. ΠΠ°ΡΠ΅ΠΌ Π΅Π³ΠΎ ΡΠΆΠ΅ ΡΡΠ°Π½ΡΠΏΠΎΡΡΠΈΡΡΡΡ Π·Π°ΠΊΠ°Π·ΡΠΈΠΊΡ Π² Π·Π°Π²ΠΈΡΠΈΠΌΠΎΡΡΠΈ ΠΎΡ ΡΠ°ΡΡΡΠΎΡΠ½ΠΈΡ Π°Π²ΡΠΎΠΌΠ°ΡΠΈΠ½Π°ΠΌΠΈ ΠΈΠ»ΠΈ ΠΆΠ΅Π»Π΅Π·Π½ΠΎΠ΄ΠΎΡΠΎΠΆΠ½ΡΠΌΠΈ Π²Π°Π³ΠΎΠ½Π°ΠΌΠΈ.
2.2. ΠΠΎΠΌΠ΅Π½ΠΊΠ»Π°ΡΡΡΠ° ΠΈ Ρ
Π°ΡΠ°ΠΊΡΠ΅ΡΠΈΡΡΠΈΠΊΠ° ΠΏΡΠΎΠ΄ΡΠΊΡΠΈΠΈ
Π‘ΠΎΠ³Π»Π°ΡΠ½ΠΎ ΠΠΠ‘Π’ 9759-83 ΠΏΡΠ΅Π΄ΡΡΠΌΠΎΡΡΠ΅Π½Ρ ΡΠ»Π΅Π΄ΡΡΡΠΈΠ΅ ΡΡΠ°ΠΊΡΠΈΠΈ ΠΊΠ΅ΡΠ°ΠΌΠ·ΠΈΡΠΎΠ²ΠΎΠ³ΠΎ Π³ΡΠ°Π²ΠΈΡ ΠΏΠΎ ΠΊΡΡΠΏΠ½ΠΎΡΡΠΈ Π·Π΅ΡΠ΅Π½: 5… 10, 10…20, ΠΈ 20…40ΠΌΠΌ. Π ΠΊΠ°ΠΆΠ΄ΠΎΠΉ ΡΡΠ°ΠΊΡΠΈΠΈ Π΄ΠΎΠΏΡΡΠΊΠ°Π΅ΡΡΡ Π΄ΠΎ 10% Π±ΠΎΠ»Π΅Π΅ ΠΊΡΡΠΏΠ½ΡΡ
Π·Π΅ΡΠ΅Π½ ΠΏΠΎ ΡΡΠ°Π²Π½Π΅Π½ΠΈΡ Ρ Π½ΠΎΠΌΠΈΠ½Π°Π»ΡΠ½ΡΠΌΠΈ ΡΠ°Π·ΠΌΠ΅ΡΠ°ΠΌΠΈ. ΠΠ·-Π·Π° Π½Π΅Π²ΡΡΠΎΠΊΠΎΠΉ ΡΡΡΠ΅ΠΊΡΠΈΠ²Π½ΠΎΡΡΠΈ Π³ΡΠΎΡ
ΠΎΡΠ΅Π½ΠΈΡ ΠΌΠ°ΡΠ΅ΡΠΈΠ°Π»Π° Π² Π±Π°ΡΠ°Π±Π°Π½Π½ΡΡ
Π³ΡΠΎΡ
ΠΎΡΠ°Ρ
ΡΡΡΠ΄Π½ΠΎ Π΄ΠΎΠ±ΠΈΡΡΡΡ Π±ΠΎΠ»Π΅Π΅ ΡΡΠ°ΡΠ΅Π»ΡΠ½ΠΎΠ³ΠΎ ΡΠ°Π·Π΄Π΅Π»Π΅Π½ΠΈΡ ΠΊΠ΅ΡΠ°ΠΌΠ·ΠΈΡΠ° Π½Π° ΡΡΠ°ΠΊΡΠΈΠΈ.
ΠΠΎ Π½Π°ΡΡΠΏΠ½ΠΎΠΉ ΠΏΠ»ΠΎΡΠ½ΠΎΡΡΠΈ ΠΊΠ΅ΡΠ°ΠΌΠ·ΠΈΡΠΎΠ²ΡΠΉ Π³ΡΠ°Π²ΠΈΠΉ ΠΏΠΎΠ΄ΡΠ°Π·Π΄Π΅Π»ΡΠ΅ΡΡΡ Π½Π° 8 ΠΌΠ°ΡΠΎΠΊ: Π250…600, ΠΏΡΠΈΡΠ΅ΠΌ ΠΊ Π250 ΠΎΡΠ½ΠΎΡΠΈΡΡΡ ΠΊΠ΅ΡΠ°ΠΌΠ·ΠΈΡΠΎΠ²ΡΠΉ Π³ΡΠ°Π²ΠΈΠΉ Ρ Π½Π°ΡΡΠΏΠ½ΠΎΠΉ ΠΏΠ»ΠΎΡΠ½ΠΎΡΡΡΡ Π΄ΠΎ 250 ΠΊΠ³/ΠΌ3, ΠΊ ΠΠΠΠ — Π΄ΠΎ 300 ΠΊΠ³/ΠΌ3 ΠΈ Ρ. Π΄. ΠΠ°ΡΡΠΏΠ½ΡΡ ΠΏΠ»ΠΎΡΠ½ΠΎΡΡΡ ΠΎΠΏΡΠ΅Π΄Π΅Π»ΡΡΡ ΠΏΠΎ ΡΡΠ°ΠΊΡΠΈΡΠΌ Π² ΠΌΠ΅ΡΠ½ΡΡ ΡΠΎΡΡΠ΄Π°Ρ . Π§Π΅ΠΌ ΠΊΡΡΠΏΠ½Π΅Π΅ ΡΡΠ°ΠΊΡΠΈΡ ΠΊΠ΅ΡΠ°ΠΌΠ·ΠΈΡΠΎΠ²ΠΎΠ³ΠΎ Π³ΡΠ°Π²ΠΈΡ, ΡΠ΅ΠΌ, ΠΊΠ°ΠΊ ΠΏΡΠ°Π²ΠΈΠ»ΠΎ, ΠΌΠ΅Π½ΡΡΠ΅ Π½Π°ΡΡΠΏΠ½Π°Ρ ΠΏΠ»ΠΎΡΠ½ΠΎΡΡΡ, ΠΏΠΎΡΠΊΠΎΠ»ΡΠΊΡ ΠΊΡΡΠΏΠ½ΡΠ΅ ΡΡΠ°ΠΊΡΠΈΠΈ ΡΠΎΠ΄Π΅ΡΠΆΠ°Ρ Π½Π°ΠΈΠ±ΠΎΠ»Π΅Π΅ Π²ΡΠΏΡΡΠ΅Π½Π½ΡΠ΅ Π³ΡΠ°Π½ΡΠ»Ρ.
ΠΠ»Ρ ΠΊΠ°ΠΆΠ΄ΠΎΠΉ ΠΌΠ°ΡΠΊΠΈ ΠΏΠΎ Π½Π°ΡΡΠΏΠ½ΠΎΠΉ ΠΏΠ»ΠΎΡΠ½ΠΎΡΡΠΈ ΡΡΠ°Π½Π΄Π°ΡΡ ΡΡΡΠ°Π½Π°Π²Π»ΠΈΠ²Π°Π΅Ρ ΡΡΠ΅Π±ΠΎΠ²Π°Π½ΠΈΡ ΠΊ ΠΏΡΠΎΡΠ½ΠΎΡΡΠΈ ΠΊΠ΅ΡΠ°ΠΌΠ·ΠΈΡΠΎΠ²ΠΎΠ³ΠΎ Π³ΡΠ°Π²ΠΈΡ ΠΏΡΠΈ ΡΠ΄Π°Π²Π»ΠΈΠ²Π°Π½ΠΈΠΈ Π² ΡΠΈΠ»ΠΈΠ½Π΄ΡΠ΅. ΠΠΎ Π·Π°ΠΊΠ°Π·Π°ΠΌ ΠΏΠΎΡΡΠ΅Π±ΠΈΡΠ΅Π»Π΅ΠΉ Π΄Π»Ρ ΠΏΡΠΈΠ³ΠΎΡΠΎΠ²Π»Π΅Π½ΠΈΡ ΠΊΠΎΠ½ΡΡΡΡΠΊΡΠΈΠΎΠ½Π½ΡΡ Π»Π΅Π³ΠΊΠΈΡ Π±Π΅ΡΠΎΠ½ΠΎΠ² ΡΡΠ°Π½Π΄Π°ΡΡ Π΄ΠΎΠΏΡΡΠΊΠ°Π΅Ρ Π²ΡΠΏΡΡΠΊ ΠΊΠ΅ΡΠ°ΠΌΠ·ΠΈΡΠ½ΠΎΠ³ΠΎ Π³ΡΠ°Π²ΠΈΡ ΡΠ°ΠΊ ΠΆΠ΅ Π700 ΠΈ 800 Ρ ΠΏΡΠΎΡΠ½ΠΎΡΡΡΡ ΠΏΡΠΈ ΡΠ΄Π°Π²Π»ΠΈΠ²Π°Π½ΠΈΠΈ Π² ΡΠΈΠ»ΠΈΠ½Π΄ΡΠ΅ ΡΠΎΠΎΡΠ²Π΅ΡΡΡΠ²Π΅Π½Π½ΠΎ Π½Π΅ ΠΌΠ΅Π½Π΅Π΅ 3,3 ΠΈ 4,5 ΠΠΠ°.
Π‘ΡΠ°Π½Π΄Π°ΡΡΠ½Π°Ρ ΠΌΠ΅ΡΠΎΠ΄ΠΈΠΊΠ° ΠΏΡΠ΅Π΄ΡΡΠΌΠ°ΡΡΠΈΠ²Π°Π΅Ρ ΡΠ²ΠΎΠ±ΠΎΠ΄Π½ΡΡ Π·Π°ΡΡΠΏΠΊΡ ΠΊΠ΅ΡΠ°ΠΌΠ·ΠΈΡΠΎΠ²ΠΎΠ³ΠΎ Π³ΡΠ°Π²ΠΈΡ Π² ΡΠΈΠ»ΠΈΠ½Π΄Ρ Π° Π·Π°ΡΠ΅ΠΌ ΡΠ΄Π°Π²Π»ΠΈΠ²Π°Π½ΠΈΠ΅ Π΅Π³ΠΎ Ρ ΡΠΌΠ΅Π½ΡΡΠ΅Π½ΠΈΠ΅ΠΌ ΠΏΠ΅ΡΠ²ΠΎΠ½Π°ΡΠ°Π»ΡΠ½ΠΎΠ³ΠΎ ΠΎΠ±ΡΠ΅ΠΌΠ° Π½Π° 20%. ΠΠΎΠ΄ Π΄Π΅ΠΉΡΡΠ²ΠΈΠ΅ΠΌ Π½Π°Π³ΡΡΠ·ΠΊΠΈ ΠΏΡΠ΅ΠΆΠ΄Π΅ Π²ΡΠ΅Π³ΠΎ ΠΏΡΠΎΠΈΡΡ ΠΎΠ΄ΠΈΡ ΡΠΏΠ»ΠΎΡΠ½Π΅Π½ΠΈΠ΅ Π³ΡΠ°Π²ΠΈΡ Π·Π° ΡΡΠ΅Ρ Π½Π΅ΠΊΠΎΡΠΎΡΠΎΠ³ΠΎ ΡΠΌΠ΅ΡΠ΅Π½ΠΈΡ Π·Π΅ΡΠ΅Π½ ΠΈ ΠΈΡ Π±ΠΎΠ»Π΅Π΅ ΠΊΠΎΠΌΠΏΠ°ΠΊΡΠ½ΠΎΠΉ ΡΠΊΠ»Π°Π΄ΠΊΠΈ. ΠΡΠ½ΠΎΠ²ΡΠ²Π°ΡΡΡ Π½Π° ΠΎΠΏΡΡΠ½ΡΡ Π΄Π°Π½Π½ΡΡ , ΠΌΠΎΠΆΠ½ΠΎ ΠΏΠΎΠ»Π°Π³Π°ΡΡ, ΡΡΠΎ Π·Π° ΡΡΠ΅Ρ Π±ΠΎΠ»Π΅Π΅ ΠΏΠ»ΠΎΡΠ½ΠΎΠΉ ΡΠΊΠ»Π°Π΄ΠΊΠΈ ΠΊΠ΅ΡΠ°ΠΌΠ·ΠΈΡΠΎΠ²ΠΎΠ³ΠΎ Π³ΡΠ°Π²ΠΈΡ Π΄ΠΎΡΡΠΈΠ³Π°Π΅ΡΡΡ ΡΠΌΠ΅Π½ΡΡΠ΅Π½ΠΈΠ΅ ΠΎΠ±ΡΠ΅ΠΌΠ° ΡΠ²ΠΎΠ±ΠΎΠ΄Π½ΠΎΠΉ Π·Π°ΡΡΠΏΠΊΠΈ Π² ΡΡΠ΅Π΄Π½Π΅ΠΌ Π½Π° 7%. Π‘Π»Π΅Π΄ΠΎΠ²Π°ΡΠ΅Π»ΡΠ½ΠΎ, ΠΎΡΡΠ°Π»ΡΠ½ΡΠ΅ 13% ΡΠΌΠ΅Π½ΡΡΠ΅Π½ΠΈΠ΅ ΠΎΠ±ΡΠ΅ΠΌΠ° ΠΏΡΠΈΡ ΠΎΠ΄ΡΡΡΡ Π½Π° ΡΠΌΡΡΠΈΠ΅ Π·Π΅ΡΠ΅Π½. ΠΡΠ»ΠΈ ΠΏΠ΅ΡΠ²ΠΎΠ½Π°ΡΠ°Π»ΡΠ½Π°Ρ Π²ΡΡΠΎΡΠ° Π·Π΅ΡΠ½Π° Π, ΡΠΎ ΠΏΠΎΡΠ»Π΅ ΡΠΌΡΡΠΈΡ ΠΎΠ½Π° ΡΠΌΠ΅Π½ΡΡΠ°Π΅ΡΡΡ Π½Π° 13%.
ΠΠ· ΡΡΠΈΡ ΡΠΎΠΎΠ±ΡΠ°ΠΆΠ΅Π½ΠΈΠΉ Π² ΠΠΠ‘Π’ 9757-83 Β«ΠΠ°ΠΏΠΎΠ»Π½ΠΈΡΠ΅Π»ΠΈ ΠΏΠΎΡΠΈΡΡΡΠ΅ Π½Π΅ΠΎΡΠ³Π°Π½ΠΈΡΠ΅ΡΠΊΠΈΠ΅ Π΄Π»Ρ Π»Π΅Π³ΠΊΠΈΡ Π±Π΅ΡΠΎΠ½ΠΎΠ². ΠΠ±ΡΠΈΠ΅ ΡΠ΅Ρ Π½ΠΈΡΠ΅ΡΠΊΠΈΠ΅ ΡΡΠ»ΠΎΠ²ΠΈΡΒ» ΠΏΡΠ΅Π΄ΡΡΠΌΠΎΡΡΠ΅Π½Π° ΠΌΠ°ΡΠΊΠΈΡΠΎΠ²ΠΊΠ° ΠΏΠΎΡΠΈΡΡΡΡ Π·Π°ΠΏΠΎΠ»Π½ΠΈΡΠ΅Π»Π΅ΠΉ Π½Π΅ ΡΠΎΠ»ΡΠΊΠΎ ΠΏΠΎ Π½Π°ΡΡΠΏΠ½ΠΎΠΉ ΠΏΠ»ΠΎΡΠ½ΠΎΡΡΠΈ, Π½ΠΎ ΠΈ ΠΏΠΎ ΠΏΡΠΎΡΠ½ΠΎΡΡΠΈ, ΠΏΡΠΈΡΠ΅ΠΌ Π΄Π»Ρ ΠΊΠ΅ΡΠ°ΠΌΠ·ΠΈΡΠ° ΠΈ ΠΏΠΎΠ΄ΠΎΠ±Π½ΠΎΠ³ΠΎ Π΅ΠΌΡ ΠΏΠΎΡΠΈΡΡΠΎΠ³ΠΎ Π³ΡΠ°Π²ΠΈΡ ΡΠΈΡΠ»Π°, ΠΎΠΏΡΠ΅Π΄Π΅Π»ΡΡΡΠΈΠ΅ ΠΌΠ°ΡΠΊΡ ΠΏΠΎ ΠΏΡΠΎΡΠ½ΠΎΡΡΠΈ, Π² ΡΡΠ΅Π΄Π½Π΅ΠΌ Π² 4,5 ΡΠ°Π·Π° ΠΏΡΠ΅Π²ΡΡΠ°ΡΡ ΠΏΠΎΠΊΠ°Π·Π°ΡΠ΅Π»ΠΈ ΠΏΡΠΎΡΠ½ΠΎΡΡΠΈ, ΠΏΠΎΠ»ΡΡΠ΅Π½Π½ΡΠ΅ ΠΏΡΠΈ ΠΈΡΠΏΡΡΠ°Π½ΠΈΠΈ ΡΠ΄Π°Π²Π»ΠΈΠ²Π°Π½ΠΈΠ΅ΠΌ Π² ΡΠΈΠ»ΠΈΠ½Π΄ΡΠ΅.
ΠΠ°ΡΠΊΠΈΡΠΎΠ²ΠΊΠ° ΠΏΠΎ ΠΏΡΠΎΡΠ½ΠΎΡΡΠΈ ΠΏΠΎΠ·Π²ΠΎΠ»ΡΠ΅Ρ ΡΡΠ°Π·Ρ Π½Π°ΠΌΠ΅ΡΠΈΡΡ ΠΎΠ±Π»Π°ΡΡΡ ΡΠ°ΡΠΈΠΎΠ½Π°Π»ΡΠ½ΠΎΠ³ΠΎ ΠΏΡΠΈΠΌΠ΅Π½Π΅Π½ΠΈΡ ΡΠΎΠ³ΠΎ ΠΈΠ»ΠΈ ΠΈΠ½ΠΎΠ³ΠΎ ΠΊΠ΅ΡΠ°ΠΌΠ·ΠΈΡΠ° Π² Π±Π΅ΡΠΎΠ½Π°Ρ
ΡΠΎΠΎΡΠ²Π΅ΡΡΡΠ²ΡΡΡΠΈΡ
ΠΌΠ°ΡΠΎΠΊ. ΠΠΎΠ»Π΅Π΅ ΡΠΎΡΠ½Π΅Π΅ Π΄Π°Π½Π½ΡΠ΅ ΠΏΠΎΠ»ΡΡΠ°ΡΡ ΠΏΡΠΈ ΠΈΡΠΏΡΡΠ°Π½ΠΈΠΈ Π·Π°ΠΏΠΎΠ»Π½ΠΈΡΠ΅Π»Ρ Π² Π±Π΅ΡΠΎΠ½Π΅.
ΠΠ»Ρ Π±ΡΡΡΡΠΎΠ³ΠΎ ΠΎΠΏΡΠ΅Π΄Π΅Π»Π΅Π½ΠΈΡ ΠΏΡΠΎΡΠ½ΠΎΡΡΠΈ ΠΎΡΠ΄Π΅Π»ΡΠ½ΡΡ
Π·Π΅ΡΠ΅Π½
ΠΊΠ΅ΡΠ°ΠΌΠ·ΠΈΡΠΎΠ²ΠΎΠ³ΠΎ Π³ΡΠ°Π²ΠΈΡ Π² Π‘ΠΈΠ±ΠΠΠΠΠΠ ΡΠ°Π·ΡΠ°Π±ΠΎΡΠ°Π½ ΠΌΠ΅ΡΠΎΠ΄ ΠΈΡΠΏΡΡΠ°Π½ΠΈΡ
ΠΈΡ
Π³ΠΈΠ΄ΡΠΎΡΡΠ°ΡΠΈΡΠ΅ΡΠΊΠΈΠΌ Π΄Π°Π²Π»Π΅Π½ΠΈΠ΅ΠΌ Π² ΠΆΠΈΠ΄ΠΊΠΎΡΡΠΈ (ΠΌΠ°ΡΠ»Π΅), Π²
ΠΠΠΠΊΠ΅ΡΠ°ΠΌΠ·ΠΈΡΠ΅ β Π°Π½Π°Π»ΠΎΠ³ΠΈΡΠ½ΡΠΉ ΠΌΠ΅ΡΠΎΠ΄ ΠΎΠ±ΡΠ΅ΠΌΠ½ΠΎΠ³ΠΎ ΡΠΆΠ°ΡΠΈΡ Π³ΠΈΠ΄ΡΠΎΠΏΠ»Π°ΡΡΠΌΠ°ΡΡΠΎΠΉ.
Π Π·Π°Π²ΠΈΡΠΈΠΌΠΎΡΡΠΈ ΠΎΡ ΠΎΡΠΎΠ±Π΅Π½Π½ΠΎΡΡΠ΅ΠΉ ΡΡΡΡΡ ΠΈ ΡΠ΅Ρ Π½ΠΎΠ»ΠΎΠ³ΠΈΠΈ ΠΏΡΠΎΠΈΠ·Π²ΠΎΠ΄ΡΡΠ²Π° Π΄Π΅ΠΉΡΡΠ²ΠΈΡΠ΅Π»ΡΠ½Π°Ρ ΠΏΡΠΎΡΠ½ΠΎΡΡΡ ΠΊΠ΅ΡΠ°ΠΌΠ·ΠΈΡΠ° ΠΌΠΎΠΆΠ΅Ρ ΠΎΡΠ»ΠΈΡΠ°ΡΡΡΡ ΠΎΡ ΡΠ°ΡΡΠ΅ΡΠ½ΠΎΠΉ, Π½ΠΎ ΠΏΡΠ΅Π΄Π²Π°ΡΠΈΡΠ΅Π»ΡΠ½Π°Ρ ΠΎΡΠΈΠ΅Π½ΡΠΈΡΠΎΠ²ΠΎΡΠ½Π°Ρ Π΅Π΅ ΠΎΡΠ΅Π½ΠΊΠ° Π²ΡΠ΅ ΠΆΠ΅ Π΄Π°Π΅Ρ ΠΏΡΠ΅Π΄ΡΡΠ°Π²Π»Π΅Π½ΠΈΠ΅ ΠΎ Π²ΠΎΠ·ΠΌΠΎΠΆΠ½ΠΎΡΡΠΈ ΠΈ ΡΠ΅Π»Π΅ΡΠΎΠΎΠ±ΡΠ°Π·Π½ΠΎΡΡΠΈ ΠΈΡΠΏΠΎΠ»ΡΠ·ΠΎΠ²Π°Π½ΠΈΡ Π΄Π°Π½Π½ΠΎΠ³ΠΎ ΠΊΠ΅ΡΠ°ΠΌΠ·ΠΈΡΠ° Π΄Π»Ρ ΠΏΠΎΠ»ΡΡΠ΅Π½ΠΈΡ Π±Π΅ΡΠΎΠ½Π° ΡΡΠ΅Π±ΡΠ΅ΠΌΡΡ ΠΊΠ»Π°ΡΡΠΎΠ² ΠΏΠΎ ΠΏΡΠΎΡΠ½ΠΎΡΡΠΈ. ΠΡΠΈΠ²Π΅Π΄Π΅Π½Π½ΡΠ΅ ΡΠΈΡΠ»ΠΎΠ²ΡΠ΅ Π·Π½Π°ΡΠ΅Π½ΠΈΡ ΡΠ°ΡΡΠ΅ΡΠ½ΠΎΠΉ ΠΏΡΠΎΡΠ½ΠΎΡΡΠΈ ΠΊΠ΅ΡΠ°ΠΌΠ·ΠΈΡΠΎΠ²ΠΎΠ³ΠΎ Π³ΡΠ°Π²ΠΈΡ ΠΏΠΎΠΊΠ°Π·ΡΠ²Π°ΡΡ, ΡΡΠΎ ΡΡΠΎΡ ΠΏΠΎΡΠΈΡΡΡΠΉ Π·Π°ΠΏΠΎΠ»Π½ΠΈΡΠ΅Π»Ρ ΠΌΠΎΠΆΠ΅Ρ Π±ΡΡΡ Π΄ΠΎΡΡΠ°ΡΠΎΡΠ½ΠΎ ΠΏΡΠΎΡΠ½ΡΠΌ Π΄Π»Ρ Π²ΡΡΠΎΠΊΠΎΠΏΡΠΎΡΠ½ΡΡ Π»Π΅Π³ΠΊΠΈΡ ΠΊΠΎΠ½ΡΡΡΡΠΊΡΠΈΠΎΠ½Π½ΡΡ Π±Π΅ΡΠΎΠ½ΠΎΠ², Π½Π΅ΡΠΌΠΎΡΡΡ Π½Π° Π½ΠΈΠ·ΠΊΠΈΠ΅ ΠΏΠΎΠΊΠ°Π·Π°ΡΠ΅Π»ΠΈ ΠΏΡΠΎΡΠ½ΠΎΡΡΠΈ ΠΏΡΠΈ ΡΡΠ°Π½Π΄Π°ΡΡΠ½ΠΎΠΌ ΠΈΡΠΏΡΡΠ°Π½ΠΈΠΈ.
ΠΠ΅ΡΠ½Π° ΠΊΠ΅ΡΠ°ΠΌΠ·ΠΈΡΠΎΠ²ΠΎΠ³ΠΎ Π³ΡΠ°Π²ΠΈΡ ΠΌΠΎΠ³ΡΡ ΠΈΠΌΠ΅ΡΡ ΡΠ°ΡΠΎΠΎΠ±ΡΠ°Π·Π½ΡΡ ΠΈΠ»ΠΈ Π²ΡΡΡΠ½ΡΡΡΡ ΡΠΎΡΠΌΡ, ΡΡΠΎ Π·Π°Π²ΠΈΡΠΈΡ ΠΎΡ ΡΠΎΡΠΌΡ ΡΡΡΡΠΎΠ²ΡΡ Π³ΡΠ°Π½ΡΠ». ΠΠΎ ΡΡΠ°Π½Π΄Π°ΡΡΡ ΡΡΠ΅Π΄Π½Π΅Π΅ Π·Π½Π°ΡΠ΅Π½ΠΈΠ΅ ΠΊΠΎΡΡΡΠΈΡΠΈΠ΅Π½ΡΠ° Π΄ΠΎΠ»ΠΆΠ½ΠΎ Π±ΡΡΡ Π½Π΅ Π±ΠΎΠ»Π΅Π΅ 1,5, Π·Π΅ΡΠ½Π° Ρ ΠΊΠΎΡΡΡΠΈΡΠΈΠ΅Π½ΡΠΎΠΌ ΡΠΎΡΠΌΡ Π±ΠΎΠ»Π΅Π΅ 2,5 Π² ΠΊΠ΅ΡΠ°ΠΌΠ·ΠΈΡΠΎΠ²ΠΎΠΌ Π³ΡΠ°Π²ΠΈΠΈ ΠΏΠ΅ΡΠ²ΠΎΠΉ ΠΊΠ°ΡΠ΅Π³ΠΎΡΠΈΠΈ ΠΊΠ°ΡΠ΅ΡΡΠ²Π° ΡΠ°ΠΊΠΈΡ Π·Π΅ΡΠ΅Π½ Π΄ΠΎΠΏΡΡΠΊΠ°Π΅ΡΡΡ Π½Π΅ Π±ΠΎΠ»Π΅Π΅ 15% ΠΏΠΎ ΠΌΠ°ΡΡΠ΅.
Π‘ΠΎΠ΄Π΅ΡΠΆΠ°Π½ΠΈΠ΅ ΡΠ°ΡΠΊΠΎΠ»ΠΎΡΡΡ Π·Π΅ΡΠ΅Π½ Π² ΠΊΠ΅ΡΠ°ΠΌΠ·ΠΈΡΠΎΠ²ΠΎΠΌ Π³ΡΠ°Π²ΠΈΠΈ Π΄ΠΎΠΏΡΡΠΊΠ°Π΅ΡΡΡ Π½Π΅ Π±ΠΎΠ»Π΅Π΅ 10… 15% ΠΏΠΎ ΠΌΠ°ΡΡΠ΅ Π² Π·Π°Π²ΠΈΡΠΈΠΌΠΎΡΡΠΈ ΠΎΡ ΠΊΠ°ΡΠ΅Π³ΠΎΡΠΈΠΈ ΠΊΠ°ΡΠ΅ΡΡΠ²Π°.
ΠΠ΅ΡΠ°ΠΌΠ·ΠΈΡΠΎΠ²ΡΠΉ Π³ΡΠ°Π²ΠΈΠΉ Π΄ΠΎΠ»ΠΆΠ΅Π½ Π²ΡΠ΄Π΅ΡΠΆΠΈΠ²Π°ΡΡ Π½Π΅ ΠΌΠ΅Π½Π΅Π΅ 15 ΡΠΈΠΊΠ»ΠΎΠ² ΠΏΠΎΠΏΠ΅ΡΠ΅ΠΌΠ΅Π½Π½ΠΎΠ³ΠΎ Π·Π°ΠΌΠΎΡΠ°ΠΆΠΈΠ²Π°Π½ΠΈΡ ΠΈ ΠΎΡΡΠ°ΠΈΠ²Π°Π½ΠΈΡ Π² Π½Π°ΡΡΡΠ΅Π½Π½ΠΎΠΌ Π²ΠΎΠ΄ΠΎΠΉ ΡΠΎΡΡΠΎΡΠ½ΠΈΠΈ Ρ ΠΏΠΎΡΠ΅ΡΠ΅ΠΉ ΠΌΠ°ΡΡΡ Π΄Π°Π½Π½ΠΎΠΉ ΡΡΠ°ΠΊΡΠΈΠΈ Π½Π΅ Π±ΠΎΠ»Π΅Π΅ 8%.
ΠΡΠΈ ΠΈΡΠΏΡΡΠ°Π½ΠΈΠΈ ΠΊΠΈΠΏΡΡΠ΅Π½ΠΈΠ΅ΠΌ ΠΏΠΎΡΠ΅ΡΡ ΠΌΠ°ΡΡΡ Π½Π΅ Π΄ΠΎΠ»ΠΆΠ½Π° ΠΏΡΠ΅Π²ΡΡΠ°ΡΡ 5%. Π’Π°ΠΊΠΈΠΌ ΠΈΡΠΏΡΡΠ°Π½ΠΈΠ΅ΠΌ Π²ΡΡΠ²Π»ΡΠ΅ΡΡΡ Π½Π°Π»ΠΈΡΠΈΠ΅ ΠΎΠΏΠ°ΡΠ½ΡΡ ΠΈΠ·Π²Π΅ΡΡΠ½ΡΠΊΠΎΠ²ΡΡ Π²ΠΊΠ»ΡΡΠ΅Π½ΠΈΠΉ — Β«Π΄ΡΡΠΈΠΊΠΎΠ²Β».
ΠΠ³ΡΠ°Π½ΠΈΡΠΈΠ²Π°Π΅ΡΡΡ Π²ΠΎΠ΄ΠΎΠΏΠΎΠ³Π»ΠΎΡΠ΅Π½ΠΈΠ΅ (Π½Π΅ Π±ΠΎΠ»Π΅Π΅ 20…30% ΠΏΠΎ ΠΌΠ°ΡΡΠ΅ Π·Π° 1Ρ Π² Π·Π°Π²ΠΈΡΠΈΠΌΠΎΡΡΠΈ ΠΎΡ ΠΌΠ°ΡΠΊΠΈ), ΡΠΎΠ΄Π΅ΡΠΆΠ°Π½ΠΈΠ΅ Π²ΠΎΠ΄ΠΎΡΠ°ΡΡΠ²ΠΎΡΠΈΠΌΡΡ ΡΠ΅ΡΠ½ΠΈΡΡΡΡ ΠΈ ΡΠ΅ΡΠ½ΠΎΠΊΠΈΡΠ»ΡΡ ΡΠΎΠ΅Π΄ΠΈΠ½Π΅Π½ΠΈΠΉ. ΠΡΠΈ ΠΈ Π΄ΡΡΠ³ΠΈΠ΅ ΡΡΠ΅Π±ΠΎΠ²Π°Π½ΠΈΡ ΡΡΠ°Π½Π΄Π°ΡΡΠ° ΠΎΠ±Π΅ΡΠΏΠ΅ΡΠΈΠ²Π°ΡΡ ΡΡΠΎΠΉΠΊΠΎΡΡΡ ΠΈ Π΄ΠΎΠ»Π³ΠΎΠ²Π΅ΡΠ½ΠΎΡΡΡ ΠΊΠ΅ΡΠ°ΠΌΠ·ΠΈΡΠ°.
Β ΠΠΎ Π΄Π°Π½Π½ΡΠΌ ΠΈΡΡΠ»Π΅Π΄ΠΎΠ²Π°ΡΠ΅Π»Π΅ΠΉ, ΠΈΠ·ΡΡΠ°Π²ΡΠΈΡ
ΠΊΠ°ΡΠ΅ΡΡΠ²ΠΎ ΠΊΠ΅ΡΠ°ΠΌΠ·ΠΈΡΠ° Π½Π° ΠΌΠ½ΠΎΠ³ΠΈΡ
ΠΏΡΠ΅Π΄ΠΏΡΠΈΡΡΠΈΡΡ
, ΠΊΠ΅ΡΠ°ΠΌΠ·ΠΈΡ Π²Π΅Π·Π΄Π΅ Π½Π΅ΠΎΠ΄Π½ΠΎΡΠΎΠ΄Π΅Π½. ΠΡΠ΅Π²ΠΈΠ΄Π½ΠΎ, ΡΡΠΎ ΠΏΡΠ΅Π΄ΠΎΠΏΡΠ΅Π΄Π΅Π»Π΅Π½Π½ΠΎ ΡΠ°ΠΌΠΎΠΉ ΡΠ΅Ρ
Π½ΠΎΠ»ΠΎΠ³ΠΈΠ΅ΠΉ ΠΏΠΎΠ»ΡΡΠ΅Π½ΠΈΡ ΠΊΠ΅ΡΠ°ΠΌΠ·ΠΈΡΠΎΠ²ΠΎΠ³ΠΎ Π³ΡΠ°Π²ΠΈΡ, ΠΊΠΎΠ³Π΄Π° ΠΊΠ°ΠΆΠ΄Π°Ρ Π³ΡΠ°Π½ΡΠ»Π° Π²ΡΠΏΡΡΠΈΠ²Π°Π΅ΡΡΡ ΠΏΠΎ-ΡΠ°Π·Π½ΠΎΠΌΡ ΠΏΡΠΈ Π½Π΅ΠΎΠ΄Π½ΠΎΡΠΎΠ΄Π½ΠΎΡΡΠΈ ΡΡΡΡΡ ΠΈ Π½Π΅ΠΏΠΎΡΡΠΎΡΠ½ΡΡΠ²Π΅ ΡΠ΅ΠΌΠΏΠ΅ΡΠ°ΡΡΡΠ½ΡΡ
ΡΡΠ»ΠΎΠ²ΠΈΠΉ Π² ΠΏΠ΅ΡΠΈ. Π ΡΠ΅Π·ΡΠ»ΡΡΠ°ΡΠ΅ ΠΊΠ΅ΡΠ°ΠΌΠ·ΠΈΡΠΎΠ²ΡΠΉ Π³ΡΠ°Π²ΠΈΠΉ — ΡΡΠΎ ΡΠΎΠ²ΠΎΠΊΡΠΏΠ½ΠΎΡΡΡ Π½Π΅ΠΎΠ΄ΠΈΠ½Π°ΠΊΠΎΠ²ΡΡ
Π²ΡΠΏΡΡΠ΅Π½Π½ΡΡ
Π³ΡΠ°Π½ΡΠ» ΡΠ°Π·Π»ΠΈΡΠ½ΠΎΠΉ ΠΏΠ»ΠΎΡΠ½ΠΎΡΡΠΈ ΠΈ ΠΏΡΠΎΡΠ½ΠΎΡΡΠΈ.
ΠΠ»Ρ ΠΏΠΎΠ»ΡΡΠ΅Π½ΠΈΡ ΠΎΠ΄Π½ΠΎΡΠΎΠ΄Π½ΠΎΡΡΠΈ ΠΊΠ΅ΡΠ°ΠΌΠ·ΠΈΡΠ° Π΅ΡΡΡ Π΄Π²Π° ΠΏΡΡΠΈ:
—Β Β Β Β Β ΠΏΠ΅ΡΠ²ΡΠΉ ΠΏΡΡΡ ΡΠΎΡΡΠΎΠΈΡ Π² ΡΠΎΠ²Π΅ΡΡΠ΅Π½ΡΡΠ²ΠΎΠ²Π°Π½ΠΈΠΈ ΡΠ΅Ρ
Π½ΠΎΠ»ΠΎΠ³ΠΈΠΈ
ΠΏΡΠΎΠΈΠ·Π²ΠΎΠ΄ΡΡΠ²Π°, ΡΡΡΠ΅Π΄Π½Π΅Π½ΠΈΠ΅ ΡΡΡΡΡ, Π±ΠΎΠ»Π΅Π΅ ΡΡΠ°ΡΠ΅Π»ΡΠ½ΠΎ Π΅Π³ΠΎ ΠΏΠ΅ΡΠ΅ΡΠ°Π±ΠΎΡΠΊΠ΅
ΠΈ Π³ΡΠ°Π½ΡΠ»ΡΡΠΈΠΈ, ΡΡΠ°Π±ΠΈΠ»ΠΈΠ·Π°ΡΠΈΠΈ ΡΠ΅ΠΆΠΈΠΌΠΎΠ² ΡΠ΅ΡΠΌΠΎΠΏΠΎΠ΄Π³ΠΎΡΠΎΠ²ΠΊΠΈ, ΠΎΠ±ΠΆΠΈΠ³Π° ΠΈ
ΠΎΡ
Π»Π°ΠΆΠ΄Π΅Π½ΠΈΡ, ΡΠ»ΡΡΡΠ΅Π½ΠΈΡ ΡΡΠ°ΠΊΡΠΈΠΎΠ½ΠΈΡΠΎΠ²Π°Π½ΠΈΡ.
—Β Β Β Β Π²ΡΠΎΡΠΎΠΉ ΠΏΡΡΡ — ΡΠ°Π·Π΄Π΅Π»Π΅Π½ΠΈΠ΅ Π³ΠΎΡΠΎΠ²ΠΎΠΉ ΠΏΡΠΎΠ΄ΡΠΊΡΠΈΠΈ Π½Π° ΡΡΠ°ΠΊΡΠΈΠΈ Π½Π΅
ΡΠΎΠ»ΡΠΊΠΎ ΠΏΠΎ ΠΊΡΡΠΏΠ½ΠΎΡΡΠΈ, Π½ΠΎ ΠΈ ΠΏΠΎ ΠΏΠ»ΠΎΡΠ½ΠΎΡΡΠΈ Π·Π΅ΡΠ΅Π½.
ΠΡΠΈΠΌΠ΅Π½ΠΈΡΠ΅Π»ΡΠ½ΠΎ ΠΊ ΠΊΠ΅ΡΠ°ΠΌΠ·ΠΈΡΠΎΠ²ΠΎΠΌΡ Π³ΡΠ°Π²ΠΈΡ ΡΠ΅ΡΠΌΠΈΠ½ Β«ΠΎΠ±ΠΎΠ³Π°ΡΠ΅Π½ΠΈΠ΅Β» ΠΎΠ·Π½Π°ΡΠ°Π΅Ρ ΡΠ°Π·Π΄Π΅Π»Π΅Π½ΠΈΠ΅ Π΅Π³ΠΎ Π½Π° ΠΊΠ»Π°ΡΡΡ ΠΏΠΎ ΠΏΠ»ΠΎΡΠ½ΠΎΡΡΠΈ Π·Π΅ΡΠ΅Π½. ΠΠΎΠ»Π΅Π΅ Π»Π΅Π³ΠΊΠΈΠΉ Π±ΡΠ΄Π΅Ρ Π±ΠΎΠ³Π°ΡΠ΅, Ρ ΠΎΡΠΎΡΠΎ Π²ΡΠΏΡΡΠ΅Π½Π½ΡΠΌΠΈ Π·Π΅ΡΠ½Π°ΠΌΠΈ, Π±ΠΎΠ»Π΅Π΅ ΡΡΠΆΠ΅Π»ΡΠΉ — Π±ΠΎΠ³Π°ΡΠ΅ ΠΌΠ΅Π½Π΅Π΅ Π²ΡΠΏΡΡΠ΅Π½Π½ΡΠΌΠΈ, Π·Π°ΡΠΎ Π±ΠΎΠ»Π΅Π΅ ΠΏΡΠΎΡΠ½ΡΠΌΠΈ Π·Π΅ΡΠ½Π°ΠΌΠΈ.
Π‘ΡΠΈΡΠ°Π΅ΡΡΡ, ΡΡΠΎ ΠΊΠ΅ΡΠ°ΠΌΠ·ΠΈΡΠΎΠ²ΡΠΉ Π³ΡΠ°Π²ΠΈΠΉ ΠΈ Π΄ΡΡΠ³ΠΈΠ΅ ΠΏΠΎΡΠΈΡΡΡΠ΅ Π·Π°ΠΏΠΎΠ»Π½ΠΈΡΠ΅Π»ΠΈ ΠΏΠΎΠ΄Π»Π΅ΠΆΠ°Ρ ΠΎΠ±ΠΎΠ³Π°ΡΠ΅Π½ΠΈΡ ΡΠΎΠ»ΡΠΊΠΎ Π² ΡΡΠ»ΠΎΠ²ΠΈΡΡ
ΡΡΡ
ΠΎΠΉ ΡΠ΅ΠΏΠ°ΡΠ°ΡΠΈΠΈ, ΡΡΠΎ ΠΈΡ
Π½Π΅Π»ΡΠ·Ρ ΡΠ²Π»Π°ΠΆΠ½ΡΡΡ, ΠΏΠΎΡΠΊΠΎΠ»ΡΠΊΡ ΠΏΠΎ ΠΠΠ‘Π’ 9759-83 Π²Π»Π°ΠΆΠ½ΠΎΡΡΡ ΠΏΠΎΡΡΠ°Π²Π»ΡΠ΅ΠΌΠΎΠ³ΠΎ ΠΊΠ΅ΡΠ°ΠΌΠ·ΠΈΡΠΎΠ²ΠΎΠ³ΠΎ Π³ΡΠ°Π²ΠΈΡ Π΄ΠΎΠ»ΠΆΠ½Π° Π±ΡΡΡ Π½Π΅ Π±ΠΎΠ»Π΅Π΅ 2%. ΠΠ΄Π½Π°ΠΊΠΎ ΡΡΠΎ ΠΎΠ³ΡΠ°Π½ΠΈΡΠ΅Π½ΠΈΠ΅ ΠΊΠ°ΡΠ°Π΅ΡΡΡ ΠΏΠΎΡΡΠ°Π²Π»ΡΠ΅ΠΌΠΎΠ³ΠΎ Π³ΡΠ°Π²ΠΈΡ, Π° ΠΏΡΠΈ ΠΈΡΠΏΠΎΠ»ΡΠ·ΠΎΠ²Π°Π½ΠΈΠΈ Π΅Π³ΠΎ ΠΌΠΎΠΆΠ½ΠΎ ΡΠ²Π»Π°ΠΆΠ½ΡΡΡ, ΠΊΠ°ΠΊ ΡΠΎΠ³ΠΎ ΡΡΠ΅Π±ΡΠ΅Ρ ΡΠ΅Ρ
Π½ΠΎΠ»ΠΎΠ³ΠΈΡ. Π ΡΠ΅Ρ
Π½ΠΎΠ»ΠΎΠ³ΠΈΠΈ Π»Π΅Π³ΠΊΠΈΡ
Π±Π΅ΡΠΎΠ½ΠΎΠ² Π½Π΅ΡΠ΅Π΄ΠΊΠΎ ΡΠ΅ΠΊΠΎΠΌΠ΅Π½Π΄ΡΠ΅ΡΡΡ ΠΏΡΠ΅Π΄Π²Π°ΡΠΈΡΠ΅Π»ΡΠ½ΠΎ ΡΠ²Π»Π°ΠΆΠ½ΡΡΡ ΠΏΠΎΡΠΈΡΡΡΠ΅ Π·Π°ΠΏΠΎΠ»Π½ΠΈΡΠ΅Π»ΠΈ, ΡΡΠΎΠ±Ρ ΡΠΌΠ΅Π½ΡΡΠΈΡΡ ΠΏΠΎΠ³Π»ΠΎΡΠ΅Π½ΠΈΠ΅ ΠΈΠΌΠΈ Π²ΠΎΠ΄Ρ ΠΈΠ· Π±Π΅ΡΠΎΠ½Π½ΠΎΠΉ ΡΠΌΠ΅ΡΠΈ.
2.3. Π₯Π°ΡΠ°ΠΊΡΠ΅ΡΠΈΡΡΠΈΠΊΠ° ΠΈΡΠΏΠΎΠ»ΡΠ·ΡΠ΅ΠΌΠΎΠ³ΠΎ ΡΡΡΡΡ
Π‘ΡΡΡΠ΅ΠΌ Π΄Π»Ρ ΠΏΡΠΎΠΈΠ·Π²ΠΎΠ΄ΡΡΠ²Π° ΠΊΠ΅ΡΠ°ΠΌΠ·ΠΈΡΠ° ΡΠ»ΡΠΆΠ°Ρ Π³Π»ΠΈΠ½ΠΈΡΡΡΠ΅ ΠΏΠΎΡΠΎΠ΄Ρ, ΠΎΡΠ½ΠΎΡΡΡΠΈΠ΅ΡΡ Π² ΠΎΡΠ½ΠΎΠ²Π½ΠΎΠΌ ΠΊ ΠΎΡΠ°Π΄ΠΎΡΠ½ΡΠΌ Π³ΠΎΡΠ½ΡΠΌ.
ΠΠ»Ρ ΠΏΡΠΎΠΈΠ·Π²ΠΎΠ΄ΡΡΠ²Π° ΠΊΠ΅ΡΠ°ΠΌΠ·ΠΈΡΠ° Π½Π°ΠΈΠ±ΠΎΠ»Π΅Π΅ ΠΏΡΠΈΠ³ΠΎΠ΄Π½Ρ ΠΌΠΎΠ½ΡΠΌΠΎΡΠΈΠ»Π»ΠΎΠ½ΠΈΡΠΎΠ²ΡΠ΅ ΠΈ Π³ΠΈΠ΄ΡΠΎΡΠ»ΡΠ΄ΠΈΡΡΡΠ΅ Π³Π»ΠΈΠ½Ρ, ΡΠΎΠ΄Π΅ΡΠΆΠ°ΡΠΈΠ΅ Π½Π΅ Π±ΠΎΠ»Π΅Π΅ 30% ΠΊΠ²Π°ΡΡΠ°.
ΠΡΠ½ΠΎΠ²Π½ΠΎΠΉ ΠΊΡΠΈΡΠ΅ΡΠΈΠΉ ΠΏΡΠΈΠ³ΠΎΠ΄Π½ΠΎΡΡΠΈ Π³Π»ΠΈΠ½ΠΈΡΡΠΎΠ³ΠΎ ΡΡΡΡΡ Π΄Π»Ρ
ΠΏΡΠΎΠΈΠ·Π²ΠΎΠ΄ΡΡΠ²Π°Β Β Β ΠΊΠ΅ΡΠ°ΠΌΠ·ΠΈΡΠ° — ΡΠΏΠΎΡΠΎΠ±Π½ΠΎΡΡΡΒ Π²ΡΠΏΡΡΠΈΠ²Π°ΡΡΡΡΒ ΠΏΡΠΈ
ΡΠ΅ΡΠΌΠΈΡΠ΅ΡΠΊΠΎΠΉ ΠΎΠ±ΡΠ°Π±ΠΎΡΠΊΠ΅ Π² ΠΏΡΠ΅Π΄Π΅Π»Π°Ρ 1050-1250Β°Π‘ ΠΈ ΠΎΠ±ΡΠ°Π·ΠΎΠ²ΡΠ²Π°ΡΡ ΠΏΡΠΈ ΡΡΠΎΠΌ ΠΌΠ°ΡΠ΅ΡΠΈΠ°Π», ΠΈΠΌΠ΅ΡΡΠΈΠΉ ΡΡΠ΅ΠΈΡΡΠΎΠ΅ ΡΡΡΠΎΠ΅Π½ΠΈΠ΅ Ρ ΠΏΠ»ΠΎΡΠ½ΠΎΡΡΡΡ Π² ΠΊΡΡΠΊΠ΅ Π² ΠΏΡΠ΅Π΄Π΅Π»Π°Ρ 200-1350 ΠΊΠ³/ΠΌ3.
Π Π°Π·Π»ΠΈΡΠ°ΡΡΒ Β Β Β ΡΠ»Π°Π±ΠΎ-,Β Β Β Β ΡΡΠ΅Π΄Π½Π΅-Β Β Β Β ΠΈΒ Β Β Ρ ΠΎΡΠΎΡΠΎΠ²ΡΠΏΡΡΠΈΠ²Π°ΡΡΠΈΠ΅ΡΡ
Π³Π»ΠΈΠ½ΠΈΡΡΡΠ΅ ΠΏΠΎΡΠΎΠ΄Ρ Ρ ΠΊΠΎΡΡΡΠΈΡΠΈΠ΅Π½ΡΠΎΠΌ Π²ΡΠΏΡΡΠΈΠ²Π°Π½ΠΈΡ ΡΠΎΠΎΡΠ²Π΅ΡΡΡΠ²Π΅Π½Π½ΠΎ Π΄ΠΎ 2,5; 2,5 — 4,5 ΠΈ ΠΠ² ΡΠ²ΡΡΠ΅ 4,5; ΡΠ΅ΠΌ Π²ΡΡΠ΅ ΠΊΠΎΡΡΡΠΈΡΠΈΠ΅Π½Ρ Π²ΡΠΏΡΡΠΈΠ²Π°Π½ΠΈΡ ΡΡΡΡΡ, ΡΠ΅ΠΌ ΠΌΠ΅Π½ΡΡΠ΅ ΠΏΠ»ΠΎΡΠ½ΠΎΡΡΡ ΠΊΠ΅ΡΠ°ΠΌΠ·ΠΈΡΠ°, ΠΈ ΡΠ΅ΠΌ Π±ΠΎΠ»Π΅Π΅ ΡΠ΅Π½Π½ΠΎ ΡΡΠΎ ΡΡΡΡΡ Π΄Π»Ρ ΠΏΡΠΎΠΈΠ·Π²ΠΎΠ΄ΡΡΠ²Π° ΠΊΠ΅ΡΠ°ΠΌΠ·ΠΈΡΠ°.
ΠΡΠΈ ΠΎΡΡΡΡΡΡΠ²ΠΈΠΈ Ρ ΠΎΡΠΎΡΠΎ- ΠΈ ΡΡΠ΅Π΄Π½Π΅Π²ΡΠΏΡΡΠΈΠ²Π°ΡΡΠΈΡ Π³Π»ΠΈΠ½ΠΈΡΡΡΡ ΠΏΠΎΡΠΎΠ΄ Π΄Π»Ρ ΠΏΡΠΎΠΈΠ·Π²ΠΎΠ΄ΡΡΠ²Π° ΠΊΠ΅ΡΠ°ΠΌΠ·ΠΈΡΠ°, ΠΈΡΠΏΠΎΠ»ΡΠ·ΡΠ΅ΠΌΠΎΠ³ΠΎ Π² ΠΊΠΎΠ½ΡΡΡΡΠΊΡΠΈΠ²Π½ΠΎ-ΡΠ΅ΠΏΠ»ΠΎΠΈΠ·ΠΎΠ»ΡΡΠΈΠΎΠ½Π½ΡΡ Π±Π΅ΡΠΎΠ½Π°Ρ , ΡΡΡΡΠ΅ΠΌ ΠΌΠΎΠ³ΡΡ ΡΠ»ΡΠΆΠΈΡΡ ΡΠ»Π°Π±ΠΎΠ²ΡΠΏΡΡΠΈΠ²Π°ΡΡΠΈΠ΅ΡΡ Π³Π»ΠΈΠ½ΠΈΡΡΡΠ΅ ΠΏΠΎΡΠΎΠ΄Ρ Ρ ΠΆΠ΅Π»Π΅Π·ΠΈΡΡΡΠΌΠΈ, ΠΎΡΠ³Π°Π½ΠΈΡΠ΅ΡΠΊΠΈΠΌΠΈ ΠΈ Π΄ΡΡΠ³ΠΈΠΌΠΈ Π΄ΠΎΠ±Π°Π²ΠΊΠ°ΠΌΠΈ.
Π£ΡΡΠ°Π½ΠΎΠ²ΠΈΡΡ ΡΠ΅Π½Π½ΠΎΡΡΡ ΠΊΠ΅ΡΠ°ΠΌΠ·ΠΈΡΠΎΠ²ΠΎΠ³ΠΎ ΡΡΡΡΡ ΠΏΠΎ ΠΊΠ°ΠΊΠΎΠΌΡ-Π»ΠΈΠ±ΠΎ ΠΎΠ΄Π½ΠΎΠΌΡ ΠΏΡΠΈΠ·Π½Π°ΠΊΡ Π²Π΅ΡΡΠΌΠ° Π·Π°ΡΡΡΠ΄Π½ΠΈΡΠ΅Π»ΡΠ½ΠΎ, ΠΏΠΎΡΡΠΎΠΌΡ Π² Π±ΠΎΠ»ΡΡΠΈΠ½ΡΡΠ²Π΅ ΡΠ»ΡΡΠ°Π΅Π² ΠΎΠΏΡΠ΅Π΄Π΅Π»ΡΡΡ ΡΡΠ΄ ΡΠ²ΠΎΠΉΡΡΠ²: Π³Π΅Π½Π΅Π·ΠΈΡ, Π²Π½Π΅ΡΠ½ΠΈΠΉ Π²ΠΈΠ΄, ΠΌΠΈΠ½Π΅ΡΠ°Π»ΠΎΠ³ΠΈΡΠ΅ΡΠΊΠΈΠΉ, Ρ ΠΈΠΌΠΈΡΠ΅ΡΠΊΠΈΠΉ ΠΈ Π³ΡΠ°Π½ΡΠ»ΠΎΠΌΠ΅ΡΡΠΈΡΠ΅ΡΠΊΠΈΠΉ ΡΠΎΡΡΠ°Π², ΠΎΠ³Π½Π΅ΡΠΏΠΎΡΠ½ΠΎΡΡΡ, ΠΈΠ½ΡΠ΅ΡΠ²Π°Π» Π²ΡΠΏΡΡΠΈΠ²Π°Π½ΠΈΡ, ΡΠΎΠ΄Π΅ΡΠΆΠ°Π½ΠΈΠ΅ ΡΠ²ΠΎΠ±ΠΎΠ΄Π½ΠΎΠ³ΠΎ ΠΊΠ΅ΡΠ°ΠΌΠ·ΠΈΡΠ° Π·Π°ΡΠΎΡΠ΅Π½Π½ΠΎΡΡΡ ΠΊΡΡΠΏΠ½ΠΎΠ·Π΅ΡΠ½ΠΈΡΡΡΠΌΠΈ (ΠΊΠ°ΠΌΠ½Π΅Π²ΠΈΠ΄Π½ΡΠΌΠΈ ΠΈ ΠΊΠ°ΡΠ±ΠΎΠ½Π°ΡΠ½ΡΠΌΠΈ) Π²ΠΊΠ»ΡΡΠ΅Π½ΠΈΡΠΌΠΈ, Π° ΡΠ°ΠΊΠΆΠ΅ ΡΡΡΡΠΊΡΡΡΠ½ΠΎ-ΠΌΠ΅Ρ Π°Π½ΠΈΡΠ΅ΡΠΊΠΈΠ΅ ΡΠ²ΠΎΠΉΡΡΠ²Π°, Π±ΠΎΠ»ΡΡΠΈΠ½ΡΡΠ²ΠΎ ΠΈΠ· ΠΊΠΎΡΠΎΡΡΡ ΠΎΠΊΠ°Π·ΡΠ²Π°Π΅Ρ ΠΏΡΡΠΌΠΎΠ΅ ΠΈ ΠΏΡΠΈΡΠΎΠΌ Π²Π΅ΡΡΠΌΠ° ΡΡΡΠ΅ΡΡΠ²Π΅Π½Π½ΠΎΠ΅ Π²Π»ΠΈΡΠ½ΠΈΠ΅ Π½Π° ΠΎΡΠ½ΠΎΠ²Π½ΡΠ΅ ΠΊΡΠΈΡΠ΅ΡΠΈΠΈ ΠΊΠ΅ΡΠ°ΠΌΠ·ΠΈΡΠΎΠ²ΠΎΠ³ΠΎ ΡΡΡΡΡ — ΠΏΠ»ΠΎΡΠ½ΠΎΡΡΡ ΠΈ ΠΊΠΎΡΡΡΠΈΡΠΈΠ΅Π½Ρ Π²ΡΠΏΡΡΠΈΠ²Π°Π½ΠΈΡ.
Π€ΠΈΠ·ΠΈΠΊΠΎ-ΠΌΠ΅Ρ
Π°Π½ΠΈΡΠ΅ΡΠΊΠΈΠ΅ ΠΈ Π²Π°ΠΆΠ½Π΅ΠΉΡΠΈΠ΅ ΡΠ΅Ρ
Π½ΠΎΠ»ΠΎΠ³ΠΈΡΠ΅ΡΠΊΠΈΠ΅ ΡΠ²ΠΎΠΉΡΡΠ²Π° Π³Π»ΠΈΠ½ΠΈΡΡΠΎΠ³ΠΎ ΡΡΡΡΡ Π² ΠΎΡΠ½ΠΎΠ²Π½ΠΎΠΌ ΠΎΠΏΡΠ΅Π΄Π΅Π»ΡΠ΅ΡΡΡ Π΅Π³ΠΎ Π²Π΅ΡΠ΅ΡΡΠ²Π΅Π½Π½ΡΠΌ, ΠΌΠΈΠ½Π΅ΡΠ°Π»ΠΎΠ³ΠΈΡΠ΅ΡΠΊΠΈΠΌ, Π³ΡΠ°Π½ΡΠ»ΠΎΠΌΠ΅ΡΡΠΈΡΠ΅ΡΠΊΠΈΠΌ ΠΈ Ρ
ΠΈΠΌΠΈΡΠ΅ΡΠΊΠΈΠΌ ΡΠΎΡΡΠ°Π²Π°ΠΌΠΈ.
coolreferat.com
ΠΠΈΠ½ΠΈ ΡΠ΅Ρ ΠΏΠΎ ΠΏΡΠΎΠΈΠ·Π²ΠΎΠ΄ΡΡΠ²Ρ ΠΊΠΎΠ»Π±Π°Ρ
ΠΠΈΠ½ΠΈΡΡΠ΅ΡΡΡΠ²ΠΎ ΡΠ΅Π»ΡΡΠΊΠΎΠ³ΠΎ Ρ ΠΎΠ·ΡΠΉΡΡΠ²Π° ΠΈ ΠΏΡΠΎΠ΄ΠΎΠ²ΠΎΠ»ΡΡΡΠ²ΠΈΡ Π ΠΎΡΡΠΈΠΉΡΠΊΠΎΠΉ Π€Π΅Π΄Π΅ΡΠ°ΡΠΈΠΈΠΡΠΈΠΌΠΎΡΡΠΊΠ°Ρ Π³ΠΎΡΡΠ΄Π°ΡΡΡΠ²Π΅Π½Π½Π°Ρ ΡΠ΅Π»ΡΡΠΊΠΎΡ ΠΎΠ·ΡΠΉΡΡΠ²Π΅Π½Π½Π°Ρ Π°ΠΊΠ°Π΄Π΅ΠΌΠΈΡ
ΠΠ½ΡΡΠΈΡΡΡ ΠΌΠ΅Ρ Π°Π½ΠΈΠ·Π°ΡΠΈΠΈ ΡΠ΅Π»ΡΡΠΊΠΎΠ³ΠΎ Ρ ΠΎΠ·ΡΠΉΡΡΠ²Π°
ΠΠ°ΡΠ΅Π΄ΡΠ° ΠΠΠΠΠ‘Π₯Π
ΠΠ£Π Π‘ΠΠΠΠ― Π ΠΠΠΠ’Π
Π’Π΅ΠΌΠ°: «ΠΠΈΠ½ΠΈ — ΡΠ΅Ρ ΠΏΠΎ ΠΏΡΠΎΠΈΠ·Π²ΠΎΠ΄ΡΡΠ²Ρ ΠΊΠΎΠ»Π±Π°Ρ «
ΠΡΠΎΡΠ΅ΡΡ — ΠΈΠ·ΠΌΠ΅Π»ΡΡΠ΅Π½ΠΈΠ΅
ΠΠΏΠΏΠ°ΡΠ°Ρ — Π²ΠΎΠ»ΡΠΎΠΊ
ΠΡΠΏΠΎΠ»Π½ΠΈΠ»: ΡΡΡΠ΄Π΅Π½Ρ 645 Π³ΡΡΠΏΠΏΡ
ΠΡΠΎΠ²Π΅ΡΠΈΠ»:
Π£ΡΡΡΡΠΈΠΉΡΠΊ 2009
Π‘ΠΎΠ΄Π΅ΡΠΆΠ°Π½ΠΈΠ΅
Β 1. ΠΠ²Π΅Π΄Π΅Π½ΠΈΠ΅
2. Π’Π΅Ρ Π½ΠΎΠ»ΠΎΠ³ΠΈΡ ΠΏΡΠΎΠΈΠ·Π²ΠΎΠ΄ΡΡΠ²Π° ΠΊΠΎΠ»Π±Π°Ρ
3. ΠΡΠΎΡΠ΅ΡΡ ΠΈΠ·ΠΌΠ΅Π»ΡΡΠ΅Π½ΠΈΡ
4. ΠΠΏΠΏΠ°ΡΠ°Ρ — Π²ΠΎΠ»ΡΠΎΠΊ
4.1 ΠΠ±Π·ΠΎΡ ΡΡΡΠ΅ΡΡΠ²ΡΡΡΠΈΡ Π°ΠΏΠΏΠ°ΡΠ°ΡΠΎΠ²
4.2 Π’Π΅Ρ Π½ΠΎΠ»ΠΎΠ³ΠΈΡΠ΅ΡΠΊΠΈΠΉ ΡΠ°ΡΡΠ΅Ρ Π°ΠΏΠΏΠ°ΡΠ°ΡΠ°
4.3 ΠΡΠΎΡΠ½ΠΎΡΡΠ½ΠΎΠΉ ΡΠ°ΡΡΠ΅Ρ Π°ΠΏΠΏΠ°ΡΠ°ΡΠ°
4.4 ΠΠΊΡΠΏΠ»ΡΠ°ΡΠ°ΡΠΈΡ Π°ΠΏΠΏΠ°ΡΠ°ΡΠ°
5. ΠΡΠ³Π°Π½ΠΈΠ·Π°ΡΠΈΡ ΡΡΡΠ΄Π° Π½Π° ΠΏΡΠ΅Π΄ΠΏΡΠΈΡΡΠΈΠΈ
6. Π’Π΅Ρ Π½ΠΈΠΊΠΎ-ΡΠΊΠΎΠ½ΠΎΠΌΠΈΡΠ΅ΡΠΊΠΈΠ΅ ΠΏΠΎΠΊΠ°Π·Π°ΡΠ΅Π»ΠΈ
7. ΠΠΎΠ½ΡΡΡΡΠΊΡΠΈΠ²Π½ΡΠ΅ ΡΠ΅ΡΠ΅Π½ΠΈΡ
7.1 Π€ΡΠ½Π΄Π°ΠΌΠ΅Π½ΡΡ
7.2 Π‘ΡΠ΅Π½Ρ
7.3 ΠΠ΅ΡΠ΅Π³ΠΎΡΠΎΠ΄ΠΊΠΈ
7.4 ΠΠ΅ΡΠ΅ΠΊΡΡΡΠΈΡ
7.5 ΠΡΠΎΠ²Π»Ρ
7.6 ΠΡΠ΄Π΅Π»ΠΎΡΠ½ΡΠ΅ ΡΠ°Π±ΠΎΡΡ
7.7 ΠΠΎΠ»Ρ
8. Π Π°ΡΡΠ΅Ρ Π±ΠΈΠ·Π½Π΅Ρ ΠΏΠ»Π°Π½Π° ΠΊΠΎΠ»Π±Π°ΡΠ½ΠΎΠ³ΠΎ ΠΌΠΈΠ½ΠΈ ΡΠ΅Ρ Π°
ΠΠΈΡΠ΅ΡΠ°ΡΡΡΠ°
1. ΠΠ²Π΅Π΄Π΅Π½ΠΈΠ΅
ΠΡΠΎΠΈΠ·Π²ΠΎΠ΄ΡΡΠ²ΠΎ ΠΌΡΡΠ° ΠΈ ΠΌΡΡΠ½ΡΡ
ΠΏΡΠΎΠ΄ΡΠΊΡΠΎΠ² Π²ΠΊΠ»ΡΡΠ°ΡΡ Π²ΠΈΠ΄Ρ Π΄Π΅ΡΡΠ΅Π»ΡΠ½ΠΎΡΡΠΈ, ΡΠ²ΡΠ·Π°Π½Π½ΡΠ΅ Ρ ΡΠ±ΠΎΠ΅ΠΌ, ΠΎΠ±ΡΠ°Π±ΠΎΡΠΊΠΎΠΉ ΠΈ ΡΠΏΠ°ΠΊΠΎΠ²ΡΠ²Π°Π½ΠΈΠ΅ΠΌ ΠΌΡΡΠ° ΠΊΡΡΠΏΠ½ΠΎΠ³ΠΎ ΡΠΎΠ³Π°ΡΠΎΠ³ΠΎ ΡΠΊΠΎΡΠ°, ΡΠ²ΠΈΠ½Π΅ΠΉ, ΠΎΠ²Π΅Ρ, ΠΊΠΎΠ· ΠΈ Π΄Ρ., ΠΏΡΠΎΠΈΠ·Π²ΠΎΠ΄ΡΡΠ²ΠΎΠΌ ΡΠ²Π΅ΠΆΠ΅Π³ΠΎ, ΠΎΡ
Π»Π°ΠΆΠ΄Π΅Π½Π½ΠΎΠ³ΠΎ ΠΈΠ»ΠΈ Π·Π°ΠΌΠΎΡΠΎΠΆΠ΅Π½Π½ΠΎΠ³ΠΎ ΠΌΡΡΠ°, ΠΏΡΠΎΠΈΠ·Π²ΠΎΠ΄ΡΡΠ²ΠΎΠΌ ΠΌΡΡΠ½ΡΡ
ΠΏΡΠΎΠ΄ΡΠΊΡΠΎΠ² Ρ ΠΏΠΎΠΌΠΎΡΡΡ ΡΠ°ΠΊΠΈΡ
ΠΏΡΠΎΡΠ΅ΡΡΠΎΠ² ΠΊΠ°ΠΊ:
ΡΡΡΠΊΠ°;
ΠΊΠΎΠΏΡΠ΅Π½ΠΈΠ΅;
ΡΠΎΠ»Π΅Π½ΠΈΠ΅;
ΠΏΠΎΠ³ΡΡΠΆΠ΅Π½ΠΈΠ΅ Π² ΡΠ°ΡΡΠΎΠ»;
ΠΊΠΎΠ½ΡΠ΅ΡΠ²ΠΈΡΠΎΠ²Π°Π½ΠΈΠ΅.
Π‘ΡΠ΄Π° Π²ΠΊΠ»ΡΡΠ°Π΅ΡΡΡ ΠΏΡΠΎΠΈΠ·Π²ΠΎΠ΄ΡΡΠ²ΠΎ ΠΊΠΎΠ»Π±Π°Ρ, Π²ΡΡΠ°ΠΏΠ»ΠΈΠ²Π°Π½ΠΈΠ΅ ΠΈ ΠΎΡΠΈΡΡΠΊΠ° ΡΠ²ΠΈΠ½ΠΎΠ³ΠΎ ΡΠ°Π»Π° ΠΈ Π΄ΡΡΠ³ΠΈΡ
ΠΆΠΈΡΠΎΠ².
ΠΠ° ΡΠ΅Π»ΡΡΠΊΠΎΡ
ΠΎΠ·ΡΠΉΡΡΠ²Π΅Π½Π½ΡΡ
ΠΏΡΠ΅Π΄ΠΏΡΠΈΡΡΠΈΡΡ
ΡΠΈΡΠΎΠΊΠΎΠ΅ ΡΠ°ΡΠΏΡΠΎΡΡΡΠ°Π½Π΅Π½ΠΈΠ΅ ΠΏΠΎΠ»ΡΡΠΈΠ»ΠΈ ΠΌΡΡΠΎΠΏΠ΅ΡΠ΅ΡΠ°Π±Π°ΡΡΠ²Π°ΡΡΠΈΠ΅ ΡΠ΅Ρ
Π° ΠΌΠ°Π»ΠΎΠΉ ΠΈ ΡΡΠ΅Π΄Π½Π΅ΠΉ ΠΌΠΎΡΠ½ΠΎΡΡΠΈ, Π² ΠΎΡΠ½ΠΎΠ²Π½ΠΎΠΌ ΠΊΠΎΠ»Π±Π°ΡΠ½ΡΠ΅.
ΠΠΎΡΠ½ΠΎΡΡΡ ΠΌΡΡΠΎΠΏΠ΅ΡΠ΅ΡΠ°Π±Π°ΡΡΠ²Π°ΡΡΠΈΡ
ΠΏΡΠ΅Π΄ΠΏΡΠΈΡΡΠΈΠΉ ΠΎΠ±ΡΡΠ½ΠΎ Π½Π΅ ΠΏΡΠ΅Π²ΡΡΠ°Π΅Ρ 2-Ρ
ΡΠΎΠ½Π½ ΠΌΡΡΠ½ΡΡ
ΠΏΡΠΎΠ΄ΡΠΊΡΠΎΠ² Π² ΡΠΌΠ΅Π½Ρ. Π’Π°ΠΊΠΈΠ΅ ΠΏΡΠ΅Π΄ΠΏΡΠΈΡΡΠΈΡ ΠΏΠΎΠ»ΡΡΠΈΠ»ΠΈ Π½Π°Π·Π²Π°Π½ΠΈΠ΅ ΠΌΠΈΠ½ΠΈ-Π·Π°Π²ΠΎΠ΄ΠΎΠ² ΠΌΠ°Π»ΠΎΠΉ (Π΄ΠΎ 1 ΡΠΎΠ½Π½Ρ) ΠΈ ΡΡΠ΅Π΄Π½Π΅ΠΉ (Π΄ΠΎ 2-Ρ
ΡΠΎΠ½Π½) ΠΌΠΎΡΠ½ΠΎΡΡΠΈ.
Π Π·Π°Π²ΠΈΡΠΈΠΌΠΎΡΡΠΈ ΠΎΡ Π²ΠΈΠ΄Π° ΠΏΡΠΎΠΈΠ·Π²ΠΎΠ΄ΠΈΠΌΠΎΠΉ ΠΏΡΠΎΠ΄ΡΠΊΡΠΈΠΈ, ΡΠ΅Ρ
Π½ΠΎΠ»ΠΎΠ³ΠΈΡΠ΅ΡΠΊΠΎΠ΅ ΠΎΠ±ΠΎΡΡΠ΄ΠΎΠ²Π°Π½ΠΈΠ΅ ΠΌΠΈΠ½ΠΈ-ΡΠ΅Ρ
ΠΎΠ² ΠΌΠ°Π»ΠΎΠΉ ΠΌΠΎΡΠ½ΠΎΡΡΠΈ Π²ΠΊΠ»ΡΡΠ°Π΅Ρ 8 — 12 Π΅Π΄ΠΈΠ½ΠΈΡ. Π ΡΠΎΡΡΠ°Π² ΠΎΠ±ΠΎΡΡΠ΄ΠΎΠ²Π°Π½ΠΈΡ ΡΠ°ΠΊΠΎΠ³ΠΎ ΡΠ΅Ρ
Π° Π²Ρ
ΠΎΠ΄ΡΡ:
ΠΏΠΈΡΠ΅Π²Π°ΡΠΎΡΠ½ΡΠΉ ΠΊΠΎΡΠ΅Π»;
ΠΌΡΡΠΎΡΡΠ±ΠΊΠ°;
ΡΠ°ΡΡΠ΅ΠΌΠ΅ΡΠ°Π»ΠΊΠ°, Π»ΠΎΡΠΊΠΈ Π΄Π»Ρ ΡΠ°ΡΡΠ°;
Π²Π°ΠΊΡΡΠΌΠ½ΡΠΉ ΡΠΏΡΠΈΡ;
ΠΊΠΎΠΏΡΠΈΠ»ΡΠ½Π°Ρ ΠΏΠ΅ΡΡ;
Π·Π°ΡΠΎΠ»ΠΎΡΠ½ΡΠ΅ Π²Π°Π½Π½Ρ;
Π΄ΠΎΡΠΊΠΈ ΠΈ Π½ΠΎΠΆΠΈ ΡΠ°Π·Π΄Π΅Π»ΠΎΡΠ½ΡΠ΅;
ΡΡΠΎΠ» ΠΈ ΡΠ΅Π»Π΅ΠΆΠΊΠ°.
ΠΠΎΠ»Π΅Π΅ ΡΠΈΡΠΎΠΊΠΈΠΉ Π°ΡΡΠΎΡΡΠΈΠΌΠ΅Π½Ρ ΠΏΡΠΎΠ΄ΡΠΊΡΠΈΠΈ ΠΌΠΎΠΆΠ½ΠΎ Π²ΡΡΠ°Π±Π°ΡΡΠ²Π°ΡΡ Π² ΡΠΎΠΌ ΡΠ»ΡΡΠ°Π΅, Π΅ΡΠ»ΠΈ ΡΠ΅Ρ
Π½ΠΎΠ»ΠΎΠ³ΠΈΡΠ΅ΡΠΊΠΎΠ΅ ΠΎΠ±ΠΎΡΡΠ΄ΠΎΠ²Π°Π½ΠΈΠ΅ ΡΠ΅Ρ
Π° ΠΏΠΎΠ·Π²ΠΎΠ»ΡΠ΅Ρ ΠΏΠΎΠ»ΡΡΠ°ΡΡ ΡΠ°ΡΡ ΠΊΠ°ΠΊ Π³ΡΡΠ±ΠΎΠ³ΠΎ, ΡΠ°ΠΊ ΠΈ ΡΠΎΠ½ΠΊΠΎΠ³ΠΎ ΠΈΠ·ΠΌΠ΅Π»ΡΡΠ΅Π½ΠΈΡ.
Π‘ΡΠ΅Π΄ΠΈ ΠΌΠ°Π»ΡΡ
ΠΊΠΎΠ»Π±Π°ΡΠ½ΡΡ
ΡΠ΅Ρ
ΠΎΠ² ΠΎΡΠΎΠ±ΠΎΠ΅ ΠΌΠ΅ΡΡΠΎ Π·Π°Π½ΠΈΠΌΠ°ΡΡ ΠΌΡΡΠΎΠΏΠ΅ΡΠ΅ΡΠ°Π±Π°ΡΡΠ²Π°ΡΡΠΈΠ΅ Π»ΠΈΠ½ΠΈΠΈ, ΡΠ°Π·ΠΌΠ΅ΡΠ΅Π½Π½ΡΠ΅ Π² ΡΠΏΠ΅ΡΠΈΠ°Π»ΡΠ½ΡΡ
ΠΌΠΎΠ΄ΡΠ»ΡΡ
. Π‘ΡΠ΅Π΄ΠΈ Π½ΠΈΡ
— ΠΌΠ°Π»ΡΠΉ ΠΊΠΎΠ»Π±Π°ΡΠ½ΡΠΉ ΡΠ΅Ρ
Π² ΠΊΠΎΠ½ΡΠ΅ΠΉΠ½Π΅ΡΠ½ΠΎΠΌ ΠΈΡΠΏΠΎΠ»Π½Π΅Π½ΠΈΠΈ ΠΠΠ¦-300Π. ΠΠ½ ΠΏΡΠ΅Π΄Π½Π°Π·Π½Π°ΡΠ΅Π½ Π΄Π»Ρ ΠΏΡΠΎΠΈΠ·Π²ΠΎΠ΄ΡΡΠ²Π° Π²Π°ΡΠ΅Π½ΡΡ
, Π²Π°ΡΠ΅Π½ΠΎ-ΠΊΠΎΠΏΡΠ΅Π½ΡΡ
, ΠΏΠΎΠ»ΡΠΊΠΎΠΏΡΠ΅Π½ΡΡ
ΠΊΠΎΠ»Π±Π°Ρ Ρ ΡΠ°Π·Π»ΠΈΡΠ½ΠΎΠΉ ΠΎΠ±ΠΎΠ»ΠΎΡΠΊΠΎΠΉ, Π° ΡΠ°ΠΊ ΠΆΠ΅ ΡΡΡΡΠ½ΡΡ
ΠΊΠΎΠΏΡΠ΅Π½ΠΎΡΡΠ΅ΠΉ. ΠΠ±ΡΠ°Ρ ΠΏΡΠΎΠΈΠ·Π²ΠΎΠ΄ΠΈΡΠ΅Π»ΡΠ½ΠΎΡΡΡ ΡΠ΅Ρ
Π° — 200 ΠΊΠ³ Π³ΠΎΡΠΎΠ²ΡΡ
ΠΊΠΎΠ»Π±Π°ΡΠ½ΡΡ
ΠΈΠ·Π΄Π΅Π»ΠΈΠΉ ΠΈ 300 ΠΊΠ³ ΠΌΡΡΠ½ΡΡ
ΠΊΠΎΠΏΡΠ΅Π½ΡΡ
ΠΈΠ·Π΄Π΅Π»ΠΈΠΉ Π² ΡΠΌΠ΅Π½Ρ.
2. Π’Π΅Ρ Π½ΠΎΠ»ΠΎΠ³ΠΈΡ ΠΏΡΠΎΠΈΠ·Π²ΠΎΠ΄ΡΡΠ²Π° ΠΊΠΎΠ»Π±Π°Ρ
ΠΠΈΠ»ΠΎΠ²Π°Π½Π½ΡΡ Π³ΠΎΠ²ΡΠ΄ΠΈΠ½Ρ — ΡΠ²ΠΈΠ½ΠΈΠ½Ρ, Π³ΡΡΠ΄ΠΈΠ½ΠΊΡ, ΠΏΠΎΠ»ΠΎΡΡ ΡΠΏΠΈΠ³Π° Π·Π°ΠΌΠΎΡΠ°ΠΆΠΈΠ²Π°ΡΡ Π² ΡΠ°Π·ΠΈΠΊΠ°Ρ ΠΈΠ»ΠΈ Π½Π° ΠΏΡΠΎΡΠΈΠ²Π½ΡΡ ΡΠ»ΠΎΠ΅ΠΌ Π½Π΅ Π±ΠΎΠ»Π΅Π΅ 10 ΡΠΌ Π² ΠΌΠΎΡΠΎΠ·ΠΈΠ»ΡΠ½ΠΎΠΉ ΠΊΠ°ΠΌΠ΅ΡΠ΅ Π΄ΠΎ ΡΠ΅ΠΌΠΏΠ΅ΡΠ°ΡΡΡΡ ΠΌΠΈΠ½ΡΡ (1-5) Π‘ Π² ΡΠΎΠ»ΡΠ΅ ΠΊΡΡΠΊΠ° ΠΈΠ»ΠΈ Π±Π»ΠΎΠΊΠ° Π² ΡΠ΅ΡΠ΅Π½ΠΈΠ΅ 8-12 Ρ ΠΈΠ»ΠΈ Π½Π° Π°Π³ΡΠ΅Π³Π°ΡΠ΅ Π΄Π»Ρ ΠΏΠΎΠ΄ΠΌΠΎΡΠ°ΠΆΠΈΠ²Π°Π½ΠΈΡ ΠΌΡΡΠ° ΠΈ ΡΠΏΠΈΠ³Π° Ρ ΠΏΠΎΡΠ»Π΅Π΄ΡΡΡΠΈΠΌ Π²ΡΡΠ°Π²Π½ΠΈΠ²Π°Π½ΠΈΠ΅ΠΌ ΡΠ΅ΠΌΠΏΠ΅ΡΠ°ΡΡΡΡ ΠΏΠΎ Π²ΡΠ΅ΠΌΡ ΠΎΠ±ΡΠ΅ΠΌΡ Π±Π»ΠΎΠΊΠ° Π΄ΠΎ ΠΌΠΈΠ½ΡΡ (1-3) Π‘ Π² ΠΊΠ°ΠΌΠ΅ΡΠ΅ Π½Π°ΠΊΠΎΠΏΠΈΡΠ΅Π»Π΅. ΠΠ΅ΡΠ΅ΡΠ°Π±ΠΎΡΠΊΡ Π·Π°ΠΌΠΎΡΠΎΠΆΠ΅Π½Π½ΡΡ Π±Π»ΠΎΠΊΠΎΠ² ΠΆΠΈΠ»ΠΎΠ²Π°Π½Π½ΠΎΠ³ΠΎ ΠΌΡΡΠ° ΠΏΡΠΎΠ²ΠΎΠ΄ΡΡ Ρ ΠΏΡΠ΅Π΄Π²Π°ΡΠΈΡΠ΅Π»ΡΠ½ΡΠΌ ΠΎΡΠ΅ΠΏΠ»Π΅Π½ΠΈΠ΅ΠΌ Π΄ΠΎ ΡΠ΅ΠΌΠΏΠ΅ΡΠ°ΡΡΡΡ ΠΌΠΈΠ½ΡΡ (1-5) Π‘, Π Π΅ΠΊΠΎΠΌΠ΅Π½Π΄ΡΠ΅ΡΡΡ ΠΈΡ ΠΏΡΠ΅Π΄Π²Π°ΡΠΈΡΠ΅Π»ΡΠ½ΠΎ ΠΈΠ·ΠΌΠ΅Π»ΡΡΠ°ΡΡ Π½Π° ΠΌΠ°ΡΠΈΠ½Π°Ρ Π΄Π»Ρ ΠΈΠ·ΠΌΠ΅Π»ΡΡΠ΅Π½ΠΈΡ ΠΌΡΡΠ½ΡΡ Π±Π»ΠΎΠΊΠΎΠ² Π½Π° ΠΊΡΡΠΊΠΈ ΡΠΎΠ»ΡΠΈΠ½ΠΎΠΉ ΠΏΡΠΈΠΌΠ΅ΡΠ½ΠΎ ΠΎΡ 30 Π΄ΠΎ 50 ΠΌΠΌ.ΠΡΠΈΠ³ΠΎΡΠΎΠ²Π»Π΅Π½ΠΈΠ΅ ΡΠ°ΡΡΠ°. ΠΡΠΈΠ³ΠΎΡΠΎΠ²Π»Π΅Π½ΠΈΠ΅ ΡΠ°ΡΡΠ° ΠΎΡΡΡΠ΅ΡΡΠ²Π»ΡΠ΅ΡΡΡ Π½Π° ΠΊΡΡΡΠ΅ΡΠ°Ρ (ΡΠΈΠΏΠ° Π€ΠΠ «ΠΡΠ΅ΠΌΠ΅Ρ-1 ΠΡΠ°Π±Π±Π΅» ΠΈΠ»ΠΈ «ΠΡΡ ΠΠ°ΡΡΠ΅Ρ — 500»), ΠΏΡΠ΅Π΄Π½Π°Π·Π½Π°ΡΠ΅Π½Π½ΡΡ Π΄Π»Ρ ΠΈΠ·ΠΌΠ΅Π»ΡΡΠ΅Π½ΠΈΡ Π·Π°ΠΌΠΎΡΠΎΠΆΠ΅Π½Π½ΠΎΠ³ΠΎ ΠΌΡΡΠ°. ΠΡΠΈ ΠΈΠ·ΠΌΠ΅Π»ΡΡΠ΅Π½ΠΈΠΈ ΠΊΡΡΠΏΠ½ΡΡ ΠΊΡΡΠΊΠΎΠ² Π³ΠΎΠ²ΡΠ΄ΠΈΠ½Ρ ΠΈ Π½Π΅ΠΆΠΈΡΠ½ΠΎΠΉ ΡΠ²ΠΈΠ½ΠΈΠ½Ρ, ΠΏΡΠΈΠΌΠ΅ΡΠ½ΠΎ ΡΠ΅ΡΠ΅Π· 3 ΠΌΠΈΠ½ Π΄ΠΎΠ±Π°Π²Π»ΡΡΡ ΡΠΎΠ»Ρ, ΠΏΡΡΠ½ΠΎΡΡΠΈ, Π³Π»ΡΠΊΠΎΠ·Ρ, ΠΌΠ°Π»ΡΡΠΎΠ΄Π΅ΠΊΡΡΡΠΈΠ½Ρ, ΡΠ΅ΡΠ½ΠΎΠΊ, Π²ΠΈΠ½Π½ΠΎ-ΡΠΏΠΈΡΡΠΎΠ²ΡΡ ΠΊΠΎΠΌΠΏΠΎΠ·ΠΈΡΠΈΡ, Π½ΠΈΡΡΠΈΡ Π½Π°ΡΡΠΈΡ (10 Π³ Π² Π²ΠΈΠ΄Π΅ ΡΠ°ΡΡΠ²ΠΎΡΠ° 5% ΠΊΠΎΠ½ΡΠ΅Π½ΡΡΠ°ΡΠΈΠΈ), ΡΡΡ ΠΎΠ΅ ΠΌΠΎΠ»ΠΎΠΊΠΎ, Π·Π°ΡΠ΅ΠΌ Π² ΠΌΠ΅ΡΠ°Π»ΠΊΡ Π΄ΠΎΠ±Π°Π²Π»ΡΡΡ ΡΠ²ΠΈΠ½ΠΈΠ½Ρ ΠΊΠΎΠ»Π±Π°ΡΠ½ΡΡ, Π³ΡΡΠ΄ΠΈΠ½ΠΊΡ, ΡΠΏΠΈΠ³ ΠΈ ΠΏΡΠΎΠ΄ΠΎΠ»ΠΆΠ°ΡΡ ΠΊΡΡΡΠ΅ΡΠΎΠ²Π°ΡΡ. ΠΠΊΠΎΠ½ΡΠ°Π½ΠΈΠ΅ ΠΏΡΠΎΡΠ΅ΡΡΠ° ΠΊΡΡΡΠ΅ΡΠΎΠ²Π°Π½ΠΈΡ ΠΎΠΏΡΠ΅Π΄Π΅Π»ΡΡΡ ΠΏΠΎ ΡΠΈΡΡΠ½ΠΊΡ ΡΠ°ΡΡΠ°. Π‘ΡΠ°Π²Π½ΠΈΡΠ΅Π»ΡΠ½ΠΎ ΠΎΠ΄ΠΈΠ½Π°ΠΊΠΎΠ²ΡΠ΅ ΠΏΠΎ Π²Π΅Π»ΠΈΡΠΈΠ½Π΅ ΠΊΡΡΠΎΡΠΊΠΈ Π³ΡΡΠ΄ΠΈΠ½ΠΊΠΈ, ΡΠ²ΠΈΠ½ΠΈΠ½Ρ ΠΊΠΎΠ»Π±Π°ΡΠ½ΠΎΠΉ ΠΈΠ»ΠΈ ΡΠΏΠΈΠ³Π° Π΄ΠΎΠ»ΠΆΠ½Ρ Π±ΡΡΡ ΡΠ°Π²Π½ΠΎΠΌΠ΅ΡΠ½ΠΎ ΡΠ°ΡΠΏΡΠ΅Π΄Π΅Π»Π΅Π½Ρ Π² ΡΠ°ΡΡΠ΅, ΡΠ°Π·ΠΌΠ΅ΡΠΎΠΌ, ΡΠΎΠΎΡΠ²Π΅ΡΡΡΠ²ΡΡΡΠΈΠΌ ΠΊΠ°ΠΆΠ΄ΠΎΠΌΡ Π½Π°ΠΈΠΌΠ΅Π½ΠΎΠ²Π°Π½ΠΈΡ ΠΊΠΎΠ»Π±Π°ΡΡ. Π’Π΅ΠΌΠΏΠ΅ΡΠ°ΡΡΡΠ° ΡΠ°ΡΡΠ° ΠΏΠΎΡΠ»Π΅ ΠΊΡΡΡΠ΅ΡΠΎΠ²Π°Π½ΠΈΡ ΠΌΠΈΠ½ΡΡ (1-3) Π‘.
ΠΠ°ΠΏΠΎΠ»Π½Π΅Π½ΠΈΠ΅ ΠΎΠ±ΠΎΠ»ΠΎΡΠ΅ΠΊ ΡΠ°ΡΡΠ΅ΠΌ ΠΠ°ΠΏΠΎΠ»Π½Π΅Π½ΠΈΠ΅ ΠΎΠ±ΠΎΠ»ΠΎΡΠ΅ΠΊ ΡΠ°ΡΡΠ΅ΠΌ ΠΏΡΠΎΠ²ΠΎΠ΄ΡΡ Π½Π° Π°Π²ΡΠΎΠΌΠ°ΡΠ°Ρ ΡΠΈΠΏΠ° (Handtmann-300, ΠΠ°ΡΠ»-Π¨Π½Π΅Π»Π») Π³ΠΈΠ΄ΡΠ°Π²Π»ΠΈΡΠ΅ΡΠΊΠΈΠΌΠΈ ΡΠΏΡΠΈΡΠ°ΠΌΠΈ. Π Π΅ΠΊΠΎΠΌΠ΅Π½Π΄ΡΠ΅ΡΡΡ ΠΏΡΠΈΠΌΠ΅Π½ΡΡΡ ΡΠ΅Π²ΠΊΠΈ Π΄ΠΈΠ°ΠΌΠ΅ΡΡΠΎΠΌ Π½Π° 10 ΠΌΠΌ ΠΌΠ΅Π½ΡΡΠ΅ Π΄ΠΈΠ°ΠΌΠ΅ΡΡΠ° ΠΎΠ±ΠΎΠ»ΠΎΡΠΊΠΈ. ΠΠ±ΠΎΠ»ΠΎΡΠΊΡ ΡΠ»Π΅Π΄ΡΠ΅Ρ Π½Π°ΠΏΠΎΠ»Π½ΡΡΡ ΠΏΠ»ΠΎΡΠ½ΠΎ, ΠΎΡΠΎΠ±ΠΎ ΡΠΏΠ»ΠΎΡΠ½ΡΡ ΡΠ°ΡΡ ΠΏΡΠΈ Π·Π°Π²ΡΠ·ΡΠ²Π°Π½ΠΈΠΈ ΡΠ²ΠΎΠ±ΠΎΠ΄Π½ΠΎΠ³ΠΎ ΠΊΠΎΠ½ΡΠ° ΠΎΠ±ΠΎΠ»ΠΎΡΠΊΠΈ. ΠΠ°ΡΠΎΠ½Ρ ΠΏΠ΅ΡΠ΅Π²ΡΠ·ΡΠ²Π°ΡΡ ΡΠΏΠ°Π³Π°ΡΠΎΠΌ, Π½Π°Π½ΠΎΡΡ ΡΠΎΠ²Π°ΡΠ½ΡΠ΅ ΠΎΡΠΌΠ΅ΡΠΊΠΈ. ΠΠΎΠ·Π΄ΡΡ , ΠΏΠΎΠΏΠ°Π²ΡΠΈΠΉ Π² ΡΠ°ΡΡ ΠΏΡΠΈ ΡΠΏΡΠΈΡΠ΅Π²Π°Π½ΠΈΠΈ, ΡΠ΄Π°Π»ΡΡΡ ΠΏΡΡΠ΅ΠΌ ΠΏΡΠΎΠΊΠ°Π»ΡΠ²Π°Π½ΠΈΡ ΠΎΠ±ΠΎΠ»ΠΎΡΠΊΠΈ. ΠΡΠΈ Π½Π°Π»ΠΈΡΠΈΠΈ ΡΠΏΠ΅ΡΠΈΠ°Π»ΡΠ½ΠΎΠ³ΠΎ ΠΎΠ±ΠΎΡΡΠ΄ΠΎΠ²Π°Π½ΠΈΡ ΠΈ ΠΌΠ°ΡΠΊΠΈΡΠΎΠ²Π°Π½Π½ΠΎΠΉ ΠΎΠ±ΠΎΠ»ΠΎΡΠΊΠΈ ΠΏΡΠΎΠ²ΠΎΠ΄ΠΈΡΡΡ Π½Π°ΠΏΠΎΠ»Π½Π΅Π½ΠΈΠ΅ ΠΎΠ±ΠΎΠ»ΠΎΡΠ΅ΠΊ ΡΠ°ΡΡΠ΅ΠΌ, Π½Π°Π»ΠΎΠΆΠ΅Π½ΠΈΠ΅ ΡΠΊΡΠ΅ΠΏΠΎΠΊ Π½Π° ΠΊΠΎΠ½ΡΡ Π±Π°ΡΠΎΠ½ΠΎΠ² Ρ ΠΎΠ΄Π½ΠΎΠ²ΡΠ΅ΠΌΠ΅Π½Π½ΡΠΌ ΠΈΠ·Π³ΠΎΡΠΎΠ²Π»Π΅Π½ΠΈΠ΅ΠΌ ΠΈ Π²Π²ΠΎΠ΄ΠΎΠΌ ΠΏΠ΅ΡΠ»ΠΈ ΠΏΠΎΠ΄ ΡΠΊΡΠ΅ΠΏΠΊΡ. ΠΠ°ΡΠΎΠ½Ρ Π½Π°Π²Π΅ΡΠΈΠ²Π°ΡΡ Π½Π° ΠΏΠ°Π»ΠΊΠΈ, ΠΊΠΎΡΠΎΡΡΠ΅ ΡΠ°Π·ΠΌΠ΅ΡΠ°ΡΡ Π½Π° ΡΠ°ΠΌΡ ΠΈΠ»ΠΈ ΡΠΊΠ»Π°Π΄ΡΠ²Π°ΡΡ Π² Π³ΠΎΡΠΈΠ·ΠΎΠ½ΡΠ°Π»ΡΠ½ΠΎΠ΅ ΠΏΠΎΠ»ΠΎΠΆΠ΅Π½ΠΈΠ΅ Π½Π° ΡΠΏΠ΅ΡΠΈΠ°Π»ΡΠ½ΡΠ΅ Π»ΠΎΡΠΊΠΈ, ΠΏΡΠ΅Π΄ΡΡΠ°Π²Π»ΡΡΡΠΈΠ΅ ΡΠΎΠ±ΠΎΠΉ ΠΊΠ°ΡΠΊΠ°Ρ ΠΈΠ· Ρ ΡΠΎΠΌΠΈΡΡΠΎΠΉ Π½Π΅ΡΠΆΠ°Π²Π΅ΡΡΠ΅ΠΉ ΡΡΠ°Π»ΠΈ, Π½Π° ΠΊΠΎΡΠΎΡΠΎΠΌ Π·Π°ΠΊΡΠ΅ΠΏΠ»Π΅Π½Π° ΠΆΠ΅Π»ΠΎΠ±ΠΎΡΠ½Π°Ρ ΠΏΡΠΎΠΊΠ»Π°Π΄ΠΊΠ° ΠΈΠ· Π½Π΅ΡΠΆΠ°Π²Π΅ΡΡΠ΅ΠΉ ΡΠ΅ΡΠΊΠΈ Ρ ΡΡΠ΅ΠΉΠΊΠ°ΠΌΠΈ 2Ρ 2 ΠΌΠΌ. ΠΠΎΡΠΊΠΈ ΠΏΠΎΠΌΠ΅ΡΠ°ΡΡ Π² ΡΡΠ°Π½Π΄Π°ΡΡΠ½ΡΠ΅ ΡΠ°ΠΌΡ. ΠΡΠΈ Π½Π°Π²Π΅ΡΠΈΠ²Π°Π½ΠΈΠΈ ΠΏΠ° ΠΏΠ°Π»ΠΊΠΈ Π±Π°ΡΠΎΠ½Ρ Π½Π΅ Π΄ΠΎΠ»ΠΆΠ½Ρ ΡΠΎΠΏΡΠΈΠΊΠ°ΡΠ°ΡΡΡΡ Π΄ΡΡΠ³ Ρ Π΄ΡΡΠ³ΠΎΠΌ Π²ΠΎ ΠΈΠ·Π±Π΅ΠΆΠ°Π½ΠΈΠ΅ ΡΠ»ΠΈΠΏΠΎΠ², ΠΏΠΎΡΠ»Π΅ ΡΠ΅Π³ΠΎ Π½Π°Π³ΡΡΠΆΠ΅Π½Π½ΡΠ΅ Π±Π°ΡΠΎΠ½Π°ΠΌΠΈ ΡΠ°ΠΌΡ Π½Π°ΠΏΡΠ°Π²Π»ΡΡΡ Π½Π° ΠΎΡΠ°Π΄ΠΊΡ.
ΠΡΠ°Π΄ΠΊΠ° ΠΡΠ°Π΄ΠΊΡ ΠΏΡΠΎΠ²ΠΎΠ΄ΡΡ Π² ΡΠ΅ΡΠ΅Π½ΠΈΠ΅ 5-7 ΡΡΡΠΎΠΊ ΠΏΡΠΈ ΡΠ΅ΠΌΠΏΠ΅ΡΠ°ΡΡΡΠ΅ Π²ΠΎΠ·Π΄ΡΡ Π° (1) Π‘ ΠΈ ΠΎΡΠ½ΠΎΡΠΈΡΠ΅Π»ΡΠ½ΠΎΠΉ Π²Π»Π°ΠΆΠ½ΠΎΡΡΠΈ (84-90)%. Π‘ΠΊΠΎΡΠΎΡΡΡ Π΄Π²ΠΈΠΆΠ΅Π½ΠΈΡ Π²ΠΎΠ·Π΄ΡΡ Π° Π² ΠΏΡΠΎΡΠ΅ΡΡΠ΅ ΠΎΡΠ°Π΄ΠΊΠΈ 0.1 ΠΌ/ΡΠ΅ΠΊ. ΠΠΊΠΎΠ½ΡΠ°Π½ΠΈΠ΅ ΠΎΡΠ°Π΄ΠΊΠΈ ΠΎΠΏΡΠ΅Π΄Π΅Π»ΡΠ΅ΡΡΡ ΠΏΠΎ ΠΏΠΎΠ΄ΡΠΎΡ ΡΠ΅ΠΉ ΠΎΠ±ΠΎΠ»ΠΎΡΠΊΠ΅, ΠΏΠ»ΠΎΡΠ½ΠΎ ΠΎΠ±Π»Π΅Π³Π°ΡΡΠ΅ΠΉ ΠΊΠΎΠ»Π±Π°ΡΡ, ΠΏΡΠΈ Π½Π°ΠΆΠ°ΡΠΈΠΈ Π½Π° ΠΊΠΎΡΠΎΡΡΡ ΡΠ°ΡΡ Π½Π΅ Π²Π΄Π°Π²Π»ΠΈΠ²Π°Π΅ΡΡΡ, ΡΡΠ°Π½ΠΎΠ²ΠΈΡΡΡ ΡΠΏΡΡΠ³ΠΈΠΌ ΡΡΠΊΠΎ-ΠΊΡΠ°ΡΠ½ΠΎΠ³ΠΎ ΡΠ²Π΅ΡΠ°.
Π’Π΅ΡΠΌΠΈΡΠ΅ΡΠΊΠ°Ρ ΠΎΠ±ΡΠ°Π±ΠΎΡΠΊΠ°. ΠΠΎΠΏΡΠ΅Π½ΠΈΠ΅ ΠΠΎΡΠ»Π΅ ΠΎΡΠ°Π΄ΠΊΠΈ ΠΊΠΎΠ»Π±Π°ΡΡ ΠΊΠΎΠΏΡΡΡ Π² ΠΊΠΎΠΏΡΠΈΠ»ΡΠ½ΡΡ ΠΊΠ°ΠΌΠ΅ΡΠ°Ρ Π΄ΡΠΌΠΎΠΌ ΠΎΡ Π΄ΡΠ΅Π²Π΅ΡΠ½ΡΡ ΠΎΠΏΠΈΠ»ΠΎΠΊ ΡΠ²Π΅ΡΠ΄ΠΎΠ»ΠΈΡΡΠ²Π΅Π½Π½ΡΡ ΠΏΠΎΡΠΎΠ΄ (Π±ΡΠΊ, Π΄ΡΠ±, Π²ΡΠ· ΠΈ Π΄Ρ.) Π² ΡΠ΅ΡΠ΅Π½ΠΈΠ΅ 2-3 ΡΡΡΠΎΠΊ ΠΏΡΠΈ ΡΠ΅ΠΌΠΏΠ΅ΡΠ°ΡΡΡΠ΅ (18-22) Π‘ ΠΈ ΠΎΡΠ½ΠΎΡΠΈΡΠ΅Π»ΡΠ½ΠΎΠΉ Π²Π»Π°ΠΆΠ½ΠΎΡΡΠΈ (74-80)% ΠΈ ΡΠΊΠΎΡΠΎΡΡΠΈ Π΄Π²ΠΈΠΆΠ΅Π½ΠΈΡ Π²ΠΎΠ·Π΄ΡΡ Π° ΠΎΡ 0,2 Π΄ΠΎ 0.5 ΠΌ/Ρ. ΠΡΠΎΡΠ΅ΡΡ ΠΊΠΎΠΏΡΠ΅Π½ΠΈΡ ΡΠ»Π΅Π΄ΡΠ΅Ρ ΠΏΠΎΡΡΠΎΡΠ½Π½ΠΎ ΠΊΠΎΠ½ΡΡΠΎΠ»ΠΈΡΠΎΠ²Π°ΡΡ Π²ΠΎ ΠΈΠ·Π±Π΅ΠΆΠ°Π½ΠΈΠ΅ ΠΎΠ±ΡΠ°Π·ΠΎΠ²Π°Π½ΠΈΡ «Π·Π°ΠΊΠ°Π»Π°» — ΡΠΏΠ»ΠΎΡΠ½Π΅Π½Π½ΠΎΠ³ΠΎ ΠΏΠΎΠ²Π΅ΡΡ Π½ΠΎΡΡΠ½ΠΎΠ³ΠΎ ΡΠ»ΠΎΡ. Π‘ΡΡΠΊΠ°. ΠΠΎΡΠ»Π΅ ΠΊΠΎΠΏΡΠ΅Π½ΠΈΡ ΠΊΠΎΠ»Π±Π°ΡΡ ΡΡΡΠ°Ρ 5-7 ΡΡΡΠΎΠΊ Π² ΡΡΡΠΈΠ»ΠΊΠ°Ρ ΠΏΡΠΈ ΡΠ΅ΠΌΠΏΠ΅ΡΠ°ΡΡΡΠ΅ (11-15) Π‘, ΠΎΡΠ½ΠΎΡΠΈΡΠ΅Π»ΡΠ½ΠΎΠΉ Π²Π»Π°ΠΆΠ½ΠΎΡΡΠΈ Π²ΠΎΠ·Π΄ΡΡ Π° (79+85)% ΠΈ ΡΠΊΠΎΡΠΎΡΡΠΈ Π²ΠΎΠ·Π΄ΡΡ Π° 0.1 ΠΌ/Ρ. ΠΠ°Π»ΡΠ½Π΅ΠΉΡΡΡ ΡΡΡΠΊΡ ΠΏΡΠΎΠ²ΠΎΠ΄ΡΡ Π² ΡΠ΅ΡΠ΅Π½ΠΈΠ΅ 16-17 ΡΡΡΠΎΠΊ ΠΏΡΠΈ ΡΠ΅ΠΌΠΏΠ΅ΡΠ°ΡΡΡΠ΅ (10-12) Π‘, ΠΎΡΠ½ΠΎΡΠΈΡΠ΅Π»ΡΠ½ΠΎΠΉ Π²Π»Π°ΠΆΠ½ΠΎΡΡΠΈ (74-78)%, ΠΏΡΠΈ ΡΠΊΠΎΡΠΎΡΡΠΈ Π΄Π²ΠΈΠΆΠ΅Π½ΠΈΡ Π²ΠΎΠ·Π΄ΡΡ Π° 0.05-0.1 ΠΌ/Ρ. ΠΠ±ΡΠ°Ρ ΠΏΡΠΎΠ΄ΠΎΠ»ΠΆΠΈΡΠ΅Π»ΡΠ½ΠΎΡΡΡ ΡΡΡΠΊΠΈ ΡΠΎΡΡΠ°Π²Π»ΡΠ΅Ρ 21-26 ΡΡΡΠΎΠΊ Π² Π·Π°Π²ΠΈΡΠΈΠΌΠΎΡΡΠΈ ΠΎΡ Π΄ΠΈΠ°ΠΌΠ΅ΡΡΠ° ΠΎΠ±ΠΎΠ»ΠΎΡΠΊΠΈ.
Π£ΠΏΠ°ΠΊΠΎΠ²ΠΊΠ°, ΠΌΠ°ΡΠΊΠΈΡΠΎΠ²ΠΊΠ° Π£ΠΏΠ°ΠΊΠΎΠ²ΠΊΠ°. ΠΠΎΠ»Π±Π°ΡΡ, Π² ΡΠΎΠΌ ΡΠΈΡΠ»Π΅ ΡΠ°ΡΠΎΠ²Π°Π½Π½ΡΠ΅, ΡΠΏΠ°ΠΊΠΎΠ²ΡΠ²Π°ΡΡ Π² ΠΏΠΎΠ»ΠΈΠΌΠ΅ΡΠ½ΡΠ΅ ΠΌΠ½ΠΎΠ³ΠΎΠΎΠ±ΠΎΡΠΎΡΠ½ΡΠ΅ ΡΡΠΈΠΊΠΈ ΠΏΠΎ Π’Π£ 10.10.01-04-89, ΠΈΠ»ΠΈ ΡΠ°ΡΡ, ΠΈΠ·Π³ΠΎΡΠΎΠ²Π»Π΅Π½Π½ΡΡ ΠΈΠ· Π΄ΡΡΠ³ΠΈΡ ΠΌΠ°ΡΠ΅ΡΠΈΠ°Π»ΠΎΠ², ΡΠ°Π·ΡΠ΅ΡΠ΅Π½Π½ΡΡ Π΄Π»Ρ ΠΊΠΎΠ½ΡΠ°ΠΊΡΠ° Ρ ΠΏΠΈΡΠ΅Π²ΠΎΠΉ ΠΏΡΠΎΠ΄ΡΠΊΡΠΈΠ΅ΠΉ ΠΎΡΠ³Π°Π½Π°ΠΌΠΈ ΠΈ ΡΡΡΠ΅ΠΆΠ΄Π΅Π½ΠΈΡΠΌΠΈ ΠΠΎΡΡΠ°Π½ΡΠΏΠΈΠ΄Π½Π°Π΄Π·ΠΎΡΠ°, Π° ΡΠ°ΠΊΠΆΠ΅ ΠΊΠΎΠ½ΡΠ΅ΠΉΠ½Π΅ΡΡ ΠΈΠ»ΠΈ ΡΠ°ΡΡ — ΠΎΠ±ΠΎΡΡΠ΄ΠΎΠ²Π°Π½ΠΈΠ΅ ΠΏΠΎ Π’Π£ 10.02.07.00 49-88. Π’Π°ΡΠ° Π΄ΠΎΠ»ΠΆΠ½Π° Π±ΡΡΡ ΡΠΈΡΡΠΎΠΉ, ΡΡΡ ΠΎΠΉ, Π±Π΅Π· ΠΏΠ»Π΅ΡΠ΅Π½ΠΈ ΠΈ ΠΏΠΎΡΡΠΎΡΠΎΠ½Π½Π΅Π³ΠΎ Π·Π°ΠΏΠ°Ρ Π°. ΠΠ½ΠΎΠ³ΠΎΠΎΠ±ΠΎΡΠΎΡΠ½Π°Ρ ΡΠ°ΡΠ° Π΄ΠΎΠ»ΠΆΠ½Π° ΠΈΠΌΠ΅ΡΡ ΠΊΡΡΡΠΊΡ. ΠΡΠΈ ΠΎΡΡΡΡΡΡΠ²ΠΈΠΈ ΠΊΡΡΡΠΊΠΈ Π΄ΠΎΠΏΡΡΠΊΠ°Π΅ΡΡΡ Π΄Π»Ρ ΠΌΠ΅ΡΡΠ½ΠΎΠΉ ΡΠ΅Π°Π»ΠΈΠ·Π°ΡΠΈΠΈ ΡΠ°ΡΡ Π½Π°ΠΊΡΡΠ²Π°ΡΡ ΠΎΠ±Π΅ΡΡΠΎΡΠ½ΠΎΠΉ Π±ΡΠΌΠ°Π³ΠΎΠΉ, ΠΏΠ΅ΡΠ³Π°ΠΌΠ΅Π½ΡΠΎΠΌ, ΠΏΠΎΠ΄ΠΏΠ΅ΡΠ³Π°ΠΌΠ΅Π½ΡΠΎΠΌ. ΠΠΎΠΏΡΡΠΊΠ°Π΅ΡΡΡ Π²ΡΠΏΡΡΠΊΠ°ΡΡ ΡΡΡΠΎΠΊΠΎΠΏΡΠ΅Π½ΡΠ΅ ΠΊΠΎΠ»Π±Π°ΡΡ ΡΠΏΠ°ΠΊΠΎΠ²Π°Π½Π½ΡΠΌΠΈ ΠΏΠΎΠ΄ Π²Π°ΠΊΡΡΠΌΠΎΠΌ Π² ΠΏΡΠΎΠ·ΡΠ°ΡΠ½ΡΠ΅ Π³Π°Π·ΠΎΠ½Π΅ΠΏΡΠΎΠ½ΠΈΡΠ°Π΅ΠΌΡΠ΅ ΠΏΠ»Π΅Π½ΠΊΠΈ ΠΈΠ»ΠΈ ΠΏΠ°ΠΊΠ΅ΡΡ ΠΈΠ· Π½Π΅Π΅, ΠΏΡΠΈ ΡΠ΅ΡΠ²ΠΈΡΠΎΠ²ΠΎΡΠ½ΠΎΠΉ Π½Π°ΡΠ΅Π·ΠΊΠ΅ (Π»ΠΎΠΌΡΠΈΠΊΠ°ΠΌΠΈ) ΠΌΠ°ΡΡΠΎΠΉ Π½Π΅ΡΡΠΎ ΠΏΠΎ 100, 150, 200, 250 Π³ ΠΈΠ»ΠΈ ΠΌΠ°ΡΡΠΎΠΉ Π½Π΅ΡΡΠΎ ΠΎΡ 100 Π΄ΠΎ 250 Π³ ΠΏΡΠΈ ΠΏΠΎΡΡΠΈΠΎΠ½Π½ΠΎΠΉ Π½Π°ΡΠ΅Π·ΠΊΠ΅ (ΡΠ΅Π»ΡΠΌ ΠΊΡΡΠΊΠΎΠΌ), ΠΏΠΎΡΡΠΈΡΠΌΠΈ ΠΈΠ»ΠΈ ΡΠ΅Π»ΡΠΌΠΈ Π±Π°ΡΠΎΠ½Π°ΠΌΠΈ. ΠΠΎΠΏΡΡΠΊΠ°Π΅ΡΡΡ ΠΈΠ·Π³ΠΎΡΠ°Π²Π»ΠΈΠ²Π°ΡΡ Π΄Π»Ρ ΠΌΠ΅ΡΡΠ½ΠΎΠΉ ΡΠ΅Π°Π»ΠΈΠ·Π°ΡΠΈΠΈ Π½Π΅ΡΠ΅Π»ΡΠ΅ Π±Π°ΡΠΎΠ½Ρ ΡΡΡΠΎΠΊΠΎΠΏΡΠ΅Π½ΡΡ ΠΊΠΎΠ»Π±Π°Ρ ΠΌΠ°ΡΡΠΎΠΉ Π½Π΅ ΠΌΠ΅Π½Π΅Π΅ 250 Π³. ΠΡΠΈ ΡΡΠΎΠΌ ΡΡΠ΅Π·Π°Π½Π½ΡΠ΅ ΠΊΠΎΠ½ΡΡ Π±Π°ΡΠΎΠ½ΠΎΠ² Π΄ΠΎΠ»ΠΆΠ½Ρ Π±ΡΡΡ ΠΎΠ±Π΅ΡΠ½ΡΡΡ ΡΠ°Π»ΡΠ΅ΡΠΊΠΎΠΉ ΠΈΠ· ΡΠ΅Π»Π»ΡΠ»ΠΎΠ·Π½ΠΎΠΉ ΠΏΠ»Π΅Π½ΠΊΠΈ, ΠΏΠ΅ΡΠ³Π°ΠΌΠ΅Π½ΡΠ°, ΠΏΠΎΠ΄ΠΏΠ΅ΡΠ³Π°ΠΌΠ΅Π½ΡΠ° ΠΈΠ»ΠΈ Π΄ΡΡΠ³ΠΈΡ ΠΌΠ°ΡΠ΅ΡΠΈΠ°Π»ΠΎΠ², ΡΠ°Π·ΡΠ΅ΡΠ΅Π½Π½ΡΡ Π΄Π»Ρ ΠΏΡΠΈΠΌΠ΅Π½Π΅Π½ΠΈΡ Π² ΠΌΡΡΠ½ΠΎΠΉ ΠΏΡΠΎΠΌΡΡΠ»Π΅Π½Π½ΠΎΡΡΠΈ, ΠΈ ΠΏΠ΅ΡΠ΅Π²ΡΠ·Π°Π½Ρ ΡΠΏΠ°Π³Π°ΡΠΎΠΌ, Π½ΠΈΡΠΊΠ°ΠΌΠΈ ΠΈΠ»ΠΈ ΡΠ΅Π·ΠΈΠ½ΠΎΠ²ΠΎΠΉ ΠΎΠ±Ρ Π²Π°ΡΠΊΠΎΠΉ. ΠΠΎΠ»ΠΈΡΠ΅ΡΡΠ²ΠΎ Π½Π΅ΡΠ΅Π»ΡΡ Π±Π°ΡΠΎΠ½ΠΎΠ² Π½Π΅ Π΄ΠΎΠ»ΠΆΠ½ΠΎ ΠΏΡΠ΅Π²ΡΡΠ°ΡΡ 5% ΠΎΡ ΠΏΠ°ΡΡΠΈΠΈ. Π ΠΊΠ°ΠΆΠ΄ΡΠΉ ΡΡΠΈΠΊ ΠΈΠ»ΠΈ ΠΊΠΎΠ½ΡΠ΅ΠΉΠ½Π΅Ρ ΡΠΏΠ°ΠΊΠΎΠ²ΡΠ²Π°ΡΡ ΠΊΠΎΠ»Π±Π°ΡΡ ΠΎΠ΄Π½ΠΎΠ³ΠΎ Π½Π°ΠΈΠΌΠ΅Π½ΠΎΠ²Π°Π½ΠΈΡ. ΠΠ°ΡΠΊΠΈΡΠΎΠ²ΠΊΠ°. Π’ΡΠ°Π½ΡΠΏΠΎΡΡΠ½Π°Ρ ΠΌΠ°ΡΠΊΠΈΡΠΎΠ²ΠΊΠ° ΠΏΠΎ ΠΠΠ‘Π’ 14192-77 Ρ Π½Π°Π½Π΅ΡΠ΅Π½ΠΈΠ΅ΠΌ ΠΌΠ°Π½ΠΈΠΏΡΠ»ΡΡΠΈΠΎΠ½Π½ΠΎΠ³ΠΎ Π·Π½Π°ΠΊΠ° «Π‘ΠΊΠΎΡΠΎΠΏΠΎΡΡΡΡΠΈΠΉΡΡ Π³ΡΡΠ·». ΠΠΎΠΏΡΡΠΊΠ°Π΅ΡΡΡ Π½Π΅ Π½Π°Π½ΠΎΡΠΈΡΡ ΡΡΠ°Π½ΡΠΏΠΎΡΡΠ½ΡΡ ΠΌΠ°ΡΠΊΠΈΡΠΎΠ²ΠΊΡ Π½Π° ΠΌΠ½ΠΎΠ³ΠΎΠΎΠ±ΠΎΡΠΎΡΠ½ΡΡ ΡΠ°ΡΡ Ρ ΠΏΡΠΎΠ΄ΡΠΊΡΠΈΠ΅ΠΉ, ΠΏΡΠ΅Π΄Π½Π°Π·Π½Π°ΡΠ΅Π½Π½ΠΎΠΉ Π΄Π»Ρ ΠΌΠ΅ΡΡΠ½ΠΎΠΉ ΡΠ΅Π°Π»ΠΈΠ·Π°ΡΠΈΠΈ. ΠΠ°ΡΠΊΠΈΡΠΎΠ²ΠΊΠ°, Ρ Π°ΡΠ°ΠΊΡΠ΅ΡΠΈΠ·ΡΡΡΠ°Ρ ΠΏΡΠΎΠ΄ΡΠΊΡΠΈΡ, Π½Π°Π½ΠΎΡΠΈΡΡΡ Π½Π° ΠΎΠ΄Π½Ρ ΠΈΠ· ΡΠΎΡΡΠΎΠ²ΡΡ ΡΡΠΎΡΠΎΠ½ ΡΡΠ°Π½ΡΠΏΠΎΡΡΠ½ΠΎΠΉ ΡΠ°ΡΡ Π½Π΅ΡΠΌΡΠ²Π°ΡΡΠ΅ΠΉΡΡ, Π½Π΅ ΠΏΠ°Ρ Π½ΡΡΠ΅ΠΉ ΠΊΡΠ°ΡΠΊΠΎΠΉ ΠΏΡΠΈ ΠΏΠΎΠΌΠΎΡΠΈ ΡΡΠ°ΠΌΠΏΠ°, ΡΡΠ°ΡΠ°ΡΠ΅ΡΠ° ΠΈΠ»ΠΈ Π½Π°ΠΊΠ»Π΅ΠΈΠ²Π°Π½ΠΈΡ ΡΡΠ»ΡΠΊΠ° Ρ ΡΠΊΠ°Π·Π°Π½ΠΈΠ΅ΠΌ: — Π½Π°ΠΈΠΌΠ΅Π½ΠΎΠ²Π°Π½ΠΈΡ ΠΏΡΠ΅Π΄ΠΏΡΠΈΡΡΠΈΡ-ΠΈΠ·Π³ΠΎΡΠΎΠ²ΠΈΡΠ΅Π»Ρ, Π΅Π³ΠΎ ΠΌΠ΅ΡΡΠΎΠ½Π°Ρ ΠΎΠΆΠ΄Π΅Π½ΠΈΡ ΠΈ ΡΠΎΠ²Π°ΡΠ½ΠΎΡ Π·Π½Π°ΠΊΠ° (ΠΏΡΠΈ Π΅Π³ΠΎ Π½Π°Π»ΠΈΡΠΈΠΈ), — Π½Π°ΠΈΠΌΠ΅Π½ΠΎΠ²Π°Π½ΠΈΡ ΠΈ ΡΠΎΡΡΠ°Π²Π° ΠΏΡΠΎΠ΄ΡΠΊΡΠ°. — Π΄Π°ΡΡ ΠΈΠ·Π³ΠΎΡΠΎΠ²Π»Π΅Π½ΠΈΡ, — ΡΡΠΎΠΊΠ° ΠΈ ΡΡΠ»ΠΎΠ²ΠΈΠΉ Ρ ΡΠ°Π½Π΅Π½ΠΈΡ, — ΠΏΠΈΡΠ΅Π²ΠΎΠΉ ΠΈ ΡΠ½Π΅ΡΠ³Π΅ΡΠΈΡΠ΅ΡΠΊΠΎΠΉ ΡΠ΅Π½Π½ΠΎΡΡΠΈ 100 Π³ ΠΏΡΠΎΠ΄ΡΠΊΡΠ°, — ΠΌΠ°ΡΡΡ Π½Π΅ΡΡΠΎ, — ΠΎΠ±ΠΎΠ·Π½Π°ΡΠ΅Π½ΠΈΡ Π½Π°ΡΡΠΎΡΡΠΈΡ ΡΠ΅Ρ Π½ΠΈΡΠ΅ΡΠΊΠΈΡ ΡΡΠ»ΠΎΠ²ΠΈΠΉ. ΠΡΠΎΠΌΠ΅ ΡΠΎΠ³ΠΎ, Π°Π½Π°Π»ΠΎΠ³ΠΈΡΠ½ΠΎ ΡΡΠ»ΡΠΊ Π²ΠΊΠ»Π°Π΄ΡΠ²Π°ΡΡ Π² ΠΊΠ°ΠΆΠ΄ΡΡ Π΅Π΄ΠΈΠ½ΠΈΡΡ ΡΠ°ΡΡ. ΠΠΎΠΏΡΡΠΊΠ°Π΅ΡΡΡ ΠΏΡΠΈ ΠΎΡΠ³ΡΡΠ·ΠΊΠ΅ ΠΏΡΠΎΠ΄ΡΠΊΡΠΈΠΈ Π΄Π»Ρ ΠΌΠ΅ΡΡΠ½ΠΎΠΉ ΡΠ΅Π°Π»ΠΈΠ·Π°ΡΠΈΠΈ ΠΌΠ½ΠΎΠ³ΠΎΠΎΠ±ΠΎΡΠΎΡΠ½ΡΡ ΡΠ°ΡΡ Π½Π΅ ΠΌΠ°ΡΠΊΠΈΡΠΎΠ²Π°ΡΡ, Π½ΠΎ ΠΎΠ±ΡΠ·Π°ΡΠ΅Π»ΡΠ½ΠΎ Π²ΠΊΠ»Π°Π΄ΡΠ²Π°ΡΡ Π² ΠΊΠ°ΠΆΠ΄ΡΠΉ ΡΡΠΈΠΊ ΠΈΠ»ΠΈ ΡΠ°ΡΡ — ΠΎΠ±ΠΎΡΡΠ΄ΠΎΠ²Π°Π½ΠΈΠ΅ ΡΡΠ»ΡΠΊ Ρ Π²ΡΡΠ΅ΠΏΠ΅ΡΠ΅ΡΠΈΡΠ»Π΅Π½Π½ΡΠΌΠΈ ΠΎΠ±ΠΎΠ·Π½Π°ΡΠ΅Π½ΠΈΡΠΌΠΈ. ΠΡΠΎΠΌΠ΅ ΡΠΎΠ³ΠΎ, Π² ΠΊΠ°ΠΆΠ΄ΡΡ Π΅Π΄ΠΈΠ½ΠΈΡΡ ΡΡΠ°Π½ΡΠΏΠΎΡΡΠ½ΠΎΠΉ ΡΠ°ΡΡ Ρ ΡΠ°ΡΠΎΠ²Π°Π½Π½ΠΎΠΉ ΠΏΡΠΎΠ΄ΡΠΊΡΠΈΠ΅ΠΉ Π²ΠΊΠ»Π°Π΄ΡΠ²Π°ΡΡ ΡΡΠΌΠΌΠ°ΡΠ½ΡΠΉ ΡΠ΅ΠΊ Ρ ΡΠΊΠ°Π·Π°Π½ΠΈΠ΅ΠΌ: Π½Π° ΠΊΠ°ΠΆΠ΄ΠΎΠΉ ΡΠΏΠ°ΠΊΠΎΠ²ΠΎΡΠ½ΠΎΠΉ
Π΅Π΄ΠΈΠ½ΠΈΡΠ΅ ΡΠ°ΡΠΎΠ²Π°Π½Π½ΠΎΠΉ ΠΏΡΠΎΠ΄ΡΠΊΡΠΈΠΈ ΡΡΠΈΠΊΠ΅ΡΠΊΠΈ Π² Π²ΠΈΠ΄Π΅ ΠΏΠ΅ΡΠ°ΡΠΈ Π½Π° ΠΏΠ»Π΅Π½ΠΊΠ΅ ΠΈΠ»ΠΈ Π½Π°ΠΊΠ»Π΅Π΅Π½Π½ΠΎΠΉ Π½Π° ΡΠΏΠ°ΠΊΠΎΠ²ΠΊΡ. ΠΠ°ΡΠΊΠΈΡΠΎΠ²Π°Π½Π½Π°Ρ ΠΎΠ±ΠΎΠ»ΠΎΡΠΊΠ° Π΄ΠΎΠ»ΠΆΠ½Π° ΡΠΎΠ΄Π΅ΡΠΆΠ°ΡΡ: — Π½Π°ΠΈΠΌΠ΅Π½ΠΎΠ²Π°Π½ΠΈΠ΅ ΠΏΡΠ΅Π΄ΠΏΡΠΈΡΡΠΈΡ-ΠΈΠ·Π³ΠΎΡΠΎΠ²ΠΈΡΠ΅Π»Ρ — Π΅Π³ΠΎ ΠΌΠ΅ΡΡΠΎΠ½Π°Ρ ΠΎΠΆΠ΄Π΅Π½ΠΈΠ΅ ΠΈ ΡΠΎΠ²Π°ΡΠ½ΡΠΉ Π·Π½Π°ΠΊ. — Π½Π°ΠΈΠΌΠ΅Π½ΠΎΠ²Π°Π½ΠΈΠ΅ ΠΏΡΠΎΠ΄ΡΠΊΡΠΈΠΈ. — ΠΎΠ±ΠΎΠ·Π½Π°ΡΠ΅Π½ΠΈΠ΅ Π½Π°ΡΡΠΎΡΡΠΈΡ ΡΠ΅Ρ Π½ΠΈΡΠ΅ΡΠΊΠΈΡ ΡΡΠ»ΠΎΠ²ΠΈΠΉ.
ΠΠΎΠ½ΡΡΠΎΠ»Ρ ΠΏΡΠΎΠΈΠ·Π²ΠΎΠ΄ΡΡΠ²Π° ΠΠ° Π²ΡΠ΅Ρ ΡΡΠ°Π΄ΠΈΡΡ ΠΏΡΠΎΠΈΠ·Π²ΠΎΠ΄ΡΡΠ²Π° ΠΊΠΎΠ»Π±Π°Ρ ΠΎΡΡΡΠ΅ΡΡΠ²Π»ΡΠ΅ΡΡΡ ΠΊΠΎΠ½ΡΡΠΎΠ»Ρ Π·Π° ΡΠΎΠ±Π»ΡΠ΄Π΅Π½ΠΈΠ΅ΠΌ ΡΠ΅Ρ Π½ΠΎΠ»ΠΎΠ³ΠΈΡΠ΅ΡΠΊΠΈΡ ΡΠ΅ΠΆΠΈΠΌΠΎΠ². ΠΠΎΠ½ΡΡΠΎΠ»Ρ ΡΠ΅ΠΌΠΏΠ΅ΡΠ°ΡΡΡΡ Π²Π½ΡΡΡΠΈ Π±Π»ΠΎΡΠ½ΠΎΠ³ΠΎ ΠΌΡΡΠΎΡΡΡΡΡ Π² ΡΡΡΠ°Ρ ΠΈ ΠΏΠΎΠ»ΡΡΡΡΠ°Ρ ΠΎΡΡΡΠ΅ΡΡΠ²Π»ΡΠ΅ΡΡΡ ΠΏΠΎΠ»ΡΠΏΡΠΎΠ²ΠΎΠ΄Π½ΠΈΠΊΠΎΠ²ΡΠΌ ΠΈΠ·ΠΌΠ΅ΡΠΈΡΠ΅Π»Π΅ΠΌ ΡΠ΅ΠΌΠΏΠ΅ΡΠ°ΡΡΡ. Π’Π΅ΠΌΠΏΠ΅ΡΠ°ΡΡΡΡ ΡΠ°ΡΡΠ° Π² ΠΊΡΡΡΠ΅ΡΠ΅ ΠΈΠ·ΠΌΠ΅ΡΡΡΡ ΡΠ΅ΡΠΌΠΎΡΠΎΠΏΡΠΎΡΠΈΠ²Π»Π΅Π½ΠΈΠ΅ΠΌ Ρ ΡΠ΅ΡΠΌΠΎΠ²ΠΎΠΉ ΠΈΠ½Π΄ΠΈΠΊΠ°ΡΠΈΠ΅ΠΉ. Π§ΠΈΡΠ»ΠΎ ΠΎΠ±ΠΎΡΠΎΡΠΎΠ² ΡΠ°ΡΠΈ ΠΊΡΡΡΠ΅ΡΠ° ΠΈ ΠΏΡΠΎΠ΄ΠΎΠ»ΠΆΠΈΡΠ΅Π»ΡΠ½ΠΎΡΡΡ ΠΊΡΡΡΠ΅ΡΠΎΠ²Π°Π½ΠΈΡ — ΡΠ΅ΠΊΡΠ½Π΄ΠΎΠΌΠ΅ΡΠΎΠΌ ΠΏΠΎ ΠΠΠ‘Π’ 5072-79Π ΠΈΠ»ΠΈ ΡΠ°Ρ ΠΎΠΌΠ΅ΡΡΠ°ΠΌΠΈ ΡΠΈΡΡΠΎΠ²ΡΠΌΠΈ. ΠΠΎΠ½ΡΡΠΎΠ»Ρ ΡΠ΅ΠΌΠΏΠ΅ΡΠ°ΡΡΡΡ Π² ΡΡΡΡΠ΅Π²ΠΎΠΌ, ΡΠΏΡΠΈΡΠΎΠ²ΠΎΡΠ½ΠΎΠΌ ΡΠ΅Ρ Π°Ρ , Π² ΠΊΠ°ΠΌΠ΅ΡΠ°Ρ ΡΠ°Π΄ΠΊΠΈ, ΡΡΡΠΊΠΈ Π³ΠΎΡΠΎΠ²ΠΎΠΉ ΠΏΡΠΎΠ΄ΡΠΊΡΠΈΠΈ ΠΎΡΡΡΠ΅ΡΡΠ²Π»ΡΠ΅ΡΡΡ ΡΡΠ΅ΠΊΠ»ΡΠ½Π½ΡΠΌΠΈ ΠΆΠΈΠ΄ΠΊΠΎΡΡΠ½ΡΠΌΠΈ (Π½Π΅ΡΡΡΡΠ½ΡΠΌΠΈ), ΡΠΏΠΈΡΡΠΎΠ²ΡΠΌΠΈ ΡΠ΅ΡΠΌΠΎΠΌΠ΅ΡΡΠ°ΠΌΠΈ ΠΏΠΎ ΠΠΠ‘Π’ 28498-90 ΡΠΎ ΡΠΊΠ°Π»ΠΎΠΉ Π΄Π΅Π»Π΅Π½ΠΈΡ ΠΎΡ 0 Π΄ΠΎ 100Π‘. ΠΠΎΠ½ΡΡΠΎΠ»Ρ ΠΎΡΠ½ΠΎΡΠΈΡΠ΅Π»ΡΠ½ΠΎΠΉ Π²Π»Π°ΠΆΠ½ΠΎΡΡΠΈ Π²ΠΎΠ·Π΄ΡΡ Π° Π² ΠΎΡΠ°Π΄ΠΎΡΠ½ΠΎΠΉ ΠΊΠ°ΠΌΠ΅ΡΠ΅, ΡΡΡΠΈΠ»ΠΊΠ°Ρ , ΠΊΠ°ΠΌΠ΅ΡΠ°Ρ Ρ ΡΠ°Π½Π΅Π½ΠΈΡ Π³ΠΎΡΠΎΠ²ΠΎΠΉ ΠΏΡΠΎΠ΄ΡΠΊΡΠΈΠΈ Π΄ΠΎΠ»ΠΆΠ΅Π½ ΠΎΡΡΡΠ΅ΡΡΠ²Π»ΡΡΡΡΡ ΠΏΡΠΈΡ ΡΠΎΠΌΠ΅ΡΡΠ°ΠΌΠΈ, Π°ΡΠΏΠΈΡΠ°ΡΠΈΠΎΠ½Π½ΡΠΌΠΈ Π³ΠΈΠ³ΡΠΎΠΌΠ΅ΡΡΠ°ΠΌΠΈ ΠΈ Π³ΠΈΠ³ΡΠΎΠ³ΡΠ°ΡΠ°ΠΌΠΈ ΠΌΠ΅ΡΡΠΎΠ»ΠΎΠ³ΠΈΡΠ΅ΡΠΊΠΈΠΌΠΈ. Π Π°Π²ΡΠΎΠΌΠ°ΡΠΈΡΠ΅ΡΠΊΠΈΡ ΡΠ΅ΡΠΌΠΎΠΊΠ°ΠΌΠ΅ΡΠ°Ρ ΠΊΠΎΠ½ΡΡΠΎΠ»Ρ ΡΠ΅ΠΌΠΏΠ΅ΡΠ°ΡΡΡΡ ΠΈ Π²Π»Π°ΠΆΠ½ΠΎΡΡΠΈ ΠΎΡΡΡΠ΅ΡΡΠ²Π»ΡΠ΅ΡΡΡ Π°Π²ΡΠΎΠΌΠ°ΡΠΈΡΠ΅ΡΠΊΠΈΠΌΠΈ ΠΏΠΎΡΠ΅Π½ΡΠΈΠΎΠΌΠ΅ΡΡΠ°ΠΌΠΈ ΠΈΠ»ΠΈ ΡΠ»Π΅ΠΊΡΡΠΎΠ½Π½ΡΠΌΠΈ ΠΌΠΎΡΡΠ°ΠΌΠΈ, ΠΊΠΎΡΠΎΡΡΠ΅ Π΄ΠΎΠ»ΠΆΠ½Ρ ΡΠΎΠΎΡΠ²Π΅ΡΡΡΠ²ΠΎΠ²Π°ΡΡ ΡΡΠ΅Π±ΠΎΠ²Π°Π½ΠΈΡΠΌ, ΠΈΠ·Π»ΠΎΠΆΠ΅Π½Π½ΡΠΌ Π² ΠΠΠ‘Π’ 22261-82. ΠΠΠ‘Π’ 9999-79. Π‘ΠΊΠΎΡΠΎΡΡΡ Π΄Π²ΠΈΠΆΠ΅Π½ΠΈΡ Π²ΠΎΠ·Π΄ΡΡ Π° Π² ΠΎΡΠ°Π΄ΠΎΡΠ½ΡΡ , ΡΠ΅ΡΠΌΠΈΡΠ΅ΡΠΊΠΈΡ ΠΊΠ°ΠΌΠ΅ΡΠ°Ρ , ΡΡΡΠΈΠ»ΠΊΠ°Ρ ΠΈΠ·ΠΌΠ΅ΡΡΠ΅ΡΡΡ Π°Π½Π΅ΠΌΠΎΠΌΠ΅ΡΡΠ°ΠΌΠΈ. ΠΠ·Π²Π΅ΡΠΈΠ²Π°Π½ΠΈΠ΅ ΡΡΡΡΡ ΠΏΡΠΈ ΠΏΠΎΡΠΎΠ»Π΅ ΠΈ ΡΠΎΡΡΠ°Π²Π»Π΅Π½ΠΈΠ΅ ΡΠ΅ΡΠ΅ΠΏΡΡΡ ΡΠΏΠ΅ΡΠΈΠΉ ΠΏΡΠΎΠΈΠ·Π²ΠΎΠ΄ΡΡ Π½Π° Π²Π΅ΡΠ°Ρ ΠΎΠ±ΡΠ΅Π³ΠΎ Π½Π°Π·Π½Π°ΡΠ΅Π½ΠΈΡ ΠΏΠΎ ΠΠΠ‘Π’ 23676-79, ΠΠΠ‘Π’ 14004-68 ΠΈΠ»ΠΈ Π²Π΅ΡΠΎΠ²ΡΡ Π΄ΠΎΠ·Π°ΡΠΎΡΠ°Ρ ΠΏΠΎ ΠΠΠ‘Π’ 24619-81. ΠΠΎΠ½ΡΡΠΎΠ»ΡΠ½ΠΎΠ΅ Π΄ΠΎΠ·ΠΈΡΠΎΠ²Π°Π½ΠΈΠ΅ ΡΠ°ΡΡΠ²ΠΎΡΠ° Π½ΠΈΡΡΠΈΡΠ° Π½Π°ΡΡΠΈΡ ΠΏΡΠΈ ΠΏΠΎΡΠΎΠ»Π΅ ΡΡΡΡΡ ΠΈΠ»ΠΈ ΠΏΡΠΈΠ³ΠΎΡΠΎΠ²Π»Π΅Π½ΠΈΠΈ ΡΠ°ΡΡΠ° ΠΎΡΡΡΠ΅ΡΡΠ²Π»ΡΡΡ ΠΏΠΎ ΠΌΠ°ΡΡΠΎΠ²ΠΎΠΉ Π΄ΠΎΠ»Π΅ Π΅Π³ΠΎ Π² Π³ΠΎΡΠΎΠ²ΠΎΠΌ ΠΏΡΠΎΠ΄ΡΠΊΡΠ΅. Π Π΅ΠΊΠΎΠΌΠ΅Π½Π΄ΡΠ΅ΡΡΡ Π΄Π»Ρ Π΄ΠΎΠ·ΠΈΡΠΎΠ²Π°Π½ΠΈΡ ΡΠ°ΡΡΠ²ΠΎΡΠ° Π½ΠΈΡΡΠΈΡΠ° Π½Π°ΡΡΠΈΡ ΠΏΡΠΈ ΠΏΠΎΡΠΎΠ»Π΅ ΠΌΡΡΠ° ΠΈΠ»ΠΈ ΠΏΡΠΈΠ³ΠΎΡΠΎΠ²Π»Π΅Π½ΠΈΠΈ ΡΠ°ΡΡΠ° ΠΏΡΠΈΠΌΠ΅Π½ΡΡΡ ΠΌΠ΅ΡΠ½ΡΠ΅ ΠΏΠ»Π°ΡΡΠΌΠ°ΡΡΠΎΠ²ΡΠ΅ ΠΈΠ»ΠΈ ΠΎΠ±ΡΠ΅ΠΌΠ½ΡΠ΅ (Π½Π΅ΠΌΠ΅ΡΠ½ΡΠ΅) ΠΈΠ· Π½Π΅ΡΠΆΠ°Π²Π΅ΡΡΠ΅ΠΉ ΡΡΠ°Π»ΠΈ ΠΊΡΡΠΆΠΊΠΈ. ΠΠΎ ΠΎΠΊΠΎΠ½ΡΠ°Π½ΠΈΠΈ ΡΠ΅Ρ Π½ΠΎΠ»ΠΎΠ³ΠΈΡΠ΅ΡΠΊΠΎΠ³ΠΎ ΠΏΡΠΎΡΠ΅ΡΡΠ° ΠΊΠΎΠ»Π±Π°ΡΡ ΠΏΡΠΎΠ²Π΅ΡΡΡΡ ΠΎΡΠ³Π°Π½ΠΎΠ»Π΅ΠΏΡΠΈΡΠ΅ΡΠΊΠΈ, ΠΎΡΠ±ΡΠ°ΠΊΠΎΠ²ΡΠ²Π°ΡΡ Π½Π΅ ΡΠΎΠΎΡΠ²Π΅ΡΡΡΠ²ΡΡΡΠΈΠ΅ ΠΏΠΎ ΠΊΠ°ΡΠ΅ΡΡΠ²Ρ ΡΡΠ΅Π±ΠΎΠ²Π°Π½ΠΈΡΠΌ Π’Π£. ΠΠΎΠ»Π±Π°ΡΡ ΡΡΡΠΎΠΊΠΎΠΏΡΠ΅Π½ΡΠ΅ Ρ ΠΏΡΠΎΠΈΠ·Π²ΠΎΠ΄ΡΡΠ²Π΅Π½Π½ΡΠΌΠΈ Π΄Π΅ΡΠ΅ΠΊΡΠ°ΠΌΠΈ (Ρ ΡΠ΅ΡΡΠΌΠΈ ΠΏΡΡΠ½Π°ΠΌΠΈ. ΠΏΡΡΡΠΎΡΠ°ΠΌΠΈ ΠΈ Ρ.Π΄.) Π½Π°ΠΏΡΠ°Π²Π»ΡΡΡ Π½Π° Π²ΡΡΠ°Π±ΠΎΡΠΊΡ Π²Π°ΡΠ΅Π½ΠΎ-ΠΊΠΎΠΏΡΠ΅Π½ΡΡ , ΠΏΠΎΠ»ΡΠΊΠΎΠΏΡΠ΅Π½ΡΡ ΠΊΠΎΠ»Π±Π°Ρ ΠΏΠ΅ΡΠ²ΠΎΠ³ΠΎ ΡΠΎΡΡΠ° Π² ΠΊΠΎΠ»ΠΈΡΠ΅ΡΡΠ²Π΅ Π΄ΠΎ 3% ΠΊ ΠΌΠ°ΡΡΠ΅ ΡΡΡΡΡ, ΡΠ²Π΅ΡΡ ΡΠ΅ΡΠ΅ΠΏΡΡΡΡ Π² ΡΠΎΠΎΡΠ²Π΅ΡΡΡΠ²ΠΈΠΈ Ρ Π΄Π΅ΠΉΡΡΠ²ΡΡΡΠ΅ΠΉ Π½ΠΎΡΠΌΠ°ΡΠΈΠ²Π½ΠΎ-ΡΠ΅Ρ Π½ΠΈΡΠ΅ΡΠΊΠΎΠΉ Π΄ΠΎΠΊΡΠΌΠ΅Π½ΡΠ°ΡΠΈΠ΅ΠΉ. ΠΡΠ°Π²ΠΈΠ»Π° ΠΎΡΠ±ΠΎΡΠ° ΠΏΡΠΎΠ± ΠΈ ΠΏΠΎΠ΄Π³ΠΎΡΠΎΠ²ΠΊΠ° ΠΈΡ ΠΊ ΠΈΡΠΏΡΡΠ°Π½ΠΈΡ, ΠΌΠ΅ΡΠΎΠ΄Ρ ΠΈΡΠΏΡΡΠ°Π½ΠΈΠΉ, ΠΏΠ΅ΡΠΈΠΎΠ΄ΠΈΡΠ½ΠΎΡΡΡ ΠΊΠΎΠ½ΡΡΠΎΠ»Ρ ΠΊΠ°ΡΠ΅ΡΡΠ²Π° ΠΏΡΠΎΠ²ΠΎΠ΄ΡΡΡΡ Ρ ΡΡΠ΅Π±ΠΎΠ²Π°Π½ΠΈΡΠΌΠΈ Π’Π£ Π½Π° Π΄Π°Π½Π½ΡΠ΅ Π²ΠΈΠ΄Ρ ΠΏΡΠΎΠ΄ΡΠΊΡΠΎΠ².
Π’ΡΠ΅Π±ΠΎΠ²Π°Π½ΠΈΡ Π±Π΅Π·ΠΎΠΏΠ°ΡΠ½ΠΎΡΡΠΈ Π’Π΅Ρ Π½ΠΎΠ»ΠΎΠ³ΠΈΡΠ΅ΡΠΊΠΈΠΉ ΠΏΡΠΎΡΠ΅ΡΡ Π΄ΠΎΠ»ΠΆΠ΅Π½ ΡΠΎΠΎΡΠ²Π΅ΡΡΡΠ²ΠΎΠ²Π°ΡΡ ΡΡΠ΅Π±ΠΎΠ²Π°Π½ΠΈΡΠΌ Π±Π΅Π·ΠΎΠΏΠ°ΡΠ½ΠΎΡΡΠΈ ΠΠΠ‘Π’ 12.3,002-75. ΠΠ‘Π’ 149176-81 ΠΡΠΈΠΌΠ΅Π½ΡΠ΅ΠΌΠΎΠ΅ ΠΎΠ±ΠΎΡΡΠ΄ΠΎΠ²Π°Π½ΠΈΠ΅ Π΄ΠΎΠ»ΠΆΠ½ΠΎ ΠΎΡΠ²Π΅ΡΠ°ΡΡ ΡΡΠ΅Π±ΠΎΠ²Π°Π½ΠΈΡΠΌ ΠΠΠ‘Π’ 122003-74 ΠΠ‘Π’ 27-32-463-79 ΠΈ ΠΠ‘Π’ 27-00-216-75 ΠΏΠΎ ΡΠ΅Ρ Π½ΠΈΠΊΠ΅ Π±Π΅Π·ΠΎΠΏΠ°ΡΠ½ΠΎΡΡΠΈ. ΠΡΠΈ ΡΠ°Π±ΠΎΡΠ΅ Ρ Π½ΠΈΡΡΠΈΡΠΎΠΌ Π½Π°ΡΡΠΈΡ Π΄ΠΎΠ»ΠΆΠ½Π° ΡΠΎΠ±Π»ΡΠ΄Π°ΡΡΡΡ ΠΈΠ½ΡΡΡΡΠΊΡΠΈΡ ΠΏΠΎ ΠΏΡΠΈΠΌΠ΅Π½Π΅Π½ΠΈΡ ΠΈ Ρ ΡΠ°Π½Π΅Π½ΠΈΡ Π½ΠΈΡΡΠΈΡΠ° Π½Π°ΡΡΠΈΡ, ΡΡΠ²Π΅ΡΠΆΠ΄Π΅Π½Π½Π°Ρ ΠΠΈΠ½ΠΌΡΡΠΎΠΌΠΎΠ»ΠΏΡΠΎΠΌΠΎΠΌ Π‘Π‘Π‘Π . Π‘ΠΎΠ΄Π΅ΡΠΆΠ°Π½ΠΈΠ΅ Π²ΡΠ΅Π΄Π½ΡΡ Π²Π΅ΡΠ΅ΡΡΠ² Π² Π²ΠΎΠ·Π΄ΡΡ Π΅ ΡΠ°Π±ΠΎΡΠ΅ΠΉ Π·ΠΎΠ½Ρ (ΠΎΠΊΠΈΡΡ ΡΠ³Π»Π΅ΡΠΎΠ΄Π°, ΠΊΠΈΡΠ»ΠΎΡΡ, Π°Π»ΡΠ΄Π΅Π³ΠΈΠ΄Ρ) Π½Π΅ Π΄ΠΎΠ»ΠΆΠ½ΠΎ ΠΏΡΠ΅Π²ΡΡΠ°ΡΡ ΠΠΠ — ΠΏΡΠ΅Π΄ΡΡΠΌΠΎΡΡΠ΅Π½Π½ΡΡ ΠΠΠ‘Π’ 12.1 005-88.
3. ΠΡΠΎΡΠ΅ΡΡ ΠΈΠ·ΠΌΠ΅Π»ΡΡΠ΅Π½ΠΈΡ
ΠΡΠΈ ΠΏΡΠΎΠΈΠ·Π²ΠΎΠ΄ΡΡΠ²Π΅ ΠΊΠΎΠ»Π±Π°Ρ ΠΏΠ΅ΡΠ΅Π΄ ΠΏΠΎΡΠΎΠ»ΠΎΠΌ ΠΏΠΎΠ΄Π²Π΅ΡΠ³Π°ΡΡ ΠΏΡΠ΅Π΄Π²Π°ΡΠΈΡΠ΅Π»ΡΠ½ΠΎΠΌΡ ΠΈΠ·ΠΌΠ΅Π»ΡΡΠ΅Π½ΠΈΡ. ΠΠΎΡΠ»Π΅ ΠΏΠΎΡΠΎΠ»Π° Π΅Π³ΠΎ Π²Π½ΠΎΠ²Ρ ΠΈΠ·ΠΌΠ΅Π»ΡΡΠ°ΡΡ Π±ΠΎΠ»Π΅Π΅ ΡΠΎΠ½ΠΊΠΎ ΡΠΏΠ΅ΡΠΈΠ°Π»ΡΠ½ΡΠΌΠΈ Π²ΠΎΠ»ΡΠΊΠ°ΠΌΠΈ. Π‘ΡΠ΅ΠΏΠ΅Π½Ρ ΠΈΠ·ΠΌΠ΅Π»ΡΡΠ΅Π½ΠΈΡ ΠΌΡΡΠ° Π½Π° Π²ΠΎΠ»ΡΠΊΠ΅ ΠΎΠΏΡΠ΅Π΄Π΅Π»ΡΠ΅ΡΡΡ Π²Π΅Π»ΠΈΡΠΈΠ½ΠΎΠΉ ΠΎΡΠ²Π΅ΡΡΡΠΈΠΉ ΡΠ΅ΡΡΡΠΊΠΈ ΠΈ ΠΊΠΎΠ»ΠΈΡΠ΅ΡΡΠ²ΠΎΠΌ ΡΠ΅ΠΆΡΡΠΈΡ Π΄Π΅ΡΠ°Π»Π΅ΠΉ. ΠΡΠΈ ΠΏΡΠΎΠΈΠ·Π²ΠΎΠ΄ΡΡΠ²Π΅ ΠΊΠΎΠΏΡΡΠ½ΡΡ ΠΊΠΎΠ»Π±Π°Ρ ΠΏΠ΅ΡΠ΅ΡΠΈΡΠ°Π½ΠΈΠ΅ ΠΌΡΡΠ° Π½Π° Π²ΠΎΠ»ΠΊΠ΅ ΡΠ²Π»ΡΠ΅ΡΡΡ Π½Π΅ΠΆΠ΅Π»Π°ΡΠ΅Π»ΡΠ½ΡΠΌ, ΠΏΠΎΡΡΠΎΠΌΡ ΠΈΡΠΏΠΎΠ»ΡΠ·ΡΡΡ Π΄ΡΡΠ³ΠΈΠ΅ ΡΠΏΠΎΡΠΎΠ±Ρ.ΠΡΠΎΡΠΈΡΠ½ΠΎΠ΅ ΠΈΠ·ΠΌΠ΅Π»ΡΡΠ΅Π½ΠΈΠ΅ ΠΌΡΡΠΎΠΏΡΠΎΠ΄ΡΠΊΡΠΎΠ² ΡΠΆΠ΅ ΡΠΎ ΡΠΏΠ΅ΡΠΈΡΠΌΠΈ, Π΄ΠΎΠ±Π°Π²ΠΊΠ°ΠΌΠΈ ΠΈ Π΄ΡΡΠ³ΠΈΠΌΠΈ ΠΊΠΎΠΌΠΏΠΎΠ½Π΅Π½ΡΠ°ΠΌΠΈ, ΠΊΠΎΡΠΎΡΡΠ΅ ΠΏΡΠ΅Π΄ΡΡΠΌΠΎΡΡΠ΅Π½Ρ ΡΠ΅Ρ Π½ΠΎΠ»ΠΎΠ³ΠΈΠ΅ΠΉ — ΡΡΠΎ ΠΎΡΠ΅Π½Ρ Π²Π°ΠΆΠ½ΡΠΉ ΠΏΡΠΎΡΠ΅ΡΡ ΠΏΡΠΈ ΠΏΡΠΎΠΈΠ·Π²ΠΎΠ΄ΡΡΠ²Π΅ ΡΠΎΡΠΈΡΠΎΠΊ, ΡΠ°ΡΠ΄Π΅Π»Π΅ΠΊ, Π²Π°ΡΠ΅Π½ΡΡ ΠΈ Π»ΠΈΠ²Π΅ΡΠ½ΡΡ ΠΊΠΎΠ»Π±Π°Ρ, Π° ΡΠ°ΠΊΠΆΠ΅ ΠΌΡΡΠ½ΡΡ Ρ Π»Π΅Π±ΠΎΠ² ΠΈ ΠΏΠ°ΡΡΠ΅ΡΠΎΠ². ΠΡΠΈ ΠΏΡΠΎΠΈΠ·Π²ΠΎΠ΄ΡΡΠ²Π΅ ΡΡΠΈΡ ΠΊΠΎΠ»Π±Π°ΡΠ½ΡΡ ΠΈΠ·Π΄Π΅Π»ΠΈΠΉ ΡΡΠ΅Π±ΡΠ΅ΡΡΡ ΠΎΡΠ΅Π½Ρ Π²ΡΡΠΎΠΊΠ°Ρ ΡΡΠ΅ΠΏΠ΅Π½Ρ ΠΈΠ·ΠΌΠ΅Π»ΡΡΠ΅Π½ΠΈΡ, ΠΊΠΎΡΠΎΡΠ°Ρ ΠΎΠ±Π΅ΡΠΏΠ΅ΡΠΈΠ²Π°Π΅Ρ ΠΎΠ΄Π½ΠΎΡΠΎΠ΄Π½ΠΎΡΡΡ ΡΡΡΡΠΊΡΡΡΡ, ΡΠ°Π²Π½ΠΎΠΌΠ΅ΡΠ½ΠΎΠ΅ ΠΏΠ΅ΡΠ΅ΠΌΠ΅ΡΠΈΠ²Π°Π½ΠΈΠ΅, Π²ΡΡΠΎΠΊΡΡ Π»ΠΈΠΏΠΊΠΎΡΡΡ, Π²ΡΠ·ΠΊΠΎΡΡΡ ΠΈ Π²Π»Π°Π³ΠΎΡΠ΄Π΅ΡΠΆΠΈΠ²Π°ΡΡΡΡ ΡΠΏΠΎΡΠΎΠ±Π½ΠΎΡΡΡ ΡΠ°ΡΡΠ°. ΠΠ»Ρ ΡΡΠΎΠ³ΠΎ ΠΏΡΠΈΠΌΠ΅Π½ΡΡΡ ΠΊΡΡΡΠ΅ΡΡ ΠΈ ΠΌΠ°ΡΠΈΠ½Ρ Π½Π΅ΠΏΡΠΈΡΡΠ²Π½ΠΎΠ³ΠΎ Π΄Π΅ΠΉΡΡΠΊΠΈΡ Π΄Π»Ρ ΡΠΎΠ½ΠΊΠΎΠ³ΠΎ ΠΈΠ·ΠΌΠ΅Π»ΡΡΠ΅Π½ΠΈΡ ΠΌΡΡΠ°, ΠΏΡΠΎΠ΄ΠΎΠ»ΠΆΠΈΡΠ΅Π»ΡΠ½ΠΎΡΡΡ ΠΊΡΡΡΠ΅ΡΠΎΠ²Π°Π½ΠΈΡ Π·Π°Π²ΠΈΡΠΈΡ ΠΎΡ ΡΡΠ΅ΠΏΠ΅Π½ΠΈ ΠΈΠ·ΠΌΠ΅Π»ΡΡΠ΅Π½ΠΈΡ ΠΌΡΡΠ΅ΡΠ½ΡΡ Π²ΠΎΠ»ΠΎΠΊΠΎΠ½.4
ΠΡΠ»ΠΈ Π² ΠΏΡΠΎΡΠ΅ΡΡΠ΅ ΠΊΡΡΡΠ΅ΡΠΎΠ²Π°Π½ΠΈΡ ΠΏΠΎΠ²ΡΡΠ°Π΅ΡΡΡ ΡΠ΅ΠΌΠΏΠ΅ΡΠ°ΡΡΡΠ°, Π±Π΅Π»ΠΊΠΎΠ²Π°Ρ ΡΠ²ΡΠ·ΡΠ²Π°ΡΡΠ°Ρ ΠΎΡΠ½ΠΎΠ²Π° ΠΌΠΎΠΆΠ΅Ρ Π±ΡΡΡ Π΄Π΅Π½Π°ΡΡΡΠΈΡΠΎΠ²Π°Π½Π° ΠΈ ΡΠ°Π·ΡΡΡΠ΅Π½Π°, Π° ΡΠ²Π΅Π»ΠΈΡΠ΅Π½ΠΈΠ΅ Π½Π΅Π·Π°ΡΠΈΡΡΠ½Π½ΠΎΠΉ ΠΆΠΈΡΠΎΠ²ΠΎΠΉ Π΄ΠΈΡΠΏΠ΅ΡΡΠΈΠΈ ΡΠΏΠΎΡΠΎΠ±ΡΡΠ²ΡΠ΅Ρ ΠΎΡΠ΄Π΅Π»Π΅Π½ΠΈΡ ΠΆΠΈΡΠ° Π² ΠΏΡΠΎΡΠ΅ΡΡΠ΅ ΠΊΠΎΠΏΡΠ΅Π½ΠΈΡ ΠΈ Π²Π°ΡΠΊΠΈ. ΠΠΎΡΡΠΎΠΌΡ ΠΎΡΠ΅Π½Ρ Π²Π°ΠΆΠ½ΠΎ Π·Π΄Π΅ΡΡ Π½Π΅ Π΄ΠΎΠΏΡΡΡΠΈΡΡ ΠΏΠ΅ΡΠ΅Π³ΡΠ΅Π²Π°Π½ΠΈΡ. ΡΡΠΎΠ±Ρ ΠΈΡΠΊΠ»ΡΡΠΈΡΡ Π΄ΠΎΠ±Π°Π²Π»Π΅Π½ΠΈΠ΅ Π»ΡΠ΄Π°.
Π ΡΡΠΎΠΌ ΠΎΡΠ½ΠΎΡΠ΅Π½ΠΈΠΈ ΠΏΡΠ΅Π΄ΡΡΠ°Π²Π»ΡΠ΅Ρ ΠΎΡΠΎΠ±ΡΠΉ ΠΈΠ½ΡΠ΅ΡΠ΅Ρ ΠΊΡΡΡΠ΅Ρ «Π Π°Π·Π°Π½Ρ» ΡΠΈΡΠΌΡ «ΠΠ΅ΠΉΠ΄Π΅Π»ΡΠΌΠ°Π½», Π½ΠΎΠΆΠ΅Π²ΠΎΠΉ Π²Π°Π» ΠΊΠΎΡΠΎΡΠΎΠΉ Π²ΡΠ°ΡΠ°Π΅ΡΡΡ ΡΠΎ ΡΠΊΠΎΡΠΎΡΡΡΡ Π΄ΠΎ 4000 ΠΎΠ±/ΠΌΠΈΠ½. ΠΠ½ΠΎΠ³ΠΈΠ΅ ΠΌΠΎΠ΄Π΅Π»ΠΈ ΠΊΡΡΡΠ΅ΡΠΎΠ² ΠΈΠ·ΠΌΠ΅Π»ΡΡΠ°ΡΡ ΠΌΠΎΡΠΎΠΆΠ΅Π½ΠΎΠ΅ ΠΌΡΡΠΎ, Π² Ρ. Ρ. Π·Π°ΠΌΠΎΡΠΎΠΆΠ΅Π½Π½ΠΎΠ΅ Π±Π»ΠΎΠΊΠ°ΠΌΠΈ, Π±Π΅Π· ΠΏΡΠ΅Π΄Π²Π°ΡΠΈΡΠ΅Π»ΡΠ½ΠΎΠ³ΠΎ ΠΈΠ·ΠΌΠ΅Π»ΡΡΠ΅Π½ΠΈΡ Π½Π° Π²ΠΎΠ»ΡΠΊΠ΅. ΠΡΠΈ ΠΏΡΠΎΠΈΠ·Π²ΠΎΠ΄ΡΡΠ²Π΅ ΡΡΡΠΎΠΊΠΎΠΏΡΡΠ½ΡΡ ΠΊΠΎΠ»Π±Π°Ρ Π½Π° ΠΌΠ½ΠΎΠ³ΠΈΡ ΠΌΡΡΠΎΠΊΠΎΠΌΠ±ΠΈΠ½Π°ΡΠ°Ρ ΠΏΠ΅ΡΠ΅ΡΠ»ΠΈ Π½Π° ΠΈΠ·ΠΌΠ΅Π»ΡΡΠ΅Π½ΠΈΠ΅ ΠΌΠΎΡΠΎΠΆΠ΅Π½ΠΎΠ³ΠΎ ΠΌΡΡΠ° Π² ΠΏΠΎΠ΄ΠΎΠ±Π½ΡΡ ΠΊΡΡΡΠ΅ΡΠ°Ρ , ΠΌΠΈΠ½ΡΡ Π²ΠΎΠ»ΡΠΎΠΊ, ΡΠΎΠΊΡΠ°ΡΠ°Ρ Π²ΡΠ΅ΠΌΡ ΠΎΠΏΠ΅ΡΠ°ΡΠΈΠΈ ΠΈΠ·ΠΌΠ΅Π»ΡΡΠ΅Π½ΠΈΡ ΠΌΡΡΠ° Π² ΡΠ΅Ρ Π½ΠΎΠ»ΠΎΠ³ΠΈΡΠ΅ΡΠΊΠΎΠΌ ΠΏΡΠΎΡΠ΅ΡΡΠ΅.
Π‘ΠΎΠ²ΡΠ΅ΠΌΠ΅Π½Π½ΡΠ΅ ΠΊΡΡΡΠ΅ΡΡ Π²ΡΡΠΎΠΊΠΎΠΌΠ΅Ρ Π°Π½ΠΈΠ·ΠΈΡΠΎΠ²Π°Π½Π½ΡΠ΅, ΠΎΡΠ½Π°ΡΠ΅Π½Ρ ΡΡΡΡΠΎΠΉΡΡΠ²Π°ΠΌΠΈ ΠΈ ΠΏΡΠΈΠ±ΠΎΡΠ°ΠΌΠΈ Π΄Π»Ρ ΠΌΠ΅Ρ Π°Π½ΠΈΡΠ΅ΡΠΊΠΎΠΉ Π·Π°Π³ΡΡΠ·ΠΊΠΈ ΠΈ Π²ΡΠ³ΡΡΠ·ΠΊΠΈ ΠΌΡΡΠ°, Π΄ΠΎΠ·ΠΈΡΠΎΠ²Π°Π½ΠΈΡ Π²ΠΎΠ΄Ρ ΠΈ ΡΠ°ΡΡΠΎΠ»Π°, Π΄Π»Ρ ΠΊΠΎΠ½ΡΡΠΎΠ»Ρ Π·Π° ΠΏΡΠΎΠ΄ΠΎΠ»ΠΆΠΈΡΠ΅Π»ΡΠ½ΠΎΡΡΡΡ ΠΈ ΠΊΠ°ΡΠ΅ΡΡΠ²ΠΎΠΌ ΠΈΠ·ΠΌΠ΅Π»ΡΡΠ΅Π½ΠΈΡ, ΡΠΈΡΠ»ΠΎΠΌ ΠΎΠ±ΠΎΡΠΎΡΠΎΠ² Π½ΠΎΠΆΠ΅Π²ΠΎΠ³ΠΎ Π²Π°Π»Π°, ΡΠ°ΡΠΈ ΠΈ Π΄Ρ.
Π‘Π΅Π³ΠΎΠ΄Π½Ρ Π½Π°ΡΠ»ΠΈ ΡΠΈΡΠΎΠΊΠΎΠ΅ ΠΏΡΠΈΠΌΠ΅Π½Π΅Π½ΠΈΠ΅ ΠΌΠ°ΡΠΈΠ½Ρ Π½Π΅ΠΏΡΠΈΡΡΠ²Π½ΠΎΠ³ΠΎ Π΄Π΅ΠΉΡΡΠ²ΠΈΡ Π΄Π»Ρ ΡΠΎΠ½ΠΊΠΎΠ³ΠΎ ΠΈΠ·ΠΌΠ΅Π»ΡΡΠ΅Π½ΠΈΡ ΠΌΡΡΠ°: ΡΠΌΡΠ»ΡΡΠΈΡΠ°ΡΠΎΡΡ, ΠΌΠΈΠΊΡΠΎΠΊΡΡΡΠ΅ΡΡ, ΠΊΠΎΠ»Π»ΠΎΠΈΠ΄Π½ΡΠ΅ ΠΌΠ΅Π»ΡΠ½ΠΈΡΡ ΠΈ Π΄ΡΡΠ³ΠΎΠ΅ ΠΎΠ±ΠΎΡΡΠ΄ΠΎΠ²Π°Π½ΠΈΠ΅.
ΠΠΎ ΠΊΡΡΡΠ΅ΡΡ ΡΠ²Π»ΡΡΡΡΡ ΠΎΠ΄Π½ΠΎΠ²ΡΠ΅ΠΌΠ΅Π½Π½ΠΎ ΠΈΠ·ΠΌΠ΅Π»ΡΡΠ°ΡΡΠΈΠΌΠΈ ΠΈ ΠΏΠ΅ΡΠ΅ΠΌΠ΅ΡΠΈΠ²Π°ΡΡΠΈΠΌΠΈ ΠΌΠ°ΡΠΈΠ½Π°ΠΌΠΈ, Π½Π° Π½ΠΈΡ ΠΌΠΎΠΆΠ΅Ρ Π·Π°ΠΊΠ°Π½ΡΠΈΠ²Π°ΡΡΡΡ ΠΏΡΠΎΡΠ΅ΡΡ ΠΏΡΠΈΠ³ΠΎΡΠΎΠ²Π»Π΅Π½ΠΈΡ ΡΠ°ΡΡΠ° Π΄Π»Ρ Π±ΠΎΠ»ΡΡΠΈΠ½ΡΡΠ²Π° Π²Π°ΡΡΠ½ΡΡ , ΠΊΠΎΠΏΡΡΠ½ΡΡ , ΠΏΠΎΠ»ΡΠΊΠΎΠΏΡΡΠ½ΡΡ ΠΈ Π»ΠΈΠ²Π΅ΡΠ½ΡΡ ΠΈΠ·Π΄Π΅Π»ΠΈΠΉ. Π ΠΊΠ°ΠΆΠ΄ΡΡ ΠΌΠ°ΡΠΈΠ½Π°Ρ Π΅ΡΡΡ ΡΠ²ΠΎΠΈ ΠΏΡΠ΅ΠΈΠΌΡΡΠ΅ΡΡΠ²Π° ΠΈ Π½Π΅Π΄ΠΎΡΡΠ°ΡΠΊΠΈ.
4. ΠΠΏΠΏΠ°ΡΠ°Ρ — Π²ΠΎΠ»ΡΠΎΠΊ
4.1 ΠΠ±Π·ΠΎΡ ΡΡΡΠ΅ΡΡΠ²ΡΡΡΠΈΡ Π°ΠΏΠΏΠ°ΡΠ°ΡΠΎΠ²
Π Π΅ΠΆΡΡΠΈΠΉ ΠΌΠ΅Ρ Π°Π½ΠΈΠ·ΠΌ Π²ΠΎΠ»ΡΠΊΠ° ΡΠΎΡΡΠΎΠΈΡ ΠΈΠ· ΡΠ΅ΡΠ΅Π΄ΡΡΡΠΈΡ ΡΡ ΡΠ΅ΡΠ΅ΡΠΎΠΊ ΠΈ Π½ΠΎΠΆΠ΅ΠΉ. ΠΠ΅ΠΏΠΎΠ΄Π²ΠΈΠΆΠ½Π°Ρ ΡΠ΅ΡΠ΅ΡΠΊΠ° ΠΈ Π²ΡΠ°ΡΠ°ΡΡΠΈΠΉΡΡ ΠΊΡΠ΅ΡΡΠΎΠΎΠ±ΡΠ°Π·Π½ΡΠΉ Π½ΠΎΠΆ (ΠΎΠ΄Π½ΠΎΡΡΠΎΡΠΎΠ½Π½ΠΈΠΉ ΠΈΠ»ΠΈ Π΄Π²ΡΡΡΠΎΡΠΎΠ½Π½ΠΈΠΉ) ΠΎΠ±ΡΠ°Π·ΡΡΡ ΠΏΠ»ΠΎΡΠΊΠΎΡΡΡ ΡΠ΅Π·Π°Π½ΠΈΡ. Π§ΠΈΡΠ»ΠΎ ΡΠ°ΠΊΠΈΡ ΡΠ΅ΠΆΡΡΠΈΡ ΠΏΠ»ΠΎΡΠΊΠΎΡΡΠ΅ΠΉ ΠΌΠΎΠΆΠ΅Ρ Π±ΡΡΡ ΡΠ°Π·Π»ΠΈΡΠ½ΠΎΠ΅ (1…4 ΡΡ) Π² Π·Π°Π²ΠΈΡΠΈΠΌΠΎΡΡΠΈ ΠΎΡ ΡΡΠ΅ΠΏΠ΅Π½ΠΈ ΠΈΠ·ΠΌΠ΅Π»ΡΡΠ΅Π½ΠΈΡ: ΡΠ΅ΠΌ Π±ΠΎΠ»ΡΡΠ΅ ΡΡΠ΅ΠΏΠ΅Π½Ρ ΠΈΠ·ΠΌΠ΅Π»ΡΡΠ΅Π½ΠΈΡ, ΡΠ΅ΠΌ Π±ΠΎΠ»ΡΡΠ΅ Π΄ΠΎΠ»ΠΆΠ½ΠΎ Π±ΡΡΡ ΡΠΈΡΠ»ΠΎ ΠΏΠ»ΠΎΡΠΊΠΎΡΡΠ΅ΠΉ ΡΠ΅Π·Π°Π½ΠΈΡ. ΠΡΠΈ Π½Π΅Π±ΠΎΠ»ΡΡΠΎΠΉ ΡΡΠ΅ΠΏΠ΅Π½ΠΈ ΠΈΠ·ΠΌΠ΅Π»ΡΡΠ΅Π½ΠΈΡ (Π΄ΠΈΠ°ΠΌΠ΅ΡΡ ΠΎΡΠ²Π΅ΡΡΡΠΈΠΉ 16…25 ΠΌΠΌ) Π΄ΠΎΡΡΠ°ΡΠΎΡΠ½ΠΎ ΠΎΠ΄Π½ΠΎΠΉ ΠΏΠ»ΠΎΡΠΊΠΎΡΡΠΈ ΡΠ΅Π·Π°Π½ΠΈΡ, ΠΏΡΠΈ Π±ΠΎΠ»ΡΡΠΎΠΉ (Π΄ΠΈΠ°ΠΌΠ΅ΡΡ ΠΎΡΠ²Π΅ΡΡΡΠΈΠΈ 2…3 ΠΌΠΌ) — ΡΠΈΡΠ»ΠΎ ΠΏΠ»ΠΎΡΠΊΠΎΡΡΠ΅ΠΉ ΡΠ΅Π·Π°Π½ΠΈΡ ΡΠ»Π΅Π΄ΡΠ΅Ρ Π΄ΠΎΠ²ΠΎΠ΄ΠΈΡΡ Π΄ΠΎ ΡΠ΅ΡΡΡΠ΅Ρ .B Π²ΠΎΠ»ΡΠΊΠ΅ ΠΌΡΡΠΎ ΠΏΠΎΠ΄Π²Π΅ΡΠ³Π°Π΅ΡΡΡ ΡΠ΅Π·Π°Π½ΠΈΡ, ΡΠΌΡΡΠΈΡ ΠΈ ΡΠ°Π·ΡΡΠ²Ρ, ΠΏΡΠΈΡΠ΅ΠΌ ΡΠ΅ΠΌ ΠΌΠ΅Π½ΡΡΠ΅ Π΄ΠΈΠ°ΠΌΠ΅ΡΡ ΠΎΡΠ²Π΅ΡΡΡΠΈΠΉ ΡΠ΅ΡΠ΅ΡΠΊΠΈ Π²ΠΎΠ»ΡΠΊΠ°, ΡΠ΅ΠΌ ΡΠΈΠ»ΡΠ½Π΅Π΅ ΡΠ°Π·ΡΡΡΠ°Π΅ΡΡΡ ΠΈ ΠΏΠ΅ΡΠ΅ΡΠΈΡΠ°Π΅ΡΡΡ ΡΠΊΠ°Π½Ρ, ΡΠ΅ΠΌ Π±ΠΎΠ»ΡΡΠ΅ Π½Π°Π³ΡΠ΅Π²Π°Π΅ΡΡΡ ΠΌΡΡΠΎ Π² ΡΠ΅Π·ΡΠ»ΡΡΠ°ΡΠ΅ ΡΡΠ΅Π½ΠΈΡ (Π½Π° 8…9Β°Π‘). ΠΠ° ΡΡΠ΅ΠΏΠ΅Π½Ρ Π½Π°Π³ΡΠ΅Π²Π° Π²Π»ΠΈΡΠ΅Ρ ΡΠ°ΠΊΠΆΠ΅ ΠΏΡΠ°Π²ΠΈΠ»ΡΠ½ΠΎΡΡΡ ΡΠ±ΠΎΡΠΊΠΈ ΡΠ΅ΠΆΡΡΠ΅Π³ΠΎ ΠΌΠ΅Ρ Π°Π½ΠΈΠ·ΠΌΠ°.
ΠΠ°ΠΈΠ±ΠΎΠ»Π΅Π΅ ΡΠ°ΡΠΏΡΠΎΡΡΡΠ°Π½Π΅Π½Ρ Π²ΠΎΠ»ΡΠΊΠΈ Ρ ΡΠ΅ΡΠ΅ΡΠΊΠΎΠΉ 220 ΠΌΠΌ ΠΈ ΠΎΠ΄Π½ΠΎΡΠ½Π΅ΠΊΠΎΠ²ΠΎΠΉ ΠΏΠΎΠ΄Π°ΡΠ΅ΠΉ ΡΡΡΡΡ. Π Π½Π°ΡΡΠΎΡΡΠ΅Π΅ Π²ΡΠ΅ΠΌΡ ΠΈΠΌΠ΅ΡΡΡΡ Π²ΠΎΠ»ΡΠΊΠΈ Ρ Π΄Π²ΡΠΌΡ ΠΏΠΎΠ΄Π°ΡΡΠΈΠΌΠΈ ΡΠ½Π΅ΠΊΠ°ΠΌΠΈ, ΠΏΡΠΈΡΠ΅ΠΌ ΡΠ°Π·ΠΌΠ΅Ρ Π³ΠΎΡΠ»ΠΎΠ²ΠΈΠ½Ρ Π²ΠΎΠ»ΡΠΊΠ° ΡΠ²Π΅Π»ΠΈΡΠ΅Π½ (Π³ΠΎΡΠ»ΠΎΠ²ΠΈΠ½Π° Π²ΠΎΠ»ΡΠΊΠ° Π²ΠΌΠ΅ΡΠ°Π΅Ρ Π΄ΠΎ 100 ΠΊΠ³ ΠΌΡΡΠ°), ΡΡΠΎ Π΄Π°Π΅Ρ Π²ΠΎΠ·ΠΌΠΎΠΆΠ½ΠΎΡΡΡ ΠΈΠ·ΠΌΠ΅Π»ΡΡΠ°ΡΡ Π½Π° Π½Π΅ΠΌ ΠΌΠΎΡΠΎΠΆΠ΅Π½ΠΎΠ΅ ΠΌΡΡΠΎ Π² Π±Π»ΠΎΠΊΠ°Ρ ; Π΄ΠΈΠ°ΠΌΠ΅ΡΡ ΡΠ΅ΡΠ΅ΡΠΊΠΈ 160 ΠΌΠΌ.
Π’Π΅Ρ
Π½ΠΈΡΠ΅ΡΠΊΠΈΠ΅ Ρ
Π°ΡΠ°ΠΊΡΠ΅ΡΠΈΡΡΠΈΠΊΠΈ Π²ΠΎΠ»ΡΠΊΠΎΠ² ΡΠ°Π±Π».1
Π’Π΅Ρ
Π½ΠΈΡΠ΅ΡΠΊΠ°Ρ Ρ
Π°ΡΠ°ΠΊΡΠ΅ΡΠΈΡΡΠΈΠΊΠ° | Π€Π-2-Π-200 | ΠΠ-82 | ΠΠΠ£-200 | ΠΠ-200 |
ΠΠΈΠ°ΠΌΠ΅ΡΡ ΡΠ΅ΡΠ΅ΡΠΎΠΊ, ΠΌΠΌ ΠΠΈΠ°ΠΌΠ΅ΡΡ ΡΠ°Π±ΠΎΡΠ΅Π³ΠΎ ΡΠ½Π΅ΠΊΠ°, ΠΌΠΌ Π§ΠΈΡΠ»ΠΎ ΠΎΠ±ΠΎΡΠΎΡΠΎΠ² ΡΠ°Π±ΠΎΡΠ΅Π³ΠΎ ΡΠ½Π΅ΠΊΠ°, ΠΎΠ±/ΠΌΠΈΠ½ ΠΡΡΠΎΡΠ° Π΄ΠΎ ΠΏΡΠΈΠ΅ΠΌΠ½ΠΎΠΉ ΡΠ°ΡΠΈ, ΠΌΠΌ ΠΠ»Π΅ΠΊΡΡΠΎΠ΄Π²ΠΈΠ³Π°ΡΠ΅Π»Ρ: Π’ΠΈΠΏ ΠΌΠΎΡΠ½ΠΎΡΡΡ, ΠΊΠΡ/ΡΠ°Ρ ΡΠΈΡΠ»ΠΎ ΠΎΠ±ΠΎΡΠΎΡΠΎΠ² Π² ΠΌΠΈΠ½ ΠΠ°Π±Π°ΡΠΈΡΠ½ΡΠ΅ ΡΠ°Π·ΠΌΠ΅ΡΡ, ΠΌΠΌ ΠΠ»ΠΈΠ½Π° Π¨ΠΈΡΠΈΠ½Π° ΠΡΡΠΎΡΠ° ΠΠ΅Ρ, ΠΊΠ³ | 200 160 280 920 Π71-4 20 1450 1450 1850 1700 1300 | 82 70 245 660 ΠΠΠ41-4 2,8 1420 710 400 660 200 | 200 170 304 1250 ΠΠ72-4 20 1460 1800 840 1250 1300 | 200 160 276 1140 ΠΠ63-4 14 1460 1370 670 1140 900 |
4.2 Π’Π΅Ρ Π½ΠΎΠ»ΠΎΠ³ΠΈΡΠ΅ΡΠΊΠΈΠΉ ΡΠ°ΡΡΠ΅Ρ Π°ΠΏΠΏΠ°ΡΠ°ΡΠ°
1. ΠΠΏΡΠ΅Π΄Π΅Π»Π΅Π½ΠΈΠ΅ ΠΏΡΠΎΠΈΠ·Π²ΠΎΠ΄ΠΈΡΠ΅Π»ΡΠ½ΠΎΡΡΠΈ Π²ΠΎΠ»ΡΠΊΠ°:ΠΠΎ ΠΏΡΠΎΠΏΡΡΠΊΠ½ΠΎΠΉ ΡΠΏΠΎΡΠΎΠ±Π½ΠΎΡΡΠΈ ΡΠ½Π΅ΠΊΠ°
coolreferat.com
ΠΠ°ΠΊ ΠΎΡΠΊΡΡΡΡ ΡΠ²ΠΎΠΉ ΡΠ΅Ρ ΠΏΠΎ ΠΏΡΠΎΠΈΠ·Π²ΠΎΠ΄ΡΡΠ²Ρ ΠΌΡΡΠ½ΡΡ ΠΏΠΎΠ»ΡΡΠ°Π±ΡΠΈΠΊΠ°ΡΠΎΠ²
06 ΠΠΏΡ 2013 | ΠΠ²ΡΠΎΡ: ΠΠ²Π°Π½ Π§Π΅ΡΠ΅Π΄ΠΎΠ² |ΠΠΊΡΠΏΠ΅ΡΡΡ ΡΠ²ΠΈΠ΄Π΅ΡΠ΅Π»ΡΡΡΠ²ΡΡΡ, ΡΡΠΎ ΠΎΡΠ½ΠΎΠ²Π½Π°Ρ Π΄ΠΎΠ»Ρ ΠΏΠΎΡΡΠ΅Π±Π»Π΅Π½ΠΈΡ ΠΏΡΠΎΠ΄ΡΠΊΡΠΎΠ² ΠΈΠ· ΠΎΡ Π»Π°ΠΆΠ΄Π΅Π½Π½ΠΎΠ³ΠΎ ΠΌΡΡΠ° ΠΏΡΠΈΡ ΠΎΠ΄ΠΈΡΡΡ Π½Π° ΠΏΠΎΠ»ΡΡΠ°Π±ΡΠΈΠΊΠ°ΡΡ Π²ΡΡΠΎΠΊΠΎΠΉ ΡΡΠ΅ΠΏΠ΅Π½ΠΈ Π³ΠΎΡΠΎΠ²Π½ΠΎΡΡΠΈ. ΠΠ»Ρ ΠΏΡΠΎΠΈΠ·Π²ΠΎΠ΄ΠΈΡΠ΅Π»Π΅ΠΉ ΡΡΠΎΡ ΡΠ°ΠΊΡ ΠΎΠ·Π½Π°ΡΠ°Π΅Ρ Π½Π΅ΠΎΠ±Ρ ΠΎΠ΄ΠΈΠΌΠΎΡΡΡ Π·Π½Π°ΡΠΈΡΠ΅Π»ΡΠ½ΠΎΠ³ΠΎ ΡΠ²Π΅Π»ΠΈΡΠ΅Π½ΠΈΡ Π°ΡΡΠΎΡΡΠΈΠΌΠ΅Π½ΡΠ½ΠΎΠΉ ΠΌΠ°ΡΡΠΈΡΡ. ΠΡΠΎ ΡΡΠ΅Π±ΡΠ΅Ρ Π΄ΠΎΠΏΠΎΠ»Π½ΠΈΡΠ΅Π»ΡΠ½ΡΡ ΠΈΠ½Π²Π΅ΡΡΠΈΡΠΈΠΉ Π² ΠΎΠ±ΠΎΡΡΠ΄ΠΎΠ²Π°Π½ΠΈΠ΅. ΠΠ°ΠΊ ΠΌΠΈΠ½ΠΈΠΌΠΈΠ·ΠΈΡΠΎΠ²Π°ΡΡ Π·Π°ΡΡΠ°ΡΡ, Π΄ΠΎΠ±ΠΈΡΡΡΡ ΡΠΈΡΠΎΠΊΠΎΠ³ΠΎ Π°ΡΡΠΎΡΡΠΈΠΌΠ΅Π½ΡΠ° ΠΈΠ·Π΄Π΅Π»ΠΈΠΉ, ΠΏΠΎΠ»ΡΡΠΈΡΡ Π΄ΠΎΠΏΠΎΠ»Π½ΠΈΡΠ΅Π»ΡΠ½ΡΡ ΠΏΡΠΈΠ±ΡΠ»Ρ?
Π ΡΡΠΎΠΌ ΠΎΠ±Π·ΠΎΡΠ΅ ΡΠ°ΡΡΠΌΠΎΡΡΠ΅Π½Ρ ΠΎΡΠ³Π°Π½ΠΈΠ·Π°ΡΠΈΠΎΠ½Π½ΡΠ΅ ΠΎΡΠΎΠ±Π΅Π½Π½ΠΎΡΡΠΈ ΠΎΡΠ½Π°ΡΠ΅Π½ΠΈΡ Π½Π΅Π±ΠΎΠ»ΡΡΠΈΡ ΠΏΡΠ΅Π΄ΠΏΡΠΈΡΡΠΈΠΉ, ΡΠ²ΡΠ·Π°Π½Π½ΡΠ΅ Ρ Π²ΡΠ±ΠΎΡΠΎΠΌ ΠΎΠ±ΠΎΡΡΠ΄ΠΎΠ²Π°Π½ΠΈΡ Π΄Π»Ρ ΠΎΡΠ³Π°Π½ΠΈΠ·Π°ΡΠΈΠΈ, Π½ΠΎ ΡΠ°ΡΠ΅ ΠΌΠΎΠ΄Π΅ΡΠ½ΠΈΠ·Π°ΡΠΈΠΈ ΠΏΡΠΎΠΈΠ·Π²ΠΎΠ΄ΡΡΠ²Π°, ΡΠ°Π·ΡΠ°Π±ΠΎΡΠΊΠΎΠΉ ΠΈ ΠΎΡΠ²ΠΎΠ΅Π½ΠΈΠ΅ΠΌ ΡΠ΅Ρ Π½ΠΎΠ»ΠΎΠ³ΠΈΠΈ ΠΈ ΡΠ΅ΡΠ΅ΠΏΡΡΡΡ. ΠΠ½ Π±ΡΠ΄Π΅Ρ ΠΏΠΎΠ»Π΅Π·Π΅Π½ Π»ΠΈΡΠ°ΠΌ, ΠΏΡΠΈΠ½ΠΈΠΌΠ°ΡΡΠΈΠΌ ΡΠ΅ΡΠ΅Π½ΠΈΡ, Π½Π°ΡΠΈΠ½Π°ΡΡΠΈΠΌ ΠΏΡΠ΅Π΄ΠΏΡΠΈΠ½ΠΈΠΌΠ°ΡΠ΅Π»ΡΠΌ, ΡΠ΅ΠΌ ΡΡΠΊΠΎΠ²ΠΎΠ΄ΠΈΡΠ΅Π»ΡΠΌ, ΡΡΠΈ ΠΏΡΠΎΠΈΠ·Π²ΠΎΠ΄ΡΡΠ²Π° Π½ΡΠΆΠ΄Π°ΡΡΡΡ Π² ΠΌΠΎΠ΄Π΅ΡΠ½ΠΈΠ·Π°ΡΠΈΠΈ.
Π’Π΅Ρ Π½ΠΎΠ»ΠΎΠ³ΠΈΠΈ ΠΈ ΡΠ΅ΡΠ΅ΠΏΡΡΡΡ
ΠΡΠΈ Π²ΡΠ±ΠΎΡΠ΅ ΡΠΈΠΏΠ° ΠΏΠ΅ΡΠ΅ΡΠ°Π±ΠΎΡΠΊΠΈ ΠΌΡΡΠ½ΠΎΠ³ΠΎ ΡΡΡΡΡ ΠΏΡΠΎΠΈΠ·Π²ΠΎΠ΄ΠΈΡΠ΅Π»Ρ Π² ΠΏΠ΅ΡΠ²ΡΡ ΠΎΡΠ΅ΡΠ΅Π΄Ρ ΠΈΠ·ΡΡΠ°Π΅Ρ ΡΠΏΡΠΎΡ Π½Π° ΠΌΡΡΠ½ΡΠ΅ ΠΈΠ·Π΄Π΅Π»ΠΈΡ Π² ΡΠ²ΠΎΠ΅ΠΌ ΡΠ΅Π³ΠΈΠΎΠ½Π΅. ΠΡΠ½ΠΎΠ²Π½ΠΎΠΉ ΡΠ΅Π½Π΄Π΅Π½ΡΠΈΠ΅ΠΉ ΡΡΠ½ΠΊΠ° ΠΌΡΡΠ½ΠΎΠΉ ΠΏΡΠΎΠ΄ΡΠΊΡΠΈΠΈ ΡΠ²Π»ΡΠ΅ΡΡΡ ΠΏΠΎΠ²ΡΡΠ΅Π½Π½ΡΠΉ ΡΠΏΡΠΎΡ Π½Π° ΠΎΡ Π»Π°ΠΆΠ΄Π΅Π½Π½ΠΎΠ΅ (ΡΠ²Π΅ΠΆΠ΅Π΅) ΠΌΡΡΠΎ, ΠΌΡΡΠ½ΡΠ΅ Π΄Π΅Π»ΠΈΠΊΠ°ΡΠ΅ΡΡ ΠΈ ΠΊΠΎΠ»Π±Π°ΡΠ½ΡΠ΅ ΠΈΠ·Π΄Π΅Π»ΠΈΡ (Ρ ΠΊΠΎΠΌΠΌΠ΅ΡΡΠ΅ΡΠΊΠΈΠΌΠΈ ΠΏΡΠ΅Π΄Π»ΠΎΠΆΠ΅Π½ΠΈΡΠΌΠΈ ΠΏΠΎ ΠΎΠ±ΠΎΡΡΠ΄ΠΎΠ²Π°Π½ΠΈΡ ΠΌΠΎΠΆΠ½ΠΎ ΠΎΠ·Π½Π°ΠΊΠΎΠΌΠΈΡΡΡΡ Π½Π° ΡΠ°ΠΉΡΠ΅ www.iaip.ru). ΠΡΠΈ Π²ΡΠ±ΠΎΡΠ΅ ΡΠΈΠΏΠ° ΠΏΠ΅ΡΠ΅ΡΠ°Π±ΠΎΡΠΊΠΈ ΠΏΡΠΎΠΈΠ·Π²ΠΎΠ΄ΠΈΡΠ΅Π»Ρ Π½Π΅ Π² ΠΏΠΎΡΠ»Π΅Π΄Π½ΡΡ ΠΎΡΠ΅ΡΠ΅Π΄Ρ Π΄ΡΠΌΠ°Π΅Ρ ΠΎ ΡΠΎΠΌ, ΡΡΠΎΠ±Ρ Π²ΡΡΠ°Π±Π°ΡΡΠ²Π°ΡΡ ΠΏΡΠΎΠ΄ΡΠΊΡΠΈΡ Ρ Π²ΡΡΠΎΠΊΠΎΠΉ Π΄ΠΎΠ±Π°Π²Π»Π΅Π½Π½ΠΎΠΉ ΡΡΠΎΠΈΠΌΠΎΡΡΡΡ, ΡΡΠΎΠ±Ρ ΠΎΠ½Π° Π±ΡΠ»Π° Π²ΠΎΡΡΡΠ΅Π±ΠΎΠ²Π°Π½Π° ΡΡΠ½ΠΊΠΎΠΌ ΠΈ ΠΈΠΌΠ΅Π»Π° Π΄ΠΎΡΡΠ°ΡΠΎΡΠ½ΡΠΉ ΡΡΠΎΠΊ Π³ΠΎΠ΄Π½ΠΎΡΡΠΈ.
Π‘Π°ΠΌΠΎΠ΅ ΠΏΡΠΎΡΡΠΎΠ΅ β ΠΎΠ±ΡΠ°ΡΠΈΡΡΡΡ ΠΊ ΠΏΡΠΎΡΠ΅ΡΡΠΈΠΎΠ½Π°Π»Π°ΠΌ, ΠΊΠΎΡΠΎΡΡΠ΅ ΠΏΠΎΠ΄ΡΠΊΠ°ΠΆΡΡ: ΠΊΠ°ΠΊΠΎΠ΅ Π²ΡΠ±ΡΠ°ΡΡ ΠΎΠ±ΠΎΡΡΠ΄ΠΎΠ²Π°Π½ΠΈΠ΅, Π³Π΄Π΅ Π½Π°ΠΉΡΠΈ ΡΠΏΠ΅ΡΠΈΠ°Π»ΠΈΠ·ΠΈΡΠΎΠ²Π°Π½Π½ΡΡ Π»ΠΈΡΠ΅ΡΠ°ΡΡΡΡ ΠΈ Π½ΠΎΡΠΌΠ°ΡΠΈΠ²Π½ΠΎ-ΡΠ΅Ρ Π½ΠΈΡΠ΅ΡΠΊΡΡ Π΄ΠΎΠΊΡΠΌΠ΅Π½ΡΠ°ΡΠΈΡ, ΠΊΠ°ΠΊ ΡΠ΅ΡΡΠΈΡΠΈΡΠΈΡΠΎΠ²Π°ΡΡ ΠΏΡΠΎΠ΄ΡΠΊΡΠΈΡ.
ΠΠ°ΠΏΡΠΈΠΌΠ΅Ρ, ΠΈΠ·Π²Π΅ΡΡΠ½ΡΠΉ ΠΏΡΠΎΠΈΠ·Π²ΠΎΠ΄ΠΈΡΠ΅Π»Ρ ΠΌΡΡΠ½ΡΡ ΠΏΠΎΠ»ΡΡΠ°Π±ΡΠΈΠΊΠ°ΡΠΎΠ² ΠΈΠ· Π’Π°ΡΠ°ΡΡΡΠ°Π½Π° ΠΏΠΎΡΡΠ°Π²ΠΈΠ» ΡΠ΅Π»ΡΡ ΡΠ°Π·ΡΠ°Π±ΠΎΡΠ°ΡΡ Π΄ΠΎΠΊΡΠΌΠ΅Π½ΡΠ°ΡΠΈΡ Π½Π° ΠΏΠ΅Π»ΡΠΌΠ΅Π½ΠΈ ΠΈ ΠΌΡΡΠ½ΡΠ΅ ΠΏΠΎΠ»ΡΡΠ°Π±ΡΠΈΠΊΠ°ΡΡ (Π½Π°ΡΡΡΠ°Π»ΡΠ½ΡΠ΅, ΡΡΠ±Π»Π΅Π½ΡΠ΅, ΠΏΠ°Π½ΠΈΡΠΎΠ²Π°Π½Π½ΡΠ΅, Π»ΡΠ»Ρ-ΠΊΠ΅Π±Π°Π±Ρ, Π±ΠΈΡΡΡΠ΅ΠΊΡΡ, ΡΠ΅ΡΡΠ΅Π»ΠΈ) Ρ ΠΌΠ°ΠΊΡΠΈΠΌΠ°Π»ΡΠ½ΠΎ Π²ΠΎΠ·ΠΌΠΎΠΆΠ½ΡΠΌ ΡΡΠΎΠΊΠΎΠΌ ΡΠ΅Π°Π»ΠΈΠ·Π°ΡΠΈΠΈ. ΠΡΠΎ ΡΠ²ΡΠ·Π°Π½ΠΎ Ρ ΡΠ΅ΠΌ, ΡΡΠΎ ΠΊΡΡΠΏΠ½ΡΠ΅ ΠΏΡΠΎΠΈΠ·Π²ΠΎΠ΄ΠΈΡΠ΅Π»ΠΈ ΠΏΠΎΡΡΠ°Π²Π»ΡΡΡ Π² ΠΌΠ°Π³Π°Π·ΠΈΠ½Ρ ΠΠ°Π·Π°Π½ΠΈ ΠΈ ΠΠ°Π±Π΅ΡΠ΅ΠΆΠ½ΡΡ Π§Π΅Π»Π½ΠΎΠ² ΠΏΡΠΎΠ΄ΡΠΊΡΠΈΡ ΡΠΎ ΡΡΠΎΠΊΠΎΠΌ Π³ΠΎΠ΄Π½ΠΎΡΡΠΈ 6 ΠΌΠ΅Ρ., Π° ΠΌΠ΅ΡΡΠ½ΡΠ΅ ΠΏΡΠΎΠΈΠ·Π²ΠΎΠ΄ΠΈΡΠ΅Π»ΠΈ Β«ΠΎΡΡΡΠ°ΡΡΒ», Π²ΡΡΠ°Π±Π°ΡΡΠ²Π°Ρ ΠΏΡΠΎΠ΄ΡΠΊΡΠΈΡ ΡΠΎ ΡΡΠΎΠΊΠΎΠΌ ΡΠ΅Π°Π»ΠΈΠ·Π°ΡΠΈΠΈ Π½Π΅ Π±ΠΎΠ»Π΅Π΅ 3 ΠΌΠ΅Ρ. ΠΠ°ΡΠΈ ΡΠΏΠ΅ΡΠΈΠ°Π»ΠΈΡΡΡ Π½Π΅ ΡΠΎΠ»ΡΠΊΠΎ ΡΠ°Π·ΡΠ°Π±ΠΎΡΠ°Π»ΠΈ ΠΎΡΠΈΠ³ΠΈΠ½Π°Π»ΡΠ½ΡΡ Π΄ΠΎΠΊΡΠΌΠ΅Π½ΡΠ°ΡΠΈΡ, Π½ΠΎ ΠΈ ΠΏΡΠΎΠ²Π΅Π»ΠΈ ΡΠ΅ΡΡΠΈΡΠΈΠΊΠ°ΡΠΈΡ ΠΏΡΠΎΠ΄ΡΠΊΡΠΈΠΈ. Π’Π°ΠΊ ΡΡΠΎ Π½Π° ΠΏΡΠΈΠ»Π°Π²ΠΊΠ°Ρ Π’Π°ΡΠ°ΡΡΡΠ°Π½Π° ΡΠΊΠΎΡΠΎ ΠΏΠΎΡΠ²ΠΈΡΡΡ ΠΊΠΎΠ½ΠΊΡΡΠ΅Π½ΡΠΎΡΠΏΠΎΡΠΎΠ±Π½Π°Ρ ΠΌΡΡΠ½Π°Ρ ΠΏΡΠΎΠ΄ΡΠΊΡΠΈΡ ΠΌΠ΅ΡΡΠ½ΡΡ ΠΏΡΠΎΠΈΠ·Π²ΠΎΠ΄ΠΈΡΠ΅Π»Π΅ΠΉ.
ΠΠ΅ΠΎΠ±Ρ ΠΎΠ΄ΠΈΠΌΠΎ ΠΎΡΠΌΠ΅ΡΠΈΡΡ, ΡΡΠΎ ΠΏΠΎΠΊΡΠΏΠ°ΡΠ΅Π»ΠΈ ΡΠ΅ΠΉΡΠ°Ρ ΡΠ°Π·Π±ΠΈΡΠ°ΡΡΡΡ Π² ΠΏΡΠΎΠ΄ΡΠΊΡΠΈΠΈ Π½Π΅ Ρ ΡΠΆΠ΅ ΠΏΡΠΎΡΠ΅ΡΡΠΈΠΎΠ½Π°Π»ΠΎΠ²: ΠΈΠ·ΡΡΠ°ΡΡ, ΠΏΠΎ ΠΊΠ°ΠΊΠΎΠΌΡ Π½ΠΎΡΠΌΠ°ΡΠΈΠ²Ρ ΠΈΠ·Π³ΠΎΡΠΎΠ²Π»Π΅Π½Π° ΠΏΡΠΎΠ΄ΡΠΊΡΠΈΡ (ΠΠΠ‘Π’ ΠΈΠ»ΠΈ Π’Π£), ΠΊΠ°ΠΊΠΈΠ΅ ΠΈΡΠΏΠΎΠ»ΡΠ·ΡΡΡΡΡ Π΄ΠΎΠ±Π°Π²ΠΊΠΈ ΠΈ ΠΊΠΎΠ½ΡΠ΅ΡΠ²Π°Π½ΡΡ, ΠΊΠ°ΠΊΠΎΠΉ ΡΡΠΎΠΊ Π³ΠΎΠ΄Π½ΠΎΡΡΠΈ ΠΈ ΡΠ΅ΠΌ ΠΎΠ½ ΠΎΠ±ΡΡΠ»ΠΎΠ²Π»Π΅Π½. ΠΠΎΡΡΠΎΠΌΡ ΠΏΡΠΎΠΈΠ·Π²ΠΎΠ΄ΠΈΡΠ΅Π»Ρ, Π²ΡΠΏΡΡΠΊΠ°ΡΡΠΈΠΉ ΠΏΡΠΎΠ΄ΡΠΊΡΠΈΡ ΠΏΠΎ ΠΠΠ‘Π’Ρ, ΠΈΠΌΠ΅Π΅Ρ ΡΡΠ΄ ΠΏΡΠ΅ΠΈΠΌΡΡΠ΅ΡΡΠ², ΠΎΡΠ½ΠΎΠ²Π½ΠΎΠ΅ ΠΈΠ· ΠΊΠΎΡΠΎΡΡΡ β Π΄ΠΎΠ²Π΅ΡΠΈΠ΅ ΠΏΠΎΠΊΡΠΏΠ°ΡΠ΅Π»Ρ.
ΠΡΠ±ΠΎΡ ΡΠ΅Ρ Π½ΠΎΠ»ΠΎΠ³ΠΈΡΠ΅ΡΠΊΠΎΠ³ΠΎ ΠΎΠ±ΠΎΡΡΠ΄ΠΎΠ²Π°Π½ΠΈΡ
ΠΠΎΠ½Π΅ΡΠ½ΠΎ, ΡΡΠ°ΡΡΡ ΠΎΡΠΈΠ΅Π½ΡΠΈΡΠΎΠ²Π°Π½Π° ΡΠΊΠΎΡΠ΅Π΅ Π½Π° ΠΏΡΠ΅Π΄ΠΏΡΠΈΠ½ΠΈΠΌΠ°ΡΠ΅Π»Π΅ΠΉ, ΠΊΠΎΡΠΎΡΡΠ΅ ΠΏΡΠΈΠ½ΡΠ»ΠΈ ΡΠ΅ΡΠ΅Π½ΠΈΠ΅ ΠΎΡΠ³Π°Π½ΠΈΠ·ΠΎΠ²Π°ΡΡ ΠΏΡΠΎΠΈΠ·Π²ΠΎΠ΄ΡΡΠ²ΠΎ ΠΌΡΡΠ½ΡΡ ΠΏΠΎΠ»ΡΡΠ°Π±ΡΠΈΠΊΠ°ΡΠΎΠ² Π½Π΅Π±ΠΎΠ»ΡΡΠΈΡ ΠΎΠ±ΡΠ΅ΠΌΠΎΠ². Π’Π°ΠΊ, Π·Π½Π°ΡΠΈΡΠ΅Π»ΡΠ½Π°Ρ ΡΠ°ΡΡΡ ΠΏΡΠΎΠΈΠ·Π²ΠΎΠ΄ΠΈΡΠ΅Π»Π΅ΠΉ ΡΡΡΠ΅ΠΌΠΈΡΡΡ ΠΎΡ ΡΠ±ΠΎΡ ΡΠΊΠΎΡΠ° ΠΈ ΠΏΠ΅ΡΠ²ΠΈΡΠ½ΠΎΠΉ ΡΠ°Π·Π΄Π΅Π»ΠΊΠΈ ΡΡΡ ΠΏΠ΅ΡΠ΅ΠΉΡΠΈ ΠΊ ΡΠ³Π»ΡΠ±Π»Π΅Π½Π½ΠΎΠΉ ΠΏΠ΅ΡΠ΅ΡΠ°Π±ΠΎΡΠΊΠ΅ ΡΡΡΡΡ Ρ ΡΠ΅Π»ΡΡ ΠΏΠΎΡΡΠ°Π²ΠΊΠΈ ΠΏΠΎΡΡΠ΅Π±ΠΈΡΠ΅Π»Ρ ΠΊΠΎΠ½Π΅ΡΠ½ΡΡ ΠΏΡΠΎΠ΄ΡΠΊΡΠΎΠ² (ΠΊΠΎΠ»Π±Π°ΡΠ½ΡΡ ΠΈΠ·Π΄Π΅Π»ΠΈΠΉ ΠΈ ΠΏΠΎΠ»ΡΡΠ°Π±ΡΠΈΠΊΠ°ΡΠΎΠ²). ΠΡΠΎ ΡΠΏΠΎΡΠΎΠ±ΡΡΠ²ΡΠ΅Ρ Π²ΡΡ ΠΎΠ΄Ρ ΠΏΡΠΎΠΈΠ·Π²ΠΎΠ΄ΠΈΡΠ΅Π»Ρ Π½Π° ΡΠ΅Π³ΠΈΠΎΠ½Π°Π»ΡΠ½ΡΠΉ ΠΈ ΠΎΠ±ΡΠ΅ΡΠΎΡΡΠΈΠΉΡΠΊΠΈΠΉ ΡΡΠ½ΠΎΠΊ ΠΌΡΡΠΎΠΏΡΠΎΠ΄ΡΠΊΡΠΎΠ², ΡΠ½ΠΈΠΆΠ°Π΅Ρ ΡΠ΅Π±Π΅ΡΡΠΎΠΈΠΌΠΎΡΡΡ ΠΏΡΠΎΠ΄ΡΠΊΡΠΈΠΈ (ΠΈΠΌΠ΅Π½Π½ΠΎ ΡΠ½ΠΈΠΆΠ΅Π½ΠΈΠ΅ ΡΠ΅Π±Π΅ΡΡΠΎΠΈΠΌΠΎΡΡΠΈ Π΄Π΅Π»Π°Π΅Ρ ΡΡΠ½ΠΎΠΊ Β«Π±Π΅Π·Π΄ΠΎΠ½Π½ΡΠΌΒ», Π΄Π°Π΅Ρ Π²ΠΎΠ·ΠΌΠΎΠΆΠ½ΠΎΡΡΡ Β«ΠΈΠ³ΡΠ°ΡΡΒ» ΡΠ΅Π½ΠΎΠΉ), ΡΠ²Π΅Π»ΠΈΡΠΈΠ²Π°Π΅Ρ ΡΠ΅Π½ΡΠ°Π±Π΅Π»ΡΠ½ΠΎΡΡΡ ΠΏΡΠΎΠΈΠ·Π²ΠΎΠ΄ΡΡΠ²Π°, ΡΠΎΠ·Π΄Π°Π΅Ρ Π΄ΠΎΠΏΠΎΠ»Π½ΠΈΡΠ΅Π»ΡΠ½ΡΠ΅ ΡΠ°Π±ΠΎΡΠΈΠ΅ ΠΌΠ΅ΡΡΠ°.
ΠΡΠΈ ΠΌΠΎΠ΄Π΅ΡΠ½ΠΈΠ·Π°ΡΠΈΠΈ ΠΏΡΠΎΠΈΠ·Π²ΠΎΠ΄ΡΡΠ²Π° Π²Π°ΠΆΠ½ΠΎ Π·Π½Π°ΡΡ: ΠΊΠ°ΠΊΠ°Ρ ΠΌΠ°ΡΠΈΠ½Π° Π½ΡΠΆΠ΄Π°Π΅ΡΡΡ Π² Π·Π°ΠΌΠ΅Π½Π΅ ΠΈΠ»ΠΈ ΠΊΠ°ΠΊΠΈΠ΅ Π΅Π΄ΠΈΠ½ΠΈΡΡ ΠΎΠ±ΠΎΡΡΠ΄ΠΎΠ²Π°Π½ΠΈΡ Π½Π΅ΠΎΠ±Ρ ΠΎΠ΄ΠΈΠΌΠΎ ΠΏΡΠΈΠΎΠ±ΡΠ΅ΡΡΠΈ ΠΈ (ΡΡΠΎ ΠΎΡΠ΅Π½Ρ Π²Π°ΠΆΠ½ΠΎ!) ΠΏΡΠ°Π²ΠΈΠ»ΡΠ½ΠΎ Π²ΡΡΡΠΎΠΈΡΡ Π² Π»ΠΈΠ½ΠΈΡ, Π²ΠΎΠ·ΠΌΠΎΠΆΠ½ΠΎΡΡΡ ΠΈΡΠΏΠΎΠ»ΡΠ·ΠΎΠ²Π°Π½ΠΈΡ Π±Π΅Π·ΠΎΡΡ ΠΎΠ΄Π½ΡΡ ΡΠ΅Ρ Π½ΠΎΠ»ΠΎΠ³ΠΈΠΉ. Π£ ΡΠΏΠ΅ΡΠΈΠ°Π»ΠΈΡΡΠΎΠ² ΠΈΠΌΠ΅ΡΡΡΡ ΠΎΡΠ²Π΅ΡΡ Π½Π° ΡΡΠ°Π½Π΄Π°ΡΡΠ½ΡΠ΅ Π²ΠΎΠΏΡΠΎΡΡ: ΡΠ°Π·ΡΠ°Π±ΠΎΡΠ°Π½Ρ ΠΊΠΎΠΌΠΌΠ΅ΡΡΠ΅ΡΠΊΠΈΠ΅ ΠΏΡΠ΅Π΄Π»ΠΎΠΆΠ΅Π½ΠΈΡ ΠΈ ΡΡΠΊΠΈΠ·Π½ΡΠ΅ ΠΏΡΠΎΠ΅ΠΊΡΡ, ΡΠΊΠΎΠΌΠΏΠ»Π΅ΠΊΡΠΎΠ²Π°Π½Ρ ΡΠ΅Ρ Π° ΠΈ Π²ΡΡΡΡΠΎΠ΅Π½Ρ ΡΠ΅Ρ Π½ΠΎΠ»ΠΎΠ³ΠΈΡΠ΅ΡΠΊΠΈΠ΅ ΡΠ΅ΠΏΠΎΡΠΊΠΈ. Π‘ Π½Π΅ΡΡΠ°Π½Π΄Π°ΡΡΠ½ΡΠΌΠΈ Π²ΠΎΠΏΡΠΎΡΠ°ΠΌΠΈ ΡΠΎΠΆΠ΅ Π»ΡΡΡΠ΅ ΠΎΠ±ΡΠ°ΡΠ°ΡΡΡΡ ΠΊ ΠΏΡΠΎΡΠ΅ΡΡΠΈΠΎΠ½Π°Π»Π°ΠΌ, ΡΡΠΎ ΠΏΠΎΠ·Π²ΠΎΠ»ΠΈΡ ΡΠ΅ΡΠΈΡΡ ΠΈΡ Π² ΠΊΠΎΡΠΎΡΠΊΠΈΠ΅ ΡΡΠΎΠΊΠΈ ΠΈ Ρ Π½Π°ΠΈΠΌΠ΅Π½ΡΡΠΈΠΌΠΈ Π·Π°ΡΡΠ°ΡΠ°ΠΌΠΈ.
Π‘ΡΠ°Π½Π΄Π°ΡΡΠ½ΡΠΌ Π²Π°ΡΠΈΠ°Π½ΡΠΎΠΌ ΠΌΠΎΠ΄Π΅ΡΠ½ΠΈΠ·Π°ΡΠΈΠΈ Β«ΡΠ±ΠΎΠΉΠ½ΠΎΠ³ΠΎΒ» ΠΏΡΠΎΠΈΠ·Π²ΠΎΠ΄ΡΡΠ²Π° ΡΠ²Π»ΡΠ΅ΡΡΡ ΠΎΡΠ³Π°Π½ΠΈΠ·Π°ΡΠΈΡ ΠΌΠΈΠ½ΠΈ-ΡΠ΅Ρ Π° ΠΏΠΎ ΠΏΡΠΎΠΈΠ·Π²ΠΎΠ΄ΡΡΠ²Ρ ΠΊΠΎΠ»Π±Π°ΡΠ½ΡΡ ΠΈΠ·Π΄Π΅Π»ΠΈΠΉ ΡΠΈΡΠΎΠΊΠΎΠ³ΠΎ Π°ΡΡΠΎΡΡΠΈΠΌΠ΅Π½ΡΠ° Ρ ΠΏΡΠΎΠΈΠ·Π²ΠΎΠ΄ΠΈΡΠ΅Π»ΡΠ½ΠΎΡΡΡΡ ΠΎΡ 300 Π΄ΠΎ 5 000 ΠΊΠ³/ΡΠΌΠ΅Π½Ρ.
ΠΠ»Ρ ΠΊΠΎΠΌΠΏΠ»Π΅ΠΊΡΠ°ΡΠΈΠΈ ΠΌΠΈΠ½ΠΈ-ΡΠ΅Ρ ΠΎΠ² ΡΠΏΠ΅ΡΠΈΠ°Π»ΠΈΡΡΡ ΠΏΡΠ΅Π΄Π»Π°Π³Π°ΡΡ ΠΈΡΠΏΠΎΠ»ΡΠ·ΠΎΠ²Π°ΡΡ ΠΎΡΠ΅ΡΠ΅ΡΡΠ²Π΅Π½Π½ΠΎΠ΅ ΠΎΠ±ΠΎΡΡΠ΄ΠΎΠ²Π°Π½ΠΈΠ΅, ΡΡΠΎ ΠΎΠ±ΡΡΠ»ΠΎΠ²Π»Π΅Π½ΠΎ, ΠΏΡΠ΅ΠΆΠ΄Π΅ Π²ΡΠ΅Π³ΠΎ, ΠΎΠΏΡΠΈΠΌΠ°Π»ΡΠ½ΡΠΌ ΡΠΎΠΎΡΠ½ΠΎΡΠ΅Π½ΠΈΠ΅ΠΌ ΠΊΠ°ΡΠ΅ΡΡΠ²Π° ΠΈ ΡΠ΅Π½Ρ.
Π‘Π΅ΠΉΡΠ°Ρ ΠΏΡΠ°ΠΊΡΠΈΡΠ΅ΡΠΊΠΈ Π»ΡΠ±ΠΎΠ΅, ΠΈΠΌΠ΅ΡΡΠ΅Π΅ΡΡ Π² ΠΏΡΠΎΠ΄Π°ΠΆΠ΅ ΠΎΠ±ΠΎΡΡΠ΄ΠΎΠ²Π°Π½ΠΈΠ΅, ΠΏΠΎΠ·Π²ΠΎΠ»ΡΠ΅Ρ ΠΏΠΎΠ»ΡΡΠΈΡΡ Π²ΡΡΠΎΠΊΠΎΠΊΠ°ΡΠ΅ΡΡΠ²Π΅Π½Π½ΡΠ΅ ΠΊΠΎΠ»Π±Π°ΡΠ½ΡΠ΅ ΠΈΠ·Π΄Π΅Π»ΠΈΡ, Π½ΠΎ ΠΎΡΠ΅Π½Ρ Π²Π°ΠΆΠ½ΠΎ Π½Π°ΠΉΡΠΈ ΡΠΎΡΠ½ΠΎΠ΅ ΡΠΎΠΎΡΠ½ΠΎΡΠ΅Π½ΠΈΠ΅: ΠΊΠΎΠ»Π±Π°ΡΠ½ΡΠ΅ ΠΈΠ·Π΄Π΅Π»ΠΈΡ ΠΈ ΠΌΡΡΠ½ΡΠ΅ ΠΏΠΎΠ»ΡΡΠ°Π±ΡΠΈΠΊΠ°ΡΡ Π΄ΠΎΠ»ΠΆΠ½Ρ Π±ΡΡΡ ΠΊΠ°ΡΠ΅ΡΡΠ²Π΅Π½Π½ΡΠΌΠΈ ΠΈ ΠΎΠ΄Π½ΠΎΠ²ΡΠ΅ΠΌΠ΅Π½Π½ΠΎ Π½Π΅Π΄ΠΎΡΠΎΠ³ΠΈΠΌΠΈ β ΠΈΠΌΠ΅Π½Π½ΠΎ ΡΠΎΠ³Π΄Π° ΠΎΠ½ΠΈ Π±ΡΠ΄ΡΡ ΠΏΠΎΠ»ΡΠ·ΠΎΠ²Π°ΡΡΡΡ ΠΏΠΎΠ²ΡΡΠ΅Π½Π½ΡΠΌ ΡΠΏΡΠΎΡΠΎΠΌ.
ΠΠ° ΡΡΠ½ΠΊΠ΅ ΠΏΡΠΈΡΡΡΡΡΠ²ΡΠ΅Ρ ΠΎΠ±ΠΎΡΡΠ΄ΠΎΠ²Π°Π½ΠΈΠ΅ Π·Π°ΠΏΠ°Π΄Π½ΡΡ ΠΏΡΠΎΠΈΠ·Π²ΠΎΠ΄ΠΈΡΠ΅Π»Π΅ΠΉ, Π½ΠΎ ΠΎΠ½ΠΎ Π΄ΠΎΡΠΎΠΆΠ΅ ΠΎΡΠ΅ΡΠ΅ΡΡΠ²Π΅Π½Π½ΠΎΠ³ΠΎ Π² Π½Π΅ΡΠΊΠΎΠ»ΡΠΊΠΎ ΡΠ°Π·, ΠΈ ΠΎΡΠ½Π°ΡΡΠΈΡΡ ΠΊΠΎΠ»Π±Π°ΡΠ½ΡΠΉ ΡΠ΅Ρ ΠΌΠ°ΡΠΈΠ½Π°ΠΌΠΈ Hi-ΠΊΠ»Π°ΡΡΠ° ΠΌΠΎΠ³ΡΡ ΡΠ΅Π±Π΅ ΠΏΠΎΠ·Π²ΠΎΠ»ΠΈΡΡ ΡΠΎΠ»ΡΠΊΠΎ ΠΊΡΡΠΏΠ½ΡΠ΅ ΠΏΡΠ΅Π΄ΠΏΡΠΈΡΡΠΈΡ.
ΠΠ°ΠΊ Π±ΡΠ»ΠΎ ΠΎΡΠΌΠ΅ΡΠ΅Π½ΠΎ Π²ΡΡΠ΅, ΠΏΡΠΈ ΠΏΡΠΎΠΈΠ·Π²ΠΎΠ΄ΡΡΠ²Π΅ ΠΊΠΎΠ»Π±Π°ΡΠ½ΡΡ ΠΈΠ·Π΄Π΅Π»ΠΈΠΉ ΠΌΡΡΠΎ ΠΏΠΎΠ΄Π²Π΅ΡΠ³Π°Π΅ΡΡΡ Π½Π΅ΡΠΊΠΎΠ»ΡΠΊΠΈΠΌ ΠΎΠ±ΡΠ·Π°ΡΠ΅Π»ΡΠ½ΡΠΌ ΠΌΠ°Π½ΠΈΠΏΡΠ»ΡΡΠΈΡΠΌ, ΠΏΠΎΡΡΠΎΠΌΡ ΡΠ΅Ρ Π²ΠΊΠ»ΡΡΠ°Π΅Ρ Π² ΡΠ΅Π±Ρ ΠΎΡΠ½ΠΎΠ²Π½ΠΎΠ΅ ΠΎΠ±ΠΎΡΡΠ΄ΠΎΠ²Π°Π½ΠΈΠ΅, Ρ. Π΅. Π²ΡΠΏΠΎΠ»Π½ΡΡΡΠ΅Π΅ Π·Π°Π΄Π°Π½Π½ΡΠΉ ΡΠ΅Ρ Π½ΠΎΠ»ΠΎΠ³ΠΈΡΠ΅ΡΠΊΠΈΠΉ ΠΏΡΠΎΡΠ΅ΡΡ ΠΈ Π½Π΅ΠΏΠΎΡΡΠ΅Π΄ΡΡΠ²Π΅Π½Π½ΠΎ ΠΊΠΎΠ½ΡΠ°ΠΊΡΠΈΡΡΡΡΠ΅Π΅ Ρ ΡΡΡΡΠ΅ΠΌ, ΠΈ Π²ΡΠΏΠΎΠΌΠΎΠ³Π°ΡΠ΅Π»ΡΠ½ΠΎΠ΅ ΠΎΠ±ΠΎΡΡΠ΄ΠΎΠ²Π°Π½ΠΈΠ΅, ΠΎΠ±Π΅ΡΠΏΠ΅ΡΠΈΠ²Π°ΡΡΠ΅Π΅ ΡΠ°Π±ΠΎΡΡ ΠΎΡΠ½ΠΎΠ²Π½ΠΎΠ³ΠΎ. ΠΡΠΈΠΌΠ΅ΡΠ½ΡΠΉ ΠΊΠΎΠΌΠΏΠ»Π΅ΠΊΡ ΠΎΠ±ΠΎΡΡΠ΄ΠΎΠ²Π°Π½ΠΈΡ Π΄Π»Ρ Π½Π΅Π±ΠΎΠ»ΡΡΠΎΠ³ΠΎ ΡΠ΅Ρ Π° ΠΏΡΠΈΠ²Π΅Π΄Π΅Π½ Π² ΡΠ°Π±Π»ΠΈΡΠ΅.
- ΠΠ°ΠΈΠΌΠ΅Π½ΠΎΠ²Π°Π½ΠΈΠ΅ ΠΎΠ±ΠΎΡΡΠ΄ΠΎΠ²Π°Π½ΠΈΡ
- ΠΠΎΠΏΡΠΈΠ»ΡΠ½Π°Ρ ΠΊΠ°ΠΌΠ΅ΡΠ°
- Π₯ΠΎΠ»ΠΎΠ΄ΠΈΠ»ΡΠ½Π°Ρ ΠΊΠ°ΠΌΠ΅ΡΠ° ΠΠ₯Π‘ (ΡΡΠ΅Π΄Π½Π΅ΡΠ΅ΠΌΠΏΠ΅ΡΠ°ΡΡΡΠ½Π°Ρ) ΠΈ ΠΠ₯Π (Π½ΠΈΠ·ΠΊΠΎΡΠ΅ΠΌΠΏΠ΅ΡΠ°ΡΡΡΠ½Π°Ρ)*
- ΠΠ»Π΅ΠΊΡΡΠΎΠΌΡΡΠΎΡΡΠ±ΠΊΠ° (Π²ΠΎΠ»ΡΠΎΠΊ)
- ΠΡΡΡΠ΅Ρ
- Π€Π°ΡΡΠ΅ΠΌΠ΅ΡΠ°Π»ΠΊΠ°
- Π¨ΠΏΡΠΈΡ ΠΊΠΎΠ»Π±Π°ΡΠ½ΡΠΉ Π²Π°ΠΊΡΡΠΌΠ½ΡΠΉ
- ΠΠΌΠΊΠΎΡΡΠΈ Π΄Π»Ρ Π·Π°ΡΠΎΠ»ΠΊΠΈ ΡΠ°ΡΡΠ°
- Π‘ΡΠΎΠ» ΠΏΡΠΎΠΈΠ·Π²ΠΎΠ΄ΡΡΠ²Π΅Π½Π½ΡΠΉ
- Π‘ΡΠΎΠ» Π΄Π»Ρ Π²ΡΠ·ΠΊΠΈ ΠΊΠΎΠ»Π±Π°Ρ Π‘ΠΠ-1950
- Π’Π΅Π»Π΅ΠΆΠΊΠ° ΡΠ΅Ρ Π½ΠΎΠ»ΠΎΠ³ΠΈΡΠ΅ΡΠΊΠ°Ρ Π€Π’Π’-200
- ΠΡΠ΄ΠΎΠ³Π΅Π½Π΅ΡΠ°ΡΠΎΡ ΡΠ΅ΡΡΡΠ°ΠΉΡΠΎΠ³ΠΎ Π»ΡΠ΄Π°*
ΠΠ»Ρ ΡΠΎΠ³ΠΎ ΡΡΠΎΠ±Ρ Π²ΡΡΠ°Π±Π°ΡΡΠ²Π°ΡΡ ΠΌΡΡΠ½ΡΠ΅ Π΄Π΅Π»ΠΈΠΊΠ°ΡΠ΅ΡΡ, ΠΏΡΠ΅Π΄Π»Π°Π³Π°Π΅ΠΌΡΠΉ ΠΊΠΎΠΌΠΏΠ»Π΅ΠΊΡ ΠΎΠ±ΠΎΡΡΠ΄ΠΎΠ²Π°Π½ΠΈΡ Π½Π΅ΠΎΠ±Ρ ΠΎΠ΄ΠΈΠΌΠΎ Π΄ΠΎΠΏΠΎΠ»Π½ΠΈΡΡ ΡΠΏΡΠΈΡΠ΅ΠΌ-ΠΈΠ½ΡΠ΅ΠΊΡΠΎΡΠΎΠΌ ΠΈ ΠΌΡΡΠΎΠΌΠ°ΡΡΠ°ΠΆΠ΅ΡΠΎΠΌ, ΠΊΠΎΡΠΎΡΡΠ΅ ΠΏΠΎΠ·Π²ΠΎΠ»ΡΡ ΠΏΡΠΈΠ΄Π°ΡΡ ΠΈΠ·Π΄Π΅Π»ΠΈΡΠΌ ΠΌΡΠ³ΠΊΠΈΠΉ, Π½Π΅ΠΏΠΎΠ²ΡΠΎΡΠΈΠΌΡΠΉ Π²ΠΊΡΡ ΠΈ ΡΡΡ Π»ΡΡ ΡΡΡΡΠΊΡΡΡΡ.
ΠΠ΅ΡΡΠ°Π½Π΄Π°ΡΡΠ½ΡΠΉ ΠΏΠΎΠ΄Ρ ΠΎΠ΄ ΠΊ ΡΠ΅ΡΠ΅Π½ΠΈΡ Π²ΠΎΠΏΡΠΎΡΠΎΠ² ΠΎΡΠ³Π°Π½ΠΈΠ·Π°ΡΠΈΠΈ ΠΏΡΠΎΠΈΠ·Π²ΠΎΠ΄ΡΡΠ²Π° β ΠΊΠΎΠ³Π΄Π° ΠΎΠΊΠΎΠ½ΡΠ°ΡΠ΅Π»ΡΠ½ΠΎΠ΅ ΡΠ΅ΡΠ΅Π½ΠΈΠ΅ ΠΏΡΠΈΠ½ΠΈΠΌΠ°Π΅ΡΡΡ ΠΏΠΎΡΠ»Π΅ ΡΡΠ°ΡΠ΅Π»ΡΠ½ΠΎΠ³ΠΎ Π°Π½Π°Π»ΠΈΠ·Π° ΠΈΡΡ ΠΎΠ΄Π½ΡΡ Π΄Π°Π½Π½ΡΡ (Π½Π°Π»ΠΈΡΠΈΠ΅ ΡΡΡΡΠ΅Π²ΠΎΠΉ Π±Π°Π·Ρ, ΠΎΡΠ³Π°Π½ΠΈΠ·ΠΎΠ²Π°Π½Π½ΠΎΠΉ ΡΠΈΡΡΠ΅ΠΌΡ ΡΠ±ΡΡΠ°, ΡΠ°Π±ΠΎΡΠ°ΡΡΠΈΠ΅ ΠΌΠΎΡΠ½ΠΎΡΡΠΈ, Ρ Π°ΡΠ°ΠΊΡΠ΅ΡΠΈΡΡΠΈΠΊΠ° ΡΠΏΡΠΎΡΠ°, ΠΏΠΎΠ·ΠΈΡΠΈΠΎΠ½ΠΈΡΠΎΠ²Π°Π½ΠΈΠ΅ ΠΏΡΠ΅Π΄ΠΏΡΠΈΡΡΠΈΡ) ΡΠΎΠ²ΠΌΠ΅ΡΡΠ½ΡΠΌΠΈ ΡΡΠΈΠ»ΠΈΡΠΌΠΈ Π·Π°ΠΊΠ°Π·ΡΠΈΠΊΠ° ΠΈ ΡΠΏΠ΅ΡΠΈΠ°Π»ΠΈΡΡΠΎΠ² ΡΠΈΡΠΌΡ.
ΠΠ° ΠΏΡΠΈΠΌΠ΅ΡΠΎΠΌ ΡΠ°ΠΊΠΎΠ³ΠΎ ΠΏΠΎΠ΄Ρ ΠΎΠ΄Π° ΠΌΡ ΠΎΠ±ΡΠ°ΡΠΈΠ»ΠΈΡΡ ΠΊ Π½Π°ΡΠΈΠΌ ΠΏΠ°ΡΡΠ½Π΅ΡΠ°ΠΌ (ΡΠΌ. Π Π΅Π΅ΡΡΡ ΠΠ°Π΄Π΅ΠΆΠ½ΡΡ ΠΠΎΡΡΠ°Π²ΡΠΈΠΊΠΎΠ² www.iaip.ru), ΠΊΠΎΡΠΎΡΡe ΠΈΠΌΠ΅ΡΡ ΠΎΠ³ΡΠΎΠΌΠ½ΡΠΉ ΠΎΠΏΡΡ ΠΏΠΎΡΡΠ°Π²ΠΊΠΈ ΠΌΡΡΠΎΠΏΠ΅ΡΠ΅ΡΠ°Π±Π°ΡΡΠ²Π°ΡΡΠΈΡ ΡΠ΅Ρ ΠΎΠ² Π² ΡΡΡΠ°Π½Ρ ΠΠ»ΠΈΠΆΠ½Π΅Π³ΠΎ ΠΠ°ΡΡΠ±Π΅ΠΆΡΡ, ΠΠ»ΠΈΠΆΠ½Π΅Π³ΠΎ ΠΠΎΡΡΠΎΠΊΠ° ΠΈ Π΄Ρ. ΡΡΡΠ°Π½. ΠΠ΄ΠΈΠ½ ΠΈΠ· Π½ΠΈΡ ΡΠΎΠΎΠ±ΡΠΈΠ», ΡΡΠΎ Β«Π½Π΅Π΄Π°Π²Π½ΠΎ ΠΊ Π½Π°ΠΌ ΠΎΠ±ΡΠ°ΡΠΈΠ»ΠΈΡΡ ΠΏΡΠ΅Π΄ΠΏΡΠΈΠ½ΠΈΠΌΠ°ΡΠ΅Π»ΠΈ ΠΈΠ· ΠΠ»ΠΈΠΆΠ½Π΅Π³ΠΎ ΠΠ°ΡΡΠ±Π΅ΠΆΡΡ, ΠΊΠΎΡΠΎΡΡΠ΅ Π·Π°Π΄ΡΠΌΠ°Π»ΠΈ ΠΎΡΠ³Π°Π½ΠΈΠ·ΠΎΠ²Π°ΡΡ ΠΏΡΠΎΠΈΠ·Π²ΠΎΠ΄ΡΡΠ²ΠΎ ΠΎΡΠΈΠ³ΠΈΠ½Π°Π»ΡΠ½ΠΎΠΉ ΠΌΡΡΠ½ΠΎΠΉ ΠΏΡΠΎΠ΄ΡΠΊΡΠΈΠΈ, ΡΠ°ΠΊΠΎΠΉ, ΠΊΠΎΡΠΎΡΠΎΠΉ Π½Π΅Ρ Π½ΠΈ Ρ ΠΊΠΎΠ³ΠΎ Π² ΡΠ΅Π³ΠΈΠΎΠ½Π΅Β».
ΠΠ° Π½Π°ΡΠ°Π»ΡΠ½ΠΎΠΌ ΡΡΠ°ΠΏΠ΅ ΡΠ°Π±ΠΎΡΡ Π±ΡΠ»ΠΎ ΠΏΠΎΠ΄Π³ΠΎΡΠΎΠ²Π»Π΅Π½ΠΎ Π½Π΅ΡΠΊΠΎΠ»ΡΠΊΠΎ ΠΊΠΎΠΌΠΌΠ΅ΡΡΠ΅ΡΠΊΠΈΡ ΠΏΡΠ΅Π΄Π»ΠΎΠΆΠ΅Π½ΠΈΠΉ, Π² ΠΊΠΎΡΠΎΡΡΡ ΠΏΡΠ΅Π΄Π»Π°Π³Π°Π»ΠΈΡΡ ΡΠ°Π·Π»ΠΈΡΠ½ΡΠ΅ Π²Π°ΡΠΈΠ°Π½ΡΡ ΠΊΠΎΠΌΠΏΠ»Π΅ΠΊΡΠ°ΡΠΈΠΈ ΡΠ΅Ρ ΠΎΠ² (ΠΏΡΠΎΠΈΠ·Π²ΠΎΠ΄ΠΈΡΠ΅Π»ΡΠ½ΠΎΡΡΡ, ΡΠ°Π·Π»ΠΈΡΠ½ΠΎΠ΅ ΡΠΎΡΠ΅ΡΠ°Π½ΠΈΠ΅ ΠΎΡΠ΅ΡΠ΅ΡΡΠ²Π΅Π½Π½ΡΡ ΠΈ ΠΈΠΌΠΏΠΎΡΡΠ½ΡΡ ΠΌΠ°ΡΠΈΠ½). ΠΠΎΡΠ»Π΅ ΠΎΠ±ΡΡΠΆΠ΄Π΅Π½ΠΈΡ Π±ΡΠ»ΠΎ ΠΏΡΠΈΠ½ΡΡΠΎ ΡΠ΅ΡΠ΅Π½ΠΈΠ΅ ΡΠΊΠΎΠΌΠΏΠ»Π΅ΠΊΡΠΎΠ²Π°ΡΡ ΡΠ΅Ρ Π° ΠΈΠΌΠΏΠΎΡΡΠ½ΡΠΌ ΠΎΠ±ΠΎΡΡΠ΄ΠΎΠ²Π°Π½ΠΈΠ΅ΠΌ, ΠΏΠΎΠ·Π²ΠΎΠ»ΡΡΡΠΈΠΌ Π²ΡΡΠ°Π±Π°ΡΡΠ²Π°ΡΡ ΠΌΡΡΠ½ΡΠ΅ ΠΏΠΎΠ»ΡΡΠ°Π±ΡΠΈΠΊΠ°ΡΡ Ρ ΡΠΈΡΠΎΠΊΠΎΠΉ Π°ΡΡΠΎΡΡΠΈΠΌΠ΅Π½ΡΠ½ΠΎΠΉ ΠΌΠ°ΡΡΠΈΡΠ΅ΠΉ. ΠΠ° ΡΠ»Π΅Π΄ΡΡΡΠ΅ΠΌ ΡΡΠ°ΠΏΠ΅ β ΡΠ°Π·ΡΠ°Π±ΠΎΡΠ°Π½ ΡΡΠΊΠΈΠ·Π½ΡΠΉ ΠΏΡΠΎΠ΅ΠΊΡ Π΄Π»Ρ ΡΠ΅Ρ ΠΎΠ², ΠΊΠΎΡΠΎΡΡΠΉ ΠΏΠΎΠ·Π²ΠΎΠ»ΠΈΠ»:
- ΠΎΡΠ΅Π½ΠΈΡΡ ΡΡΠ½ΠΊΡΠΈΠΎΠ½Π°Π»ΡΠ½ΠΎ-ΡΠ΅Ρ Π½ΠΎΠ»ΠΎΠ³ΠΈΡΠ΅ΡΠΊΡΡ ΡΡ Π΅ΠΌΡ ΠΏΡΠΎΠΈΠ·Π²ΠΎΠ΄ΡΡΠ²Π°,
- ΠΏΡΠΎΡΠ°Π±ΠΎΡΠ°ΡΡ ΠΎΠΏΡΠΈΠΌΠ°Π»ΡΠ½ΡΠΉ ΡΠΎΡΡΠ°Π² ΠΎΠ±ΠΎΡΡΠ΄ΠΎΠ²Π°Π½ΠΈΡ,
- ΠΈΠ·ΡΡΠΈΡΡ ΡΠΏΠ΅ΡΠΈΡΠΈΠΊΠ°ΡΠΈΡ ΠΎΠ±ΠΎΡΡΠ΄ΠΎΠ²Π°Π½ΠΈΡ,
- ΡΠ΄Π΅Π»Π°ΡΡ ΠΊΡΠ°ΡΠΊΠΎΠ΅ ΠΎΠΏΠΈΡΠ°Π½ΠΈΠ΅ ΡΠ΅Ρ Π½ΠΎΠ»ΠΎΠ³ΠΈΡΠ΅ΡΠΊΠΎΠ³ΠΎ ΠΏΡΠΎΡΠ΅ΡΡΠ°,
- ΡΡΠΎΡΠΌΡΠ»ΠΈΡΠΎΠ²Π°ΡΡ ΠΏΠ΅ΡΠ΅ΡΠ΅Π½Ρ ΠΎΡΠ½ΠΎΠ²Π½ΡΡ ΡΡΠ΅Π±ΠΎΠ²Π°Π½ΠΈΠΉ ΠΏΠΎ ΠΈΠ½ΠΆΠ΅Π½Π΅ΡΠ½ΠΎΠΌΡ ΠΎΠ±Π΅ΡΠΏΠ΅ΡΠ΅Π½ΠΈΡ ΠΏΠΎ ΠΏΡΠ΅Π΄Π²Π°ΡΠΈΡΠ΅Π»ΡΠ½ΠΎΠΌΡ ΠΏΠ»Π°Π½Ρ,
- Π΄Π°ΡΡ ΡΠ΅ΠΊΠΎΠΌΠ΅Π½Π΄Π°ΡΠΈΠΈ ΠΏΠΎ ΡΠΊΡΠΏΠ»ΠΈΠΊΠ°ΡΠΈΠΈ ΠΏΠΎΠΌΠ΅ΡΠ΅Π½ΠΈΠΉ ΠΈ ΡΠ°ΡΡΡΠ°Π½ΠΎΠ²ΠΊΠ΅ ΠΎΠ±ΠΎΡΡΠ΄ΠΎΠ²Π°Π½ΠΈΡ Ρ ΡΠΊΠ°Π·Π°Π½ΠΈΠ΅ΠΌ ΡΠΎΡΠ΅ΠΊ ΠΏΠΎΠ΄Π²ΠΎΠ΄Π° ΡΠ»Π΅ΠΊΡΡΠΎΡΠ½Π΅ΡΠ³ΠΈΠΈ ΠΈ Π²ΠΎΠ΄ΠΎΡΠ½Π°Π±ΠΆΠ΅Π½ΠΈΡ.
ΠΡ Π·Π½Π°Π»ΠΈ, ΡΡΠΎ Π½Π°Ρ ΠΊΠ»ΠΈΠ΅Π½Ρ ΡΡΡΠ΅ΠΌΠΈΡΡΡ ΠΌΠ°ΠΊΡΠΈΠΌΠ°Π»ΡΠ½ΠΎ ΡΠ°ΡΡΠΈΡΠΈΡΡ Π°ΡΡΠΎΡΡΠΈΠΌΠ΅Π½Ρ Π²ΡΠΏΡΡΠΊΠ°Π΅ΠΌΠΎΠΉ ΠΏΡΠΎΠ΄ΡΠΊΡΠΈΠΈ, Π·Π°Π½ΡΡΡ ΡΠ²ΠΎΡ Π½ΠΈΡΡ Π½Π° ΡΡΠ½ΠΊΠ΅, ΠΏΠΎΡΡΠΎΠΌΡ ΠΏΡΠ΅Π΄Π»ΠΎΠΆΠΈΠ»ΠΈ ΠΏΡΠΈΠΎΠ±ΡΠ΅ΡΡΠΈ ΡΠ΅Ρ Π½ΠΎΠ»ΠΎΠ³ΠΈΡΠ΅ΡΠΊΠΎΠ΅ ΠΎΠ±ΠΎΡΡΠ΄ΠΎΠ²Π°Π½ΠΈΠ΅ ΡΠΈΡΠΌΡ Deighton (ΠΠ΅Π»ΠΈΠΊΠΎΠ±ΡΠΈΡΠ°Π½ΠΈΡ). ΠΠ±ΠΎΡΡΠ΄ΠΎΠ²Π°Π½ΠΈΠ΅ ΠΈΡΠΏΠΎΠ»ΡΠ·ΡΠ΅ΡΡΡ Π΄Π»Ρ Π²ΡΠΏΡΡΠΊΠ° ΡΡΠ±Π»Π΅Π½ΡΡ ΠΌΡΡΠ½ΡΡ ΠΈ ΡΡΠ±Π½ΡΡ ΠΏΠΎΠ»ΡΡΠ°Π±ΡΠΈΠΊΠ°ΡΠΎΠ²: ΠΊΠΎΡΠ»Π΅Ρ, ΡΠ΅ΡΡΠ΅Π»Π΅ΠΉ, Π³Π°ΠΌΠ±ΡΡΠ³Π΅ΡΠΎΠ², Π½Π°Π³Π³Π΅ΡΡΠΎΠ², ΡΡΠ±Π½ΡΡ ΠΏΠ°Π»ΠΎΡΠ΅ΠΊ β ΠΈ Π΄Π»Ρ ΠΏΡΠΈΠ³ΠΎΡΠΎΠ²Π»Π΅Π½ΠΈΡ Π²Π΅Π³Π΅ΡΠ°ΡΠΈΠ°Π½ΡΠΊΠΈΡ Π±Π»ΡΠ΄. Π ΠΏΠΎΡΠΊΠΎΠ»ΡΠΊΡ Π½Π°Ρ ΠΏΠ°ΡΡΠ½Π΅Ρ Π΄Π΅Π»Π°Π΅Ρ ΡΡΠ°Π²ΠΊΡ Π½Π° ΡΠ΅Π°Π»ΠΈΠ·Π°ΡΠΈΡ Π½ΠΎΠ²ΡΡ ΠΈΠ΄Π΅ΠΉ, Π΅Π³ΠΎ Π·Π°ΠΈΠ½ΡΠ΅ΡΠ΅ΡΠΎΠ²Π°Π»Π° Π²ΠΎΠ·ΠΌΠΎΠΆΠ½ΠΎΡΡΡ ΠΏΡΠΎΠΈΠ·Π²ΠΎΠ΄ΠΈΡΡ Π½Π° ΡΡΠΎΠΌ ΠΆΠ΅ ΠΎΠ±ΠΎΡΡΠ΄ΠΎΠ²Π°Π½ΠΈΠΈ Π°ΡΠ°Π½ΡΠΈΠ½ΠΈ ΠΈ ΠΊΠ°ΡΡΠΎΡΠ΅Π»ΡΠ½ΡΠ΅ ΠΊΡΠΎΠΊΠ΅ΡΡ Ρ Π±Π΅ΠΊΠΎΠ½ΠΎΠΌ.
ΠΠ°Π½Π½ΠΎΠ΅ ΠΎΠ±ΠΎΡΡΠ΄ΠΎΠ²Π°Π½ΠΈΠ΅ ΠΈΠ΄Π΅Π°Π»ΡΠ½ΠΎ ΠΏΠΎΠ΄Ρ ΠΎΠ΄ΠΈΡ Π΄Π»Ρ ΠΏΡΠ΅Π΄ΠΏΡΠΈΡΡΠΈΠΉ ΠΌΠ°Π»ΠΎΠ³ΠΎ ΠΈ ΡΡΠ΅Π΄Π½Π΅Π³ΠΎ Π±ΠΈΠ·Π½Π΅ΡΠ° ΠΈ ΠΏΠΎΠ·Π²ΠΎΠ»ΡΠ΅Ρ ΡΠΎΡΠΌΠΎΠ²Π°ΡΡ ΡΠΈΡΠΎΠΊΡΡ Π³Π°ΠΌΠΌΡ ΠΈΠ·Π΄Π΅Π»ΠΈΠΉ, ΠΏΠΎΠΊΡΡΠ²Π°ΡΡ ΠΏΠΎΠ²Π΅ΡΡ Π½ΠΎΡΡΡ ΠΏΡΠΎΠ΄ΡΠΊΡΠΎΠ² ΠΆΠΈΠ΄ΠΊΠΎΠΉ ΠΈ ΡΡΡ ΠΎΠΉ ΠΏΠ°Π½ΠΈΡΠΎΠ²ΠΎΡΠ½ΠΎΠΉ ΡΠΌΠ΅ΡΡΡ, ΠΎΠ±ΠΆΠ°ΡΠΈΠ²Π°ΡΡ Π²ΠΎ ΡΡΠΈΡΡΡΠ΅ Π΄ΠΎ Π³ΠΎΡΠΎΠ²Π½ΠΎΡΡΠΈ.
Π ΡΠ΅Ρ Π½ΠΎΠ»ΠΎΠ³ΠΈΡΠ΅ΡΠΊΡΡ ΡΠ΅ΠΏΠΎΡΠΊΡ Π²Ρ ΠΎΠ΄ΡΡ ΠΊΠΎΡΠ»Π΅ΡΠΎΡΠΎΡΠΌΠΎΠ²ΠΎΡΠ½ΡΠ΅ ΠΌΠ°ΡΠΈΠ½Ρ, ΠΌΠ°ΡΠΈΠ½Π° Π΄Π»Ρ Π½Π°Π½Π΅ΡΠ΅Π½ΠΈΡ Π½Π° ΠΏΠΎΠ²Π΅ΡΡ Π½ΠΎΡΡΡ ΠΊΠΎΡΠ»Π΅Ρ ΠΆΠΈΠ΄ΠΊΠΎΠΉ ΠΏΠ°Π½ΠΈΡΠΎΠ²ΠΎΡΠ½ΠΎΠΉ ΡΠΌΠ΅ΡΠΈ, ΠΌΠ°ΡΠΈΠ½Π° Π΄Π»Ρ Π½Π°Π½Π΅ΡΠ΅Π½ΠΈΡ Π½Π° ΠΏΠΎΠ²Π΅ΡΡ Π½ΠΎΡΡΡ ΠΊΠΎΡΠ»Π΅Ρ ΠΆΠΈΠ΄ΠΊΠΎΠΉ ΠΏΠ°Π½ΠΈΡΠΎΠ²ΠΎΡΠ½ΠΎΠΉ ΡΠΌΠ΅ΡΠΈ.
Π£Π½ΠΈΠ²Π΅ΡΡΠ°Π»ΡΠ½ΡΠ΅ ΠΊΠΎΡΠ»Π΅ΡΠΎΡΠΎΡΠΌΠΎΠ²ΠΎΡΠ½ΡΠ΅ ΠΌΠ°ΡΠΈΠ½Ρ ΡΠ΅ΡΠΈΠΈ Formatic ΠΈΠΌΠ΅ΡΡ Π±Π°ΡΠ°Π±Π°Π½Π½ΡΠΉ ΡΠΈΠΏ ΠΈΡΠΏΠΎΠ»Π½Π΅Π½ΠΈΡ ΠΈ ΡΠ°Π±ΠΎΡΠ°ΡΡ ΡΠ»Π΅Π΄ΡΡΡΠΈΠΌ ΠΎΠ±ΡΠ°Π·ΠΎΠΌ: ΡΠ°ΡΡ Π·Π°Π³ΡΡΠΆΠ°Π΅ΡΡΡ Π² Π±ΡΠ½ΠΊΠ΅Ρ ΠΈ Ρ ΠΏΠΎΠΌΠΎΡΡΡ ΡΡΡΠ°Π½ΠΎΠ²Π»Π΅Π½Π½ΡΡ Π½Π° Π²Π΅ΡΡΠΈΠΊΠ°Π»ΡΠ½ΠΎΠΌ Π²Π°Π»Ρ Π»ΠΎΠΏΠ°ΡΡΠ΅ΠΉ ΠΏΠ΅ΡΠ΅ΠΌΠ΅ΡΠ°Π΅ΡΡΡ ΠΊ Π±Π°ΡΠ°Π±Π°Π½Ρ. ΠΠ°ΡΠ°Π±Π°Π½ ΠΈΠΌΠ΅Π΅Ρ ΠΎΡΠ²Π΅ΡΡΡΠΈΡ ΡΠΎΠΎΡΠ²Π΅ΡΡΡΠ²ΡΡΡΠ΅ΠΉ ΡΠΎΡΠΌΡ (ΠΎΡ 1 Π΄ΠΎ 3) ΠΈ ΠΏΠΎΡΡΠ΅Π½Ρ, Π² ΡΠΎΡΠ½ΠΎΡΡΠΈ ΠΏΠΎΠ²ΡΠΎΡΡΡΡΠΈΠΉ ΠΊΠΎΠ½ΡΠΈΠ³ΡΡΠ°ΡΠΈΡ ΠΎΡΠ²Π΅ΡΡΡΠΈΡ. Π ΠΊΡΠ°ΠΉΠ½Π΅ΠΌ Π²Π΅ΡΡ Π½Π΅ΠΌ ΠΏΠΎΠ»ΠΎΠΆΠ΅Π½ΠΈΠΈ Π±Π°ΡΠ°Π±Π°Π½Π° ΠΏΠΎΡΡΠ΅Π½Ρ ΠΎΠΏΡΡΠΊΠ°Π΅ΡΡΡ, Π±Π»Π°Π³ΠΎΠ΄Π°ΡΡ ΡΠ΅ΠΌΡ ΠΎΠ±ΡΠ°Π·ΡΠ΅ΡΡΡ ΠΏΠΎΠ»ΠΎΡΡΡ, Π²ΠΏΠΎΡΠ»Π΅Π΄ΡΡΠ²ΠΈΠΈ Π·Π°ΠΏΠΎΠ»Π½ΡΠ΅ΠΌΠ°Ρ ΡΠ°ΡΡΠ΅ΠΌ. ΠΡΠΈ ΠΏΠΎΠ²ΠΎΡΠΎΡΠ΅ Π±Π°ΡΠ°Π±Π°Π½Π° Π² ΠΊΡΠ°ΠΉΠ½Π΅Π΅ Π½ΠΈΠΆΠ½Π΅Π΅ ΠΏΠΎΠ»ΠΎΠΆΠ΅Π½ΠΈΠ΅ ΡΡΠΎΡΠΌΠΎΠ²Π°Π½Π½ΡΠΉ ΠΏΡΠΎΠ΄ΡΠΊΡ Π²ΡΡΠ°Π»ΠΊΠΈΠ²Π°Π΅ΡΡΡ ΠΏΠΎΡΡΠ½Π΅ΠΌ Π½Π° Π΄Π²ΠΈΠΆΡΡΠΈΠΉΡΡ ΡΡΠ°Π½ΡΠΏΠΎΡΡΠ΅Ρ. Π‘ ΡΠ΅Π»ΡΡ ΠΏΡΠ΅Π΄ΠΎΡΠ²ΡΠ°ΡΠ΅Π½ΠΈΡ Π²Π΅ΡΠΎΡΡΠ½ΠΎΠ³ΠΎ Π½Π°ΡΡΡΠ΅Π½ΠΈΡ ΡΠ΅Π»ΠΎΡΡΠ½ΠΎΡΡΠΈ Π΄ΠΎΠΏΠΎΠ»Π½ΠΈΡΠ΅Π»ΡΠ½ΠΎ ΠΏΡΠ΅Π΄ΡΡΠΌΠ°ΡΡΠΈΠ²Π°Π΅ΡΡΡ ΡΡΠ½ΠΊΡΠΈΡ ΡΡΠ΅Π·Π°Π½ΠΈΡ ΠΈΠ·Π΄Π΅Π»ΠΈΡ ΡΡΡΡΠ½ΠΎΠΉ.
ΠΠ»ΠΈΠ΅Π½Ρ ΠΎΡΠ΅Π½Ρ Π·Π°ΠΈΠ½ΡΠ΅ΡΠ΅ΡΠΎΠ²Π°Π»ΡΡ Π²ΠΎΠ·ΠΌΠΎΠΆΠ½ΠΎΡΡΡΡ ΠΏΠΎΠ»ΡΡΠ΅Π½ΠΈΡ ΠΈΠ·Π΄Π΅Π»ΠΈΠΉ ΡΠ°ΠΌΡΡ ΡΠ°Π·Π½ΠΎΠΎΠ±ΡΠ°Π·Π½ΡΡ ΠΊΠΎΠ½ΡΠΈΠ³ΡΡΠ°ΡΠΈΠΉ: ΠΎΡ ΡΡΠ°Π΄ΠΈΡΠΈΠΎΠ½Π½ΡΡ ΠΊΡΡΠ³Π»ΡΡ Π΄ΠΎ Π²Π΅ΡΡΠΌΠ° ΠΏΡΠΈΡΡΠ΄Π»ΠΈΠ²ΡΡ ΠΈ Π·Π°ΠΌΡΡΠ»ΠΎΠ²Π°ΡΡΡ , Π½Π°ΠΏΡΠΈΠΌΠ΅Ρ, Β«Π·Π°ΠΉΡΠΈΠΊΠΎΠ²Β» ΠΈ Β«ΠΌΠΈΡΠ΅ΠΊΒ». ΠΡΡΠ°Π±ΠΎΡΠΊΠ° Β«Π΄Π΅ΡΡΠΊΠΎΠΉΒ» ΠΏΡΠΎΠ΄ΡΠΊΡΠΈΠΈ ΠΏΠΎΠ·Π²ΠΎΠ»ΠΈΠ»Π° ΠΈΠΌ ΠΏΡΠ°ΠΊΡΠΈΡΠ΅ΡΠΊΠΈ Β«ΠΌΠΎΠ½ΠΎΠΏΠΎΠ»ΠΈΠ·ΠΈΡΠΎΠ²Π°ΡΡΒ» ΡΡΠΎΡ ΡΠ΅Π³ΠΌΠ΅Π½Ρ ΡΡΠ½ΠΊΠ° Π² ΡΠ΅Π³ΠΈΠΎΠ½Π΅.
ΠΠ»Ρ Π²ΡΡΠ°Π±ΠΎΡΠΊΠΈ ΠΈΠ·Π΄Π΅Π»ΠΈΠΉ ΠΎΠΊΡΡΠ³Π»ΠΎΠΉ (ΠΊΡΡΠ³Π»ΠΎΠΉ ΠΈΠ»ΠΈ Π²ΡΡΡΠ½ΡΡΠΎΠΉ) ΡΠΎΡΠΌΡ ΠΈΡΠΏΠΎΠ»ΡΠ·ΡΠ΅ΡΡΡ ΠΎΠ±ΠΎΡΡΠ΄ΠΎΠ²Π°Π½ΠΈΠ΅ Ρ ΠΈΠ½ΡΠΌ ΠΏΡΠΈΠ½ΡΠΈΠΏΠΎΠΌ Π΄Π΅ΠΉΡΡΠ²ΠΈΡ β ΡΠΊΡΡΡΡΠ·ΠΈΠΎΠ½Π½ΠΎ-ΡΠΎΡΠΌΡΡΡΠ΅Π΅. ΠΡΠΎΡΠ΅ΡΡ ΡΠΎΡΠΌΠΎΠ²Π°Π½ΠΈΡ ΠΈΠ·Π΄Π΅Π»ΠΈΡ ΠΏΡΠΎΠΈΡΡ ΠΎΠ΄ΠΈΡ ΡΠ»Π΅Π΄ΡΡΡΠΈΠΌ ΠΎΠ±ΡΠ°Π·ΠΎΠΌ: ΡΠ΅ΡΡΠΎ ΠΈ Π½Π°ΡΠΈΠ½ΠΊΠ° Π·Π°Π³ΡΡΠΆΠ°ΡΡΡΡ Π² ΠΎΡΠ΄Π΅Π»ΡΠ½ΡΠ΅ ΡΠΏΠ΅ΡΠΈΠ°Π»ΡΠ½ΡΠ΅ Π±ΡΠ½ΠΊΠ΅ΡΠ°. ΠΠ°Π»Π΅Π΅ ΠΏΡΠΎΠΈΡΡ ΠΎΠ΄ΠΈΡ ΠΏΠΎΡΡΠ΅ΠΏΠ΅Π½Π½ΠΎΠ΅ Π½Π°Π³Π½Π΅ΡΠ°Π½ΠΈΠ΅ ΠΊΠ°ΠΆΠ΄ΠΎΠ³ΠΎ ΠΈΠ½Π³ΡΠ΅Π΄ΠΈΠ΅Π½ΡΠ° Π² ΡΠΎΡΠΌΠΎΠ²ΠΎΡΠ½ΡΠΉ ΡΠ·Π΅Π» Π°Π²ΡΠΎΠΌΠ°ΡΠ°, Π³Π΄Π΅ ΠΎΡΡΡΠ΅ΡΡΠ²Π»ΡΠ΅ΡΡΡ ΡΠΎΡΠ½Π°Ρ Π΄ΠΎΠ·ΠΈΡΠΎΠ²ΠΊΠ° Π½Π°ΡΠΈΠ½ΠΊΠΈ Π΄Π»Ρ ΠΈΠ·Π΄Π΅Π»ΠΈΡ. ΠΠ°ΡΠ΅ΠΌ, ΠΈΠ·Π΄Π΅Π»ΠΈΠ΅ Ρ Π½Π°ΡΠΈΠ½ΠΊΠΎΠΉ ΠΎΠΊΠΎΠ½ΡΠ°ΡΠ΅Π»ΡΠ½ΠΎ ΡΠΎΡΠΌΠΈΡΡΠ΅ΡΡΡ ΠΈ ΠΎΡΡΠ°ΠΆΠΈΠ²Π°Π΅ΡΡΡ Ρ ΠΏΠΎΠΌΠΎΡΡΡ Π΄ΠΈΠ°ΡΡΠ°Π³ΠΌΠ΅Π½ΡΠ½ΠΎΠ³ΠΎ ΠΌΠ΅Ρ Π°Π½ΠΈΠ·ΠΌΠ°, ΠΏΡΠΈ ΡΡΠΎΠΌ Π΄ΠΈΠ°ΡΡΠ°Π³ΠΌΠ° Π½Π΅ ΠΎΠ±ΡΠ΅Π·Π°Π΅Ρ, Π° Π·Π°Π²Π°Π»ΡΡΠΎΠ²ΡΠ²Π°Π΅Ρ ΠΈΠ·Π΄Π΅Π»ΠΈΠ΅ ΠΈ Π½Π°ΡΠΈΠ½ΠΊΠ° ΡΠ°Π²Π½ΠΎΠΌΠ΅ΡΠ½ΠΎ ΡΠ°ΡΠΏΡΠ΅Π΄Π΅Π»ΡΠ΅ΡΡΡ Π²Π½ΡΡΡΠΈ. ΠΠΊΡΡΡΡΠ·ΠΈΠΎΠ½Π½ΠΎ-ΡΠΎΡΠΌΡΡΡΠ΅Π΅ ΠΎΠ±ΠΎΡΡΠ΄ΠΎΠ²Π°Π½ΠΈΠ΅ ΡΠ°ΠΊΠΆΠ΅ ΠΏΠΎΠ·Π²ΠΎΠ»ΡΠ΅Ρ ΡΠ°Π±ΠΎΡΠ°ΡΡ Ρ ΡΠ°Π·Π»ΠΈΡΠ½ΡΠΌΠΈ ΡΠ°ΡΡΠ°ΠΌΠΈ: ΠΌΡΡΠ½ΡΠΌ, ΡΡΠ±Π½ΡΠΌ, ΠΊΡΡΠΈΠ½ΡΠΌ, ΠΊΠΎΡΠΎΡΡΠ΅ ΡΠ²Π»ΡΡΡΡΡ Β«ΠΎΠ±ΠΎΠ»ΠΎΡΠΊΠΎΠΉΒ» Π³ΠΎΡΠΎΠ²ΠΎΠ³ΠΎ ΠΏΡΠΎΠ΄ΡΠΊΡΠ°. Π Π² ΠΊΠ°ΡΠ΅ΡΡΠ²Π΅ Β«Π½Π°ΡΠΈΠ½ΠΊΠΈΒ» Π²ΠΎΠ·ΠΌΠΎΠΆΠ½ΠΎ ΠΈΡΠΏΠΎΠ»ΡΠ·ΠΎΠ²Π°ΡΡ ΡΡΡ, ΠΊΠ°ΡΡΠΎΡΠ΅Π»ΡΠ½ΠΎΠ΅ ΠΏΡΡΠ΅, ΡΠ°ΡΡΠΈ Π½Π° ΠΎΡΠ½ΠΎΠ²Π΅ ΠΎΠ²ΠΎΡΠ΅ΠΉ. ΠΡΡΡΡΠ°Ρ ΠΏΠ΅ΡΠ΅ΡΡΡΠΎΠΉΠΊΠ° ΠΎΠ±ΠΎΡΡΠ΄ΠΎΠ²Π°Π½ΠΈΡ (ΠΈΠ·ΠΌΠ΅Π½Π΅Π½ΠΈΠ΅ ΡΠΎΡΠΌΡ, ΡΠΎΠΎΡΠ½ΠΎΡΠ΅Π½ΠΈΠ΅ Β«Π½Π°ΡΠΈΠ½ΠΊΠΈΒ» ΠΈ Β«ΠΎΠ±ΠΎΠ»ΠΎΡΠΊΠΈΒ») ΠΏΠΎΠ·Π²ΠΎΠ»ΡΠ΅Ρ Π² ΡΠ΅ΡΠ΅Π½ΠΈΠ΅ ΡΠΌΠ΅Π½Ρ Π²ΡΠΏΡΡΠΊΠ°ΡΡ ΡΠΈΡΠΎΠΊΠΈΠΉ Π°ΡΡΠΎΡΡΠΈΠΌΠ΅Π½Ρ ΠΈΠ·Π΄Π΅Π»ΠΈΠΉ. Π Π·Π°Π²ΠΈΡΠΈΠΌΠΎΡΡΠΈ ΠΎΡ ΠΌΠΎΠ΄Π΅Π»ΠΈ ΠΊΠΎΡΠ»Π΅ΡΠΎΡΠΎΡΠΌΠΎΠ²ΠΎΡΠ½ΠΎΠ³ΠΎ Π°Π²ΡΠΎΠΌΠ°ΡΠ° Π²ΠΎΠ·ΠΌΠΎΠΆΠ½ΠΎ ΡΠ²Π΅Π»ΠΈΡΠ΅Π½ΠΈΠ΅ ΠΏΡΠΎΠΈΠ·Π²ΠΎΠ΄ΠΈΡΠ΅Π»ΡΠ½ΠΎΡΡΠΈ ΠΎΡ 1 200 Π΄ΠΎ 8 000 ΡΡΡΠΊ Π² ΡΠ°Ρ.
ΠΡ ΠΏΡΠ΅Π΄Π»ΠΎΠΆΠΈΠ»ΠΈ Π΄ΠΎΠΏΠΎΠ»Π½ΠΈΡΡ ΡΠ΅Ρ Π½ΠΎΠ»ΠΎΠ³ΠΈΡΠ΅ΡΠΊΡΡ ΡΠ΅ΠΏΠΎΡΠΊΡ ΠΎΠ±ΠΎΡΡΠ΄ΠΎΠ²Π°Π½ΠΈΠ΅ΠΌ ΡΠ΅ΡΠΈΠΈ EconoRobe, ΠΊΠΎΡΠΎΡΠΎΠ΅ ΠΏΡΠ΅Π΄Π½Π°Π·Π½Π°ΡΠ΅Π½ΠΎ Π΄Π»Ρ Π½Π°Π½Π΅ΡΠ΅Π½ΠΈΡ Π½Π° ΠΏΠΎΠ²Π΅ΡΡ Π½ΠΎΡΡΡ ΠΊΠΎΡΠ»Π΅Ρ ΠΆΠΈΠ΄ΠΊΠΎΠΉ ΠΏΠ°Π½ΠΈΡΠΎΠ²ΠΎΡΠ½ΠΎΠΉ ΡΠΌΠ΅ΡΠΈ β Π»ΡΠ΅Π·ΠΎΠ½Π° ΠΈΠ»ΠΈ ΠΊΠ»ΡΡΠ°. ΠΠ°ΡΠΈΠ½Ρ ΡΠΎΡΡΠΎΡΡ ΠΈΠ· ΠΎΡΠ½ΠΎΠ²Π°Π½ΠΈΡ Π½Π° ΠΊΠΎΠ»Π΅ΡΠ°Ρ (Π΄Π»Ρ ΡΠ΄ΠΎΠ±ΡΡΠ²Π° ΠΏΠ΅ΡΠ΅ΠΌΠ΅ΡΠ΅Π½ΠΈΡ), ΡΠ΅ΡΡΠ°ΡΠΎΠ³ΠΎ ΡΡΠ°Π½ΡΠΏΠΎΡΡΠ΅ΡΠ°, Π²Π°Π½Π½Ρ Π΄Π»Ρ Π»ΡΠ΅Π·ΠΎΠ½Π° (ΠΊΠ»ΡΡΠ°), Π½Π°ΡΠΎΡΠ° Π΄Π»Ρ ΠΏΠ΅ΡΠ΅ΠΊΠ°ΡΠΈΠ²Π°Π½ΠΈΡ ΠΆΠΈΠ΄ΠΊΠΎΡΡΠΈ, ΡΠ°ΡΠΏΡΠ΅Π΄Π΅Π»ΠΈΡΠ΅Π»ΡΠ½ΠΎΠΉ Π³ΠΎΠ»ΠΎΠ²ΠΊΠΈ Π΄Π»Ρ ΡΠ°Π²Π½ΠΎΠΌΠ΅ΡΠ½ΠΎΠ³ΠΎ ΡΡΠ΅ΠΊΠ°Π½ΠΈΡ ΠΏΠ°Π½ΠΈΡΠΎΠ²ΠΊΠΈ. Π‘ΡΠΎΡΠΌΠΎΠ²Π°Π½Π½ΡΠ΅ ΠΌΡΡΠ½ΡΠ΅ ΠΈ ΡΡΠ±Π½ΡΠ΅ ΠΈΠ·Π΄Π΅Π»ΠΈΡ ΡΠΊΠ»Π°Π΄ΡΠ²Π°ΡΡΡΡ Π½Π° ΡΠ΅ΡΡΠ°ΡΡΠΉ ΡΡΠ°Π½ΡΠΏΠΎΡΡΠ΅Ρ ΠΈ Π΄Π²ΠΈΠΆΡΡΡΡ Π²Π΄ΠΎΠ»Ρ Π½ΠΈΠΆΠ½Π΅ΠΉ Π²Π°Π½Π½Ρ ΡΠΊΠ²ΠΎΠ·Ρ Π½Π΅ΠΏΡΠ΅ΡΡΠ²Π½ΡΠ΅ ΠΏΠΎΡΠΎΠΊΠΈ ΠΊΠ»ΡΡΠ° (Π»ΡΠ΅Π·ΠΎΠ½Π°). ΠΠΎΠ»ΡΡΠ°Π±ΡΠΈΠΊΠ°ΡΡ ΠΏΡΠΈ ΡΡΠΎΠΌ ΠΊΠ°ΠΊ ΠΎΡΠΎΡΠ°ΡΡΡΡ, ΡΠ°ΠΊ ΠΈ ΡΠ°ΡΡΠΈΡΠ½ΠΎ ΠΏΠΎΠ³ΡΡΠΆΠ°ΡΡΡΡ Π² ΠΆΠΈΠ΄ΠΊΡΡ ΠΏΠ°Π½ΠΈΡΠΎΠ²ΠΊΡ. ΠΠ° Π²ΡΡ ΠΎΠ΄Π΅ ΠΈΠ·Π±ΡΡΠΎΠΊ ΠΊΠ»ΡΡΠ° Ρ ΠΏΠΎΠ²Π΅ΡΡ Π½ΠΎΡΡΠΈ ΠΏΡΠΎΠ΄ΡΠΊΡΠ° ΡΠ΄ΡΠ²Π°Π΅ΡΡΡ Π²Π΅Π½ΡΠΈΠ»ΡΡΠΎΡΠΎΠΌ ΠΈ Π½Π°ΠΏΡΠ°Π²Π»ΡΠ΅ΡΡΡ Π½Π° ΠΏΠΎΠ²ΡΠΎΡΠ½ΠΎΠ΅ ΠΈΡΠΏΠΎΠ»ΡΠ·ΠΎΠ²Π°Π½ΠΈΠ΅. Π’Π°ΠΊΠΈΠΌ ΠΎΠ±ΡΠ°Π·ΠΎΠΌ, ΠΏΡΠΎΠΈΡΡ ΠΎΠ΄ΠΈΡ Π½Π΅ΠΏΡΠ΅ΡΡΠ²Π½Π°Ρ ΡΠΈΡΠΊΡΠ»ΡΡΠΈΡ ΠΏΠ°Π½ΠΈΡΠΎΠ²ΠΊΠΈ ΠΈ Π΅Π΅ ΡΠ°Π²Π½ΠΎΠΌΠ΅ΡΠ½ΠΎΠ΅ ΡΠ°ΡΠΏΡΠ΅Π΄Π΅Π»Π΅Π½ΠΈΠ΅ ΠΏΠΎ ΠΏΠΎΠ²Π΅ΡΡ Π½ΠΎΡΡΠΈ ΠΊΠΎΡΠ»Π΅Ρ. Π‘Π΅ΡΡΠ°ΡΡΠΉ ΡΡΠ°Π½ΡΠΏΠΎΡΡΠ΅Ρ ΠΈΠΌΠ΅Π΅Ρ ΠΎΡΠ΄Π΅Π»ΡΠ½ΡΠΉ ΠΏΡΠΈΠ²ΠΎΠ΄, ΡΡΠΎ ΠΏΠΎΠ·Π²ΠΎΠ»ΡΠ΅Ρ ΡΠ΅Π³ΡΠ»ΠΈΡΠΎΠ²Π°ΡΡ ΡΠΊΠΎΡΠΎΡΡΡ Π΅Π³ΠΎ ΠΏΠ΅ΡΠ΅ΠΌΠ΅ΡΠ΅Π½ΠΈΡ (ΠΎΡ 1 Π΄ΠΎ 15 ΠΌ/ΠΌΠΈΠ½) ΠΈ Π² Π΄Π°Π»ΡΠ½Π΅ΠΉΡΠ΅ΠΌ ΡΠΎΡΡΡΠΊΠΎΠ²Π°ΡΡ ΠΌΠ°ΡΠΈΠ½Ρ Ρ Π΄ΡΡΠ³ΠΈΠΌΠΈ ΡΠΈΠΏΠ°ΠΌΠΈ ΠΎΠ±ΠΎΡΡΠ΄ΠΎΠ²Π°Π½ΠΈΡ. ΠΡΠΎΠΈΠ·Π²ΠΎΠ΄ΠΈΡΠ΅Π»ΡΠ½ΠΎΡΡΡ ΡΡΠΈΡ ΠΌΠ°ΡΠΈΠ½ ΠΈΠ·ΠΌΠ΅Π½ΡΠ΅ΡΡΡ Π² Π΄ΠΈΠ°ΠΏΠ°Π·ΠΎΠ½Π΅ 240β720 ΠΊΠ³ Π² ΡΠ°Ρ. ΠΠ°Π½ΠΈΡΠΎΠ²ΠΎΡΠ½ΡΠ΅ ΠΌΠ°ΡΠΈΠ½Ρ ΡΠ΅ΡΠΈΠΈ EconoCrumb ΡΠΏΠΎΡΠΎΠ±Π½Ρ ΡΠ°Π±ΠΎΡΠ°ΡΡ Ρ Π»ΡΠ±ΡΠΌΠΈ ΡΡΠ°ΠΊΡΠΈΡΠΌΠΈ ΠΏΠ°Π½ΠΈΡΠΎΠ²ΠΎΡΠ½ΡΡ ΡΠΌΠ΅ΡΠ΅ΠΉ β ΠΎΡ ΠΌΡΠΊΠΈ Π΄ΠΎ ΡΠΏΠ΅ΡΠΈΠΉ Π³ΡΡΠ±ΠΎΠ³ΠΎ ΠΏΠΎΠΌΠΎΠ»Π°.
ΠΡΠΎΠ΄ΡΠΊΡ, ΠΏΡΠ΅Π΄Π²Π°ΡΠΈΡΠ΅Π»ΡΠ½ΠΎ ΡΠ²Π»Π°ΠΆΠ½Π΅Π½Π½ΡΠΉ Ρ ΠΏΠΎΠΌΠΎΡΡΡ Π»ΡΠ΅Π·ΠΎΠ½Π° ΠΈΠ»ΠΈ ΠΊΠ»ΡΡΠ°, ΡΡΠ°Π½ΡΠΏΠΎΡΡΠΈΡΡΠ΅ΡΡΡ ΡΠ΅ΡΡΠ°ΡΡΠΌ ΠΊΠΎΠ½Π²Π΅ΠΉΠ΅ΡΠΎΠΌ ΠΈ ΠΏΠ΅ΡΠ΅Π½ΠΎΡΠΈΡΡΡ Π½Π° Π½ΠΈΠΆΠ½ΠΈΠΉ ΡΠ»ΠΎΠΉ ΡΡΡ ΠΎΠΉ ΠΏΠ°Π½ΠΈΡΠΎΠ²ΠΊΠΈ. ΠΡΠΈ ΠΏΡΠΈΠ±Π»ΠΈΠΆΠ΅Π½ΠΈΠΈ ΠΊ Π±ΡΠ½ΠΊΠ΅ΡΡ ΠΏΡΠΎΠ΄ΡΠΊΡ ΡΠ²Π΅ΡΡ Ρ ΡΠ°Π²Π½ΠΎΠΌΠ΅ΡΠ½ΠΎ ΠΏΠΎΡΡΠΏΠ°Π΅ΡΡΡ ΠΏΠ°Π½ΠΈΡΠΎΠ²ΠΊΠΎΠΉ. Π’ΠΎΠ»ΡΠΈΠ½Π° Π²Π΅ΡΡ Π½Π΅Π³ΠΎ ΡΠ»ΠΎΡ ΡΠ΅Π³ΡΠ»ΠΈΡΡΠ΅ΡΡΡ Π²ΡΡΡΠ½ΡΡ. ΠΠ·Π±ΡΡΠΊΠΈ ΠΏΠ°Π½ΠΈΡΠΎΠ²ΠΊΠΈ ΡΠ΄ΡΠ²Π°ΡΡΡΡ Π²Π΅Π½ΡΠΈΠ»ΡΡΠΎΡΠΎΠΌ ΠΈ Π²Π½ΠΎΠ²Ρ Π²ΠΎΠ·Π²ΡΠ°ΡΠ°ΡΡΡΡ Π² ΡΠΈΡΡΠ΅ΠΌΡ ΡΠΈΡΠΊΡΠ»ΡΡΠΈΠΈ. ΠΡΠΎΠΈΠ·Π²ΠΎΠ΄ΠΈΡΠ΅Π»ΡΠ½ΠΎΡΡΡ Π°Π³ΡΠ΅Π³Π°ΡΠ° β 240β720 ΠΊΠ³/Ρ. ΠΠΎΠ½Π²Π΅ΠΉΠ΅ΡΠ½ΡΠ΅ ΡΡΠΈΡΡΡΠ½ΠΈΡΡ ΡΠ΅ΡΠΈΠΈ EconoFry ΠΏΠΎΠ·Π²ΠΎΠ»ΡΡΡ ΠΎΠ±ΠΆΠ°ΡΠΈΠ²Π°ΡΡ ΡΠ°ΡΡΠΈΡΠ½ΠΎ ΠΈΠ»ΠΈ Π΄ΠΎ ΠΏΠΎΠ»Π½ΠΎΠΉ Π³ΠΎΡΠΎΠ²Π½ΠΎΡΡΠΈ ΡΡΠΎΡΠΌΠΎΠ²Π°Π½Π½ΡΠ΅ ΡΠ°Π½Π΅Π΅ ΠΈ ΠΏΠΎΠΊΡΡΡΡΠ΅ ΠΏΠ°Π½ΠΈΡΠΎΠ²ΠΊΠΎΠΉ ΠΌΡΡΠ½ΡΠ΅ ΠΈ ΡΡΠ±Π½ΡΠ΅ ΠΏΠΎΠ»ΡΡΠ°Π±ΡΠΈΠΊΠ°ΡΡ.
ΠΠ°ΠΊΠ»ΡΡΠΈΡΠ΅Π»ΡΠ½ΡΠΌ ΡΡΠ°ΠΏΠΎΠΌ ΡΡΠ°Π»ΠΈ: ΠΏΠΎΡΡΠ°Π²ΠΊΠ° ΠΎΠ±ΠΎΡΡΠ΄ΠΎΠ²Π°Π½ΠΈΡ, Π²ΡΠ΅Π·Π΄ ΡΠ΅Ρ Π½ΠΎΠ»ΠΎΠ³Π° ΠΈ Π±ΡΠΈΠ³Π°Π΄Ρ Π½Π°Π»Π°Π΄ΡΠΈΠΊΠΎΠ² Π΄Π»Ρ ΠΏΡΠΎΠ²Π΅Π΄Π΅Π½ΠΈΡ ΠΏΡΡΠΊΠΎ-Π½Π°Π»Π°Π΄ΠΎΡΠ½ΡΡ ΡΠ°Π±ΠΎΡ, ΠΊΠΎΡΠΎΡΡΠ΅ ΠΏΡΠΎΠ²Π΅Π»ΠΈ ΠΏΡΠΎΠ±Π½ΡΠΉ Π·Π°ΠΏΡΡΠΊ ΠΎΠ±ΠΎΡΡΠ΄ΠΎΠ²Π°Π½ΠΈΡ, Π²ΡΠ²Π΅Π»ΠΈ ΠΎΠ±ΠΎΡΡΠ΄ΠΎΠ²Π°Π½ΠΈΠ΅ Π½Π° ΡΠ΅Ρ Π½ΠΎΠ»ΠΎΠ³ΠΈΡΠ΅ΡΠΊΠΈΠΉ ΡΠ΅ΠΆΠΈΠΌ, ΠΎΠ±ΡΡΠΈΠ»ΠΈ ΠΏΠ΅ΡΡΠΎΠ½Π°Π».
ΠΡΠΎΠΌΠ΅ ΡΠ΅Ρ Π½ΠΎΠ»ΠΎΠ³ΠΈΡΠ΅ΡΠΊΠΎΠΉ ΡΠΎΡΡΠ°Π²Π»ΡΡΡΠ΅ΠΉ Π½Π°ΡΠΈΠΌ ΠΏΠ°ΡΡΠ½Π΅ΡΠ°ΠΌ ΡΡΠ΅Π±ΠΎΠ²Π°Π»Π°ΡΡ ΠΈΠ½ΡΠΎΡΠΌΠ°ΡΠΈΠΎΠ½Π½Π°Ρ ΠΏΠΎΠ΄Π΄Π΅ΡΠΆΠΊΠ°, ΠΏΠΎΡΡΠΎΠΌΡ ΡΠΏΠ΅ΡΠΈΠ°Π»ΠΈΡΡΡ ΠΏΠΎΠ΄ΠΎΠ±ΡΠ°Π»ΠΈ ΡΠΏΠ΅ΡΠΈΠ°Π»ΠΈΠ·ΠΈΡΠΎΠ²Π°Π½Π½ΡΡ Π»ΠΈΡΠ΅ΡΠ°ΡΡΡΡ ΠΈ Π½ΠΎΡΠΌΠ°ΡΠΈΠ²Π½ΠΎ-ΡΠ΅Ρ Π½ΠΈΡΠ΅ΡΠΊΡΡ Π΄ΠΎΠΊΡΠΌΠ΅Π½ΡΠ°ΡΠΈΡ (Π²ΠΎ ΠΌΠ½ΠΎΠ³ΠΈΡ ΡΡΡΠ°Π½Π°Ρ ΠΠ»ΠΈΠΆΠ½Π΅Π³ΠΎ ΠΠ°ΡΡΠ±Π΅ΠΆΡΡ ΡΠ°Π±ΠΎΡΠ°ΡΡ ΠΏΠΎ Π΄ΠΎΠΊΡΠΌΠ΅Π½ΡΠ°ΠΌ, ΡΠ°Π·ΡΠ°Π±ΠΎΡΠ°Π½Π½ΡΠΌ Π΅ΡΠ΅ Π² Π‘ΠΎΠ²Π΅ΡΡΠΊΠΎΠΌ Π‘ΠΎΡΠ·Π΅), ΠΏΡΠΎΠΊΠΎΠ½ΡΡΠ»ΡΡΠΈΡΠΎΠ²Π°Π»ΠΈ ΠΏΠΎ ΠΎΡΠ³Π°Π½ΠΈΠ·Π°ΡΠΈΠΈ ΠΏΡΠΎΡΠ΅Π΄ΡΡΡ ΡΠ΅ΡΡΠΈΡΠΈΠΊΠ°ΡΠΈΠΈ ΠΏΡΠΎΠΈΠ·Π²ΠΎΠ΄ΡΡΠ²Π° ΠΈ ΠΏΡΠΎΠ΄ΡΠΊΡΠΈΠΈ.
Π’Π°ΠΊΠΈΠΌ ΠΎΠ±ΡΠ°Π·ΠΎΠΌ, ΠΌΠΎΠΆΠ½ΠΎ ΡΠΊΠ°Π·Π°ΡΡ, ΡΡΠΎ Π±Π»Π°Π³ΠΎΠ΄Π°ΡΡ ΠΊΠΎΠΌΠΏΠ»Π΅ΠΊΡΠ½ΠΎΠΌΡ ΠΏΠΎΠ΄Ρ ΠΎΠ΄Ρ ΠΈ ΡΠΌΠ΅Π½ΠΈΡ ΡΠ΅ΡΠ°ΡΡ Π½Π΅ΡΡΠ°Π½Π΄Π°ΡΡΠ½ΡΠ΅ Π²ΠΎΠΏΡΠΎΡΡ Π² ΠΠ»ΠΈΠΆΠ½Π΅ΠΌ ΠΠ°ΡΡΠ±Π΅ΠΆΡΠ΅ ΠΏΠΎΡΠ²ΠΈΠ»ΡΡ Π½ΠΎΠ²ΡΠΉ ΠΏΡΠΎΠΈΠ·Π²ΠΎΠ΄ΠΈΡΠ΅Π»Ρ ΠΎΡΠΈΠ³ΠΈΠ½Π°Π»ΡΠ½ΡΡ Π²ΡΡΠΎΠΊΠΎΠΊΠ°ΡΠ΅ΡΡΠ²Π΅Π½Π½ΡΡ ΠΌΡΡΠ½ΡΡ ΠΏΠΎΠ»ΡΡΠ°Π±ΡΠΈΠΊΠ°ΡΠΎΠ².
Π Π·Π°ΠΊΠ»ΡΡΠ΅Π½ΠΈΠ΅, ΡΠ»Π΅Π΄ΡΠ΅Ρ ΠΎΡΠΌΠ΅ΡΠΈΡΡ, ΡΡΠΎ ΠΏΡΠΎΠΈΠ·Π²ΠΎΠ΄ΡΡΠ²ΠΎ ΠΌΡΡΠ½ΡΡ ΠΏΠΎΠ»ΡΡΠ°Π±ΡΠΈΠΊΠ°ΡΠΎΠ² ΠΌΠΎΠΆΠ΅Ρ Π±ΡΡΡ Π²ΡΠ³ΠΎΠ΄Π½ΡΠΌ ΠΈ ΠΏΡΠΈΠ±ΡΠ»ΡΠ½ΡΠΌ Π±ΠΈΠ·Π½Π΅ΡΠΎΠΌ, Π΅ΡΠ»ΠΈ ΠΏΡΠΈ ΠΎΡΠ³Π°Π½ΠΈΠ·Π°ΡΠΈΠΈ ΠΏΡΠΎΠΈΠ·Π²ΠΎΠ΄ΡΡΠ²Π° ΠΏΡΠ΅Π΄ΠΏΡΠΈΠ½ΡΡΡ Π½Π΅ΡΠΊΠΎΠ»ΡΠΊΠΎ ΠΎΠ±ΡΠ·Π°ΡΠ΅Π»ΡΠ½ΡΡ ΡΠ°Π³ΠΎΠ².
ΠΠΎ-ΠΏΠ΅ΡΠ²ΡΡ , ΠΏΡΠΎΠ²Π΅ΡΡΠΈ ΠΈΡΡΠ»Π΅Π΄ΠΎΠ²Π°Π½ΠΈΠ΅ ΡΡΠ½ΠΊΠ° ΠΊΠΎΠ»Π±Π°ΡΠ½ΡΡ ΠΈΠ·Π΄Π΅Π»ΠΈΠΉ ΠΈ ΠΌΡΡΠ½ΡΡ Π΄Π΅Π»ΠΈΠΊΠ°ΡΠ΅ΡΠΎΠ² ΡΠ²ΠΎΠ΅Π³ΠΎ ΡΠ΅Π³ΠΈΠΎΠ½Π°: ΠΈΠ·ΡΡΠΈΡΡ ΡΠΏΡΠΎΡ Π½Π° ΠΏΡΠΎΠ΄ΡΠΊΡΠΈΡ, ΡΠ΅Π½Ρ, Π°ΡΡΠΎΡΡΠΈΠΌΠ΅Π½Ρ, ΠΎΠ±ΡΠ΅ΠΌΡ Π²ΡΠΏΡΡΠΊΠ° ΠΈ ΠΏΡΠΎΠ΄Π°ΠΆ ΠΊΠΎΠ½ΠΊΡΡΠ΅Π½ΡΠΎΠ².
ΠΠΎ-Π²ΡΠΎΡΡΡ , ΡΠ΄Π΅Π»Π°ΡΡ ΠΏΡΠ°Π²ΠΈΠ»ΡΠ½ΡΠ΅ Π²ΡΠ²ΠΎΠ΄Ρ ΠΈ ΡΠ°ΡΡΡΠΈΡΠ°ΡΡ ΠΎΡΠ½ΠΎΠ²Π½ΡΠ΅ ΠΏΠ°ΡΠ°ΠΌΠ΅ΡΡΡ ΠΏΡΠΎΠΈΠ·Π²ΠΎΠ΄ΡΡΠ²Π° Ρ ΡΠ΅Π»ΡΡ ΠΏΠΎΠ»ΡΡΠ΅Π½ΠΈΡ ΠΌΠ°ΠΊΡΠΈΠΌΠ°Π»ΡΠ½ΠΎΠΉ ΠΏΡΠΈΠ±ΡΠ»ΠΈ.
ΠΡΠ½ΠΎΠ²Π½ΡΠΌ ΡΠ°ΠΊΡΠΎΡΠΎΠΌ, Π²Π»ΠΈΡΡΡΠΈΠΌ Π½Π° ΠΏΡΠΈΠ±ΡΠ»Ρ ΠΏΡΠ΅Π΄ΠΏΡΠΈΡΡΠΈΡ, ΡΠ²Π»ΡΡΡΡΡ ΡΠ΅Π½Ρ Π½Π° ΡΡΡΡΠ΅. ΠΠΎΡΡΠΎΠΌΡ, Π΅ΡΠ»ΠΈ ΠΎΠΏΡΠ΅Π΄Π΅Π»Π΅Π½Ρ ΠΏΠΎΡΡΠ°Π²ΡΠΈΠΊΠΈ ΡΡΡΡΡ, ΡΠ΅Π½Ρ Π½Π° ΠΊΠΎΠ½Π΅ΡΠ½ΡΡ ΠΏΡΠΎΠ΄ΡΠΊΡΠΈΡ ΡΡΠ°Π±ΠΈΠ»ΡΠ½ΡΠ΅ ΠΈ Π½ΠΈΠ·ΠΊΠΈΠ΅, ΠΎΠ½Π° ΠΏΠΎΠ»ΡΠ·ΡΠ΅ΡΡΡ ΠΏΠΎΡΡΠΎΡΠ½Π½ΡΠΌ ΡΠΏΡΠΎΡΠΎΠΌ, Π° Π²ΡΡΠΎΠΊΠ°Ρ ΠΏΡΠΈΠ±ΡΠ»Ρ Π³Π°ΡΠ°Π½ΡΠΈΡΠΎΠ²Π°Π½Π°.
ΠΡΠΎΠΌΠ΅ ΡΠΎΠ³ΠΎ, Π²Π°ΠΆΠ½ΡΠΌ ΠΌΠΎΠΌΠ΅Π½ΡΠΎΠΌ Π² ΡΠ°Π±ΠΎΡΠ΅ ΠΌΡΡΠΎΠΏΠ΅ΡΠ΅ΡΠ°Π±Π°ΡΡΠ²Π°ΡΡΠ΅Π³ΠΎ ΡΠ΅Ρ Π° ΡΠ²Π»ΡΠ΅ΡΡΡ ΠΊΠ°ΡΠ΅ΡΡΠ²ΠΎ ΠΏΡΠΎΠ΄ΡΠΊΡΠΈΠΈ, ΠΊΠΎΡΠΎΡΠΎΠ΅ Π²ΠΎ ΠΌΠ½ΠΎΠ³ΠΎΠΌ Π·Π°Π²ΠΈΡΠΈΡ ΠΎΡ ΠΈΡΠΏΠΎΠ»ΡΠ·ΡΠ΅ΠΌΡΡ ΡΠ΅Ρ Π½ΠΎΠ»ΠΎΠ³ΠΈΠΉ ΠΈ ΡΠ΅ΡΠ΅ΠΏΡΡΡ, Π° ΡΠ°ΠΊΠΆΠ΅ ΠΈΡ ΠΎΡΠΈΠ³ΠΈΠ½Π°Π»ΡΠ½ΠΎΡΡΠΈ ΠΈ Π΄ΡΡΠ³ΠΈΡ ΠΏΠ°ΡΠ°ΠΌΠ΅ΡΡΠΎΠ².
Π-ΡΡΠ΅ΡΡΠΈΡ , Π²ΡΠ±ΠΎΡ ΡΠΈΡΠΌΡ-ΠΏΠΎΡΡΠ°Π²ΡΠΈΠΊΠ° ΠΎΠ±ΠΎΡΡΠ΄ΠΎΠ²Π°Π½ΠΈΡ ΠΈ ΠΈΠ½ΡΠΎΡΠΌΠ°ΡΠΈΠΈ. ΠΡΠΎΡΠ΅ΡΡΠΈΠΎΠ½Π°Π»ΡΠ½ΠΎΠ΅ ΠΈΡΠΏΠΎΠ»ΡΠ·ΠΎΠ²Π°Π½ΠΈΠ΅ ΠΎΠ±ΠΎΡΡΠ΄ΠΎΠ²Π°Π½ΠΈΡ ΡΠΏΠΎΡΠΎΠ±ΡΡΠ²ΡΠ΅Ρ ΡΠ½ΠΈΠΆΠ΅Π½ΠΈΡ ΠΏΠΎΡΠ΅ΡΡ Π² ΠΏΡΠΎΠΈΠ·Π²ΠΎΠ΄ΡΡΠ²Π΅ ΠΈ Π²ΡΡΠ°Π±ΠΎΡΠΊΠ΅ ΠΊΠ°ΡΠ΅ΡΡΠ²Π΅Π½Π½ΠΎΠΉ ΠΊΠΎΠ½ΠΊΡΡΠ΅Π½ΡΠΎΡΠΏΠΎΡΠΎΠ±Π½ΠΎΠΉ ΠΏΡΠΎΠ΄ΡΠΊΡΠΈΠΈ.
Π’Π°ΠΊΠΈΠΌ ΠΎΠ±ΡΠ°Π·ΠΎΠΌ, ΡΡΠΎΠ±Ρ ΠΏΡΠΈΠΎΠ±ΡΠ΅ΡΡΠΈ ΠΊΠ°ΡΠ΅ΡΡΠ²Π΅Π½Π½ΠΎΠ΅ ΠΎΠ±ΠΎΡΡΠ΄ΠΎΠ²Π°Π½ΠΈΠ΅ Π΄Π»Ρ ΠΏΠ΅ΡΠ΅ΡΠ°Π±ΠΎΡΠΊΠΈ ΠΌΡΡΠ½ΠΎΠ³ΠΎ ΡΡΡΡΡ, ΡΠ΅ΡΠ°ΡΡ ΡΡΠ°Π½Π΄Π°ΡΡΠ½ΡΠ΅ ΠΈ ΠΎΡΠΈΠ³ΠΈΠ½Π°Π»ΡΠ½ΡΠ΅ Π·Π°Π΄Π°ΡΠΈ, Π½Π΅ΠΎΠ±Ρ ΠΎΠ΄ΠΈΠΌΠΎ ΠΎΠ±ΡΠ°ΡΠ°ΡΡΡΡ ΠΊ ΠΏΡΠΎΡΠ΅ΡΡΠΈΠΎΠ½Π°Π»Π°ΠΌ. ΠΠ½ΠΈ ΠΏΠΎΠΌΠΎΠ³ΡΡ Π½Π΅ ΡΠΎΠ»ΡΠΊΠΎ ΠΏΠΎΠ΄ΠΎΠ±ΡΠ°ΡΡ ΠΊΠ°ΡΠ΅ΡΡΠ²Π΅Π½Π½ΠΎΠ΅ ΠΎΠ±ΠΎΡΡΠ΄ΠΎΠ²Π°Π½ΠΈΠ΅, Π½ΠΎ ΠΈ ΠΎΠ±Π΅ΡΠΏΠ΅ΡΠ°Ρ ΠΏΠΎΠ»Π½ΡΠΉ ΠΊΠΎΠΌΠΏΠ»Π΅ΠΊΡ ΡΠ΅ΡΠ²ΠΈΡΠ½ΡΡ ΡΡΠ»ΡΠ³.
VN:F [1.9.22_1171]
ΠΏΠΎΠΆΠ°Π»ΡΠΉΡΡΠ° ΠΏΠΎΠ΄ΠΎΠΆΠ΄ΠΈΡΠ΅…
Rating: 4.6/5 (64 votes cast)
ΠΠ°ΠΊ ΠΎΡΠΊΡΡΡΡ ΡΠ²ΠΎΠΉ ΡΠ΅Ρ ΠΏΠΎ ΠΏΡΠΎΠΈΠ·Π²ΠΎΠ΄ΡΡΠ²Ρ ΠΌΡΡΠ½ΡΡ ΠΏΠΎΠ»ΡΡΠ°Π±ΡΠΈΠΊΠ°ΡΠΎΠ², 4.6 out of 5 based on 64 ratingsivan.cheredov.com
Π¦Π΅Ρ ΠΏΠΎ ΠΏΡΠΎΠΈΠ·Π²ΠΎΠ΄ΡΡΠ²Ρ Π¨ΠΠ¦
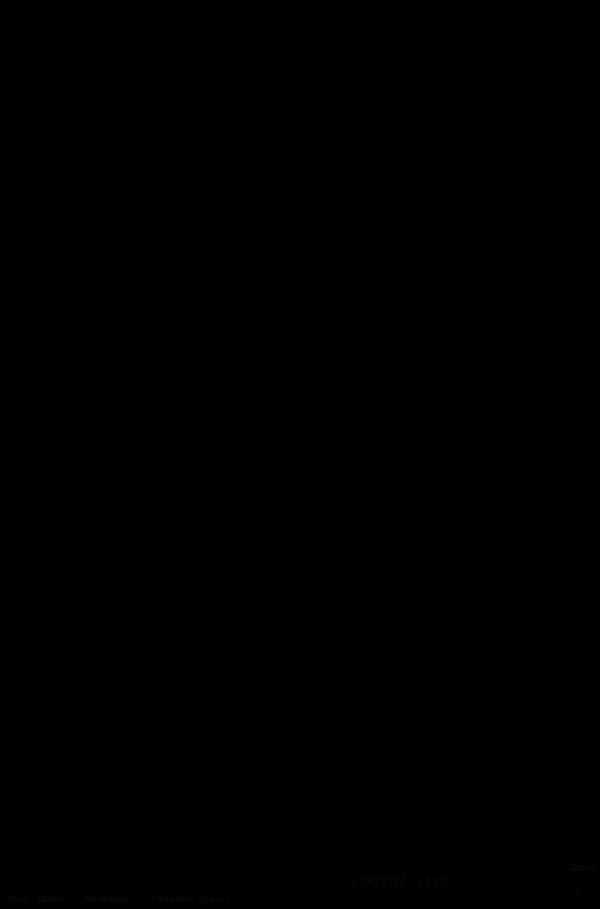
ΠΠ²Π΅Π΄Π΅Π½ΠΈΠ΅
1. ΠΠΎΠΌΠ΅Π½ΠΊΠ»Π°ΡΡΡΠ° ΠΈ ΠΏΡΠΈΠΌΠ΅Π½Π΅Π½ΠΈΠ΅ 5
2. Π’Π΅Ρ Π½ΠΎΠ»ΠΎΠ³ΠΈΡ ΠΏΡΠΎΠΈΠ·Π²ΠΎΠ΄ΡΡΠ²Π° 7
2.1 ΠΡΠ±ΠΎΡ ΡΠΏΠΎΡΠΎΠ±Π° ΠΈ ΡΠ΅Ρ Π½ΠΎΠ»ΠΎΠ³ΠΈΡΠ΅ΡΠΊΠΎΠΉ ΡΡ Π΅ΠΌΡ ΠΏΡΠΎΠΈΠ·Π²ΠΎΠ΄ΡΡΠ²Π° 7
2.2 ΠΠΏΠΈΡΠ°Π½ΠΈΠ΅ ΡΠ΅Ρ Π½ΠΎΠ»ΠΎΠ³ΠΈΡΠ΅ΡΠΊΠΎΠ³ΠΎ ΠΏΡΠΎΡΠ΅ΡΡΠ° 9
2.3 Π’Π΅Ρ Π½ΠΎΠ»ΠΎΠ³ΠΈΡΠ΅ΡΠΊΠ°Ρ ΡΡ Π΅ΠΌΠ° ΠΏΡΠΎΠΈΠ·Π²ΠΎΠ΄ΡΡΠ²Π° ΡΠ»Π°ΠΊΠΎΠΏΠΎΡΡΠ»Π°Π½Π΄ΡΠ΅ΠΌΠ΅Π½ΡΠ° 10
3. Π€ΠΎΠ½Π΄Ρ ΡΠ°Π±ΠΎΡΠ΅Π³ΠΎ Π²ΡΠ΅ΠΌΠ΅Π½ΠΈ 11
4. ΠΠ°ΡΠ΅ΡΠΈΠ°Π»ΡΠ½ΡΠΉ Π±Π°Π»Π°Π½Ρ 11
5. ΠΡΠ±ΠΎΡ ΡΠ΅Ρ Π½ΠΎΠ»ΠΎΠ³ΠΈΡΠ΅ΡΠΊΠΎΠ³ΠΎ ΠΎΠ±ΠΎΡΡΠ΄ΠΎΠ²Π°Π½ΠΈΡ 14
6. Π Π°ΡΡΠ΅Ρ ΡΠ°ΡΡ ΠΎΠ΄Π° ΡΠ½Π΅ΡΠ³ΠΎΡΠ΅ΡΡΡΡΠΎΠ² ΠΎΠ±ΠΎΡΡΠ΄ΠΎΠ²Π°Π½ΠΈΡ 19
7. ΠΠΎΠ½ΡΡΠΎΠ»Ρ ΠΊΠ°ΡΠ΅ΡΡΠ²Π° 20
8. ΠΡ ΡΠ°Π½Π° ΡΡΡΠ΄Π° 22
9. ΠΡΠ°Π²ΠΈΠ»Π° ΠΏΡΠΈΠ΅ΠΌΠΊΠΈ 27
10. ΠΡ ΡΠ°Π½Π° ΠΎΠΊΡΡΠΆΠ°ΡΡΠ΅ΠΉ ΡΡΠ΅Π΄Ρ 32
11. ΠΠΈΡΠ΅ΡΠ°ΡΡΡΠ° 34
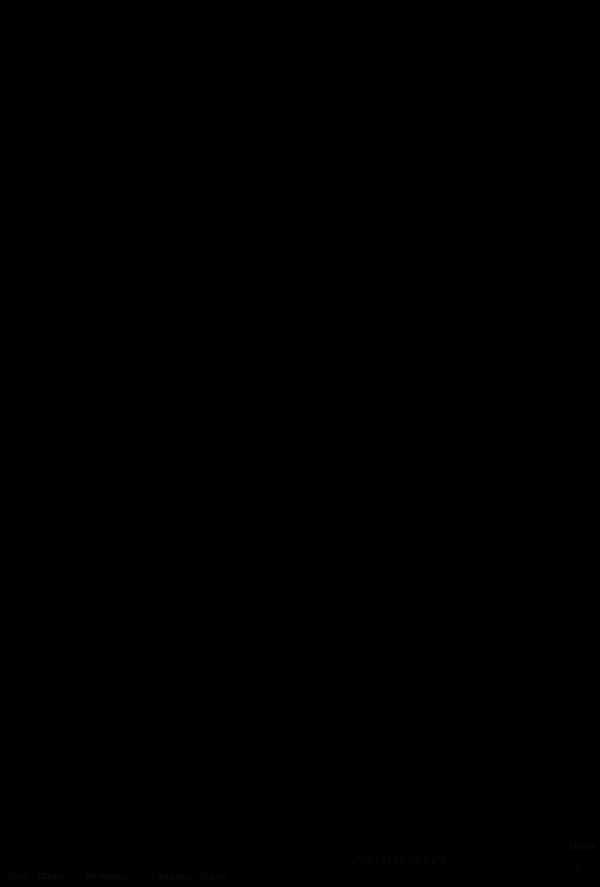
Π¦Π΅ΠΌΠ΅Π½Ρ β ΠΎΠ΄ΠΈΠ½ ΠΈΠ· Π²Π°ΠΆΠ½Π΅ΠΉΡΠΈΡ ΡΡΡΠΎΠΈΡΠ΅Π»ΡΠ½ΡΡ ΠΌΠ°ΡΠ΅ΡΠΈΠ°Π»ΠΎΠ², ΠΏΡΠ΅Π΄Π½Π°Π·Π½Π°ΡΠ΅Π½Π½ΡΡ Π΄Π»Ρ Π±Π΅ΡΠΎΠ½ΠΎΠ² ΠΈ ΡΡΡΠΎΠΈΡΠ΅Π»ΡΠ½ΡΡ ΡΠ°ΡΡΠ²ΠΎΡΠΎΠ², ΡΠΊΡΠ΅ΠΏΠ»Π΅Π½ΠΈΠ΅ ΠΎΡΠ΄Π΅Π»ΡΠ½ΡΡ ΡΠ»Π΅ΠΌΠ΅Π½ΡΠΎΠ² (Π΄Π΅ΡΠ°Π»Π΅ΠΉ) ΡΡΡΠΎΠΈΡΠ΅Π»ΡΠ½ΡΡ ΠΊΠΎΠ½ΡΡΡΡΠΊΡΠΈΠΉ, Π³ΠΈΠ΄ΡΠΎΠΈΠ·ΠΎΠ»ΡΡΠΈΠΉ ΠΈ Π΄Ρ. Π¦Π΅ΠΌΠ΅Π½Ρ ΠΏΡΠ΅Π΄ΡΡΠ°Π²Π»ΡΠ΅Ρ ΡΠΎΠ±ΠΎΠΉ Π³ΠΈΠ΄ΡΠ°Π²Π»ΠΈΡΠ΅ΡΠΊΠΈΠΉ Π²ΡΠΆΡΡΠΈΠΉ ΠΌΠ°ΡΠ΅ΡΠΈΠ°Π», ΠΊΠΎΡΠΎΡΡΠΉ ΠΏΠΎΡΠ»Π΅ ΡΠΌΠ΅ΡΠ΅Π½ΠΈΡ Ρ Π²ΠΎΠ΄ΠΎΠΉ ΠΈ ΠΏΡΠ΅Π΄Π²Π°ΡΠΈΡΠ΅Π»ΡΠ½ΠΎΠ³ΠΎ Π·Π°ΡΠ²Π΅ΡΠ΄Π΅Π²Π°Π½ΠΈΡ Π½Π° Π²ΠΎΠ·Π΄ΡΡ Π΅ ΠΏΡΠΎΠ΄ΠΎΠ»ΠΆΠ°Π΅Ρ ΡΠΎΡ ΡΠ°Π½ΡΡΡ ΠΈ Π½Π°ΡΠ°ΡΠΈΠ²Π°ΡΡ ΠΏΡΠΎΡΠ½ΠΎΡΡΡ Π² Π²ΠΎΠ΄Π΅.
ΠΡΠΎΠΈΠ·Π²ΠΎΠ΄ΡΡΠ²ΠΎ ΡΠ΅ΠΌΠ΅Π½ΡΠ° ΠΎΠ±ΡΡΠ»ΠΎΠ²Π»Π΅Π½ΠΎ Π½Π΅ΠΎΠ±Ρ ΠΎΠ΄ΠΈΠΌΠΎΡΡΡΡ Π΅Π³ΠΎ ΠΏΡΠΎΠΈΠ·Π²ΠΎΠ΄ΡΡΠ²Π° Π΄Π»Ρ ΠΏΡΠΈΠΌΠ΅Π½Π΅Π½ΠΈΡ Π² Π³Π»Π°Π²Π½ΡΠΌ ΠΎΠ±ΡΠ°Π·ΠΎΠΌ Π² ΡΡΡΠΎΠΈΡΠ΅Π»ΡΡΡΠ²Π΅. Π‘ΡΡΠΎΠΈΡΠ΅Π»ΡΡΡΠ²ΠΎ ΠΆΠΈΠ»ΡΡ Π½Π° ΠΎΡΠ½ΠΎΠ²Π΅ ΡΠ΅ΠΌΠ΅Π½ΡΠ° ΠΏΠΎΠ·Π²ΠΎΠ»ΡΠ΅Ρ ΠΏΠΎΠ»ΡΡΠΈΡΡ ΠΎΠ±ΡΠ΅ΠΊΡΡ Ρ Π½ΠΈΠ·ΠΊΠΎΠΉ ΡΠ΅ΠΏΠ»ΠΎΠΏΡΠΎΠ²ΠΎΠ΄Π½ΠΎΡΡΡΡ ΠΈ Π²ΡΡΠΎΠΊΠΎΠΉ ΠΌΠΎΡΠΎΠ·ΠΎΡΡΠΎΠΉΠΊΠΎΡΡΡΡ.
Π’Π΅Ρ Π½ΠΎΠ»ΠΎΠ³ΠΈΡ ΡΠ΅ΠΌΠ΅Π½ΡΠ½ΠΎΠ΅ ΠΏΡΠΎΠΈΠ·Π²ΠΎΠ΄ΡΡΠ²ΠΎ ΠΏΠΎΠ·Π²ΠΎΠ»ΡΠ΅Ρ ΠΈΡΠΏΠΎΠ»ΡΠ·ΠΎΠ²Π°ΡΡ Π² Π½ΡΠΌ ΠΎΡΡ ΠΎΠ΄Ρ Π΄ΠΎΠ±ΡΠ²Π°ΡΡΠ΅ΠΉ, ΠΌΠ΅ΡΠ°Π»Π»ΡΡΠ³ΠΈΡΠ΅ΡΠΊΠΎΠΉ ΠΎΡΡΠ°ΡΠ»Π΅ΠΉ, Π° ΡΠ°ΠΊΠΆΠ΅ ΠΏΠΎΠ±ΠΎΡΠ½ΡΠ΅ ΠΏΡΠΎΠ΄ΡΠΊΡΡ ΡΡΠΈΡ ΠΏΡΠΎΠΈΠ·Π²ΠΎΠ΄ΡΡΠ². ΠΠΈΠ±ΠΊΠ°Ρ ΡΠ΅Ρ Π½ΠΎΠ»ΠΎΠ³ΠΈΡ ΠΏΠΎΠ·Π²ΠΎΠ»ΡΠ΅Ρ ΠΎΡΡΡΠ΅ΡΡΠ²Π»ΡΡΡ ΠΊΠΎΠΌΠ±ΠΈΠ½ΠΈΡΠΎΠ²Π°Π½ΠΈΠ΅ ΠΏΡΠΎΠΈΠ·Π²ΠΎΠ΄ΡΡΠ²Π° ΡΠ΅ΠΌΠ΅Π½ΡΠ° Ρ ΠΏΡΠΎΠΈΠ·Π²ΠΎΠ΄ΡΡΠ²ΠΎΠΌ ΠΌΠ΅ΡΠ°Π»Π»ΠΎΠ².
Π‘ΡΡΠ΅ΡΡΠ²ΡΠ΅Ρ ΠΌΠ½ΠΎΠ³ΠΎ ΠΏΠΎΠ΄Π²ΠΈΠ΄ΠΎΠ² ΡΠ΅ΠΌΠ΅Π½ΡΠ°. ΠΠ½ΠΈ ΠΎΡΠ»ΠΈΡΠ°ΡΡΡΡ Π΄ΡΡΠ³ ΠΎΡ Π΄ΡΡΠ³Π° ΠΊΠΎΠ½Π΅ΡΠ½ΡΠΌΠΈ ΡΠ²ΠΎΠΉΡΡΠ²Π°ΠΌΠΈ, ΡΡΠ»ΠΎΠ²ΠΈΡΠΌΠΈ ΠΏΡΠΎΠΈΠ·Π²ΠΎΠ΄ΡΡΠ²Π° ΠΈ Π½Π°Π»ΠΈΡΠΈΠ΅ΠΌ Π² Π½ΠΈΡ ΡΠ°Π·Π»ΠΈΡΠ½ΡΡ Π²ΠΈΠ΄ΠΎΠ² Π΄ΠΎΠ±Π°Π²ΠΎΠΊ.
Π¨Π»Π°ΠΊΠΎΠΏΠΎΡΡΠ»Π°Π½Π΄ΡΠ΅ΠΌΠ΅Π½Ρ β Π³ΠΈΠ΄ΡΠ°Π²Π»ΠΈΡΠ΅ΡΠΊΠΎΠ΅ Π²ΡΠΆΡΡΠ΅Π΅ Π²Π΅ΡΠ΅ΡΡΠ²ΠΎ, ΠΏΠΎΠ»ΡΡΠ°Π΅ΠΌΠΎΠ΅ ΠΏΡΡΠ΅ΠΌ ΡΠΎΠ½ΠΊΠΎΠ³ΠΎ ΠΈΠ·ΠΌΠ΅Π»ΡΡΠ΅Π½ΠΈΡ ΠΏΠΎΡΡΠ»Π°Π½Π΄ΡΠ΅ΠΌΠ΅Π½ΡΠ½ΠΎΠ³ΠΎ ΠΊΠ»ΠΈΠ½ΠΊΠ΅ΡΠ° ΡΠΎΠ²ΠΌΠ΅ΡΡΠ½ΠΎ Ρ Π³ΡΠ°Π½ΡΠ»ΠΈΡΠΎΠ²Π°Π½Π½ΡΠΌ Π΄ΠΎΠΌΠ΅Π½Π½ΡΠΌ ΠΈ ΡΠ»Π΅ΠΊΡΡΠΎΡΠ΅ΡΠΌΠΎΡΠΎΡΡΠΎΡΠ½ΡΠΌ ΡΠ»Π°ΠΊΠΎΠΌ, Π° ΡΠ°ΠΊΠΆΠ΅ Ρ Π΄Π²ΡΠ²ΠΎΠ΄Π½ΡΠΌ Π³ΠΈΠΏΡΠΎΠΌ. ΠΠ»Ρ ΠΏΠΎΠ»ΡΡΠ΅Π½ΠΈΡ Π±ΡΡΡΡΠΎΡΠ²Π΅ΡΠ΄Π΅ΡΡΠ΅Π³ΠΎ ΡΠ»Π°ΠΊΠΎΠΏΠΎΡΡΠ»Π°Π½Π΄ΡΠ΅ΠΌΠ΅Π½ΡΠ° ΠΏΠΎΡΠΎΡΠΎΠΊ ΠΏΠΎΡΡΠ»Π°Π½Π΄ΡΠ΅ΠΌΠ΅Π½ΡΠ° ΠΈΠ½ΠΎΠ³Π΄Π° ΡΠ°Π·ΠΌΠ°Π»ΡΠ²Π°ΡΡ Ρ Π³ΡΠ°Π½ΡΠ»ΠΈΡΠΎΠ²Π°Π½Π½ΡΠΌ ΡΠ»Π°ΠΊΠΎΠΌ. Π¨Π»Π°ΠΊΠ° Π² ΡΠ»Π°ΠΊΠΎΠΏΠΎΡΡΠ»Π°Π½Π΄ΡΠ΅ΠΌΠ΅Π½ΡΠ΅ Π΄ΠΎΠ»ΠΆΠ½ΠΎ Π±ΡΡΡ Π½Π΅ ΠΌΠ΅Π½Π΅Π΅ 21% ΠΈ Π½Π΅ Π±ΠΎΠ»Π΅Π΅ 80% ΠΏΠΎ ΠΌΠ°ΡΡΠ΅ (ΠΠΠ‘Π’ 10178 -85). ΠΠΈΠΏΡ Π²Π²ΠΎΠ΄ΡΡ Π² ΡΠ»Π°ΠΊΠΎΠΏΠΎΡΡΠ»Π°Π½Π΄ΡΠ΅ΠΌΠ΅Π½Ρ Π΄Π»Ρ ΡΠ΅Π³ΡΠ»ΠΈΡΠΎΠ²Π°Π½ΠΈΡ ΡΡΠΎΠΊΠΎΠ² ΡΡ Π²Π°ΡΡΠ²Π°Π½ΠΈΡ, Π° ΡΠ°ΠΊΠΆΠ΅ Π² ΠΊΠ°ΡΠ΅ΡΡΠ²Π΅ Π°ΠΊΡΠΈΠ²ΠΈΠ·Π°ΡΠΎΡΠ° ΡΠ²Π΅ΡΠ΄Π΅Π½ΠΈΡ ΡΠ»Π°ΠΊΠ°.
ΠΠΎ ΡΠ²ΠΎΠΈΠΌ ΡΠΈΠ·ΠΈΠΊΠΎβΠΌΠ΅Ρ Π°Π½ΠΈΡΠ΅ΡΠΊΠΈΠΌ ΡΠ²ΠΎΠΉΡΡΠ²Π°ΠΌ ΡΠ»Π°ΠΊΠΎΠΏΠΎΡΡΠ»Π°Π½Π΄ΡΠ΅ΠΌΠ΅Π½Ρ Π±Π»ΠΈΠ·ΠΎΠΊ ΠΊ ΠΎΠ±ΡΡΠ½ΠΎΠΌΡ ΠΏΠΎΡΡΠ»Π°Π½Π΄ΡΠ΅ΠΌΠ΅Π½ΡΡ, Π½ΠΎ Π²ΡΠ³ΠΎΠ΄Π½ΠΎ ΠΎΡΠ»ΠΈΡΠ°Π΅ΡΡΡ ΠΎΡ Π½Π΅Π³ΠΎ Π±ΠΎΠ»Π΅Π΅ Π½ΠΈΠ·ΠΊΠΎΠΉ ΡΡΠΎΠΈΠΌΠΎΡΡΡΡ. ΠΡΠΈ ΠΏΡΠΎΡΠΈΡ ΡΠ°Π²Π½ΡΡ ΡΡΠ»ΠΎΠ²ΠΈΡΡ ΡΡΠΎΠΈΠΌΠΎΡΡΡ Π΅Π³ΠΎ Π½Π° 10 β 15% Π½ΠΈΠΆΠ΅ ΡΡΠΎΠΈΠΌΠΎΡΡΠΈ ΠΏΠΎΡΡΠ»Π°Π½Π΄ΡΠ΅ΠΌΠ΅Π½ΡΠ°.
Π‘Ρ Π΅ΠΌΠ°ΡΠΈΡΠ΅ΡΠΊΠΈ ΡΠ²Π΅ΡΠ΄Π΅Π½ΠΈΠ΅ ΡΠ»Π°ΠΊΠΎΠΏΠΎΡΡΠ»Π°Π½Π΄ΡΠ΅ΠΌΠ΅Π½ΡΠ° ΠΌΠΎΠΆΠ½ΠΎ ΡΠ΅Π±Π΅ ΠΏΡΠ΅Π΄ΡΡΠ°Π²ΠΈΡΡ ΠΊΠ°ΠΊ ΡΠ΅Π·ΡΠ»ΡΡΠ°Ρ ΡΡΠ΄Π° ΠΏΡΠΎΡΠ΅ΡΡΠΎΠ², ΠΏΡΠΎΡΠ΅ΠΊΠ°ΡΡΠΈΡ ΠΎΠ΄Π½ΠΎΠ²ΡΠ΅ΠΌΠ΅Π½Π½ΠΎ, Π° ΠΈΠΌΠ΅Π½Π½ΠΎ:
Π³ΠΈΠ΄ΡΠΎΠ»ΠΈΠ·Π° ΠΈ Π³ΠΈΠ΄ΡΠ°ΡΠ°ΡΠΈΠΈ ΠΊΠ»ΠΈΠ½ΠΊΠ΅ΡΠ½ΡΡ ΠΌΠΈΠ½Π΅ΡΠ°Π»ΠΎΠ²;
Π²Π·Π°ΠΈΠΌΠΎΠ΄Π΅ΠΉΡΡΠ²ΠΈΠ΅ Π³ΠΈΠ΄ΡΠ°ΡΠ° ΠΎΠΊΠΈΡΠΈ ΠΊΠ°Π»ΡΡΠΈΡ Ρ Π³Π»ΠΈΠ½ΠΎΠ·Π΅ΠΌΠΎΠΌ ΠΈ ΠΊΡΠ΅ΠΌΠ½Π΅Π·Π΅ΠΌΠΎΠΌ, Π½Π°Ρ ΠΎΠ΄ΡΡΠΈΠΌΠΈΡΡ Π² ΡΠ»Π°ΠΊΠΎΠ²ΠΎΠΌ ΡΡΠ΅ΠΊΠ»Π΅, Ρ ΠΎΠ±ΡΠ°Π·ΠΎΠ²Π°Π½ΠΈΠ΅ΠΌ Π³ΠΈΠ΄ΡΠΎΡΠΈΠ»ΠΈΠΊΠ°ΡΠΎΠ², Π³ΠΈΠ΄ΡΠΎΠ°Π»ΡΠΌΠΈΠ½Π°ΡΠΎΠ², Π° ΡΠ°ΠΊΠΆΠ΅ Π³ΠΈΠ΄ΡΠΎΡΠΈΠ»ΠΈΠΊΠΎΠ°Π»ΡΠΌΠΈΠ½Π°ΡΠΎΠ² ΠΊΠ°Π»ΡΡΠΈΡ;
Π²Π·Π°ΠΈΠΌΠΎΠ΄Π΅ΠΉΡΡΠ²ΠΈΠ΅ ΡΡΠ΅Ρ ΠΊΠ°Π»ΡΡΠΈΠ΅Π²ΠΎΠ³ΠΎ Π³ΠΈΠ΄ΡΠΎΠ°Π»ΡΠΌΠΈΠ½Π°ΡΠ° ΠΊΠ°Π»ΡΡΠΈΡ ΠΊΠ»ΠΈΠ½ΠΊΠ΅ΡΠ° Ρ ΡΡΠ»ΡΡΠ°ΡΠΎΠΌ ΠΊΠ°Π»ΡΡΠΈΡ Ρ ΠΎΠ±ΡΠ°Π·ΠΎΠ²Π°Π½ΠΈΠ΅ΠΌ Π³ΠΈΠ΄ΡΠΎΡΡΠ»ΡΡΠΎΠ°Π»ΡΠΌΠΈΠ½Π°ΡΠ° ΠΊΠ°Π»ΡΡΠΈΡ.
Π¨Π»Π°ΠΊΠΎΠΏΠΎΡΡΠ»Π°Π½Π΄ΡΠ΅ΠΌΠ΅Π½Ρ ΡΠ²Π΅ΡΠ΄Π΅Π΅Ρ Π½Π΅ΡΠΊΠΎΠ»ΡΠΊΠΎ ΠΌΠ΅Π΄Π»Π΅Π½Π½Π΅Π΅, ΡΠ΅ΠΌ ΠΏΠΎΡΡΠ»Π°Π½Π΄ΡΠ΅ΠΌΠ΅Π½Ρ, Π² ΠΎΡΠΎΠ±Π΅Π½Π½ΠΎΡΡΠΈ ΠΏΡΠΈ ΠΏΠΎΠ½ΠΈΠΆΠ΅Π½Π½ΡΡ ΠΏΠΎΠ»ΠΎΠΆΠΈΡΠ΅Π»ΡΠ½ΡΡ ΡΠ΅ΠΌΠΏΠ΅ΡΠ°ΡΡΡΠ°Ρ . ΠΡΠΎ ΠΎΠ±ΡΡΡΠ½ΡΠ΅ΡΡΡ Π·Π½Π°ΡΠΈΡΠ΅Π»ΡΠ½ΡΠΌ ΡΠΎΠ΄Π΅ΡΠΆΠ°Π½ΠΈΠ΅ΠΌ ΡΠ»Π°ΠΊΠ°. ΠΠ΄Π½Π°ΠΊΠΎ ΠΏΡΠΈ ΡΠΎΠ½ΡΠ°ΠΉΡΠ΅ΠΌ ΠΏΠΎΠΌΠΎΠ»Π΅, Π² ΠΎΡΠΎΠ±Π΅Π½Π½ΠΎΡΡΠΈ Π΄Π²ΡΡ ΡΡΡΠΏΠ΅Π½ΡΠ°ΡΠΎΠΌ, ΠΈ ΡΠΎΠ΄Π΅ΡΠΆΠ°Π½ΠΈΠΈ ΡΠ»Π°ΠΊΠ° ΠΎΠΊΠΎΠ»ΠΎ 30β35% ΡΠΊΠΎΡΠΎΡΡΡ ΡΠ²Π΅ΡΠ΄Π΅Π½ΠΈΡ ΡΠ»Π°ΠΊΠΎΠΏΠΎΡΡΠ»Π°Π½Π΄ΡΠ΅ΠΌΠ΅Π½ΡΠ° ΡΠ°ΠΊΠ°Ρ ΠΆΠ΅.
B Π·Π°Π²ΠΈΡΠΈΠΌΠΎΡΡΠΈ ΠΎΡ ΠΏΡΠΎΡΠ½ΠΎΡΡΠΈ Π½Π° ΡΠΆΠ°ΡΠΈΠ΅ ΡΠ»Π°ΠΊΠΎΠΏΠΎΡΡΠ»Π°Π½Π΄ΡΠ΅ΠΌΠ΅Π½Ρ Π²ΡΠΏΡΡΠΊΠ°ΡΡ ΡΠ΅ΡΡΡΠ΅Ρ ΠΌΠ°ΡΠΎΠΊ: 300, 400, 500 ΠΈ 600.
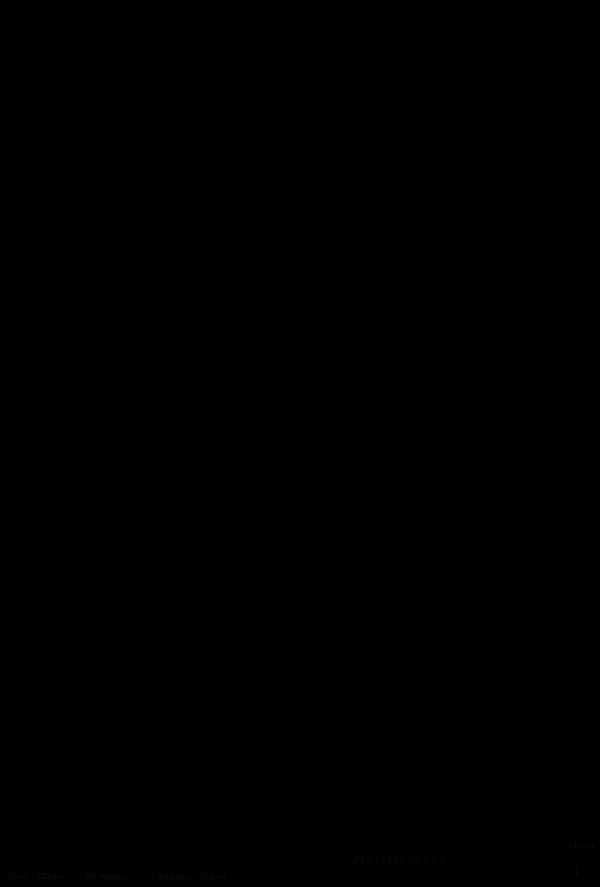
ΠΠΎ ΠΌΠΎΡΠΎΠ·ΠΎΡΡΠΎΠΉΠΊΠΎΡΡΠΈ ΡΠ»Π°ΠΊΠΎΠΏΠΎΡΡΠ»Π°Π½Π΄ΡΠ΅ΠΌΠ΅Π½Ρ ΡΡΡΡΠΏΠ°Π΅Ρ ΠΏΠΎΡΡΠ»Π°Π½Π΄ΡΠ΅ΠΌΠ΅Π½ΡΡ Π² ΡΠ°Π·Π»ΠΈΡΠ½ΠΎΠΉ ΡΡΠ΅ΠΏΠ΅Π½ΠΈ Π² Π·Π°Π²ΠΈΡΠΈΠΌΠΎΡΡΠΈ ΠΎΡ ΡΠΎΠ΄Π΅ΡΠΆΠ°Π½ΠΈΡ Π² Π½Π΅ΠΌ ΡΠ»Π°ΠΊΠ° ΠΈ Ρ ΠΈΠΌΠΈΠΊΠΎ-ΠΌΠΈΠ½Π΅ΡΠ°Π»ΠΎΠ³ΠΈΡΠ΅ΡΠΊΠΎΠ³ΠΎ ΡΠΎΡΡΠ°Π²Π° ΠΈΡΡ ΠΎΠ΄Π½ΠΎΠ³ΠΎ ΠΊΠ»ΠΈΠ½ΠΊΠ΅ΡΠ°.
Π¨Π»Π°ΠΊΠΎΠΏΠΎΡΡΠ»Π°Π½Π΄ΡΠ΅ΠΌΠ΅Π½Ρ Ρ Π°ΡΠ°ΠΊΡΠ΅ΡΠΈΠ·ΡΠ΅ΡΡΡ ΠΏΠΎΠ½ΠΈΠΆΠ΅Π½Π½ΡΠΌ ΠΈΠ»ΠΈ ΡΠΌΠ΅ΡΠ΅Π½Π½ΡΠΌ ΡΠ΅ΠΏΠ»ΠΎΠ²ΡΠ΄Π΅Π»Π΅Π½ΠΈΠ΅ΠΌ ΠΏΡΠΈ ΡΠ²Π΅ΡΠ΄Π΅Π½ΠΈΠΈ, Π° ΡΠ°ΠΊΠΆΠ΅ ΠΌΠ΅Π½ΡΡΠΈΠΌΠΈ ΠΎΠ±ΡΠ΅ΠΌΠ½ΡΠΌΠΈ Π΄Π΅ΡΠΎΡΠΌΠ°ΡΠΈΡΠΌΠΈ Π² ΡΠ°ΡΡΠ²ΠΎΡΠ΅ ΠΈ Π±Π΅ΡΠΎΠ½Π΅ β ΡΡΠ°Π΄ΠΊΠΎΠΉ (Π½Π° Π²ΠΎΠ·Π΄ΡΡ Π΅) ΠΈ Π½Π°Π±ΡΡ Π°Π½ΠΈΠ΅ΠΌ (Π² Π²ΠΎΠ΄Π΅).
Π‘ΡΡΠΎΠΈΡΠ΅Π»ΡΠ½ΠΎ-ΡΠ΅Ρ Π½ΠΈΡΠ΅ΡΠΊΠΈΠ΅ ΡΠ²ΠΎΠΉΡΡΠ²Π° ΡΠ»Π°ΠΊΠΎΠΏΠΎΡΡΠ»Π°Π½Π΄ΡΠ΅ΠΌΠ΅Π½ΡΠ° ΠΎΠ±ΡΡΠ»ΠΎΠ²Π»ΠΈΠ²Π°ΡΡ ΠΈ ΠΎΠ±Π»Π°ΡΡΠΈ Π΅Π³ΠΎ ΠΏΡΠ°ΠΊΡΠΈΡΠ΅ΡΠΊΠΎΠ³ΠΎ ΠΏΡΠΈΠΌΠ΅Π½Π΅Π½ΠΈΡ β ΡΠ΅ ΠΆΠ΅, ΡΡΠΎ ΠΈ ΠΏΠΎΡΡΠ»Π°Π½Π΄ΡΠ΅ΠΌΠ΅Π½ΡΠ° Π°Π½Π°Π»ΠΎΠ³ΠΈΡΠ½ΡΡ ΠΌΠ°ΡΠΎΠΊ. ΠΠ³ΠΎ ΡΠ΅Π»Π΅ΡΠΎΠΎΠ±ΡΠ°Π·Π½ΠΎ ΠΈΡΠΏΠΎΠ»ΡΠ·ΠΎΠ²Π°ΡΡ Π΄Π»Ρ ΠΏΡΠΎΠΈΠ·Π²ΠΎΠ΄ΡΡΠ²Π° ΠΌΠΎΠ½ΠΎΠ»ΠΈΡΠ½ΡΡ ΠΈ ΡΠ±ΠΎΡΠ½ΡΡ ΠΆΠ΅Π»Π΅Π·ΠΎΠ±Π΅ΡΠΎΠ½Π½ΡΡ ΠΊΠΎΠ½ΡΡΡΡΠΊΡΠΈΠΉ ΠΈ Π΄Π΅ΡΠ°Π»Π΅ΠΉ, Π² ΠΎΡΠΎΠ±Π΅Π½Π½ΠΎΡΡΠΈ Ρ ΠΏΡΠΈΠΌΠ΅Π½Π΅Π½ΠΈΠ΅ΠΌ ΡΠ΅ΠΏΠ»ΠΎΠ²Π»Π°ΠΆΠ½ΠΎΡΡΠ½ΠΎΠΉ ΠΎΠ±ΡΠ°Π±ΠΎΡΠΊΠΈ, Π° ΡΠ°ΠΊΠΆΠ΅ Π΄Π»Ρ ΠΈΠ·Π³ΠΎΡΠΎΠ²Π»Π΅Π½ΠΈΡ ΡΡΡΠΎΠΈΡΠ΅Π»ΡΠ½ΡΡ ΡΠ°ΡΡΠ²ΠΎΡΠΎΠ². Π¨Π»Π°ΠΊΠΎΠΏΠΎΡΡΠ»Π°Π½Π΄ΡΠ΅ΠΌΠ΅Π½Ρ ΠΏΡΠ΅Π΄Π½Π°Π·Π½Π°ΡΠ΅Π½ Π² ΠΎΡΠ½ΠΎΠ²Π½ΠΎΠΌ Π΄Π»Ρ Π±Π΅ΡΠΎΠ½Π½ΡΡ ΠΈ ΠΆΠ΅Π»Π΅Π·ΠΎΠ±Π΅ΡΠΎΠ½Π½ΡΡ Π½Π°Π·Π΅ΠΌΠ½ΡΡ , Π° ΡΠ°ΠΊΠΆΠ΅ ΠΏΠΎΠ΄Π·Π΅ΠΌΠ½ΡΡ ΠΈ ΠΏΠΎΠ΄Π²ΠΎΠ΄Π½ΡΡ ΠΊΠΎΠ½ΡΡΡΡΠΊΡΠΈΠΉ, ΠΏΠΎΠ΄Π²Π΅ΡΠ³Π°ΡΡΠΈΡ ΡΡ Π²ΠΎΠ·Π΄Π΅ΠΉΡΡΠ²ΠΈΡ ΠΏΡΠ΅ΡΠ½ΡΡ , Π° ΡΠ°ΠΊΠΆΠ΅ ΠΌΠΈΠ½Π΅ΡΠ°Π»ΠΈΠ·ΠΈΡΠΎΠ²Π°Π½Π½ΡΡ Π²ΠΎΠ΄ Ρ ΡΡΠ΅ΡΠΎΠΌ Π½ΠΎΡΠΌ Π°Π³ΡΠ΅ΡΡΠΈΠ²Π½ΠΎΡΡΠΈ Π²ΠΎΠ΄Ρ β ΡΡΠ΅Π΄Ρ.
ΠΡΠ»Π΅Π΄ΡΡΠ²ΠΈΠ΅ ΠΏΠΎΠ½ΠΈΠΆΠ΅Π½Π½ΠΎΠ³ΠΎ ΡΠ΅ΠΏΠ»ΠΎΠ²ΡΠ΄Π΅Π»Π΅Π½ΠΈΡ ΠΏΡΠΈ ΡΠ²Π΅ΡΠ΄Π΅Π½ΠΈΠΈ ΠΈ ΠΌΠ°Π»ΠΎΠΉ ΡΡΠ°Π΄ΠΊΠΈ ΡΠ»Π°ΠΊΠΎΠΏΠΎΡΡΠ»Π°Π½Π΄ΡΠ΅ΠΌΠ΅Π½ΡΠ° Π΅Π³ΠΎ ΠΌΠΎΠΆΠ½ΠΎ Π²Π΅ΡΡΠΌΠ° ΡΡΡΠ΅ΠΊΡΠΈΠ²Π½ΠΎ ΠΏΡΠΈΠΌΠ΅Π½ΡΡΡ Π΄Π»Ρ Π²Π½ΡΡΡΠΈΠΌΠ°ΡΡΠΈΠ²Π½ΠΎΠ³ΠΎ Π±Π΅ΡΠΎΠ½Π° Π³ΠΈΠ΄ΡΠΎΡΠ΅Ρ Π½ΠΈΡΠ΅ΡΠΊΠΈΡ ΡΠΎΠΎΡΡΠΆΠ΅Π½ΠΈΠΉ. Π ΡΠΈΠ»Ρ ΠΏΠΎΠ½ΠΈΠΆΠ΅Π½Π½ΠΎΠΉ ΠΌΠΎΡΠΎΠ·ΠΎΡΡΠΎΠΉΠΊΠΎΡΡΠΈ ΡΠ»Π°ΠΊΠΎΠΏΠΎΡΡΠ»Π°Π½Π΄ΡΠ΅ΠΌΠ΅Π½ΡΠ° Π΅Π³ΠΎ Π½Π΅Π»ΡΠ·Ρ ΠΏΡΠΈΠΌΠ΅Π½ΡΡΡ Π΄Π»Ρ Π±Π΅ΡΠΎΠ½Π½ΡΡ ΠΈ ΠΆΠ΅Π»Π΅Π·ΠΎΠ±Π΅ΡΠΎΠ½Π½ΡΡ ΠΊΠΎΠ½ΡΡΡΡΠΊΡΠΈΠΉ, ΠΏΠΎΠ΄Π²Π΅ΡΠ³Π°ΡΡΠΈΡ ΡΡ ΡΠΈΡΡΠ΅ΠΌΠ°ΡΠΈΡΠ΅ΡΠΊΠΎΠΌΡ ΠΏΠΎΠΏΠ΅ΡΠ΅ΠΌΠ΅Π½Π½ΠΎΠΌΡ Π·Π°ΠΌΠΎΡΠ°ΠΆΠΈΠ²Π°Π½ΠΈΡ ΠΈ ΠΎΡΡΠ°ΠΈΠ²Π°Π½ΠΈΡ ΠΈΠ»ΠΈ ΡΠ²Π»Π°ΠΆΠ½Π΅Π½ΠΈΡ ΠΈ Π²ΡΡΡΡ Π°Π½ΠΈΡ.
ΠΠ»Ρ ΠΎΡΡΡΠ΅ΡΡΠ²Π»Π΅Π½ΠΈΡ Π³ΡΠ°Π½Π΄ΠΈΠΎΠ·Π½ΡΡ ΠΎΠ±ΡΠ΅ΠΌΠΎΠ² ΡΠ°Π±ΠΎΡ ΠΏΠΎ ΠΏΡΠΎΠΌΡΡΠ»Π΅Π½Π½ΠΎΠΌΡ, ΠΆΠΈΠ»ΠΈΡΠ½ΠΎ-Π³ΡΠ°ΠΆΠ΄Π°Π½ΡΠΊΠΎΠΌΡ ΠΈ ΡΠ΅Π»ΡΡΠΊΠΎΡ ΠΎΠ·ΡΠΉΡΡΠ²Π΅Π½Π½ΠΎΠΌΡ ΡΡΡΠΎΠΈΡΠ΅Π»ΡΡΡΠ²Ρ, ΡΡΠ΅Π±ΡΠ΅ΡΡΡ Π±ΠΎΠ»ΡΡΠΎΠ΅ ΠΊΠΎΠ»ΠΈΡΠ΅ΡΡΠ²ΠΎ ΡΠ°Π·Π½ΠΎΠΎΠ±ΡΠ°Π·Π½ΡΡ ΡΡΡΠΎΠΈΡΠ΅Π»ΡΠ½ΡΡ ΠΌΠ°ΡΠ΅ΡΠΈΠ°Π»ΠΎΠ², Π² ΡΠΎΠΌ ΡΠΈΡΠ»Π΅ Π²ΡΠΆΡΡΠΈΡ Π²Π΅ΡΠ΅ΡΡΠ² ΠΈ Π±Π΅ΡΠΎΠ½ΠΎΠ².
Π ΡΡΡΠΎΠΈΡΠ΅Π»ΡΡΡΠ²Π΅ ΠΈΠΌΠ΅Π΅ΡΡΡ ΠΌΠ½ΠΎΠ³ΠΎ ΡΠ°Π±ΠΎΡ, ΠΏΡΠΈ ΠΊΠΎΡΠΎΡΡΡ ΡΠ΅Ρ Π½ΠΎΠ»ΠΎΠ³ΠΈΡΠ΅ΡΠΊΠΈ Π²ΠΎΠ·ΠΌΠΎΠΆΠ½ΠΎ ΠΈ ΡΠΊΠΎΠ½ΠΎΠΌΠΈΡΠ΅ΡΠΊΠΈ ΡΠ΅Π»Π΅ΡΠΎΠΎΠ±ΡΠ°Π·Π½ΠΎ ΠΈΡΠΏΠΎΠ»ΡΠ·ΠΎΠ²Π°Π½ΠΈΠ΅ Π±Π΅ΡΠΊΠ»ΠΈΠ½ΠΊΠ΅ΡΠ½ΡΡ ΠΈ ΠΌΠ°Π»ΠΎΠΊΠ»ΠΈΠ½ΠΊΠ΅ΡΠ½ΡΡ ΡΠ΅ΠΌΠ΅Π½ΡΠΎΠ², ΡΠΏΠΎΡΠΎΠ±ΡΡΠ²ΡΡΡΠΈΡ ΡΠΊΠΎΠ½ΠΎΠΌΠΈΠΈ Π²ΡΡΠΎΠΊΠΎΠΊΠ°ΡΠ΅ΡΡΠ²Π΅Π½Π½ΡΡ ΠΏΠΎΡΡΠ»Π°Π½Π΄ΡΠ΅ΠΌΠ΅Π½ΡΠΎΠ² ΠΈ Π΄Π°ΠΆΠ΅ ΡΠ»Π°ΠΊΠΎΠΏΠΎΡΡΠ»Π°Π½Π΄ΡΠ΅ΠΌΠ΅Π½ΡΠΎΠ² ΠΎΠ±ΡΡΠ½ΠΎΠ³ΠΎ ΡΠΎΡΡΠ°Π²Π°, Ρ. Π΅. Ρ ΡΠΎΠ΄Π΅ΡΠΆΠ°Π½ΠΈΠ΅ΠΌ ΡΠ»Π°ΠΊΠ° Π½Π΅ Π±ΠΎΠ»Π΅Π΅ 60%. ΠΠ΄Π½ΠΈΠΌ ΠΈΠ· ΡΠ°ΡΠΏΡΠΎΡΡΡΠ°Π½Π΅Π½Π½ΡΡ Π²ΠΈΠ΄ΠΎΠ² ΠΌΠ΅ΡΡΠ½ΠΎΠ³ΠΎ ΡΡΡΡΡ Π΄Π»Ρ ΠΏΡΠΎΠΈΠ·Π²ΠΎΠ΄ΡΡΠ²Π° Π±Π΅ΡΠΊΠ»ΠΈΠ½ΠΊΠ΅ΡΠ½ΡΡ ΠΈ ΠΌΠ°Π»ΠΎΠΊΠ»ΠΈΠ½ΠΊΠ΅ΡΠ½ΡΡ Π²ΡΠΆΡΡΠΈΡ Π²Π΅ΡΠ΅ΡΡΠ² ΡΠ²Π»ΡΡΡΡΡ ΠΎΡΡ ΠΎΠ΄Ρ ΠΌΠ΅ΡΠ°Π»Π»ΡΡΠ³ΠΈΠΈ ΠΈ ΡΠ½Π΅ΡΠ³Π΅ΡΠΈΠΊΠΈ Π² Π²ΠΈΠ΄Π΅ ΡΠ»Π°ΠΊΠΎΠ² ΠΈ Π·ΠΎΠ». Π¨ΠΈΡΠΎΠΊΠΎΠ΅ ΠΏΡΠΈΠΌΠ΅Π½Π΅Π½ΠΈΠ΅ Π² Π‘Π‘Π‘Π ΠΈΠ·Π΄Π΅Π»ΠΈΠΉ ΠΈ ΠΊΠΎΠ½ΡΡΡΡΠΊΡΠΈΠΉ Π·Π°Π²ΠΎΠ΄ΡΠΊΠΎΠ³ΠΎ ΠΈΠ·Π³ΠΎΡΠΎΠ²Π»Π΅Π½ΠΈΡ ΠΎΠ±ΡΡΠ»ΠΎΠ²ΠΈΠ»ΠΎ Π½Π΅ΠΎΠ±Ρ ΠΎΠ΄ΠΈΠΌΠΎΡΡΡ ΠΈΠ½ΡΠ΅Π½ΡΠΈΡΠΈΠΊΠ°ΡΠΈΠΈ ΠΏΡΠΎΡΠ΅ΡΡΠΎΠ² ΡΠ²Π΅ΡΠ΄Π΅Π½ΠΈΡ Π²ΡΠΆΡΡΠΈΡ Π²Π΅ΡΠ΅ΡΡΠ² Ρ ΠΏΠΎΠΌΠΎΡΡΡ Π²ΠΎΠ΄ΠΎ-ΡΠ΅ΠΏΠ»ΠΎΠ²ΠΎΠΉ ΠΎΠ±ΡΠ°Π±ΠΎΡΠΊΠΈ — ΠΏΡΠΎΠΏΠ°ΡΠΈΠ²Π°Π½ΠΈΠ΅ Π² ΠΊΠ°ΠΌΠ΅ΡΠ°Ρ ΠΏΡΠΈ Π°ΡΠΌΠΎΡΡΠ΅ΡΠ½ΠΎΠΌ Π΄Π°Π²Π»Π΅Π½ΠΈΠΈ ΠΈ Π·Π°ΠΏΠ°ΡΠΈΠ²Π°Π½ΠΈΡ Π² Π°Π²ΡΠΎΠΊΠ»Π°Π²Π°Ρ ΠΏΡΠΈ ΠΈΠ·Π±ΡΡΠΎΡΠ½ΠΎΠΌ Π΄Π°Π²Π»Π΅Π½ΠΈΠΈ 9-16 Π°ΡΠΌ.
ΠΡΡΠ»Π΅Π΄ΠΎΠ²Π°Π½ΠΈΡ ΠΏΠΎΠΊΠ°Π·Π°Π»ΠΈ Π²ΠΎΠ·ΠΌΠΎΠΆΠ½ΠΎΡΡΡ (Π΄Π»Ρ ΠΌΠ½ΠΎΠ³ΠΈΡ Π²ΠΈΠ΄ΠΎΠ²) ΠΏΠΎΠ»ΡΡΠ΅Π½ΠΈΡ Π±Π΅ΡΠΎΠ½ΠΎΠ² Ρ ΠΏΡΠΎΡΠ½ΠΎΡΡΡΡ ΠΏΡΠΈ ΡΠΆΠ°ΡΠΈΠΈ (ΠΏΠΎΡΠ»Π΅ ΠΏΡΠΎΠΏΠ°ΡΠΈΠ²Π°Π½ΠΈΡ) Π΄ΠΎ 20 ΠΊΠ³/ΡΠΌ2 ΠΈ Π±ΠΎΠ»Π΅Π΅ Π½Π° Π²ΡΠΆΡΡΠΈΡ ΠΈΠ· Π΄ΠΎΠ±Π°Π²Π»Π΅Π½Π½ΡΡ Π³ΡΠ°Π½ΡΠ»ΠΈΡΠΎΠ²Π°Π½Π½ΡΡ ΡΠ»Π°ΠΊΠΎΠ² Π² ΡΡΠ»ΠΎΠ²ΠΈΡΡ ΠΈΠ·ΠΎΡΠ΅ΡΠΈΡΠ΅ΡΠΊΠΎΠ³ΠΎ ΠΏΡΠΎΠΏΠ°ΡΠΈΠ²Π°Π½ΠΈΡ ΠΏΡΠΈ 95Β°Π‘ Π² ΡΠ΅ΡΠ΅Π½ΠΈΠ΅ 4-8 ΡΠ°ΡΠΎΠ².
ΠΠ°ΠΆΠ½ΠΎ ΡΠ°ΠΊΠΆΠ΅ ΠΎΡΠΌΠ΅ΡΠΈΡΡ ΠΈ Π½ΠΎΠ²ΡΠ΅ Π²ΠΎΠ·ΠΌΠΎΠΆΠ½ΠΎΡΡΠΈ ΠΏΠΎ ΠΈΠ·Π³ΠΎΡΠΎΠ²Π»Π΅Π½ΠΈΡ ΡΠ»Π°ΠΊΠΎΠΏΠΎΡΡΠ»Π°Π΄ΡΠ΅ΠΌΠ΅Π½ΡΠΎΠ², ΠΊΠΎΡΠΎΡΡΠ΅ ΠΏΡΠΎΠΈΠ·Π²ΠΎΠ΄ΡΡΡΡ Π½Π΅ ΡΠΎΠ»ΡΠΊΠΎ ΠΈΠ· ΡΡΠ°Π΄ΠΈΡΠΈΠΎΠ½Π½ΠΎ ΠΏΡΠΈΠΌΠ΅Π½ΡΠ΅ΠΌΡΡ Π΄ΠΎΠΌΠ΅Π½Π½ΡΡ ΡΠ»Π°ΠΊΠΎΠ² (Π³ΡΠ°Π½ΡΠ»ΠΈΡΠΎΠ²Π°Π½Π½ΡΡ ), Π½ΠΎ ΠΈ ΠΈΠ· ΡΠ°ΠΊΠΈΡ , ΠΊΠ°ΠΊ ΠΊΠΈΡΠ»ΡΠ΅-ΡΠΎΠΏΠ»ΠΈΠ²Π½ΡΠ΅, Π° ΡΠ°ΠΊΠΆΠ΅ ΡΠ»Π°ΠΊΠΈ ΡΠ»Π΅ΠΊΡΡΠΎΡΠ΅ΡΠΌΠΈΡΠ΅ΡΠΊΠΎΠΉ Π²ΠΎΡΠΎΠ½ΠΊΠΈ ΡΠΎΡΡΠΎΡΠ°, ΠΎΠ±ΡΡΠ½ΠΎ ΠΏΠΎΠ»ΡΡΠ°Π΅ΠΌΡΠ΅ Π² Π³ΡΠ°Π½ΡΠ»ΠΈΡΠΎΠ²Π°Π½Π½ΠΎΠΌ Π²ΠΈΠ΄Π΅.
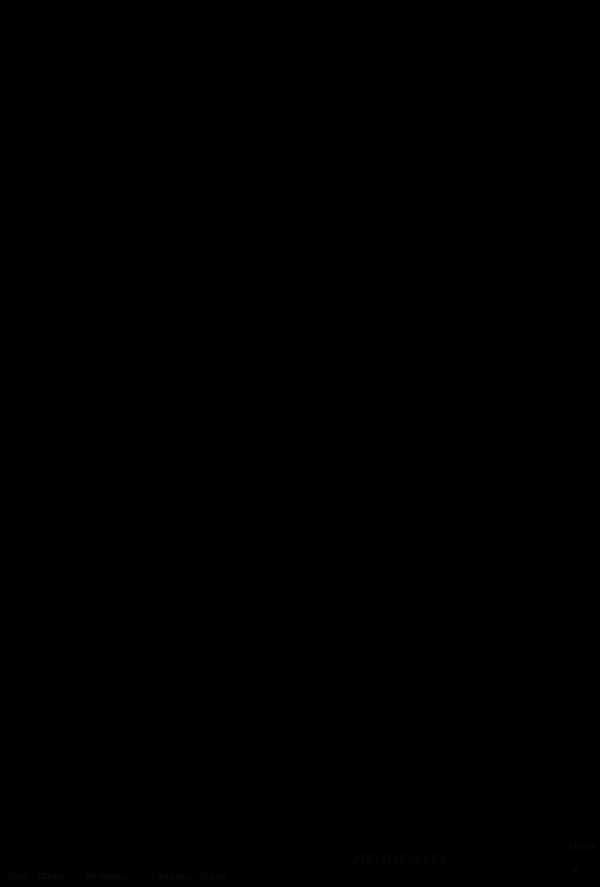
ΠΠ°ΠΈΠ±ΠΎΠ»Π΅Π΅ ΡΠΊΠΎΠ½ΠΎΠΌΠΈΡΠ΅ΡΠΊΠΈΠΌΠΈ ΠΏΠΎ Π·Π°ΡΡΠ°ΡΠ°ΠΌ ΡΡΡΡΡ, ΡΠΎΠΏΠ»ΠΈΠ²Π° ΠΈ ΡΠ»Π΅ΠΊΡΡΠΎΡΠ½Π΅ΡΠ³ΠΈΠΈ ΡΠ²Π»ΡΡΡΡΡ ΡΠ»Π°ΠΊΠΎΠ²ΡΠ΅ ΠΈ Π·ΠΎΠ»ΡΠ½ΡΠ΅ Π²ΡΠΆΡΡΠΈΠ΅ Π²Π΅ΡΠ΅ΡΡΠ²Π°, ΠΏΠΎΠ»ΡΡΠ°Π΅ΠΌΡΠ΅ ΠΈΠ· ΠΎΡΡ ΠΎΠ΄ΠΎΠ² ΠΌΠ΅ΡΠ°Π»Π»ΡΡΠ³ΠΈΡΠ΅ΡΠΊΠΎΠΉ, ΡΠ½Π΅ΡΠ³Π΅ΡΠΈΡΠ΅ΡΠΊΠΎΠΉ, ΡΠΎΡΡΠΎΡΠ½ΠΎΠΉ ΠΏΡΠΎΠΌΡΡΠ»Π΅Π½Π½ΠΎΡΡΠΈ.
ΠΡΠΎΡΡΠ°Ρ ΡΠ΅Ρ Π½ΠΎΠ»ΠΎΠ³ΠΈΡ ΠΏΡΠΎΠΈΠ·Π²ΠΎΠ΄ΡΡΠ²Π° ΡΠ»Π°ΠΊΠΎΠ²ΡΡ Π²ΡΠΆΡΡΠΈΡ Π²Π΅ΡΠ΅ΡΡΠ², ΡΠ²ΠΎΠ΄ΡΡΠ°ΡΡΡ Π² ΠΎΡΠ½ΠΎΠ²Π½ΠΎΠΌ ΠΊ Π΄ΡΠΎΠ±Π»Π΅Π½ΠΈΡ (ΠΏΡΠΈ ΠΏΡΡΠΊΠΎΠ²ΡΡ ΠΌΠ°ΡΠ΅ΡΠΈΠ°Π»Π°Ρ ), ΡΡΡΠΊΠ΅ ΠΈ ΠΏΠΎΠΌΠΎΠ»Ρ Π²Ρ ΠΎΠ΄ΡΡΠΈΡ ΠΊΠΎΠΌΠΏΠΎΠ½Π΅Π½ΡΠΎΠ², ΠΏΠΎΠ·Π²ΠΎΠ»ΡΠ΅Ρ Π±ΡΡΡΡΠΎ ΠΎΡΠ³Π°Π½ΠΈΠ·ΠΎΠ²Π°ΡΡ ΡΡΡΠΈΠ»ΡΠ½ΠΎ-ΠΏΠΎΠΌΠΎΠ»ΡΠ½ΡΠ΅ ΡΡΡΠ°Π½ΠΎΠ²ΠΊΠΈ Ρ ΠΌΠΈΠ½ΠΈΠΌΠ°Π»ΡΠ½ΡΠΌΠΈ ΠΊΠ°ΠΏΠΈΡΠ°Π»ΠΎΠ²Π»ΠΎΠΆΠ΅Π½ΠΈΡΠΌΠΈ ΠΈ ΡΡΡΠΎΠΈΡΠ΅Π»ΡΠ½ΡΠΌΠΈ ΠΎΠ±ΡΠ΅ΠΌΠ°ΠΌΠΈ Π·Π΄Π°Π½ΠΈΠΉ. Π’Π°ΠΊΠΈΠΌ ΠΎΠ±ΡΠ°Π·ΠΎΠΌ, Π΄Π»Ρ ΡΠ΄Π΅ΡΠ΅Π²Π»Π΅Π½ΠΈΡ Π±Π΅ΡΠΎΠ½Π½ΡΡ ΠΈ ΠΆΠ΅Π»Π΅Π·ΠΎΠ±Π΅ΡΠΎΠ½Π½ΡΡ ΠΈΠ·Π΄Π΅Π»ΠΈΠΉ Π½Π΅ΠΎΠ±Ρ ΠΎΠ΄ΠΈΠΌΠΎ ΠΌΠ°ΠΊΡΠΈΠΌΠ°Π»ΡΠ½ΠΎ ΠΈΡΠΏΠΎΠ»ΡΠ·ΠΎΠ²Π°ΡΡ ΠΌΠ΅ΡΡΠ½ΡΠ΅ Π²ΡΠΆΡΡΠΈΠ΅ ΠΈ Π² ΠΏΠ΅ΡΠ²ΡΡ ΠΎΡΠ΅ΡΠ΅Π΄Ρ ΡΠ»Π°ΠΊΠΎΠ²ΡΠ΅ ΡΠ΅ΠΌΠ΅Π½ΡΡ.
Π Π°ΡΠΈΠΎΠ½Π°Π»ΡΠ½ΠΎΠ΅ ΠΈΡΠΏΠΎΠ»ΡΠ·ΠΎΠ²Π°Π½ΠΈΠ΅ ΡΠ»Π°ΠΊΠΎΠ²ΡΡ ΠΎΡΡ ΠΎΠ΄ΠΎΠ² Π²ΡΠ³ΠΎΠ΄Π½ΠΎ Π΅ΡΠ΅ ΠΈ ΠΏΠΎΡΠΎΠΌΡ, ΡΡΠΎ Π½Π° ΠΈΡ ΡΠ΄Π°Π»Π΅Π½ΠΈΠ΅ Ρ ΡΠ΅ΡΡΠΈΡΠΎΡΠΈΠΈ ΠΌΠ΅ΡΠ°Π»Π»ΡΡΠ³ΠΈΡΠ΅ΡΠΊΠΈΡ ΠΏΡΠ΅Π΄ΠΏΡΠΈΡΡΠΈΠΉ ΠΈ ΡΠ»Π΅ΠΊΡΡΠΎΡΡΠ°Π½ΡΠΈΠΉ Π·Π°ΡΡΠ°ΡΠΈΠ²Π°ΡΡΡΡ Π·Π½Π°ΡΠΈΡΠ΅Π»ΡΠ½ΡΠ΅ ΠΌΠ°ΡΠ΅ΡΠΈΠ°Π»ΡΠ½ΡΠ΅ ΠΈ ΡΡΡΠ΄ΠΎΠ²ΡΠ΅ ΡΠ΅ΡΡΡΡΡ.
Π¨Π»Π°ΠΊΠΈ ΠΏΡΠΈΠ²Π»Π΅ΠΊΠ°ΡΡ ΠΊ ΡΠ΅Π±Π΅ Π²ΡΠ΅ Π²ΠΎΠ·ΡΠ°ΡΡΠ°ΡΡΠ΅Π΅ Π²Π½ΠΈΠΌΠ°Π½ΠΈΠ΅ ΠΈ Π²ΠΎ ΠΌΠ½ΠΎΠ³ΠΈΡ Π·Π°ΡΡΠ±Π΅ΠΆΠ½ΡΡ ΡΡΡΠ°Π½Π°Ρ . Π‘Π»Π΅Π΄ΡΠ΅Ρ ΡΡΠ΅ΡΡΡ Π²ΠΎΠ·ΠΌΠΎΠΆΠ½ΠΎΡΡΡ ΠΏΠΎΠ»ΡΡΠ΅Π½ΠΈΡ ΡΠ»Π°ΠΊΠΎΠΏΠΎΡΡΠ»Π°Π½Π΄ΡΠ΅ΠΌΠ΅Π½ΡΠΎΠ² Π²ΡΡΠΎΠΊΠΎΠΉ Π°ΠΊΡΠΈΠ²Π½ΠΎΡΡΠΈ Ρ ΠΏΠΎΠΌΠΎΡΡΡ ΡΠΎΠ½ΠΊΠΎΠ³ΠΎ ΠΏΠΎΠΌΠΎΠ»Π° Π΄ΠΎ ΡΠ΄Π΅Π»ΡΠ½ΠΎΠΉ ΠΏΠΎΠ²Π΅ΡΡ Π½ΠΎΡΡΠΈ 4000-5000 ΡΠΌ2 /Π³ ΠΈ Π²ΡΠΏΡΡΠΊΠ° ΠΈΡ ΠΌΠ°ΡΠΊΠΈ Π½Π΅ Π½ΠΈΠΆΠ΅ 400. ΠΡΠΈ ΡΡΠΎΠΌ Π²ΠΎΠ·ΠΌΠΎΠΆΠ½ΠΎ ΠΏΡΠΈΠΌΠ΅Π½Π΅Π½ΠΈΠ΅ ΡΠ°ΠΊΠΆΠ΅ ΠΈ ΠΏΠΎΠ²ΡΠΎΡΠ½ΠΎΠ³ΠΎ ΠΏΠΎΠΌΠΎΠ»Π° ΠΏΠΎΡΡΠ»Π°Π½Π΄ΡΠ΅ΠΌΠ΅Π½ΡΠ½ΠΎΠ³ΠΎ ΠΏΠΎΡΠΎΡΠΊΠ° Ρ Π³ΡΠ°Π½ΡΠ»ΠΈΡΠΎΠ²Π°Π½Π½ΡΠΌ ΡΠ»Π°ΠΊΠΎΠΌ. ΠΡΠΎΠΌΠ΅ ΡΠΎΠ³ΠΎ, ΠΎΡΠ³Π°Π½ΠΈΠ·Π°ΡΠΈΡ ΠΏΡΠΎΠΈΠ·Π²ΠΎΠ΄ΡΡΠ²Π° Π²ΡΡΠΎΠΊΠΎΠΌΠ°ΡΠΎΡΠ½ΡΡ ΡΠ»Π°ΠΊΠΎΠΏΠΎΡΡΠ»Π°Π½Π΄ΡΠ΅ΠΌΠ΅Π½ΡΠΎΠ² ΡΠ»Π΅Π΄ΡΠ΅Ρ ΠΏΡΠΎΠ²Π΅ΡΡΠΈ Π½Π° Π±Π°Π·Π΅ Π½Π°ΠΈΠ±ΠΎΠ»Π΅Π΅ Π°ΠΊΡΠΈΠ²Π½ΡΡ ΡΠ»Π°ΠΊΠΎΠ² ΠΌΠ΅ΡΠ°Π»Π»ΡΡΠ³ΠΈΡΠ΅ΡΠΊΠΈΡ Π·Π°Π²ΠΎΠ΄ΠΎΠ².
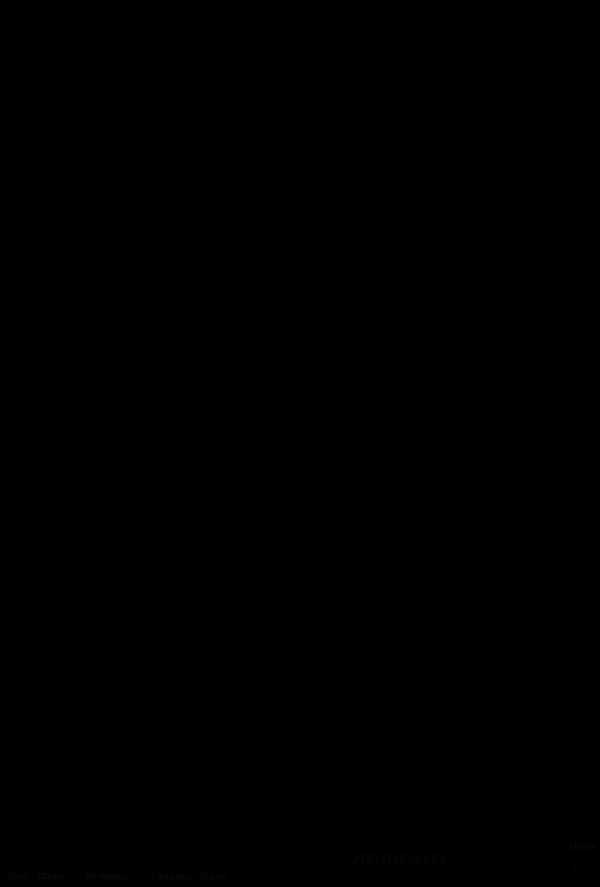
Π¨Π»Π°ΠΊΠΎΠΏΠΎΡΡΠ»Π°Π½Π΄ΡΠ΅ΠΌΠ΅Π½Ρ (ΠΠΠ‘Π’ 10178-85 ) ΡΠ²Π»ΡΠ΅ΡΡΡ Π³ΠΈΠ΄ΡΠ°Π²Π»ΠΈΡΠ΅ΡΠΊΠΈΠΌ Π²ΡΠΆΡΡΠΈΠΌ Π²Π΅ΡΠ΅ΡΡΠ²ΠΎΠΌ, ΠΏΠΎΠ»ΡΡΠ°Π΅ΠΌΡΠΌ ΠΏΡΡΠ΅ΠΌ ΡΠΎΠ²ΠΌΠ΅ΡΡΠ½ΠΎΠ³ΠΎ, ΡΠΎΠ½ΠΊΠΎΠ³ΠΎ ΠΈΠ·ΠΌΠ΅Π»ΡΡΠ΅Π½ΠΈΡ ΠΏΠΎΡΡΠ»Π°Π½Π΄ΡΠ΅ΠΌΠ΅Π½ΡΠ½ΠΎΠ³ΠΎ ΠΊΠ»ΠΈΠ½ΠΊΠ΅ΡΠ° ΠΈ Π²ΡΠΆΡΡΠ΅Π³ΠΎ Π³ΡΠ°Π½ΡΠ»ΠΈΡΠΎΠ²Π°Π½Π½ΠΎΠ³ΠΎ Π΄ΠΎΠΌΠ΅Π½Π½ΠΎΠ³ΠΎ ΠΈΠ»ΠΈ ΡΠ»Π΅ΠΊΡΡΠΎΡΠ΅ΡΠΌΠΎΡΠΎΡΡΠΎΡΠ½ΠΎΠ³ΠΎ ΡΠ»Π°ΠΊΠ° Ρ Π΄ΠΎΠ±Π°Π²Π»Π΅Π½ΠΈΠ΅ΠΌ 3-6% Π΄Π²ΡΠ²ΠΎΠ΄Π½ΠΎΠ³ΠΎ Π³ΠΈΠΏΡΠ°;
ΡΠ»Π°ΠΊΠΎΠΏΠΎΡΡΠ»Π°Π½Π΄ΡΠ΅ΠΌΠ΅Π½Ρ ΠΌΠΎΠΆΠ½ΠΎ ΠΈΠ·Π³ΠΎΡΠΎΠ²ΠΈΡΡ ΡΡΠ°ΡΠ΅Π»ΡΠ½ΡΠΌ ΡΠ»ΠΈΠ²Π°Π½ΠΈΠ΅ΠΌ ΡΠ΅Ρ ΠΆΠ΅ ΠΌΠ°ΡΠ΅ΡΠΈΠ°Π»ΠΎΠ², ΠΈΠ·ΠΌΠ΅Π»ΡΡΠ΅Π½Π½ΡΡ ΡΠ°Π·Π΄Π΅Π»ΡΠ½ΠΎ.
ΠΠΎ ΠΠΠ‘Π’ 10178-76 Π΄ΠΎΠΌΠ΅Π½Π½ΠΎΠ³ΠΎ ΡΠ»Π°ΠΊΠ° Π² ΡΡΠΎΠΌ ΡΠ΅ΠΌΠ΅Π½ΡΠ΅ Π΄ΠΎΠ»ΠΆΠ½ΠΎ Π±ΡΡΡ Π½Π΅ ΠΌΠ΅Π½Π΅Π΅ 21% Π½Π΅ Π±ΠΎΠ»Π΅Π΅ 10% ΠΌΠ°ΡΡΡ ΡΠ΅ΠΌΠ΅Π½ΡΠ°; ΡΠ°ΡΡΡ ΡΠ»Π°ΠΊΠ° ΠΌΠΎΠΆΠ½ΠΎ Π·Π°ΠΌΠ΅Π½ΠΈΡΡ Π°ΠΊΡΠΈΠ²Π½ΠΎΠΉ ΠΌΠΈΠ½Π΅ΡΠ°Π»ΡΠ½ΠΎΠΉ Π΄ΠΎΠ±Π°Π²ΠΊΠΎΠΉ (ΡΡΠ΅ΠΏΠ»ΠΎΠΌ) Π½Π΅ Π±ΠΎΠ»Π΅Π΅ 10% ΠΌΠ°ΡΡΡ ΡΠ΅ΠΌΠ΅Π½ΡΠ°, ΡΡΠΎ ΡΠΏΠΎΡΠΎΠ±ΡΡΠ²ΡΠ΅Ρ ΡΠ»ΡΡΡΠ΅Π½ΠΈΡ ΡΠ΅Ρ Π½ΠΈΡΠ΅ΡΠΊΠΈΡ ΡΠ²ΠΎΠΉΡΡΠ² Π²ΡΠΆΡΡΠ΅Π³ΠΎ. ΠΠ°ΠΈΠ±ΠΎΠ»Π΅Π΅ Π±ΡΡΡΡΠΎΠ΅ ΡΠ²Π΅ΡΠ΄Π΅Π½ΠΈΠ΅ ΠΏΡΠΎΠΈΡΡ ΠΎΠ΄ΠΈΡ ΠΏΡΠΈ 30-40% ΡΠ»Π°ΠΊΠ°.
mirznanii.com